Изготовление булатной стали
Булатная сталь — сплав железа с углеродом, который благодаря особенной технологии производства обладает узорчатой структурой и повышенной гибкостью и твердостью. С древнейших времен этот материал используется для изготовления различных видов холодного оружия. По химическому составу булат ближе к чугуну, чем к стали. Но при этом он сохраняет пластичность и ковкость, присущую низкоуглеродистым маркам металла, а в сочетании с повышенным содержанием углерода, булат обладает невероятной твердостью, которая недостижима для стали даже после ее закалки.
Работа с булатом требует высокой сноровки и тщательно соблюдения технологических процессов на каждом этапе обработки. Неправильно выбранный температурный режим может запросто испортить материал, превратив его либо в обычную сталь, либо в нековкий вид чугуна. Поэтому с булатом доверяют работать только опытным металлургам. Интересный факт, если булат расплавить, а потом дать ему застыть, он не перестанет быть булатом, его также можно многократно перековывать на различные изделия. Материал поддается сварке и может быть соединен как с самим собой, так и со сталью любой другой марки.
Как получают булат?
Булат можно получить из некоторых видов обычной стали. Основным условием является низкий уровень легированности материала. Из высоколегированной стали булат получить невозможно вообще, а из среднелегированной — только булат низкого качества. Несмотря на то, что современные материалы превосходят булат по своим свойствам и не требуют столь сложных процедур обработки, до сих пор сохранились мастерские, в которых энтузиасты изготавливают клинки по древним технологиям. Но использование более современных орудий труда позволяет выплавлять материал значительно более высокого качества.
Кроме того, сейчас многие производители добавляют в сплав дополнительные элементы, которые придают булату новые свойства. В основном это касается применения хромовых и никелевых присадок, позволяющих значительно повысить сопротивляемость коррозии. Некоторые экземпляры оружия, которые предназначаются исключительно для коллекций, и не будут использоваться в постановочных боях, полностью покрывают слоем серебра. Это позволяет защитить сталь от негативного воздействия окружающих факторов. К тому же мягкое серебро проще поддается ювелирной обработке по нанесению на клинок тематических узоров или рисунков.
Булат в отличие от дамасской стали, которая также служила для производства клинков, характеризуется беспорядочностью узора. Он получается в результате кристаллизации металлической решетки в сплаве.
Способы производства материала
Существует четыре способа изготовления булатной стали. Первый подразумевает прямое сплавление железной руды с измельченным графитом. Это наиболее простой с точки зрения подготовки способ, так как он не требует получения чистого железа. Но для его успешной реализации необходима руда с процентным содержанием металла не менее 85%, иначе не получится булатной стали хорошего качества.
Для данного варианта не подойдут руды с содержанием самородной серы, которые в природе встречаются довольно часто. Так что достать подходящий материал будет чрезвычайно сложно. В современных условиях этот способ не используется, так как найти чистое железо не проблема, но в древние времена этот метод был наиболее распространен в кузнечном деле. Второй способ подразумевает расплавление железа при непосредственном доступе углей. При этом в сплав попадает не только чистый углерод, но и его оксиды, которые и придают металлу структуру булата. Этот способ также сейчас не используется, потому что для него характерна высокая доля примесей в получаемом материале, что негативно сказывается на его качестве.
Третий способ — долговременное обжигание железа без доступа воздуха. Этот метод является самым дешевым в реализации, поэтому имеет широкое распространение. Получаемый таким способом материал называют литым булатом. Важным условием получения хорошего материала является точный расчет времени обжига. В противном случае в сплав может попасть избыточное количество углерода, что приведет к его плохой ковкости и хрупкости. Четвертый вариант — самый дорогостоящий, но при этом позволяет получать материал наилучшего качества. Он подразумевает сплавление чистого железа с графитом в безвоздушной среде. Это позволяет избавить булатную сталь от нежелательных примесей и оксидных присадок.
Изделия из булата данной марки наиболее ценятся в кругу знатоков, поэтому стоят довольно дорого. В древние времена такое оружие могли себе позволить только зажиточные воины. В наши дни клинки служат в основном в качестве украшений, которые вешают на стену. Изредка они могут служить для исторических реконструкций известных битв прошлых эпох. Для перечисленных целей используют булат наилучшего качества, чтобы оружие красиво смотрелось и по своим свойствам не отличалось от лучших клинков прославленных мастеров кузнечного дела. Самые дорогие образцы украшаются разнообразными рукотворными узорами, которые посвящены тематике баталий. Рукоятки клинков также служат для украшения. Их изготавливают из самых разнообразных материалов от искусно обработанных рогов животных до драгоценных металлов. Дополнительно эфес может быть инкрустирован разноцветными камнями.
Кроме приведенных способов существовал еще один, который не получил широкого распространения. В качестве эксперимента металлурги Советского Союза испытали следующий метод производства булатной стали. На первом этапе чистое железо или низкоуглеродистую сталь расплавляли в индукционной печи, а затем вводили в расплав кремниевые и алюминиевые присадки, после чего добавляли к полученному сплаву графит. На выходе получался чугун с 3-4% содержанием углерода. Но на этом процесс плавки не заканчивался.
В расплав постепенно добавляли железо или низкоуглеродистый стальной лом в пропорциях, чтобы массовая доля добавок составила 50-70% от массы чугуна. После остывания и кристаллизации был получен булат с высокоуглеродистой металлической сеткой, в которую были вплетены низкоуглеродистые элементы. Полученный булат обладал великолепными свойствами по ковкости и пластичности, а также показывал запредельную твердость. Но в широкое производство этот способ не пошел из-за сложности технологического процесса и высокой дороговизны выплавки. Кроме того, были уже известны и более современные и совершенные материалы, так что такие затраты на получение булата справедливо сочли неоправданными.
promplace.ru
Булатная сталь: как сварить и выковать
Булат. Бессчетное количество легенд и мифов существует вокруг него. Тысячи кузнецов и металлургов в течение веков, пытались разгадать его тайны. И по сей день, одним из самых удивительных увлечений, которым занимается большое количество людей у нас и за рубежом, несомненно, является изготовление булатных клинков.
Этот очень древний и таинственный вид кузнечного мастерства уходит своими корнями в седую старину, в древнюю Индию и Переднюю Азию. Тайны этого искусства хранились так крепко, что в последнее время стали считать, что способы получения булатной оружейной стали утеряны давным-давно.
Однако в России, интерес к легендарному булату не пропадал никогда, и у нас всегда имелись мастера, увлеченные ручной ковкой и умеющие не только сварить «нужную» сталь, но и отковать из нее хороший клинок, который идет как на «рабочие», так и на самые дорогие «коллекционные» ножи.
Изготовление булатной стали
Булат не нужно путать с «дамаском» – «сварной» сталью. Булат – это так называемая «литая сталь», и работа над булатным клинком начинается с изготовления тигля, специального огнеупорного сосуда, в котором будет вариться сталь.
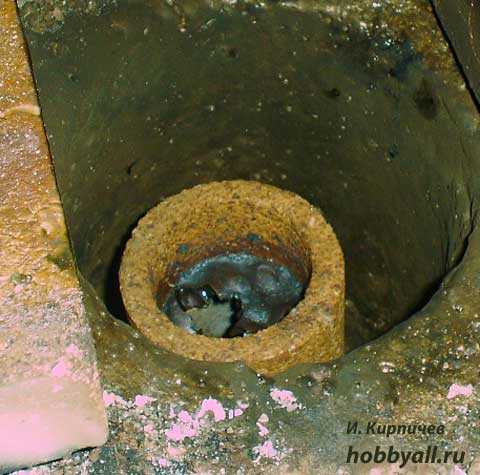
Тигель в печи
Тигель наполняют шихтой определенного состава. Секреты этого состава мастера, хобби которых – изготовление булата, порой хранят «пуще зеницы ока». Тигель, наполненный железом или определенными сортами стали с особыми добавками, ставится в печь, в которой поднимается температура, нужная для расплавления его содержимого. Спустя некоторое время, когда печь остынет, тигель вынимают, разбивают и вынимают слиток стали, который затем расковывают в полосы. Из этих полос уже потом изготавливаются клинки для холодного оружия или для обычных ножей.
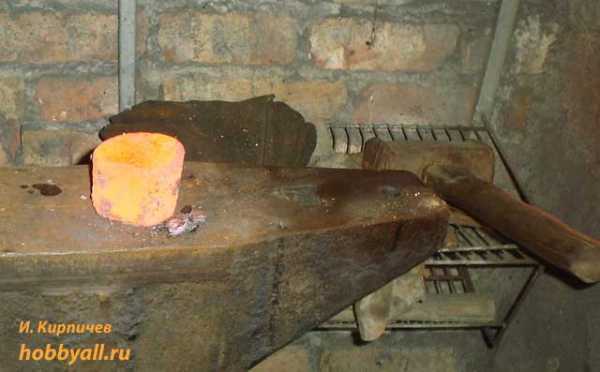
Нагретый слиток на наковальне

Ковка клинка
Узор – особенность булатной стали
Особенностью булатной стали, является узор, появляющийся на ее поверхности после травления различными химическими реактивами. По этому узору судят о возможном качестве стали и способе ее получения. С древних времен у этих узоров имеются свои названия: «шам», «табан», «кара-табан» и другие.
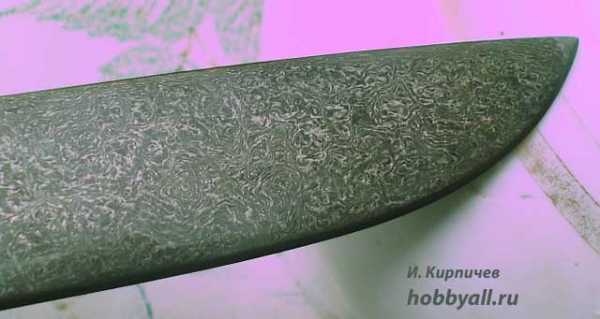
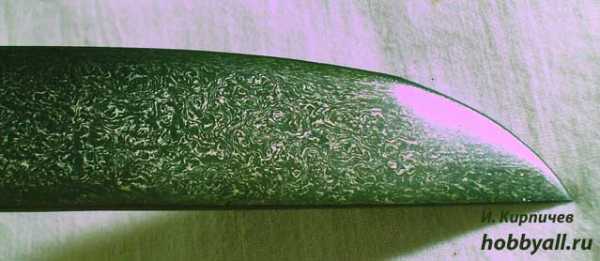
Узоры на клинках из булата
Оружие с таким узором, в средние века ценилось очень дорого, потому что булатная сталь в те времена по своим свойствам намного превосходила имеющиеся сорта обычной, «безузорчатой» стали.
Именно из-за своеобразного узора, булатную сталь нельзя спутать ни с каким другим видом стали. Оружие с булатными клинками работы старых мастеров хранится в коллекциях Эрмитажа и многих самых известных музеев мира.
Сотни мастеров в России, Соединенных Штатах, Германии, увлеченно работают с булатной сталью, отдавая своему хобби все свое свободное время.
Автор И. Кирпичев
hobbyall.ru
Где и как закалялась булатная сталь: исторические предпосылки качества
Булатная сталь – это сталь самого высокого качества. Именно из нее изготавливается боевое оружие. Ножи из такой стали обладают большой упругостью и вязкостью, сочетание этих двух характеристик позволяет ножу обладать высокими режущими качествами.
Булатная сталь — это литая углеродистая сталь, которая обладает специфической структурой. Твёрдость клинка из булата после термообработки составляет 64 HRC.
Булат vs Дамаск
И булат, и дамаск – это достаточно близкие по виду и характеру красивые стали. Дамаск образуется за счет сковывания нескольких пластин различных металлов. Это делается следующим образом: берутся несколько тонких пластин и проковываются несколько раз, после этого металлы смешиваются и образуется дамаск.
Булатную же сталь варят. Секрет данного металла состоит в составе и пропорциях сплава. Во время варки обращают внимание на любую мелочь. Сплав металлов должен свариться, но не быть слишком передержанным на огне. Дальнейшая обработка сплава зависит от предпочтения мастера. Можно расковывать весь слиток, а можно резать его вдоль или поперек, от этих действий будет зависеть будущий рисунок и прочность клинка.
Откуда пришла булатная сталь?
Булатная сталь пришла из Индии. В Индии, как известно, люди могут медитировать десятилетиями или делать один меч несколько лет. Например, у старых индусских кузнецов молоты больше были похожи на молоточки, соответственно и времени больше было на работу. Ковавшие оружие кузнецы щепетильно относились к секретам булата и технологии его изготовления. Они передавали знания только из уста в уста старшему сыну. Это делалось не просто так: даже в древние века существовал всемирный рынок вооружений с достаточно сильной конкуренцией.
Несколько позднее, после Индии, искусством изготовления булатной стали овладели мастера Сирии и Испании. В настоящее время имеются документальные данные о том, что на Руси было налажено производство сабель и кинжалов из булатной стали.
О чудесных свойствах булатной стали рассказывают легенды до сих пор. Воспоминания о ней находят в записях историков, монахов, в романах.
Самые первые сведения о булате дошли до современности от участников походов Александра Македонского.
К концу XVIII в. все секреты производства булатной стали были утеряны.
2 легенды о булатной стали
В конце IV в. до нашей эры Александр Македонский и индийский царь Пор во главе своих войск встретились на реке Гидаспу. Кровопролитная битва для индийцев закончилась трагически — индийские войска были разгромлены, а царь Пор, отважно сражавшийся и смертельно раненный, попал в плен. Александр Македонский был изумлен — доспехи царя не имели ни царапин, ни вмятин от копий и стрел. Причиной тому послужил панцирь, который был выполнен из металла удивительной твердости. Из такого же металла были сделаны и индийские мечи. После похода Александра Македонского в Индию способы получения высокопрочный мечей через Сирию и Персию проникли в Европу. Персы называли такую сталь «пулат», а европейцы — «булат».
Упоминание о булатной стали можно найти и в романе В. Скотта «Талисман». В нем рассказывается о состязании между английским королем Ричардом Львиное Сердце и султаном Саладином. Булатная сабля Саладина безжалостно рубила железные копья пополам и свободно рассекала подброшенное в воздух шелковое тонкое покрывало.
Узор – особенность булатной стали
Булатную сталь визуально легко отличить от любой другой. Важной особенностью булатной стали, является узор. Он появляется на ее поверхности после травления различными химическими реактивами. По данному узору судят о возможном качестве стали или способе ее получения. Еще с древних времен у узоров булатной стали есть свои названия: «шам», «табан», «кара-табан» и другие.
Узор булата образуется во время падения температуры отливки и представляет собой светлые линии цементитной сетки высаженного углерода по границам зерен аустенита. Важно знать, что чем темнее фон и светлее линии — тем булатная сталь дороже.
А существовала ли булатная сталь?
Неповторимость булатных клинков заставила ученых усомниться: возможно, что булатная сталь не существовала вовсе? Ведь, подобные свойства даже в настоящее время металлу придать не удается, что говорить о временах, отдаленных от нас на 2 тысячи лет.
Проверить легенды и теории непросто, потому что при раскопках ученые находят лишь фрагменты клинков. Окончательно развенчать миф о булатной стали несколько лет назад решил один из членов Русского географического общества, доктор технических наук Игорь Таганов. Он ездил с экспедициями в Индию, Иран и собирал образцы клинков. Не так давно Таганов передал несколько фрагментов на кафедру пластической обработки металлов Санкт-Петербургского государственного политехнического университета. Профессору казалось удивительным, что при современных методах анализа материалов, когда состав любого сплава можно расписать практически до каждого атома, булатная сталь еще остается секретом для науки. За изучение образцов взялся сотрудник кафедры Василий Мишин. Однако вместо того чтобы доказать, что булат — всего лишь миф, он не только раскрыл секрет стали, но и воссоздал ее.
Первым делом Василий Мишин изучил на спектрометре химический состав материала, из которого были изготовлены клинки. Самое удивительное даже для современных металлургов заключается в том, что структура булата совершенно не характерна для высокоуглеродистых сталей, а ведь именно таковой по сути является булатная сталь. Василий Мишин сумел воссоздать сплав.
Изготовление булатной стали
Булат не то же самое, что «дамаск» – «сварная» сталь. Булат – это так называемая «литая сталь», и работа над булатным клинком начинается с изготовления тигля. Это специальный огнеупорный сосуд, в котором будет вариться сталь.
Тигель наполняют шихтой определенного состава. Секреты данного состава мастера, зачастую хранят «пуще зеницы ока». Тигель, наполненный железом или определенными сортами стали с особыми добавками, ставится в печь. В печи поднимается температура, необходимая для создания однородного сплава. Спустя некоторое время, когда печь остынет, тигель вынимают, разбивают и вынимают слиток стали. Этот слиток позднее расковывают в полосы. Из этих полос потом изготавливаются клинки, как для холодного оружия, так и для обычных ножей.
Технология получения литого булата имеет много нюансов и для ее реализации требуются знания на уровне интуиции опытного кузнеца. В двух словах технология следующая:
-
губчатое железо проковывается молотом;
-
железо смешивается с древесным углем, после помещается в тигель;
-
тигель нагревается до температуры 1200 градусов;
-
далее тигель очень медленно охлаждаетя и получается вуц — небольшой слиток булата.
Приобретайте изделия из булатной стали в нашем магазине. Вы можете связаться с нашими консультантами на главной странице нашего сайта, они оперативно ответят на все интересующие Вас ваши вопросы.
rognar.ru
Как варят булат? | Культура
Вначале медные мечи рубили врагов, отбивая удары заведомо менее прочного оружия. Потом бронзовые мечи рубили мечи медные и прорубали кожаный доспех с медными бляшками.
Потом пришел век железа и поначалу много воинов, вооруженных железными мечами, менее прочными, чем бронзовые, побеждали немногих мастеров боя, снабженных бронзовым доспехом и бронзовыми мечами. А потом железо стало прочнее бронзы.
Точнее, собственно железо, по своей природе, относительно мягкое. Закалить его нельзя, закалке поддается только сталь, т. е. железо, слегка обогащенное углеродом (от 0.04% до 2.14%). Если слишком обогатить железо углеродом (от 2.14% до 4%), то получится чугун, который раньше называли «свиным железом» — за то, что был хрупким и негодным для ковки. А именно ковкой тогда и делали разнообразные изделия из железа.
Далее на многие тысячелетия сила государств, мощь их войск выковывалась кузнецами. От знаний и умений кузнецов зависела прочность мечей и надежность кольчуг или бехтерцов воинов. То есть от умения кузнеца зависели жизни воинов и победа или поражение в бою.
Фото: Depositphotos
Сотни и тысячи лет экспериментов привели к созданию булата — прекрасной узорчатой стали. Булатные мечи рубили врагов и их простые железные мечи, прорубали железные латы. В середине I тысячелетия нашей эры в Индии научились производить суперсталь для супероружия. Называли ее тогда «вуц».
Со временем тайной овладели кузнецы Персии, тогда суперсталь начали назвать фаранд, или хорасан. Тайна хранилась столь надежно, что если кузнец не успевал выбрать себе преемника, чтобы передать ему свои секреты, то в данном месте секрет стали пропадал… Пропадал и возвращался. Снова и снова.
В последний раз в промышленных масштабах пытался возродить производство литого булата директор Златоустовских заводов Аносов. Инженер, изобретатель и директор, т. е. «царь и бог» местного масштаба. Он после более чем десяти лет опытов сумел составить рецепт и добиться нужных температурных режимов для производства стали булатной прочности. Однако это производство было признано нетехнологичным, слишком сложным — и в массовое производство литой булат из Златоуста не пошел.
По другому пути пошли в Китае и там еще во II веке нашей эры научились выковывать мечи из сложенных вместе и сваренных ковкой пластинок высокоуглеродистой стали и низкоуглеродистого мягкого железа. Формально это совсем просто, но фактически это очень и очень трудоемко и нетехнологично.
Сложить через одну пластинки высокоуглеродистого и низкоуглеродистого железа. Разогреть в горне. Сварить ковкой, превратив брусочек почти в блин, потом нагреть и сложить этот блин, снова молотом превратив его в брусочек. И все это надо повторить много-много раз. Брусок раскалить в горне, расплющить, сложить, затем повторить это снова и снова.
После многократного повторения мы получаем булатную заготовку будущего изделия. В старину из заготовки выковывали мечи. Теперь обычно делают ножи. Придав изделию форму, его сначала полировали, а затем слегка протравливали кислотой — и на железе выступал узор. Это означало — получен меч дамасской стали, готовый прорубить любой доспех и перерубить любой меч из простого железа.
Кстати, в городе Дамаске дамасской стали не делали. Но зато там был огромный рынок изделий из булата, производимого персидскими и арабскими кузнецами. Потому мечи и стали называть дамасскими.
Прошли века… Люди открыли тайну производства булата, и сегодня любой хороший кузнец может всего за несколько дней повторить многомесячный подвиг кузнецов древности и сделать из «просто железа» булатную сталь, ножи или мечи.
Производство сегодня очень сильно нуждается в сверхпрочных металлических инструментах для прецизионной обработки стальных изделий. Но здесь булат победили сверхпрочные сплавы, «победит» и аналогичные, столь же прочные, что и булат, но намного более устойчивые в условиях перегрева, да к тому же — намного более технологичные, получаемые сразу большими объемами.
Фото: Depositphotos
А булат? Булатные ножи и сегодня выпускают — небольшими партиями, на любителя. Уж больно такой нож хорош. Попробуй примени его при промышленной разделке мяса. Специально для разделки туш мясникам делают особые ножи, острые и тяжелые. Но, дабы избежать случайных травм, им для защиты левой руки делают специальные кольчужные перчатки. Нож мясника не прорубает ее.
А попробуйте работать с булатным ножом! Соскользнет лезвие, ударит по кольчужной перчатке на руке — и пропорет ее, как веками делали с кольчугами врага булатные мечи.
А как все-таки варят булат? А никак не варят. Булат — кованая сталь. Варить ее в печи невозможно, хотя Амосов почти два века назад и очень старался. Булат — результат работы и искусства кузнеца, его силы, умения, знаний и терпения.
Я смотрел телепередачу: кузнец показывал, как сделать булатный нож. У него был горн, раскаляемый газом, а не на угле, был молот с механическим приводом. И все равно производство булата заняло у него несколько дней — от стопки пластинок низкоуглеродистого железа и высокоуглеродистой стали до булатного ножа с прекрасными узорами на лезвии, которым тот кузнец перерубал гвозди и легко пробивал полоску листового железа.
Фото: Depositphotos
Что еще почитать по теме?
Какова история железа? Эпоха стали
Каким японским мечом… не стоит махать?
Какое значение имел меч в Древней Руси?
shkolazhizni.ru
Изготовление булата
Много веков существовала тайна булата. Лишь в 1841 году русский ученый и металлург П.П. Аносов предложил способы изготовления булата.
Исследуя под микроскопом структуру булатных клинков, ученые обнаружили, что они состоят из двух составляющих: мягкой (низкоуглеродистой) и твердой (высокоуглеродистой) стали.
Влияние углерода на свойства стали
Известно, что сталь — это сплав железа с углеродом. Содержание углерода в стали может доходить до 2% . Если больше — это уже чугун. Свойства стали сильно зависят от концентрации углерода, содержащегося в ней. Если его мало (менее 0,1—0,2 % ), то сталь получается мягкой, пластичной, вязкой, но при этом прочность и твердость ее низкие. Шпага из такой стали согнется и останется согнутой, меч из нее затупится от первого же удара.
Если углерода много (1—2% ) — сталь, пройдя соответствующую термическую обработку, станет очень прочной, твердой, упругой, но заодно приобретет и хрупкость. Шпагу из такой стали в полукруг не согнешь — сломается, остро не заточишь — лезвие выкрошится. И только когда оба сорта связаны воедино, тесно переплетены на микроуровне, гармонично дополняя друг друга, получается булатная сталь, обладающая теми свойствами, которые принесли ей заслуженную славу.
Булат — композит
Таким образом, секрет булатной стали — в ее композитной структуре. Древние мастера ничего об этом не знали, им приходилось наощупь, путем многолетних проб и ошибок подбирать компоненты для выплавки булата, проверять различные методы его обработки. В ход шли добавки из трав, цветов, различные снадобья, у каждого мастера — свои пропорции, свои методы ковки, закалки. Но секреты древних мастеров навсегда утрачены.
Неизвестно, в какой последовательности и какие зелья бросал тот или иной ремесленник в печь, сколько рабов раздували меха, с какой скоростью мчался всадник на арабском скакуне между гор с раскаленным мечом, закаливая его. Но их целью было то, чтобы создать специальную структуру материала — смесь волокнистых частиц низко и высокоуглеродистой стали, — говоря современным языком. И это стало понятным, благодаря кропотливым исследованиям известных и неизвестных ученых. Как на вершину горы можно взобраться и с юга, и с севера, и с запада, и с востока, так и булат можно изготовить разными методами. Главное — получить нужный результат.
Древние методы изготовления булата
Существовали разные метода изготовления булата, приведем описание двух, которые,предположительно, вполне могли использовать древние ремесленники.
В горн (глиняную печь) древнеегипетского или индийского металлурга загружали мелкие куски железной руды и угля, поджигали уголь и мехами подавали в горн воздух, способствовавший повышению температуры. Образующаяся при сгорании угля окись углерода восстанавливала руду до чистого железа. Восстановленные куски частично спекались между собой, образуя пористый железный брикет. Поверхность этих кусков, взаимодействуя с углеродом, насыщалась им, а сердцевина оставалась не науглероженной. Температура плавления стали понижается с увеличением содержания углерода в ней. Температура в горне была достаточно высокой, чтобы расплавить поверхностные, сильно науглероженные части бывших кусков руды, но недостаточно высокой, чтобы расплавить их сердцевину — почти чистое железо. Расплавленные участки, сплавляясь между собой, образовывали непрерывную стальную основу (матрицу), внутри которой находились включения чистого железа.
При остывании расплавленная высокоуглеродистая сталь кристаллизовалась в виде древовидных кристаллов, в ветвях которых, как шишки на елках, задерживались нерасплавленные частицы низкоуглеродистой стали. Далее следовала многократная ковка, причем совершать ее нужно было так, чтобы древовидные кристаллы не разрушались, а только сминались. При этом частицы мягкой стали вытягивались, приобретали волокнистую форму, переплетались с кристаллами высокоуглеродистой стали, формируя характерный для булата волнистый узор. Из откованных полос изготовляли клинки, мечи, кинжалы, наконечники копий, латы и другие столь необходимые древнему воину вещи.
Далее следовала закалка — нагрев стали до определенной температуры и резкое охлаждение. При этом высокоуглеродистая сталь становилась прочной и твердой, низкоуглеродистая оставалась вязкой и мягкой, а композит из этих сталей приобретал свойства булата.
Технология изготовления самурайских мечей
Технология изготовления самурайских мечей (катана) имела свою специфику. Для них использовали руды, содержащие кроме железа ряд легирующих элементов — никель, молибден и другие. Свойства стали ухудшаются из-за присутствия серы и фосфора — вредных примесей, которые неравномерно распределяются по объему слитка. Чтобы избавиться от них, железо, полученное после восстановления руды в горне, проковывали в листы или прутья и закапывали в землю в болотистой местности. Там оно лежало несколько лет, его периодически откапывали и контролировали внешний вид.
Те места, где было повышенное содержание вредных примесей, в первую очередь разъедались водой, содержащей кислоты и соли. Участки, обогащенные никелем, молибденом и другими полезными добавками, оставались целыми. В результате лист железа приобретал вид дырчатого голландского сыра. Такой ноздреватый металл науглероживался, при этом на его поверхности и вблизи дырок образовывалась высокоуглеродистая сталь, а внутри оставалось чистое железо. Этот «кусок сыра» складывался вдвое и подвергался горячей ковке до полного схватывания между собой перегнутых частей. Затем полученный лист снова складывался вдвое и проковывался. Этот процесс повторялся многократно, при этом образовывался монолитный металл, состоящий из нескольких тысяч или даже десятков тысяч тончайших прослоек твердой и мягкой стали, чередующихся между собой.
Из таких поковок и делали японские кузнецы знаменитые самурайские мечи и ножи.
Таким образом были разгадали принципы изготовления булата.
И если подходить к вопросу по-научному, то можно сказать, что принципиальных секретов в технологии производства булата нет. Ясно, из чего его делали, как ковали и закаливали, как шлифовали и полировали. Но булатный клинок, сабля, меч — это не только продукт определенной технологии. Это еще и произведение искусства.
В каждый старинный клинок, кроме умения мастера, вложено искусство и вдохновение. А это вещи неповторимые. Каждый древний клинок делался не часами, а годами. И доводил его мастер до зеркального блеска нередко пальцами своей руки, день за днем, месяц за месяцем. И появлялся от этого блеска в металле таинственный холодок, проникающий в душу прикасающегося к клинку человека, возникало ощущение непостижимого, как всегда при соприкосновении с настоящим произведением искусства.
Секреты этого искусства еще не разгаданы. Но у настоящего искусства должна быть тайна. И может, не стоит разгадывать древнюю тайну изготовления булата, чтобы не исчезло само искусство.
Загрузка…libtime.ru
Булатная сталь с нуля — Статьи о материалах — Каталог статей
Согласно общепринятой современной классификации, булат — это композит на основе соединения железа с углеродом, обладающий резкой физико-химической неоднородностью (и характерным узором вследствие нее), полученный путем расплавления всей массы металла, предназначенного для производства булата, или ее части. Как и дамасская сталь, тоже являющаяся композитом, но полученным методом кузнечной сварки, булат характеризуется более высокими по сравнению с однородной сталью характеристиками, а именно сочетанием высокой твердости и вязкости и возможностью образования микропилы, повышающей режущие свойства. Из определения видно, что булат может быть получен как при полном, так и при частичном расплавлении составляющих, следовательно, возможно получить два вида булата, которые, как будет видно в дальнейшем, кардинально отличаются между собой. Булат, получаемый из равномерно-жидкого расплава, называется ликвационным, так как в основе технологии лежит процесс дендритной ликвации углерода при кристаллизации расплава. Поскольку данная статья посвящена, в первую очередь, описанию технологии изготовления булата для начинающих, здесь я не буду подробно описывать все металлургические процессы, сопутствующие превращению стали в булат. Вкратце процесс дендритной ликвации выглядит следующим образом. При медленной (это обязательное условие) кристаллизации стального расплава молекулы карбида железа выстраиваются в нитевидные кристаллы (дендриты), пронизывающие весь объем будущего слитка, причем, чем медленнее охлаждение, тем разветвленнее получаются дендриты. В ходе дальнейшей кристаллизации на поверхность дендритов начинает осаждаться цементит — самое высокоуглеродистое соединение железа с углеродом (и, соответственно, самое твердое). Процесс кристаллизации дендритов и осаждение цементита обезуглероживает металл, окружающий дендриты, и после полной кристаллизации в слитке обнаруживается резкая неоднородность: сверхтвердые дендриты, покрытые цементитной «броней», окружены мягкой матрицей. Более подробно уяснить для себя суть процессов, лежащих в основе булатной технологии, можно при помощи учебных пособий по современной металлургии. Булат, получаемый с использованием технологии второго типа, называется двухфазным. Данный способ построен на том факте, что чем больше углерода в стали, тем ниже температура плавления этой стали. Соответственно, самую низкую температуру плавления среди соединений железа с углеродом имеет чугун (1250-1150 С º в зависимости от содержания углерода), а самую высокую — чистое железо (1539 С º). Суть технологии заключается в том, чтобы нагреть смесь железа или малоуглеродистой стали с чугуном до расплавления последнего и выдержать, не перегревая, чтобы чугун частично науглеродил малоуглеродистые включения. Получаемый таким методом металл также характеризуется высокой степенью неоднородности. Итак, кратко рассмотрев теоретические основы производства булата, перейдем к практике. Поскольку вся работа будет основываться на расплавлении стали, необходимо решить вопрос о соответствующем нагревательном устройстве. Идеальным устройством, безусловно, будет являться электрическая печь сопротивления с рабочей температурой не менее 1400 С º. У такой печи только два недостатка — высокая стоимость и большой расход потребления электроэнергии. Тем не менее, если у кого-либо из читателей есть возможность использования электропечи, то лучшего нагревательного устройства для плавки булата не найти. Хотелось бы предостеречь от использования для этих целей печей, построенных на индукционном принципе работы, поскольку в них булатная сталь, как правило, не получается вследствие потери неоднородности расплава, происходящей из-за перемешивания жидкого металла индукционными токами высокой частоты. Для тех же, у кого нет возможности работать с электропечью, тоже далеко
не все потеряно. Во-первых, плавка булата может быть успешно проведена
и на кузнечном горне, лишь бы он был большого размера (в горн должно
помещаться 3-4 ведра топлива). Горн для плавки булата лучше
модернизировать. Я рекомендую для этой цели обложить огневую чашу горна
шамотным кирпичом по всему периметру, высотой в два кирпича. Специально для плавки можно самостоятельно соорудить некое подобие шахтной плавильной печи, лучше всего сделать это в земляной яме на открытом воздухе. Для этого дно ямы цилиндрической формы (глубиной около 60 см., диаметром около 40 см.) выкладывается шамотным кирпичом на шамотной глине, тем же кирпичом облицовываются и стенки. В стену примерно на середине высоты вмуровывается труба для подачи воздуха. Из шамотного кирпича, уложенного в металлическую оправу, сваренную наподобие ящика, изготовляется крышка. Устройство для подачи воздуха в такую печь должно быть достаточно мощным. В качестве топлива при плавке булата лучше всего использовать кокс. Кроме вопроса о нагревательном устройстве необходимо решить проблему плавильных тиглей. Для плавки стали идеальны алундовые или корундовые тигли, достать их можно, если хорошо поискать. Можно аккуратно выдолбить или выточить на токарном станке небольшой тигель из шамотного кирпича, оставив толщину стенок 5-6 мм. Возможно слепить тигель нужного объема из смеси шамотной крошки и шамотной глины, но по этому вопросу я рекомендую изучить специальную литературу или проконсультироваться у специалиста. Лично я предпочитаю все-таки использовать огнеупорные тигли фабричного производства. Объем тигля для начала не должен быть большим, лучше всего, если он будет в пределах 200-300 мл. Итак, когда все необходимое оборудование подготовлено, можно приступить непосредственно к процессу. Мы начнем с изготовления булата ликвационного типа (кстати сказать, именно этот тип булата сегодня позиционируется как «настоящий булат»). Химический состав булата может быть самым разнообразным, общих требований здесь два — значительное содержание углерода (порядка 1,5% для начала будет достаточно, хотя содержание углерода в булате может достигать и 3%), и наличие таких легирующих составляющих, как хром или ванадий. Легирующие компоненты нужны для облегчения карбидообразования в расплаве, их процентный состав может варьироваться от нескольких десятых долей процента до нескольких процентов. В этом смысле перед экспериментатором лежит практически бесконечное число вариантов, поскольку любые изменения в химическом составе булата будете влечь за собой изменения в свойствах (в том числе и в узоре) готового металла. Для начала я рекомендую выплавить булат из шихты приблизительно такого состава: 1/3 чугуна (рекомендуется использовать качественный чугун, например, от автомобильных цилиндров), 2/3 стали ШХ15 (шарикоподшипниковая, годятся и шарики, и обоймы). Желательно добавить примерно 1/10 массовую часть стали, содержащей ванадий (например, от гаечного ключа с пометкой «Хром-Ванадий»). Булат такого состава богат легирующими элементами и углеродом, то есть удовлетворяет всем необходимым требованиям. Еще раз отметим, что с весовыми долями компонентов можно экспериментировать, помня простое правило — булат может быть получен практически из любой стали. Все составляющие шихты рекомендуется измельчить на части размером примерно 5х5 мм, или даже меньше, особенно при использовании горна в качестве нагревателя. Во-первых, это уменьшит риск непроплавления отдельных частей, во-вторых, при таком размере частиц тигель может быть набит максимально плотно. После заполнения тигля шихтой на нее укладывается слой битого бутылочного стекла. Стекло служит в качестве флюса, защищая сталь от окисления и вбирая в себя шлаки. Когда тигель набит, он помещается в хорошо разгоревшийся горн так, чтобы края тигля были вровень со слоем углей. Учтите, что в процессе плавки тигель будет погружаться вглубь горна по мере выгорания углей, его необходимо поднимать клещами, а потом добавлять свежее топливо. При этом важно, чтобы тигель не опрокинулся и расплавленная сталь не вылилась. Нагрев следует вести при максимальной интенсивности дутья, чтобы сам тигель и топливо вокруг него были ярко-белыми. На полное расплавление обычно уходит до двух часов времени. Периодически следует аккуратно покачивать тигель в печи кочергой, следя за поверхностью расплава. Когда содержимое тигля при покачивании будет выглядеть абсолютно жидким, без всяких признаков вязкости (как вода), плавку можно считать состоявшейся. Теперь предстоит не менее важная часть процесса — охлаждение. Для получения булата оно должно быть максимально возможно медленным. Электропечь позволяет осуществить строгую изотермическую выдержку (идеальным является охлаждение со скоростью 1 С º в минуту), при плавке в горне приходится полагаться на интуицию. Прежде всего, печь нужно загрузить значительным количеством топлива (порядка 2-х ведер для горна, для шахтной печи — доверху), предварительно подняв тигель вровень со старым, уже горящим топливом. Пусть вас не пугает то, что тигель окажется под слоем угля — от контакта с холодным топливом верхний слой расплавленного стекла в тигле станет вязким и не допустит попадания топлива в расплав. После этого дутье уменьшается до минимума (но не выключается совсем), а горн или печь накрывается сверху крышкой (или просто закладывается шамотным кирпичом). Подобные условия вполне пригодны для дендритной кристаллизации. При слабом дутье масса топлива вместе с тиглем будет медленно, но все же остывать, и через некоторое время (порядка 4-5 часов), когда топливо уже практически сгорит и превратится в шлак, слиток достигнет температуры около 800 С º. После этого медленное охлаждение теряет свое значение, поскольку расплав уже полностью кристаллизовался и дендритная ликвация произошла. Тигель извлекается из горна и охлаждается на воздухе до комнатной температуры. После этого слиток необходимо извлечь из тигля, обычно для этого тигель приходится раскалывать молотком. Внимательно осмотрите слиток — он должен быть плотным, без усадочной раковины. Если плавки и дендритная ликвация прошли успешно, по все поверхности слитка можно рассмотреть довольно крупную кристаллическую фактуру — это первый признак того, что вы на верном пути. Сейчас самое время для того, чтобы прерваться и отдохнуть, потому что вам предстоит самая сложная и важная операция на пути к получению булата — ковка. Ковка булата, как уже было сказано выше, представляет собой довольно трудоемкий процесс, недаром среди кузнецов-оружейников бытует поговорка «Кто ковал — того и булат». Все свойства, присущие булатной стали, приобретаются большей частью во время ковки. Здесь есть одно простое и непреложное правило — ковка должна быть медленной. Перед ковкой выплавленный слиток рекомендуется отжечь. В принципе, можно ковать и не отожженный слиток, но при этом весьма велика вероятность его растрескивания, которое может произойти в любой момент ковки и свести на нет все предыдущие усилия. Отжиг булата производится в течение нескольких часов (но не менее часа) при температуре около 1000 С º (оранжевое свечение). Перегрев слитка до лимонного или, тем более, белого цвета влечет за собой потерю узора, так как карбидные нити растворяются и металл становится однородным. Как писал П. П. Аносов, «потеря узора при ковке составляет вину кузнеца». Слиток, подвергнутый отжигу, охлаждается до комнатной температуры, после чего начинается собственно ковка. Поскольку булатный слиток крайне неудобно удерживать клещами, я рекомендую приварить (лучше всего аргонной сваркой, поскольку металл высокоуглеродистый) к нижней части слитка (она обычно самая «проблемная», поэтому ее не жалко будет потом отрезать или пустить на хвостовик будущего клинка) металлический прут длиной около полуметра, за который можно будет удерживать слиток под молотом рукой. После этого слиток помещается в горящий горн и начинается операция, называемая термоциклированием. Суть ее в том, что слиток нагревается до ковочной температуры (для булата — 900-920 С º — ярко-алое, но без оттенка желтизны свечение), потом охлаждается на воздухе до 650-700 С º (свечение темно-красное, едва-едва заметное), после чего операция повторяется. Перед началом ковки рекомендуется сделать 20-30 циклов. Термоциклирование продолжается и в процессе ковки, то есть ковка начинается с верхней температуры, а на нижней заканчивается, и слиток возвращается в горн для подогрева. Всего на расковку слитка до состояния клинка требуется 100-150 термических циклов. От их количества и точного соблюдения температур зависит качество и узор металла. Учтите, что в течение первых 40-50 циклов ковки булат деформируется очень тяжело, то есть, практически не куется. Потом, когда внутренние напряжения между кристаллами будут преодолены, картина меняется на прямо противоположную — слиток начинает коваться, как пластилин. Есть несколько тонкостей, которые необходимо соблюдать при ковке булата. Когда слиток доведен до квадратного сечения, можно приступать к операциям, влекущим за собой усложнение узора. Для этого поковку нужно деформировать участками, чтобы кристаллы интенсивно перемешивались и переплетались между собой. Вариантов того, как это сделать, достаточно много. Самый простой — так называемая ковка «винтом». Суть этого метода в том, что заготовка подается под боек участками по 1-2 см от себя с проворотом на 90 после каждого удара. После этого все четыре грани проглаживаются и процесс повторяется. Более сложный метод – «косая ковка». Поверхность граней для этого набивается крест-накрест тупым зубилом или узким бойком обычного молотка, после чего опять-таки следует простая плоская ковка для сглаживания неровностей. Можно также скрутить заготовку вдоль продольной оси, как при изготовлении крученого дамаска, или насверлить поверхность на небольшую глубину с последующим проглаживанием. Все эти методы позволяют улучшить не только узор, но и качество металла. Как правило, после обычной ковки, когда слиток сначала проковывается до квадратного сечения, а потом расковывается в пластину, получается полосатый узор, а при ковке молотком с закругленным бойком — волнистый. Ковка «винтом» позволяет получить сетчатый узор, а косая ковка — коленчатый, когда на местах пересечения надрубов прямые пряди линий булатного узора образуют своеобразные гроздья. В любом случае, как и при изготовлении дамасской стали, различные виды деформации булата оставляют широкое поле для экспериментов. Следует отметить, что при изготовлении булатного клинка недостаточно просто протянуть слиток на пластину, из которой потом выточить клинок. Крайне рекомендуется спуски будущего клинка тоже оттягивать путем ковки, чтобы металл лезвия уплотнялся, а сверхпрочные карбиды концентрировались на режущей кромке. После ковки необходимо сошлифовать со всей поверхности клинка слой толщиной около полмиллиметра — этот слой обезуглерожен в процессе ковки и не обладает в полной мере булатными свойствами. Закалка производится в масле с нагрева до 850-900 С º, то есть с той же температуры, при которой вы начинали ковку. Рекомендуется применение зонной закалки, когда закаливается только лезвие, а обух остается «сырым». Отпуск клинка можно производить в обычной духовке при температуре около 300 С º, когда на клинке образуется побежалость соломенно-желтого цвета. Правильно изготовленный и термообработанный клинок из булата рекомендованного мной в первой части статьи состава должен с хрустом резать стекло сразу после закалки и слегка царапать после отпуска, обладая при этом значительной долей упругости. Травление для проявления узора производится в растворе хлорного железа в несколько этапов по 5-10 секунд с промежуточной промывкой и протиркой легким полирующим средством (например, пастой ГОИ самой мелкой зернистости). Такова технология производства классического ликвационного булата. Как уже было отмечено ранее, существует также другая группа технологий, позволяющих получать литую неоднородную сталь, которую принято называть «двухфазным булатом» или «фарандом» (именно так назвал подобную сталь арабский историк 10 века Аль Бируни). Технология получения двухфазного булата построена на разнице температур плавления сталей с различным содержанием углерода. Суть метода такова: в расплавленный чугун или высокоуглеродистую легированную сталь добавляют мелко измельченное чистое железо в таком количестве, чтобы его частицы (раскаленные, но все еще твердые из-за более высокой температуры плавления) заполнили весь объем тигля, а пространство между ними было заполнено высокоуглеродистым расплавом. После некоторой выдержки, при которой углерод из расплава частично диффундирует в железо, полученный металл проковывают. Сложность данного метода заключается в том, чтобы не перегреть металл, что может повлечь за собой расплавление железа и гомогенизацию слитка. Я приведу здесь примерную технологию изготовления булата данного типа, поскольку вариантов здесь великое множество. Безусловно, при наличии электропечи задача существенно упрощается, поскольку имеется возможность выставить постоянную температуру нагрева, чуть выше точки плавления чугуна и значительно ниже температуры плавления железа. На открытом огне дело обстоит несколько сложнее. Во-первых, нужно точно рассчитать весовые доли чугуна и железа, исходя не только из желаемого количества углерода, но и из геометрии. Как правило, оптимальным является соотношение 2 части железа на 1 часть чугуна. Чугун лучше использовать максимально высокоуглеродистый и, следовательно, максимально легкоплавкий. Сначала в тигле расплавляется весь чугун, покрытый тонким слоем флюса в виде битого стекла. Когда металл будет полностью жидким, дутье нагревательного устройства уменьшается, но так, чтобы расплав не начал застывать. После этого в тигель мелкими порциями загружается железо, лучше всего в виде самых мелких гвоздей (во-первых, железо в гвоздях качественное, во-вторых, такой размер и форма является идеально подходящими). После добавления в тигель каждой порции (для этой цели придется изготовить некое подобие ложки на длинной ручке) гвозди, еще холодные и плавающие на поверхности расплава, утрамбовываются в расплавленный чугун кочергой или просто изогнутым под прямым углом железным прутом, делается перерыв в 1-2 минуты, чтобы расплав восстановил свою температуру и. следовательно, жидкотекучесть, и добавляется следующая порция. После того, как все железо «ушло» в тигель, я рекомендую произвести замедленное охлаждение, правда, более быстрое, чем при изготовлении ликвационного булата. Достаточно будет просто засыпать тигель сверху слоем топлива, дать ему разгореться при слабом дутье, выключить подачу воздуха и дать тиглю остыть вместе с печью до комнатной температуры. Дальнейшая обработка полученного металла аналогична ковке ликвационного булата, только понижается температура отжига (до 900 С º), и исключается термоциклирование до ковки. Перегрев данного сорта булата выше красного цвета каления крайне нежелателен, так как высокоуглеродистые чугунные прослойки при температуре более 1000 С º начинают размягчаться, а потом расплавляются, вследствие чего слиток буквально «распадается на составные части». При температуре до 900 С º этот металл очень хорошо куется, а после закалки выдает весьма приличную твердость. Итак, в данной статье были приведены некоторые технологии изготовления булатной стали. Я хочу еще раз подчеркнуть, что эти технологии являются базовыми. Зная основные принципы производства булата, мастер может без конца их совершенствовать. Надеюсь, этот путь увлечет читателей, и тем, кто захочет испробовать сказанноеИсточник: http://Общероссийская газета «Пять охот» |
kras-foundry.ru
Как из булата делаются ножи
Илья Куликов – известный в кругах оружейников ярославский кузнец. В наше время кузнецом удивить кого-либо трудно, но чтобы вам было интересней, я скажу, что он необычный кузнец. Это не ремесленник, а настоящий Мастер, шутя делающий потрясающие по красоте вещи из булатной и дамасской стали.
Давайте заглянем в гости на чашку чая и посмотрим на работу Мастера. Авось и секрет какой выведаем
01.
И булат, и дамаск это очень близкие по духу неоднородные красивые стали. Дамаск получается за счет сковывания нескольких пластин различных металлов. Берутся несколько тонких пластин и многократно проковываются, металлы свариваются и получается дамаск. Булатную сталь варят. В составе и пропорциях сплава и состоит один из секретов этого металла. На фото как раз слитки булата, можно сказать, только что из тигля.
02.
Во время варки важна любая мелочь, сплав должен свариться, но не быть передержаным на огне, соль и перец по вкусу. Дальнейшие действия зависят от предпочтения мастера. Кто-то предпочитает расковывать весь слиток, кто-то режет его вдоль или поперек, от этого будет зависеть будущий рисунок и прочность клинка. Илья предпочитает резать на четыре части, как апельсин.
03.
В слитке рисунок металла напоминает срез дерева, просто круги. Такой рисунок мало кому интересен, поэтому от правильности расковки зависит не только прочность, но и будущий рисунок прожилок.
04.
Вы думаете, Илья покажет нам какие-то секреты? Конечно нет, тренироваться будем на водопроводных трубах! Это, конечно, шутка. Труба приваривается на первоначальном этапе для удобства хвата.
05.
Булатная сталь пришла к нам из Индии, где люди десятилетиями могут медитировать или месяцами делать один меч. У старых индусских кузнецов и молоты больше на молоточки походили, и времени видимо больше было.
06.
Наши кузнецы активно использовали труд подмастерьев. Мастер знал куда бить, ученик умел держать кувалду. Такой дедовский способ значительно сокращал время изготовления, но все равно был не очень-то быстрым.
07.
На помощь современным кузнецам приходит кузнечный молот. Во времена Аносова, крестного отца российского булата, это были огромные паровые махины. Почти как паровозы, только громче. Сейчас у кузнецов в почете оставшиеся после ликвидации советских заводов пневматические молоты. Не так будоражащие воображение, как паровые, но не менее производительные.
08.
Несколько нагревов, несколько подходов и четвертинка булата превращается в прямоугольную пластину-заготовку. Вручную на это действо уйдет полдня, механизированным способом минут десять-пятнадцать. А у древних индусов не один день.
09.
Чем мне понравился Илья, так это юмором и работой с деталями. Многие кузнецы мягко говоря, халтурят, не проковывая невидные глазу места, а то и вовсе “экономя” металл, приваривая вместо хвостовика болты и гвозди. А чего, он же все равно в рукоятке, никто не увидит.
10.
Тут все по-честному. Будьте уверены, что нож от Куликова сделан на совесть и потаенных “косяков” в нем нет. Кстати говоря, спасибо Илье за ликбез, когда я недавно был на производстве ножей в Златоусте, то некоторыми вопросами все же поставил людей в тупик
11.
Про златоустовских ремесленников я еще расскажу, именно там в начале XIX века Павел Петрович Аносов развернул промышленное производство литого булата для нужд российской армии.
12.
При расковке кузнец точно знает, какая сторона будет режущей, а какая станет обухом. Острием делают ту сторону, которая была внешней в слитке. Обратите внимание: вдоль клинка идет как-бы трещинка. На самом деле это “схлопнувшаяся” внешняя стенка слитка.
13.
Один из вопросов, который возникает, почему же булат, который в позапрошлом и начале прошлого века производили тоннами и про который сложено столько стихов и сказок, почему он стал такой редкостью в современном мире? Дело в том, что сейчас существует огромное количество узкоспециализированных сплавов, более простых в изготовлении, более дешевых и менее капризных. Но по совокупности свойств, ценящихся при изготовлении холодного оружия, булатная сталь по сей день остается одним из лидеров.
Кроме того, при изготовлении клинка из такой “самоварной” стали кузнец вкладывает в изделие не только умение, но и немного души, а клинок, в свою очередь, может удивлять даже своего создателя
14.
Почему же у булата и дамаска такие уникальные свойства? Все дело в неоднородности сплава. Металл с низким содержанием углерода более мягок, высокоуглеродистый наоборот, более тверд и лучше затачивается. При расковке булата и дамаска эти виды металлов смешиваются и сохраняют красивейший узор из линий. После закалки клинок приобретает и прочность, и гибкость одновременно. Кроме того такая сталь отлично держит заточку – мягкий металл стачивается, а высокоуглеродистый создает режущую кромку из мелких, не различимых глазу, зубчиков.
15.
Конечно же мифы о волшебной силе булатной стали не более чем мифы. Булатный меч не был мечом-кладенцом, режущим доспехи как масло. Более того, многие историки сомневаются в правильности названия дамасской стали.
16.
Город Дамаск никогда не был кузнечным или металлургическим центром. Это был огромный рынок, куда свозились товары с востока для продажи на запад. Булат и дамаск производился в Сирии, Персии и Индии, а в Дамаске просто продавались.
17.
Да и качество средневековых изделий, по словам Ильи, не очень впечатляет. Есть единичные экземпляры, которые и выставлены в музеях, а в запасниках лежат тонны булатного ширпотреба, которым собственно и воевали.
18.
Понятное дело, что такой трудоемкий процесс с помощью ручного труда не мог не отразиться на качестве. Ведь требовались огромные объемы относительно недорогого и надежного оружия и на мелкие недочеты глаза закрывали.
19.
Илья ножи делает не спеша, как я уже говорил, с вниманием к деталям и по-хорошему дотошно. В последнее время очень редко берется за эксклюзивные вещи, чаще делает уже проверенные модели.
20.
Такой подход объясняет очень просто. Чтобы сделать эксклюзивный надежный и удовлетворяющий требованиям булатный нож сил и времени надо затратить столько же, как и на изготовление нескольких проверенных моделей.
21.
Конечно же это не значит, что Илья делает два-три вида ножей и все. У него постоянно какие-то идеи, какие-то новые виды клинков в работе, какие-то у знакомых в “тест-драйве”. При таком подходе про каждый клинок он может сказать, что гарантирует его качество.
22.
Пока свежевыкованный клинок остывает и ждет дальнейшей обработки, посмотрим дамаск. И дамаск, и булат это не название какого-то конкретного сплава, а скорее название процесса, с помощью которого этот сплав получен. Брусок слева это дамаск из трех мягких металлов, который используется при изготовлении рукоятей. Кстати, рукояти Илья тоже делает сам. Раньше этим занимался краснодеревщик, но “хочешь хорошо – сделай сам”.
А справа брусок из метеоритного металла. Это действительно когда-то был метеорит, очень редкий металл.
23.
Единственный в мире, как говорит Илья, метеоритный нож. Внутренний слой из булата, а внешние слои из метеорита. Вид пока что страшненький, ну да на то он и экспериментальный
24.
Следующим этапом является обдирка и грубая шлифовка на наждачной ленте. Чисто теоретически клинок можно выковать практически идеально, останется только отшлифовать, но это слишком долго. Кроме того снятие слоя металла с боков добавляет оригинальности рисунку булата.
25.
Хоть в кузнице и нет главного инженера, но охране здоровья уделяется должное внимание. Еще бы, оно одно и свое, а кузнечное дело считается для легких одним из самых вредных.
26.
Вот так, с шутками и прибаутками, почти что родился новый нож. Мы не посмотрели процесс варки булата, и не посмотрим процесс закалки, но тут уж лучше Мастеру не мешать.
27.
Вот вкратце то, что мы видели: слиток булата, четвертушки, пластина-заготовка, откованный клинок, клинок после первичной грубой обдирки и клинок, подготовленный к закалке и шлифовке.
Как говорит Илья, заказчику полуфабрикат лучше не показывать, а отдать сразу готовый нож. В чем-то я с ним соглашусь
28.
Но даже без закалки его можно использовать в качестве стеклореза. Гусары?
29.
Моя дочка получила настоящий оберег из рук настоящего кузнеца – настоящий кованый гвоздь! Лисычу подарок понравился
30.
Наш клинок все еще является заготовкой, ему еще предстоит закалка, шлифовка, травление, заточка. Конечно же будет красивая функциональная рукоять и ножны. И любящий, ценящий хозяин. А иначе зачем?
Если вы захотите купить хороший нож или почитать интересные статьи о кузнечном деле и булатной стали, добро пожаловать на сайт Ильи Куликова bestbulat.ru. А еще там есть фотографии его лучших работ, например вот этой “Бухары”.
Источник
kak-eto-sdelano.ru