Композитные лопасти » Военное обозрение

В настоящее время американские военные заняты оснащением парка своих вертолетов углеродно-волоконными композитными (карбоновыми) лопастями, так как эти новые материалы обладают повышенным сроком службы, хорошо переносят повреждения, у них отсутствуют проблемы с коррозией, и они обладают высокой надежностью.
Крайним военным вертолетом, оборудованным композитными лопастями, стал Boeing AH-64D Апачи Блок III. В Форт-Ирвине, штат Калифорния, Апачи Блок III прошел первоначальные эксплуатационные испытания и оценки, продемонстрировав тем самым новые технологии и их возможности.
Одним из ключевых аспектов этих возможностей является повышение летно-технических характеристик и надежности главного ротора с лопастями из углеродного волокна, однако, по мнению руководителя программы Апачи Блок III подполковника Даниэля Бэйли (Daniel Bailey), использование таких материалов вряд ли остановится только на лопастях. «Лопасти являются первым очевидным шагом», — сказал он изданию Defence Helicopter.
Структурный элемент
Хотя такой важный летный компонент как лопасти может показаться странной отправной точкой для внедрения новых технологий, но именно здесь в последние годы американские военные оттачивали свои навыки в композитных материалах. Бейли указывает на то, что эти материалы будут широко представлены на американских военных «вертолетах завтрашнего дня»: «Следующим шагом станут композиты в фюзеляже, и мы уже идем по этому пути».
Апачи также получит новый хвостовой ротор примерно в следующем году. Вне зависимости от процесса Блок III, «наша программа композитных хвостовых роторов продолжается. Это параллельная программа Блок III, — объяснил Бэйли. — Мы находимся на заключительной стадии квалификации, но нам ещё предстоит провести множество летных испытаний. Вероятно, уже через год Апачи будет оснащен такой системой».
Новые хвостовые лопасти также будут установлены на модернизированные модели Блока II . Эта замена традиционных лопастей несущего и рулевого винтов происходит благодаря устареванию некоторых технологий. Эти лопасти, первое использование которых датируется 1970-ми годами, уже не были полностью металлическими. На вертолетах AH-64A и D Блок I и II для лопастей несущего и рулевого винтов используется композит из металла и стекловолокна.
В машиностроении композитным принято считать материал или структуру, состоящую более чем из одного элемента. Лопасти Апачи сделаны из экзотических сплавов в виде нержавеющей стали марки AM 355. Инженеры Boeing использовали различные многотрубчатые конфигурации AM 355, ламинированные и связанные вместе с трубками из стекловолокна в качестве препятствия распространению трещин, что придавало конструкции достаточно прочности для удовлетворения армейским требованиям по живучести. Эта сложная конструкция также является дорогой.
Нынешние композитные лопасти основного и хвостового винтов, представленные на Блоке III и его параллельной программе, состоят из углеродного волокна в полимерной матрице, именно это обычно имеют в виду, когда говорят о композитах.
Улучшенная конструкция
Углеродные волокна демонстрируют улучшения в том, как они изготовлены и как они функционируют. «По средствам изменения ориентации волокон и количества слоев и наполнителей вы можете довести композитные лопасти до уровней, которые были недосягаемы с металлами. По сути, вы можете изготовить лопасть с точки зрения её крутки, её аэродинамического профиля или функции хорды, оптимизируя её летные характеристики», — объяснил главный инженер вертолетных программ Боинга Джон Шиблер (John Schibler).
В композиционных материалах из углепластика слои из волокон часто расположены поочередно друг к другу под прямым углом. Правильно выбирая направление волокон в этих слоях, можно добиться необходимых характеристик в конкретных направлениях и областях.
«Преимущества заключаются в прочности материала и в том факте, что при равной прочности можно обеспечить до 30% снижения веса (по сравнению с металокомпозитами). При одинаковом весе он обеспечивает гораздо более высокую жесткость. Но обычно мы говорим об уменьшении веса», — сказал Даниэль Кагнатель (Daniele Cagnatel), вице президент современных композитных материалов GKN Aerospace North America. Компания поставляет фирме Сикорский современные углеродные волокна для лопастей основного ротора вертолета Black Hawk.
Кроме улучшения жесткости и прочности, Шиблер указывает и на экономическую выгоду: «Мы производим лопасти по сравнительно низкой закупочной стоимости, а также с низкими эксплуатационными расходами и более выгодной ремонтопригодностью».
Фирма Сикорский производит лопасти несущего и рулевого винтов с использованием лонжеронов из графитной смолы, оплетенных стекловолокном или углеродным волокном. Алан Валинг (Alan Walling), генеральный директор композитных лопастей Сикорского, сказал: «Сикорский способен производить полностью композитные лопасти несущего винта всего за треть времени, необходимого для производства металлических лопастей. При производстве композитных лопастей остается значительно меньше химических отходов. Это происходит потому, что металлические лопасти требуют травления в кислотной ванне для обеспечения необходимых летно-технических характеристик лопастей в течение долгого времени».

Улучшенные лопасти
По мнению Кагнателя: «Выбор углеродных волокон для лопастей является обязательным. Существующая структура лопастей доказала себя на практике, где углеродное волокно улучшило летно-технические характеристики по сравнению с металлом».
Выбор лопастей несущего винта Апачи Блок III, изготовленных из углеродного волокна, начался с программы Affordable Apache Rotor Program (AARP). В 2004-ом году Boeing завершила испытания лопастей в рамках программы AARP, доказав, что новые лопасти будут дешевле, прочнее и, с точки зрения усталостной долговечности, смогут служить в два раза дольше по сравнению с существующими металлическими лопастями. Бейли пояснил, что в 2006-ом году лопасти AARP были удлинены на 15 сантиметров для повышения летно-технических характеристик, а в 2008-ом году они были испытаны на Apache, в то время как квалификация лопастей Блок III была завершена в 2011-ом году.
«Композитные лопасти несущего винта для программы Апачи Блок III в настоящее время находятся в производстве. Мы изготавливаем около 20 лопастей в месяц и в ближайшее время нарастим их производство до 40 и до 60», — сказал Шиблер.
В 2013-ом году Блок III будет введен в эксплуатацию в 1-ом ударно-разведывательном батальоне американской армии (1-1 ARB), боевой авиационной бригаде, 1-й пехотной дивизии на базе Форт-Райли, штат Канзас. В мае пять вертолетов Апачи Блок III прибыли в 1-ый ударно-разведывательный батальон для подготовки пилотов и служб технического обслуживания, дополнительные вертолеты прибудут в ближайшие месяцы.
Британская армия летает на вертолетах моделей Апачи Блок I, но они могут быть модернизированы до уровня Блок III. Принятие решения по этому поводу ожидается в декабре. Если решение о модернизации до уровня Блок III будет принято, то Апачи Великобритании также могут получить лопасти несущего винта от британской экспериментальной программы ротора (British Experimental Rotor Programm IV, BERPV IV). Программа BERP IV была завершена в 2007-ом году, и композитные лопасти летают на Eh201 Merlin Mk 3 Королевских ВВС.
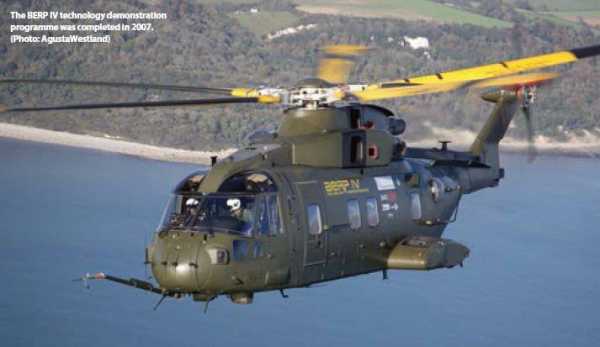
Испытаны и проверены
Тем не менее, это не первый европейский военный вертолет, использующий карбоновые лопасти. Предшественник Eurocopter, Aérospatiale утверждает, что эта честь выпала на вертолет SA 330 Puma, летающий с 1970-х годов. С тех пор этот тип используется многими вооруженными силами, включая французскую армию и ВМС США. Композитные хвостовые лопасти также используются на вертолетах AS532 Cougar, AS565 Panther, NH90 и Tiger.
Сикорский UH-60M Black Hawk использует углеродные композитные лопасти несущего винта с 2008-ого года. Из вертолетов Сикорского только MH-60R и MH-60S Seahawk имеют лопасти несущего винта из металлического (титанового) лонжерона.
Подполковник Билли Джексон (Billy Jackson), руководитель программы модернизации UH-60M Black Hawk, сказал: «Мы поставили в войска 384 вертолета UH-60М, Сикорский поставил около 400 вертолетов UH-60М, и они находятся в эксплуатации со второй половины 2008-го года. Некоторые из них уже вернулись из своего второго развертывания в Афганистане».
Армия использует более широкие композитные лопасти несущего винта, также известные как лопасти с широкой хордой благодаря их улучшенным весовым характеристикам. Экономия в весе составила 204 килограмма. «Это было основной причиной создания композитных лопастей, а не создание их просто потому, что они композитные. Главное — это их летно-технические характеристики», — объяснил Джексон.
«В течение некоторого времени они работают на Сикорском S-92 в несколько иной конфигурации, благодаря этому у нас уже был хороший объем данных. В решении перейти к полностью композитным лопастям не было много риска», — продолжил он. Фирма Сикорский применила полностью композитные лонжероны и обшивку лопастей несущего винта на своих вертолетах S-92 в конце 1990-х годов.
Летно-технические характеристики вертолетов UH-60M были проверены при двух развертываниях в Афганистане, и Джексон настаивает, что они показали хорошие результаты: «В настоящее время мы заняты сбором данных о надежности лопастей. У нас были поврежденные лопасти, а также отремонтированные и восстановленные. Что касается вопроса, обнаружили ли мы трещины в лопастях или непредвиденные сбои по причине новых композитных конструкций, ответ- нет». Основываясь на нынешнем успехе, следующим шагом могут стать полностью композитные цельноповоротные стабилизаторы.

Планы по уменьшению веса
В дополнение к тому что пояснил Бейли, что лопасти были первым шагом, а композитный фюзеляж являются следующим, Джексон сообщил: «Мы ищем другие области применения композитных материалов. Сейчас мы разрабатываем полностью композитный цельноповоротный стабилизатор, который обеспечит значительное снижение веса».
Армия приступила к разработке композитной хвостовой балки вертолета Black Hawk с целью снижения её веса, однако в настоящее время особый акцент делается на создании полностью композитного цельноповоротного стабилизатора, включающего внутренние компоненты. «Мы намерены сделать полностью композитный цельноповоротный стабилизатор для значительного уменьшения веса в области вертолета, имеющей основное воздействие на центр тяжести вертолета».
Джексон заявил, что, как уже отмечалось в предложении фирмы Сикорский, решение о создании полностью композитного цельноповоротного стабилизатора не было обусловлено стремлением улучшить его летно-технические характеристики, а лишь ставило цель сократить расходы на его производство.
«Мы ещё должны выполнить некоторые испытания, баллистические и другие виды летно-технических испытаний с целью убедиться, что новое изделие будет настолько же хорошо или даже лучше оригинального, а затем принять финансовое решение о том, как мы хотим внедрить его на существующую платформу, внедрить его в перспективное производство или пополнить им список существующих запасных частей».
Компанией, поставляющей композитную хвостовую балку, но не лопасти хвостовых винтов, является BLR Aerospace из штата Вашингтон. Вице-президент компании по сбыту и маркетингу Дэйв Мароне (Dave Marone) подтвердил изданию Defence Helicopter, что его компания производит полностью композитную хвостовую балку по заказу одного из военных заказчиков, но не согласился предоставить дополнительную информацию.
Планы на будущее
Ещё одним вертолетом, которому придется ждать до 2016-го года, чтобы получить композитные лопасти несущего винта из углеродного волокна, является американский армейский CH-47 Chinook. «Новые композитные лопасти называются Advanced Chinook Rotor Blade (ACRB). Программа успешно завершила стадию критического анализа проекта (critical design review, CDR) в январе 2012 года», — сообщил руководитель проекта модернизации CH-47 Chinook подполковник армии США Джо Хочерл (Joe Hoecherl). Летные и баллистические испытания были завершены в 2011-ом году.
Программа ACRB принесет изменения в форме лопастей и их летно-технических характеристиках, не затронув их крепления. «Эти лопасти будут взаимозаменяемыми на всех вертолетах Chinook», — сказал Хочерл. Были завершены масштабные тестирования в аэродинамической трубе, которые продемонстрировали, что новые лопасти способны обеспечить до 900 кг дополнительной вертикальной тяги, что позволит вертолету зависать с полной загрузкой на высоте в 1200 метров при температуре воздуха в 35° C.
Лопасти ACRB в аэродинамической трубе.
Предсерийное производство лопастей запланировано на апрель 2014-го года, летные испытания на третий квартал 2015-го года, а серийное производство на 2016-ый год. В феврале нынешнего года было объявлено, что Boeing разрабатывает композитные лопасти с повышенным сроком службы и требующие значительно меньше времени, необходимого для устранения несоконусности лопастей несущего винта и их балансировки. Эти лопасти также могут быть установлены на модели вертолетов CH-47D, однако эти вертолеты запланировано списать уже к 2019-му году.
Интеллектуальные композиты
Скорее всего, к 2019-му году лопасти из углеродного волокна потребуют более сложного подхода для достижения дальнейшего улучшения летно-технических характеристик. Промышленность сходится во мнении, что лопасти не будут состоять только из углеродного волокна. Кагнатель считает, что в них будут встроены датчики, способные следить за состоянием лопастей и позволяющие более точно прогнозировать срок их службы.
«Тенденции всё более указывают на встроенные системы, элементы подогрева передней кромки лопасти, а также датчики напряжения и деформации лопастей. В будущем такие датчики будут составной частью лопастей, нежели их внешними элементами», — сказал он.
Тем не менее, на лопасти также могут быть установлены движущиеся части. Директор по исследованиям и профессор инженерного факультета Бристольского Университета Пол Уивер (Paul Weaver) как раз работает над таким проектом для правительства Великобритании. Проект называется Интеллектуальные Реагирующие Композитные Структуры (Intelligent Responsive Composite Structures, IRCS). «Национальное агентство инноваций финансировало проект, завершившийся два года назад изменением формы закрылков», — сказал он изданию DH.
Национальное агентство инноваций принадлежит британскому правительству, оно занимается финансированием исследований, разработок и их коммерциализацией. В рамках программы IRCS было обнаружено, что щиткообразное устройство на задней кромке лопасти может быть использовано для повышения летно-технических характеристик при переходе от зависания к горизонтальному полету.
Фирма Сикорский также занята исследованиями в этой области. Она разрабатывает активные технологии лопастей несущего винта совместно с Министерством обороны США. На сегодняшний день не планируется установка этих устройств на существующие лопасти.
Американские военные не являются первопроходцами в развертывании углеволоконных лопастей, но тот факт, что они активно оснащают свой вертолетный парк новыми лопастями, подтверждает, что новые композиты активно внедряются в жизнь. Для Бейли важность углеродного волокна является очевидной: «Эти технологии будут стимулировать развитие будущих армейских вертолетов, будь то новые Apache, Black Hawk или Chinook».
topwar.ru
Лопасти несущего винта вертолета — О самолётах и авиастроении
Условия работы лопасти несущего винта вертолета во многом отличаются от условий работы крыла самолета. Главная изюминка в том, что действующие на нее нагрузки являются переменными во времени. Исходя из этого при выборе материала элементов лопасти в качестве основных выдвигаются следующие требования:
— усталостная прочность: трещино стойкость (сопротивление распространению усталостной трещины) и не сильный чувствительность к концентраторам напряжений;
— неизменность механических их материала соединений и свойств элементов от заданного времени эксплуатации, атмосферных условий и температуры внешней среды;
— технологические требования: возможности производства по обеспечению заданных форм сечения элементов конструкции; увеличение ресурса элементов конструкции способами упрочнения; контроль за качеством соединений и заданными геометрическими
размерами при изготовлении элементов конструкции в ходе сборки лопасти; ремонтопригодность конструкции лопасти в ходе ее эксплуатации.
Не считая перечисленного, нужно учитывать цена технологического процесса и материала изготовления лопасти и цена ее эксплуатации.
С учетом вышеизложенных требований выбирают тот материал, а что имеет большие удельную прочность — и удельный Е модуль упругости — р.
При формировании лонжерона лопасти из гибридных композиционных материалов стремятся к большой их совместимости с материалом матрицы, к примеру, по величине динамического удлинения, степени адгезии, по коэффициенту линейного и объемного расширения, влагоёмкости, времени старения, чувствительности к ударным нагрузкам.
Чувствительность к ударным нагрузкам определяется величиной ударной вязкости. Для волокнистых композитов ударная вязкость характеризуется отношением. Одним из способов увеличения ударной вязкости композитов есть введение в их состав более прочных и менее твёрдых волокон, к примеру стеклянных либо органических — в углепластики.
В ходе развития вертолетостроения основной силовой элемента лопасти — лонжерон — выполнялся из дерева, легированных сталей, алюминиевых сплавов, нержавеющей стали, титановых сплавов. На данный момент обширно практикуется изготовление лонжерона из композиционных материалов.
Агрегаты каркаса — обшивка, нервюры, хвостовой стрингер, ранее изготовляемые из фанеры, полотна, алюминиевых сплавов, в современных лопастях изготавливаются кроме этого из КМ.
Дерево отыскало использование в практике Ухтомского вертолетного завода им. Ы.И. Камова во время его становления.
Определяющими в выборе этого материала являлись следующие мысли: древесина малочувствительна к концентраторам напряжений, трещино стойкая; она не требует сложного технологического оборудования при изготовлении каркаса и лонжерона лопасти; затраты на изготовление лопасти не громадны.
Центральная часть лонжерона выполнялась из дельта- древесины (склеенные узкие страницы древесины), носовая часть профиля складывалась из комплекта склеенных сосновых реек. Хвостовая часть представляла собой каркас из фанерной обшивки, приклеенной к пенопласту. Поверхность лопасти покрывалась полотном и влагостойким лаком.
В ходе эксплуатации выявились значительные недочёты древесной лопасти:
— не обращая внимания на влагостойкое покрытие поверхности лопасти элементы конструкции насыщались влагой, что приводило к трансформации центра тяжести сечения (смещался назад) и уменьшению критической скорости флаттера лопасти;
— пропитка антисептиками не ликвидировала в ходе эксплуатации гнилостного разрушения древесины, при том что ее механические особенности ухудшались.
В практике Столичного вертолетного завода им. М.Л. Миля в лопастях НВ использовалась смешанная конструкция — лонжерон выполнялся из металлической трубы, а в элементах каркаса употреблялось полотно и дерево.
Требования прочности, аэродинамики и жёсткости с учетом технологических возможностей стали причиной необходимости трансформации форм сечения лонжерона по радиусу с цилиндрической на эллиптическую. Металлургическая индустрия не обладала оборудованием для создания данного лонжерона из одной заготовки. Исходя из этого конструкторы вынуждены были ввести телескопические стыки, соединенные металлическими заклепками, с применением упрочняющей разработке (дорнирование отверстий), плавные переходы жесткости в месте стыка, продольную шлифовку внутренней и внешней поверхностей каждой части лонжерона.
Учитывая темперамент аэродинамических нагрузок по хорде профиля, переднюю часть профиля лопасти делали из фанеры, а заднюю — из полотна в комлевой части лопасти и фанерной обшивки в средней и концевой ее части.
Аэродинамические нагрузки и центробежная сила, действующая на каркас, через нервюры передавались на лонжерон. Передача моментов и сил на лонжерон осуществлялась через фланцы, приклепанные к стенке и лонжерону нервюры.
В ходе эксплуатации выявился последовательность недочётов принятой конструктивно-силовой схемы лопасти. Наличие заклёпочных соединений и стыков значительно усложнило процесс успехи нужного ресурса лопасти. Применение в хвостовой части без моментной обшивки (полотна) приводило к тому, что под действием внешних аэродинамических центробежной силы и сил воздуха, находящегося в каркаса, значительно искажался профиль лопасти, что ухудшало его аэродинамические характеристики.
Введение дренажного отверстия на нижней поверхности в конце лопасти стало причиной местным утратам на перетекание воздуха в каркаса под действием центробежных сил. Устранение этого недочёта за счет отказа от полотна и переход па фанерную обшивку по всей поверхности лопасти значительно увеличило массу лопасти и сдвигало центр весов лопасти назад. В следствии совместной деятельности конструкторов, металлургов и технологов по устранению отмеченных недочётов был создан лонжерон заданного переменного сечения без стыков, а хвостовую часть лопасти стали выполнять из дюралюминевой обшивки, подкрепленной сотовым блоком, не изменяющей форму под действием аэродинамических нагрузок.
Для трубчатого лонжерона используется в большинстве случаев труба из высоколегированной стали типа ЗОХГСА либо 40ХНМА, закаленной и отпущенной на прочность (с^ = 1100—1300 МПа). По окончании тёплой и холодной прокатки, закалки и формообразования наружная и внутренняя поверхности трубы полируются. На внешней и внутренней поверхностях лонжерона создается наклеп виброударным методом, повышающий предел выносливости до а ю = 280—300 МПа mi» при постоянной части нагружения ат= 200—250 МПа.
В конструкции лопасти, основанной на металлической трубе, лонжерон в большинстве случаев защищен каркасом и не может быть механически поврежден в эксплуатации.
Применение прессованного профиля из дюралюминиевого материала разрешило вырабатывать профиль лонжерона с самоё целесообразным сечением ( 2.3.1). Использование замкнутого профиля, взятого способом прессования (экструзия), ограничил диапазон применения существующих дюралюминиевых сплавов. В ходе прессования происходит разделение материала на две части, исходя из этого в формирующем профиль инструменте (фильере) эти две части должны соединяться и свариваться давлением.
Дабы структура материала в местах сварки не ухудшалась, нужно использовать материал с высокой коррозионной стойкостью, Усталостная прочность дюралюминиевого лонжерона может снизиться из- за недостатков, появляющихся в ходе механической обработки и прессования профиля .лонжерона. Исходя из этого нужно не только наружную, но и внутреннюю поверхности лонжерона упрочнять виброударным методом. Предел выносливости возможно доведен до а = 55—60 МПа при о т= 60 МПа.
Для исключения минимальной возможности коррозионного повреждения прессованных лонжеронов в ходе производства и в условиях эксплуатации нужно использовать гальванические покрытия (к примеру, анодирование) по окончании промежуточных операций его обработки.
Процесс прессования не разрешает изменять форму сечения по заданному закону, исходя из этого требуемую высоту профиля по длине лопасти возможно обеспечить лишь за счет фрезерования внешней поверхности. В следствии конструктор имеет возможность разрабатывать конструктивно-силовую план лопасти лишь прямоугольной формы в плане (сужение r| = 1).
Контакт поверхности лонжерона с потоком воздуха стал причиной необходимости защиты данной поверхности от эрозионного повреждения.
Была сделана попытка формирования лонжерона лопасти из многослойного узкого страницы нержавеющей стали, соединенного в монолит при помощи склейки. Предполагалось создание конструкции, владеющей громадной стойкостью к распространению усталостной трещины. Органическим недочётом данной конструкции была невозможность обеспечения качественной устранения и склейки распознанных недостатков клеевых поверхностей.
Лопасти с лонжероном замкнутой формы разрешают применять технические средства постоянного контроля усталостных разрушений материала лонжерона. Совокупность сигнализации повреждения цельнометаллических лонжеронов складывается из заглушек давления и сигнализатора воздуха на финишах лонжерона ( 2.3.2). Внутренняя полость лонжерона заполняется воздухом под давлением, превышающим давление начала срабатывания сигнализатора.
При появления в лонжероне трещины давление воздуха в нем падает. Информация о разгерметизации полости лонжерона поступает от сигнализатора давления в виде выдвижения красного колпачка сильфона, установленного в комлевой части каждой лопасти.
Индикация давления воздуха в лонжеронах в кабину экипажа не выводится, т.к. процесс роста трещины до разрушения лонжерона многократно превышает время максимальной длительности полета вертолета. Контроль за состоянием лопасти осуществляется при меж полетном осмотре по положению сигнализатора.
Давление воздуха в лонжероне создается с учетом температуры окружающего воздуха и с учетом давления начала срабатывания сигнализатора.
В лопастях вертолета Ми-26 металлические трубчатые лонжероны по наружной поверхности облицованы стеклолентой, за счет чего при происхождении трещины в лонжероне исключается возможность обнаружения повреждения лонжерона посредством пневматической совокупности сигнализации. Для обеспечения надежного функционирования совокупности сигнализации повреждения лонжерона на всей протяженности его внешней поверхности укладываются двойные фторопластовые шнуры ( 2.3.3) и по окончании обмотки лентами из стеклоткани производится полимеризация в пресс-форме. Фторопластовые шнуры вытягиваются, образуя воздушные каналы диаметром
2 мм, открытые со стороны внешней поверхности трубы лонжерона. Появление усталостной трещины в зоне воздушных каналов ведет к падению давления в полости лонжерона и срабатыванию сигнализатора. Каналы выполняются двойными по технологическим соображениям — постоянно имеется возможность обрыва фторопластового шнура при его вытягивании из полости длиной 14 м.
Анизотропность композиционных материалов открыла много возможностей применения их в лопастях НВ. Использование КМ разрешает направленно вырабатывать жесткостные характеристики лопасти (изгибные и крутильные) за счет соответствующей ориентации армирующих волокон композита с учетом сложного характера ее нагружения.
Вертолетостроение есть самая передовой отраслью авиационной техники, тут стали смело использовать КМ в таком важном и сложно нагружаемом агрегате, как лопасть НВ.
Эффективность применения КМ в силовых элементах лопастей определяется рядом преимуществ этих материалов если сравнивать с металлами. В частности, аэродинамические и аэроупругие параметры лопастей композитов смогут выбираться не учитывая ограничений, вызываемых технологическими процессами получения катаных, экструдированных (прессованных) либо механически обработанных железных конструктивных элементов.
Композитным конструкциям возможно придать сложные аэродинамические формы, а регулируемая анизотропия материала разрешает создавать требуемую жесткость в пределах заданных аэродинамических и аэроупругих параметров. В следствии достигается громадная аэродинамическая эффективность винтов, определяемая отношением подъемной силы к аэродинамическому сопротивлению.
Посредством КМ, владеющих более большой удельной прочностью, изготавливают лопасти меньшей массы, чем железные. Понижение массы лопастей, со своей стороны, влияет па центробежные силы, инерцию ротора, частотные и другие характеристики.
Регулируемая в широких пределах анизотропия КМ разрешает приобретать нужные конструктивные и демпфирующие параметры лопасти.
Частота собственных колебаний лопасти возможно поменяна не только перераспределением массы, но и выбором армирующих волокон, имеющих низкий либо большой модуль упругости, включая их гибридизацию (смешивание), ориентации и степени армирования армирующих волокон относительно оси лопасти. Крутильная жесткость лопасти возможно значительно увеличена за счет добавления слоев с ориентацией ± 45° относительно размаха лопасти при малом трансформации частот продольных колебаний.
Одним из вероятных параметров оптимальности панели из КМ, снабжающим минимум ее массы, есть условие совпадения траектории армирования с траекторией большого главного напряжения. В большинстве случаев, КМ является совокупностью однонаправленных либо тканевых слоев с углами ориентации и различными толщинами волокон. Свойства для того чтобы материала определяются особенностями отдельных слоев и структурой.
Действенная реализация преимуществ композитов в конструкциях лопастей требует решения комплекса задач, которые связаны с выбором взаимно согласованных матрицы и (исходных компонентов волокон), определением рациональной структуры материала, соответствующей характеру внешних других воздействий и нагрузок с учетом своеобразных технологических ограничений и свойств материала при разработке элементов лопасти.
Механическое поведение КМ определяется большой прочностью армирующих волокон, прочностью связи и жёсткостью матрицы на границе «матрица — волокно».
Громаднейшее использование взяли стеклопластиковые КМ на эпоксидной матрице. Это разъясняется прежде всего низкой ценой стеклопластика. Предстоящее развитие конструкции лопасти из КМ связано с применением гибридных композиций
— сочетания углеволокна с органоволокном и других аналогичных вариантов.
Углепластик, владея большой прочностью, чувствителен к ударным нагрузкам. Введение менее твёрдого материала и защита поверхности лонжерона от каких-либо повреждений предоставляет возможности широкого применения аналогичных композиций.
Лонжерон с замкнутым коробчатым сечением ?)-образной формы возможно изготовлен способом намотки однонаправленной лентой на оправке. Данный способ изготовления лонжеронов лопасти активно используется при большом серийном производстве, где целесообразно максимально автоматизировать процесс изготовления. В практике ОКБ Н.И.
Камова выбрана разработка изготовления лонжерона частями способом выкладки из разных тканей либо лент однонаправленного материала на оправках.
Страницы материала лонжерона собирают в пакеты и подвергают предварительной опрессовке в автоклаве при низкой температуре. Страницы наряду с этим слипаются, пакеты покупают нужные для предстоящей сборки жёсткость и форму, а полимеризации связующего фактически не происходит. По окончании опрессовки пакеты являются профилем открытого контура.
После этого пакеты планируют совместно с центровочными грузами, комлевыми пластинами и нагревательным элементом в один блок, в которого находится технологическая резиновая пресс- камера. Блок пакетов с пресс- камерой помещают в особую пресс-форму, внутренний контур которой соответствует внешнему контуру носовой части лопасти.
В пресс-камеру подается сжатый азот, а пресс-форму нагревают. Наряду с этим лонжерон получает нужную форму, связующее полимеризуется и все элементы лонжерона прочно склеиваются между собой. По окончании процесса прессования лонжерон извлекают из пресс-формы, удаляют из него пресс-камеру и обрезают припуски.
Таковой метод производства дает возможность приобрести лонжерон замкнутого контура из разных армирующих наполнителей на различных связующих, в любом сочетании с неограниченными возможностями по их размещению в конструкции. К сборочному приспособлению для того чтобы заданного сечения предъявляется ряд условий при назначении режимов давления, нагрева, выдержки и охлаждения при отвердении. Эти требования направлены для исключения остаточных коробления и деформаций за счет температурных неравномерности и напряжений толщин массы и распределения материала в ходе формирования лонжерона.
Тип исходных КМ для лонжеронов выбирается в зависимости от летно-технических данных вертолета. Для малонагруженных лопастей вертолетов употребляется недорогая стеклоткань сатинового переплетения. Для высоконагруженных лопастей употребляются гибридные КМ на базе высокопрочной стеклоткани, технической ткани и углеродной ленты на эпоксидном связующем.
Использование гибридных КМ разрешает главной силовой элемент — лонжерон — изготавливать с фактически любым заданным распределением жёсткостей и масс по длине лопасти.
В силу требований, предъявляемых к лопастям, и учитывая действующие нагрузки, хвостовые секции лопасти должны отвечать следующим требованиям: прочность конструкции, минимальная масса, жесткость конструкции, достаточный ресурс (не меньше ресурса лонжерона лопастей), гладкость аэродинамической поверхности, возможность изготовления в серийном производстве, возможность ремонта в поле и др.
В эксплуатации прекрасно зарекомендовали себя хвостовые секции лопасти трёхслойной сотовой конструкции. Такая секция имеет обшивку, стрингеры и торцевые нервюры из технической ткани на базе органических волокон и заполнитель из сот. Использование в конструкции хвостовых секций самого легкого КМ позволяет снизить массу секций по сравнению со стеклопластиком и расширить ресурс.
Обширный опыт, накопленный при эксплуатации вертолетов «Ка», продемонстрировал, что лопасти из КМ имеют наилучшие эксплуатационные качества. Наиболее значимые из них пребывают в следующем:
— громадный запас прочности при практически неограниченном по условиям выносливости ресурсе. Практический срок работы лопастей из КМ определяется степенью их естественного износа, зависящего от условий эксплуатации;
— увеличение срока работы не только лопастей несущего винта, но и всего вертолета за счет понижения статических и динамических нагрузок в несущей совокупности, благоприятных уменьшения уровня и частотных характеристик вибраций вертолета. Это обеспечивается технологическим процессом, что разрешает изготавливать лонжерон с переменными по длине толщиной стенки и формой сечения, и использовать совместно различные типы армирующего материала с различной ориентацией. Эти наиболее значимые качества дают значительные преимущества не только перед железными лопастями, но и перед вторыми конструкциями лопастей из КМ;
— высокая степень ремонтопригодности. Благодаря полезным особенностям КМ — высокой стойкости к низкой скорости и концентраторам напряжений разрушения материала — достигается доступность и простота ремонта кроме того больших повреждений лопасти в поле;
— высокая стойкость лопастей фактически ко всем видам агрессивных веществ, горючим, ядохимикатам, маслам и пр.;
— стабильность летно-технических черт лопасти в ходе долгой эксплуатации в произвольных климатических условиях. Долгий опыт эксплуатации вертолетов с лопастями из КМ продемонстрировал, что трансформации механических особенностей материала так незначительны, что они не воздействуют ни на летно-технические характеристики, ни на срок работы лопастей.
На характеристики КМ в ходе эксплуатации влияет влажность.
ФОРМИРОВАНИЕ УПРУГО-МАССОВЫХ Черт ЛОПАСТИ НВ
ВЛИЯНИЕ ФОРМЫ ЛОНЖЕРОНА НА Личные ЧАСТОТЫ КОЛЕБАНИЙ ЛОПАСТИ
агрегаты и Узлы техники
Формование лопасти винта вертолета
Увлекательные записи:
Похожие статьи, которые вам, наверника будут интересны:
Несущий винт вертолета
Несущий винт вертолета складывается из втулки и лопастей. Лопасти создают потребную подъемную силу. Втулка является кинематический механизм, снабжающий…
Конструкция лопасти несущего винта вертолета
Лопасти несущего винта вертолета нужно выстроить так, дабы они, создавая нужную подъемную силу, выдерживали все появляющиеся на них нагрузки. И не просто…
Тормоз несущего винта и валы трансмиссии вертолета
Тормоз НВ (ТНВ) рекомендован для сокращения времени остановки НВ и агрегатов трансмиссии по окончании выключения двигателей. Он кроме этого употребляется…
Вал несущего винта вертолета
Вал НВ нагружается моментами и силами от его втулки и крутящим моментом, создаваемым на выходе ГР. Протяженность нала НВ определяется компоновочными,…
Реактивный привод несущего винта вертолета
Основное отличие реактивного двигателя от поршневого пребывает в том, что в реактивном двигателе энергия сгораемого горючего расходуется на создание силы…
Аэродинамика несущего винта
Несущий винт вертолета имеет несколько лопастей (в большинстве случаев, от 2 до 5), соединенных со втулкой. Втулка помогает для передачи крутящего…
stroimsamolet.ru
Из чего сделаны лопасти у вертолета?
силумин титан оболочка
из многослойного пирога
Текстолит, но не из обычной эпоксидки. При чем они не монолитные, а склеены суперклеем из множества слоев (так крепче выходит).
хитрый статегический сплав точный состав которого засекречен у игрушечного из пластмассы )
из углеволокна с наполнением газом-лопасти полые внутри
То что видел я лет тридцать назад на мелком каком-то вертолете: вдоль лопасти примерно по центру — балка прямоугольного сечения (материал мне неизвестен). К ней приклеены соты из фольги (похоже на дюраль, точно не знаю). Отверстия сот ориентированы вертикально. Все это обклеено толстой типа фольгой из материала, похожего на материал сот. На вид цельное. Легкое — невероятно (процентов 90 объема лопасти — воздух). К слову. Вертолеты появились гораздо позже самолетов, помимо прочих сложностей, в т. ч. и из-за того, что не могли научиться делать гибкие длинные лопасти, а жесткие — ломались или были тяжелы. Лопасти самолетного винта — цельнометаллические. По-моему — дюралюминий. Все это было около 40 лет назад. Сегодня — не знаю, наверняка появились новые материалы.
touch.otvet.mail.ru
Конструкция лопасти несущего винта вертолета — О самолётах и авиастроении
Лопасти несущего винта вертолета нужно выстроить так, дабы они, создавая нужную подъемную силу, выдерживали все появляющиеся на них нагрузки. И не просто выдерживали, а имели бы еще запас прочности на всякие непредвиденные случаи, каковые смогут встретиться в полете и при техобслуживании вертолета на земле (к примеру, резкий порыв ветра, восходящий поток воздуха, резкий маневр, обледенение лопастей, неумелая раскрутка винта по окончании запуска двигателя и т. д.).
Одним из расчетных режимов для подбора несущего винта вертолета есть режим вертикального комплекта на любой избранной для расчета высоте. На этом режиме из-за отсутствия поступательной скорости в плоскости вращения винта потребная мощность имеет большую величину.
Зная примерно вес конструируемого вертолета и задаваясь величиной нужной нагрузки, которую обязан будет поднимать вертолет, приступают к подбору винта. Подбор винта сводится к тому, дабы выбрать таковой такое число и диаметр винта его оборотов в 60 секунд, при которых бы расчетный груз мог быть поднят винтом отвесно вверх с мельчайшей затратой мощности.
Наряду с этим как мы знаем, что тяга несущего винта пропорциональна четвертой степени его диаметра и лишь второй степени числа оборотов, т. е. тяга, развиваемая несущим винтом, более зависит от диаметра, чем от числа оборотов. Исходя из этого заданную тягу легче взять повышением диаметра, чем повышением числа оборотов. Так, к примеру, увеличив диаметр в 2 раза, возьмём тягу в 24 = 16 раз громадную, а увеличив число оборотов вдвое, возьмём тягу лишь в 22 = 4 раза громадную.
Зная мощность двигателя, что будет установлен на вертолете для приведения во вращение несущего винта, сперва подбирают диаметр несущего винта. Для этого используют следующее соотношение:
Лопасть несущего винта трудится в сверхтяжелых условиях. На нее действуют аэродинамические силы, каковые ее изгибают, скручивают, разрывают, стремятся оторвать от нее обшивку. Дабы «противостоять» такому действию аэродинамических сил, лопасть должна быть достаточно прочной.
При полетах в ливень, в снег либо в тучах при условиях, содействующих обледенению, работа лопасти еще более усложняется. Капли дождя, попадая на лопасть с огромным» скоростями, сбивают с нее краску. При обледенении па лопастях образуются ледяные наросты, каковые искажают ее профиль, мешают ее маховому перемещению, утяжеляют ее.
При хранении вертолета на земле на лопасть разрушающе действуют резкие трансформации температуры, влажность, солнечные лучи.
Значит, лопасть должна быть не только прочной, но она еще должна быть невосприимчивой к влиянию окружающей среды. Но если бы лишь это! Тогда лопасть возможно было бы сделать цельнометаллической, покрыв ее противо-коррозийным слоем, и задача была бы решена.
Но имеется еще одно требование: лопасть, также, должна быть еще и легкой. Исходя из этого ее изготовляют полой За базу конструкции лопасти берут железный лонжерон, значительно чаще — металлическую трубу переменного сечения, площадь которого неспешно либо ступенчато значительно уменьшается от корневой части к концу лопасти.
Лонжерон, как основной продольный силовой элемент лопасти, принимает перерезывающие силы и изгибающий момент. В этом отношении работа лонжерона лопасти схожа с работой лонжерона самолетного крыла. Но на лонжерон лопасти действуют в следствии вращения винта еще центробежные силы, чего нет у лонжерона крыла самолета.
Под действием этих сил лонжерон лопасти подвергается растяжению.
К лонжерону привариваются либо приклепываются металлические фланцы для крепления поперечного силового комплекта — нервюр лопасти. Любая нервюра, которая возможно железной либо древесной, состоит из стен и полок. К железным полкам приклеивается либо приваривается железная обшивка, а к древесным полкам приклеивается фанерная либо пришивается полотняная обшивка либо к носку приклеивается фанерная обшивка, а к хвостику пришивается полотняная, как продемонстрировано.
В носовой части профиля полки нервюр крепятся к переднему стрингеру, а в хвостовой части — к заднему стрингеру. Стрингеры являются вспомогательными продольными силовыми элементами.
Обшивка, покрывающая полки нервюр, образует собой профиль лопасти в любом ее сечении. самая лёгкой есть полотняная обшивка. Но чтобы не было искажения профиля в следствии прогиба полотняной обшивки на участках между нервюрами, нервюры лопасти приходится ставить частенько, приблизительно через 5—6 см одна от второй, что утяжеляет лопасть.
Поверхность лопасти с не хорошо натянутой полотняной обшивкой выглядит ребристой и владеет низкими аэродинамическими качествами, поскольку ее лобовое сопротивление громадно. В ходе одного оборота профиль таковой лопасти изменяется, что содействует появлению дополнительной вибрации вертолета. Исходя из этого полотняная обшивка пропитывается аэролаком, что по мере собственного подсыхания очень сильно натягивает полотно.
При изготовлении обшивки из фанеры жесткость лопасти возрастает и расстояние между нервюрами возможно увеличено в 2,5 раза если сравнивать с лопастями, обтянутыми полотном. Чтобы уменьшить сопротивление, поверхность фанеры гладко обрабатывается и полируется.
Хороших большой прочности и аэродинамических форм возможно добиться, в случае если изготовить полую цельнометаллическую лопасть. Трудность ее производства пребывает в изготовлении переменного по сечению лонжерона, что образует носовую часть профиля. Хвостовая часть профиля лопасти изготовляется из листовой железной обшивки, которую передними кромками заподлицо приваривают к лонжерону, а задние кромки склепывают между собой.
Профиль лопасти винта вертолета выбирается с таким расчетом, дабы при повышении угла атаки срыв обтекания появлялся на вероятно громадных углах атаки. Это нужно чтобы избежать срыва обтекания на отступающей лопасти, где углы атаки особенно громадны. Помимо этого, чтобы не было вибраций профиль нужно подобрать таковой, у которого бы при трансформации угла атаки не изменялось положение центра давления.
Весьма ответственным причиной для работы и прочности лопасти есть обоюдное размещение центра тяжести и центра давления профиля. Дело в том, что при совместном действии кручения и изгиба, лопасть подвержена самовозбуждающейся вибрации, т. е. вибрации со все возрастающей амплитудой (флаттеру). Чтобы не было вибрации лопасть обязана балансироваться относительно хорды, т. е. должно быть обеспечено такое положение центра тяжести на хорде, которое исключало бы самовозрастание вибрации.
Задача балансировки сводится к тому, дабы у выстроенной лопасти центр тяжести профиля был впереди центра давления.
Рассматривая тяжелые условия работы лопасти несущего винта, нужно подчернуть, что повреждение древесной обшивки лопасти каплями дождя возможно предотвращено, в случае если на протяжении ее передней кромки укрепить листовую железную окантовку.
Борьба же с обледенением лопастей является более непростую задачу. В случае если такие виды обледенения в полете, как иней и изморозь, громадной опасности для вертолета не воображают, то стекловидный лед, неспешно и незаметно, но очень прочно наращивающийся на лопасти, ведет к утяжелению лопасти, искажению ее профиля и, в конечном итоге, к уменьшению подъемной силы, что ведет к резкой устойчивости вертолёта и потеря управляемости.
Существовавшая одно время теория о том, что лед благодаря машущего перемещения лопастей будет в полете скалываться, была несостоятельной. Обледенение лопасти начинается раньше всего у корневой части, где изгиб лопасти при ее машущем перемещении мал. В будущем слой льда начинает распространяться все дальше к концу лопасти, неспешно сходя на нет.
Известны случаи, в то время, когда толщина льда у корневой части достигала 6 мм, а у финиша лопасти — 2 мм.
Не допустить обледенение вероятно двумя дорогами.
Первый путь — это тщательное изучение прогноза погоды недалеко от полётов, обход встретившихся по пути туч и изменение высоты полета с целью выхода из воны обледенения, прекращение полета и т. д.
Второй путь — это оборудование лопастей противо-обледенительными устройствами.
Известен целый рад этих устройств для лопастей вертолета. Для удаления льда с лопастей несущего винта может
быть применен спиртовой противообледенитель, что разбрызгивает на передней кромке винта спирт. Последний, смешиваясь с водой, понижает температуру ее замерзания и мешает образованию льда.
Скалывание льда с лопастей винта возможно осуществлено воздухом, что нагнетается в резиновую камеру, проложенную на протяжении передней кромки несущего винта. Раздувающаяся камера надкалывает ледяную корку, отдельные куски которой после этого сметаются с лопастей винта встречным потоком воздуха.
В случае если передняя кромка лопасти винта сделана из металла, то ее возможно подогревать либо электричеством, либо теплым воздухом, пропускаемым через трубопровод, проложенный на протяжении передней кромки несущего винта.
Будущее продемонстрирует, какой из этих способов отыщет себе более широкое использование.
Для аэродинамических черт несущего винта солидное значение имеют число лопастей несущего винта, и удельная нагрузка на ометаемую винтом площадь. Теоретически число лопастей винта возможно любым, от одной вечно солидного их числа, так громадного, что они в конечном итоге сливаются в спиральную поверхность, как это предполагалось в проекте Леонардо да Винчи либо в вертолете-велосипеде И. Быкова.
Но имеется какое-то самоё выгодное число лопастей. Число лопастей не должно быть меньше трех, поскольку при двух лопастях появляются громадные колебания тяги и неуравновешенные силы винта. Продемонстрировано изменение тяги несущего винта около его среднего значения в течение одного оборота винта у однолопастного и двухлопастного винтов.
Трехлопастной винт уже фактически сохраняет среднее значение тяги в течение всего оборота.
Число лопастей винта не должно быть кроме этого большим, поскольку в этом случае любая лопасть трудится в потоке, возмущенном прошлой лопастью, что снижает коэффициент нужного действия несущего винта.
Чем больше лопастей винта, тем солидную часть площади ометаемого диска они занимают. В теорию несущего винта вертолета введено понятие коэффициента заполнения о, что подсчитывается как отношение суммарной площади
Для расчетного режима работы несущего винта вертолета (отвесный подъем) удачнейшей величиной коэффициента заполнения есть величина 0,05—0,08 (среднее значение 0,065).
Эта нагрузка есть средней. Малой нагрузкой именуют нагрузку в пределах 9—12 кг/м2. Вертолеты, имеющие такую нагрузку, маневренны и владеют громадной крейсерской скоростью.
Вертолеты неспециализированного назначения имеют среднюю нагрузку в пределах от 12 до двадцати килограмм/м2. И, наконец, громадной нагрузкой, редко используемой, есть нагрузка от 20 до тридцати килограмм/м2.
Дело в том, что не смотря на то, что высокая удельная нагрузка на ометаемую площадь и снабжает громадную нужную нагрузку вертолета, но при отказе двигателя таковой вертолет на режиме самовращения будет понижаться скоро, что недопустимо, поскольку в этом случае нарушается безопасность понижения.
Отстройка от флаттера лопастей
Упруго-массовые черт лопасти НВ
Характристика втулки несущего винта вертолета
Агрегаты техники
Ми-8 Редкие кадры. Работа лопасти в полете. Момент запуска.
Увлекательные записи:
Похожие статьи, которые вам, наверника будут интересны:
stroimsamolet.ru
Лопасть несущего винта вертолета
Использование: изобретение относится к несущим винтам вертолета. Сущность изобретения: лопасти несущих винтов включают лонжерон, хвостовые отсеки и на задних кромках некоторых отсеков пластины, используемые при отработке соконусности несущих винтов. Иногда пластины устанавливают по всей длине лопасти с целью увеличения хорды лопасти а, следовательно, ее несущей способности. Однако влияние пластин на относительных радиусах на несущую способность лопасти мало. С целью увеличения несущей способности лопасти, увеличения максимальной и крейсерской скоростей полета, а также максимальной полетной массы вертолета на относительных радиусах устанавливают пластины, увеличивающие хорду лопасти на 10%. 6 ил.
Изобретение относится к вертолетостроению, а именно к несущим винтам вертолетов.
Лопасти несущих винтов вертолетов обычно включают лонжерон и хвостовую часть в виде отсеков с сотовым заполнителем. На лопастях несущих винтов используются также пластины, установленные на нескольких хвостовых отсеках в задней кромке. Такие пластины установлены, в частности, на лопастях вертолета Ка-26 на относительных радиусах 0,8 — 0,9 [1] и на отсеках N 16, 17 лопастей вертолетов Ми-8, Ми-8МТ и модификаций этих вертолетов [2]. Эти пластины используют для выравнивания шарнирных моментов лопастей путем их отгиба при отработке несущих винтов. В качестве прототипа выбрана лопасть несущего винта вертолета Ми-8 [2], которая содержит лонжерон, хвостовые отсеки, причем на задней кромке части хвостовых отсеков установлены пластины. На ряде вертолетов, например на вертолетах Ми-8МТ, Ми-17 и их модификациях, после установки более мощного двигателя появилась возможность увеличения полетной массы вертолета, максимальной и крейсерской скоростей. Однако такая возможность ограничивалась недостаточной несущей способностью лопастей и появлением срыва потока на отступающей лопасти при больших скоростях полета, что приводит к недопустимому возрастанию нагрузок в лопасти и элементах забустерного управления. Технической задачей изобретения является усовершенствование лопастей несущего винта вертолета, которое не требовало бы больших затрат и обеспечивало бы возможность увеличения максимальной и крейсерской скоростей вертолета или его максимальной взлетной массы без существенного увеличения нагрузок в лопасти и забустерном управлении. Технический результат достигается тем, что в лопасти, содержащей лонжерон, хвостовые отсеки и пластины, которые установлены на задней кроме отсеков на относительных радиусах более примерно 0,5, увеличивают хорду приблизительно на 10%. На фиг. 1 изображена схема конструкции лопасти; на фиг. 2 — сечение А-А на фиг. 1; на фиг. 3 — сечение Б-Б на фиг. 1; на фиг. 4 — граница срыва несущего винта вертолета Ми-8; на фиг. 5 — переменный поперечный момент на автомате перекоса вертолета Ми-8МТ с серийной и уширенной лопастями; на фиг. 6 — переменный продольный момент на автомате перекоса вертолета Ми-8МТ с серийной и уширенной лопастями. Лопасть содержит лонжерон 1, хвостовой отсек 2, пластины 3. Описанные выше пластины шириной 50 мм, увеличившие хорду лопасти с 520 до 570 мм, были установлены на отсеках N 10 — 21 лопастей вертолетов типа Ми-8МТ на длине L 4,8 м при относительных радиусах . Существенно, что это не потребовало изменения сборочной оснастки лопастей и поэтому может быть внедрено в серийное производство без существенных затрат. Проведены летные испытания вертолета Ми-8МТ с указанными лопастями. Некоторые результаты таких испытаний в виде зависимостей переменной нагрузки в забустерном управлении от скорости полета для серийного и доработанного комплектов лопастей приведены на фиг. 3, 4. Согласно этим результатам у доработанных лопастей резко уменьшился прирост переменных нагрузок на больших скоростях полета, связанный со срывом потока в лопастях. Напряжения в лопастях несущего винта изменились незначительно. Указанные результаты делают возможным увеличить максимальную и крейсерскую скорости вертолета Ми-8МТВ (Ми-17) на 20 км/ч (на 9%) либо увеличить максимальную взлетную массу и полезную нагрузку вертолета с модифицированными лопастями на 1 т (7,6% взлетной массы или на 25% массы груза), что на 9 — 20% повысит транспортную производительность и соответственно снизит стоимость перевозки тонно-километра груза. Технико-экономические характеристики вертолета приблизятся к уровню лучших мировых образцов и повысится конкурентоспособность вертолета.Формула изобретения
Лопасть несущего винта вертолета, содержащая лонжерон, хвостовые отсеки и пластины, установленные на задней кромке части хвостовых отсеков, отличающаяся тем, что пластины установлены на относительных радиусах более примерно 0,5 и увеличивают хорду приблизительно на 10%РИСУНКИ
Рисунок 1, Рисунок 2, Рисунок 3, Рисунок 4, Рисунок 5, Рисунок 6findpatent.ru
Лопасти несущего винта
Автор — Владимир Ковальчук
Важным элементом конструкции модели вертолета являются лопасти несущего винта. Их весовые и аэродинамические характеристики определяют летные качества модели. В настоящее время фирмы предлагают большой ассортимент лопастей несущего винта, оптимизированных для определенного типа моделей и различных видов полета ( высшего пилотажа, авторотации, перевернутого и т.п.). Фирменные лопасти обладают единственным недостатком — большой ценой для моделистов из стран СНГ (на один комплект лопастей может потребоваться среднемесячная зарплата). Как показывает практика, моделисты, особенно начинающие, могут в летный сезон вывести из строя до десятка пар лопастей. Даже опытные моделисты не застрахованы от поломки лопастей. При любой ошибке в пилотировании или при отказе материальной части модели в первую очередь «страдают» лопасти несущего винта. Поэтому естественно желание многих моделистов самостоятельно освоить технологию изготовления лопастей несущего винта модели вертолета.
На первых радиоуправляемых моделях вертолетов применялись лопасти, изготовленные полностью из дерева. Сегодня такие лопасти применяются, как правило, на тренировочных моделях. Основным материалом фирменных лопастей в настоящее время является стекло- и углепластик. Лопасти из такого материала самостоятельно в домашних условиях изготовить довольно проблематично. Для обеспечения необходимой центровки эти лопасти загружаются дополнительным балластом. При неправильном расположении этот груз, под воздействием центробежной силы (в лопасти несущего винта эта сила достигает несколько сотен килограмм), может вылететь и вызвать тяжелые последствия для моделиста и окружающих. Поэтому самостоятельно лучше изготавливать лопасти из дерева, при балансировке которых практически не нужно использовать балласт. Кроме того, при разрушении деревянные лопасти хорошо гасят энергию удара, предохраняя от поломки элементы головки ротора и привода модели. По форме профиля лопасти бывают симметричные и плосковыпуклые. Симметричные профили применяют для лопастей спортивных моделей, выполняющих высший пилотаж. Плосковыпуклые профили применяют на лопастях «хоббийных» моделей. Следует отметить, что в домашних условиях проще изготовить лопасти с плосковыпуклым профилем, постоянным по всей длине. Как показывает практика, для таких лопастей хорошо подходит профиль Clark-Y.
Геометрические размеры лопастей определяются специальным аэродинамическим расчетом. Однако методика расчета довольна сложна и выходит за рамки настоящей статьи. Для практики целесообразно пользоваться данными, полученными, например, при измерениях фирменных лопастей. Как правило, для моделей 30 класса применяют лопасти длиной 450-500 мм, шириной 49-50мм. Для 40 класса — 520-550 мм, шириной — 49-50 мм. Для 60 класса- 620-680 мм, шириной — 55-61 мм. Например, для вертолета Хеликс, упоминавшемся в ранних статьях, при весе модели около 4,3 кГ с двигателем 10 см 3, при диаметре несущего винта, равном 1400 мм, лопасти имеют длину 625 мм и ширину 55 мм.
Кроме геометрических размеров важное значение имеет правильная поперечная и продольная балансировки лопастей. При несоблюдении условий балансировки, как правило, возникает сильная вибрация всего вертолета, разрушение тяг и рулевых машинок управления шагом, даже флаттер и разрушение лопастей. Для избежания флаттера и больших динамических нагрузок на органы управления точка крепления лопасти к головке ротора должна находиться на таком же расстоянии от передней кромки, как и центр тяжести лопасти. Кроме того, центр тяжести лопасти должен находиться ближе к передней кромке, чем фокус профиля ( центр приложения подъемной силы). Для выполнения последнего условия в носик стекло- и углепластиковых лопастей несущего винта загружают балласт. Для деревянных же лопастей с этой целью переднюю часть изготавливают из твердой и тяжелой древесины (бук, дуб), а заднюю — из бальзы средней плотности или из легкой липы и даже твердого пенопласта. Для повышения прочности и избежания коробления переднюю кромку лопасти делают не из цельного куска бука, а из склеенных вдоль волокна отдельных брусков, ориентированных в разные стороны. Дерево должно быть хорошо высушенным и не иметь сучков и других дефектов.
Для примера рассмотрим технологию изготовления деревянных лопастей (рис.1) несущего винта модели вертолета Хеликс (журнал «Моделист — конструктор» №4 за 1984 год), которая успешно применялась автором и его коллегами на протяжении последних шести лет.

«…В основном из-за упрощения обработки лопасти имеют на всей своей длине постоянный профиль Clark-Y, геометрическая крутка отсутствует — установочный угол одинаков для всех сечений. Передняя половина каждой пластины буковая, задняя из бальзы средней плотности. Так как начинающему «вертолетчику» понадобится не один комплект лопастей, лучше изготовить сразу несколько пар, да и из большого количества заготовок проще выбрать пары одинаковой массы.
Единая заготовка склеивается из бальзовой пластины (толщина 30мм, длина 650 мм, ширина — максимально доступная) и трех буковых таких же размеров, но толщиной 8 мм, на эпоксидной смоле. На ленточной или циркулярной пиле заготовка разрезается на бруски толщиной 10 мм, затем обрабатывается по профилю лопасти. Эту операцию лучше выполнить специальной фигурной фрезой после фугования нижней плоскости. Ручная же обработка верней поверхности по шаблонам трудоемка, длительна и менее точна, чем механическая. Да и возможный разброс деталей по массе при ручном способе больше. После завершения работ заготовки несколько раз покрывают эмалитом, шпаклюются нитролаком с замешанной в нем детской присыпкой. Корневая часть каждой лопасти обтягивается тонкой стеклотканью на эпоксидной смоле, а на всю поверхность накладывается длинноволокнистая бумага на эмалите. Поочередным вышкуриванием и лакировкой добиваются получения несильного ровного блеска, затем следует основательная сушка…. После этого приступают к статической балансировке и окончательной обработке лопастей.
Простейшее приспособление для фугования лопастей можно изготовить на базе деревообрабатывающего станка «Умелые руки» (рис.2).
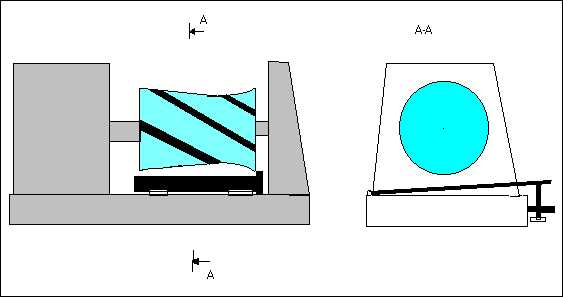
Для этого изготавливают из листа дюральки (2-3 мм) подвижный столик (выделен черным цветом на рисунке), один конец которого крепится к станку с помощью кусочков рояльных навесов. С другой стороны столик упирается в винт, поворачивая который, мы можем менять зазор между столиком и фрезой. В качестве фрезы можно использовать деревянную заготовку, обработанную на токарном станке по шаблону профиля, на поверхность которой наклеивают под углом 45 0 к торцу три-четыре полоски крупнозернистой наждачной бумаги. Как показал опыт, лучше всего наждачную бумагу приклеивать обычным канцелярским клеем, при фиксации концов на торце фрезы небольшими гвоздями. Другие клеи не выдерживали из-за сильного нагрева бумаги во время работы станка. Можно изготовить несколько фрез с различной зернистостью наждачной бумаги. Фрезу с более мелкой наждачной бумагой можно использовать для окончательной доводки поверхностей лопастей. Процесс фрезерования лопастей многократный, с постепенным поднятием столика. Фрезерование за один проход не получится из-за малой мощности станка. Вместо бальзы можно использовать легкую липу. В этом случае отфрезерованные лопасти просто покрывались лаком и полировались. Оправдало применение и жесткого пенопласта, но в этом случае всю лопасть необходимо обтягивать пленками. Современные пленки можно применять и при использовании бальзы.
Основную сложность при изготовлении лопастей представляет процесс балансировки лопастей. Не вдаваясь в теорию, отметим, что лопасти будут статически и динамически сбалансированы, если они имеют одинаковый вес и их центры тяжести находятся на одинаковом расстоянии от точки крепления к втулке и от передней кромки. Иными словами, только при выполнении одновременно этих двух условий лопасти не будут вызывать дополнительной вибрации. Существует множество методов балансировки лопастей несущего винта. Они отличаются применяемыми средствами и методами измерений и сравнений массы и координат центра тяжести лопастей. Так, например, для Хеликса предлагается «.. отбирать пары лопастей с разбросом по массе не более 5 г (большие устранить слишком сложно).Уже на данном этапе понадобятся лабораторные весы с точностью взвешивания не менее 0,1 г. Путем вывешивания на ребре дюралюминиевого уголка для каждой лопасти отыскивают положение центра тяжести по длине (радиусу ротора). Если эта величина окажется одинаковой для данной пары, можно заняться довешиванием более легкой лопасти путем нанесения на всю ее поверхность нескольких слоев жидкого лака с последующей шкуровкой. Но скорее всего, положения центров тяжести не совпадут. Совместить их лучше всего на счет высверливания двух-трех отверстий диаметром 4-5 мм в буковом концевом, более массивном торце на глубину до 70 мм. Сверловка в корне нежелательна — значительно ослабляет наиболее нагруженные участки ответственной детали. После продольной балансировки опять следует калибровка по массе каждой пары … и т.п. В приведенной методике требуются довольно точные весы, которые есть не у каждого моделиста.
Автор пользуется несколько иной методикой балансировки, без применения высокоточных весов и вывешивания лопастей на уголках. В этой методике применяются балансирные аптекарские весы (рис.3) и измеритель момента (рис.4). С помощью балансирных весов добиваемся равенства массы лопастей (путем нанесения лака или шлифования по всей длине лопасти и т.п.). Затем на измерителе моментов проверяем поочередно каждую лопасть. Если показания измерителя одинаковые, то это свидетельствует о том, что статический момент, т.е. произведение массы на расстояние от точки крепления до центра тяжести каждой лопасти, также одинаков. Если моменты от силы тяжести лопастей одинаковы при равенстве их масс, то и расстояние до центра тяжести каждой лопасти будет также равным. Иными словами, лопасти будут статически и динамически сбалансированы. Если же показания измерителя моментов отличаются, т.е. одна из лопастей по сравнению с другой создает больший или меньший момент от сил тяжести, то, при равенстве их масс, это свидетельствует о несовпадении расстояний от точки подвески до центра тяжести лопастей. Для лопасти, которая создает больший статический момент относительно точки подвести надо сдвинуть центр тяжести ближе к точке подвески, т.е. облегчить концевую часть лопасти. Или наоборот, для другой лопасти утяжелить концевую часть. Необходимо помнить, что любая такая операция (нанесение определенного количества лака или кусочков изоляционной ленты на концы лопастей, высверливанием в их торце отверстий и т.п.) изменяют массу лопастей. Поэтому необходимо вернуться к выравниванию масс лопастей на балансирных весах. Для этой цель автор, например, прикрепляет к лопастям, подвешенные к балансирным весам, одинаковые по массе куски изоляционной ленты. Затем на лопасть, которая создает больший момент, один из этих кусочков изоленты крепится непосредственно около корня её. На измерителе моментов находим точку крепления на другой лопасти второго кусочка изоленты, который обеспечивает равенство моментов от сил тяжести обеих лопастей. Если при такой балансировке количество изоленты получается значительным, то следует предварительно облегчать или утяжелять концы лопастей другими методами, например, нанесением лака или шпаклевки и шлифованием. Высверливание отверстий в торце, как показала практика, довольно трудоемкая и грубая операция, и к ней следует прибегать только в крайних случаях. Но никаких металлических балансиров (винтов, шурупов, кусков олова и т.п.) на концах лопастей устанавливать нельзя.
Следует отметить, что при использовании лаков и шпаклевок необходимо периодически проверять балансировку лопастей, поскольку со временем эти компоненты изменяют свои вес.
Можно применять и другие методики балансировки. Например, для выравнивания моментов от сил тяжести м ожно использовать головку ротора с прикрепленными лопастями. Для этого снятую головку с лопастями устанавливают на уголок и добиваются уже описанными методами равенства моментов, т.е. строгого горизонтального положения ротора. Но и в этом случае необходимо добиваться равенства не только моментов, но и масс лопастей.
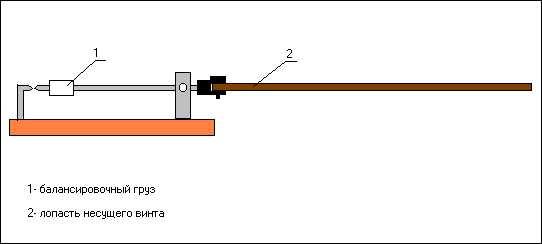
Как показывает практика, выполнение этих условий позволяет быстро провести заключительную балансировку всего ротора на работающем вертолете, которую мы подробно рассмотрим в следующих статьях.
В заключение отметим, что приведенная методика позволят быстро изготовить лопасти, пригодные для начального обучения и простого пилотажа. Для других видов полета лопасти должны иметь, как правило, симметричный профиль и специальные утяжелители для повышения весо-динамических характеристик. Но это тема требует отдельного разговора.
Обсудить на форумеwww.rcdesign.ru
Лопасти для мини вертолёта. — Паркфлаер
Для тех у кого есть мини ветролетики типа SIGMA 107 и прочие подобные модели не секрет что лопасти-одна из наиболее ломающихся частей
В среднем в Санкт Петербурге цена от 100 до 150 за пару!Да и есть не везде!(кстати модель стоила мне 1200 руб)согласитесь не рентабельно как-то их покупать.
Вот подумал и придумал как сделать их самому,причем изготовление занимает примерно час(4 шт.)!
не дольше похода в магаз=)
Приступим.
Нам потребуется:
1. Пластиковые карты (те которые в магазинах дают постоянным покупателям (без теснения)
2. 2 РАЗНЫЕ! более менее целые лопасти(лучше целые)
вот и всё!
Справа и снизу то что осталось от моих лопастей=)
Те которые что справа будут использованны для создания профиля будущей лопасти,а нижняя для шаблона.

На лопастях есть маркировка(в месте крепления)»1А» и «2В»
для профиля,повторюсь,нужны «1А» и»2В»
В моём случае остались две «1А» и одна»2В»
Одну лопасть(у меня «1А»)избавляем от профиля — греем над газом и прижимаем к столу чем-то плоским но не сильно что-бы не расплющить!
Далее обводим по шаблону лучше сразу ножом.
Для тех кто не знает ,резать надо так — сначала несколько раз проводим без нажима потом с каждым резом нажим усиливаем!аккуратно надламываем и прорезаем с обратной стороны,карта ламинирована! пленку отдирать не надо!!!
Выглядит это примерно так:
Получается вот такая заготовка.
Теперь нужно плавно,как-бы это сказать, утончить её к концу делаем это шкуркой примерно от второй трети лопасти.
Переидем к созданию профиля.
Сворачиваем в рулон небольшую тряпочку,заготовку греем над газом до размягчения,а не до состояния сопли!!! широкую часть заготовки.
кладем ее на наш рулончик…
и сверху прижимаем нужной лопастью
Повторяем действие с узкой частью
спешить не надо заготовка довольно долго остаеться элластичной!
После сей процедуры получаем вот это
Остаётся поработать шкуркой- утончить заднюю часть профиля
вот что получилось
Вот таким не хитрым образом можно изготовить лопасти для вашей птахи!
P.S.
Прошу строго не судить — моя первая статья.
за качество фоток тоже извиняюсь-что было тем и фоткал,а было не много=)))
www.parkflyer.ru