Российский титан завоевывает небо / Вооружения / Независимая газета
В год 7-й 8-го числа 7-го месяца компания Боинг представила миру свою новинку – самолет «Боинг-787», за которым уже выстроились в очередь более сорока крупнейших авиакомпаний мира. Но приоритет в приобретении нового суперлайнера будет у россиян. И это справедливо. Ведь, как ранее сообщил генеральный конструктор самолета Джим Моррис, ключевые элементы для «Боинг-787 Дримлайнер» (Boeing-787 Dreamliner) разрабатывались в Московском центре «Боинг», где трудятся 300 российских инженеров. По словам господина Морриса, российские инженеры проектировали элементы носовой части фюзеляжа, пилоны навески двигателей, а также переднюю кромку крыльев, предкрылки и элементы титановых конструкций шасси. Поставщиком же титановых элементов для конструкции «Боинг-787» стала российская компания «ВСМПО-АВИСМА». «Этот самолет на 10% своего веса состоит из российского титана», – подчеркнул господин Моррис. Иными словами, по титановым конструкциям он наполовину российский, так как общая доля этого металла в самолете достигает 20 процентов.
МНОГО ЗВАНЫХ, НО МАЛО ИЗБРАННЫХ
Многие страны имеют залежи минералов, содержащих титан, – Австралия, Канада, Индия, Норвегия, США, Украина, ЮАР. Однако, как говорится, много званых, но мало избранных. Далеко не во всех даже экономически развитых странах сумели освоить производство и технологию обработки этого самого легкого и одновременно самого прочного металла.
Титан открыли более 100 лет назад, но сам он не раскрылся человеку. Основная проблема его производства – степень очистки металла. Даже незначительные доли примеси делали его хрупким. Около века назад металл посчитали бесперспективным, и таковым он оставался примерно до середины 40-х годов двадцатого столетия. В 1948 году американцы выплавили первый промышленный титановый слиток. Российские металлурги, хотя и отстали на старте, но затем быстро догнали заокеанских конкурентов. Сегодня Россия и США стали партнерами в авиастроительной отрасли. Это произошло в немалой степени благодаря нашим передовым технологиям в обработке титана и изделий из его сплавов. Мы можем гордиться, что американские самолеты будут делать из российского титана. Производство и обработку этого металла с полным основанием можно отнести к нашим национальным достижениям. Огромная заслуга в этом принадлежит корпорации «ВСМПО-АВИСМА».
Любая история пишется языком своего времени. Время предприятия – это годы войны и противостояния политических систем, освоения космоса и конверсии оборонной промышленности и, наконец, вхождения в мировой рынок. Страницы летописи «ВСМПО-АВИСМА» открывают многие главы развития российской авиации и космонавтики.
Крупнейший в мире и практически единственный в России производитель титана – Верхнесалдинский металлургический завод, на базе которого была образована корпорация «ВСМПО-АВИСМА», дал первую плавку в 1933 году. Специалисты отмечали, что ввод в строй этого завода способствовал изменению технического уровня производства материалов для авиации. Но о титане в те годы не было и речи. В самолетостроении заканчивалась фанерно-тканая эпоха, начиналась алюминиевая, и созданное предприятие играло в ней ключевую роль, занимало особо ответственное положение в экономике страны. Завод производил из алюминия детали и полуфабрикаты, предназначенные для строительства моторов и цельнометаллических самолетов. Таковы были нужды СССР, и крылатый металл, как называли алюминий, выполнял задачи своего времени.
Военные годы подтвердили особый статус завода. Эвакуированный в 1941 году из Москвы на Урал, в Верхнюю Салду, он обеспечивал легкими сплавами военную авиацию и другие оборонные отрасли производства.
Другие времена ставят иные цели. Соперничество с американцами, прежде всего в военной сфере, способствовало разработке новых средств вооружения. В середине прошлого века на арену вышел титан.
Как известно, военные самолеты, ракеты, подводные лодки работают в экстремальных условиях и режимах. Кроме того, конструкторы новой авиатехники столкнулись с проблемой высоких температур обшивки корпуса. К конструкционным материалам летательных аппаратов сверхзвуковых скоростей предъявлялись более жесткие требования.
Незаменимым металлом для новой авиации и космонавтики стал титан, который обладает особыми свойствами: легкостью в сочетании с прочностью, исключительной коррозионной стойкостью, высоким уровнем специальных характеристик, хорошими технологическими и физическими свойствами. Сочетание этих ценных качеств делает титан уникальным материалом. Освоение его производства и обработки кардинально решило многие проблемы авиакосмической отрасли.
ИСТОРИЯ И СОВРЕМЕННОСТЬ
Верхнесалдинский металлургический завод сменил профиль в середине 50-х годов. По решению правительства здесь было организовано крупномасштабное промышленное производство продукции из титановых сплавов. В 1957 году был выплавлен первый слиток, а к концу семидесятых годов за счет реконструкции действующего производства и строительства новых цехов предприятие стало одним из крупнейших в мире производителей слитков и большинства видов проката из титановых сплавов. К концу 80-х годов завод вывел Россию в число мировых лидеров по производству этого металла.
К этому времени ВСМПО стало элитным подразделением военно-промышленного комплекса страны с мощным многопрофильным производством, оснащенным уникальным оборудованием. На него пришли трудиться высококвалифицированные научно-технические и рабочие кадры.
Завод приступил к выпуску проката: штамповок, листов, плиток, прутков, профилей, труб и слитков. Из алюминиевых сплавов начали делать крупногабаритные экструдированные панели и профили, штамповки. Половина всей продукции использовалась в гражданской и военной авиации.
ВСМПО стало основным поставщиком металла для большинства аэрокосмических проектов: пассажирских самолетов Ту-154, Ту-204, Ил-86, Ил-96, Ан-124, вертолетов семейства «Ми», военных самолетов марки «Су», «МиГ», «Ту». Титан быстро завоевал небо, а потом отправился в космос. Он использовался в строительстве ракетного комплекса «Энергия-Буран» и космического комплекса «Союз-Аполлон». Одновременно титан спустился в океанские пучины. Ему нашли применение в судостроительной отрасли, приступив к строительству атомных подводных лодок и другой оборонной техники.
В 90-х годах прошлого века Верхнесалдинский металлургический завод вышел на мировой рынок титана. Это была вынужденная мера сохранения уникального производства. В то смутное время заказы на титан от отечественных потребителей практически иссякли. Приходилось рассчитывать только на собственные силы. А сил у предприятия оказалось достаточно много, чтобы вступить в конкурентную борьбу на условиях уже сложившегося мирового рынка титана. Американские, японские, европейские авиастроители вначале настороженно отнеслись к новому производителю сверхпрочного металла. Однако их убедил высокий уровень развития российского производства. Войти в мировой авиационный и индустриальный рынок и занять там свою нишу удалось достаточно быстро.
Сегодня корпорация «ВСМПО-АВИСМА» – ведущий поставщик титановой продукции для таких мировых компаний, как Boeing, Airbus, Embraer, Goodrich, SNECMA, Rolls Roys, Pratt&Whitney и других. Корпорация поставляет титан предприятиям и других отраслей промышленности: химического машиностроения, энергетики, в том числе атомной, производства медицинских имплантатов.
На самом деле применение титана постоянно растет во всех сферах производства и повседневного быта. Чаще всего этот металл ассоциируется с ценными изделиями, такими как наручные часы, оправы для очков, спортивные товары и ювелирные изделия. В зависимости от непосредственного назначения он конкурирует с никелем, нержавеющей сталью и циркониевыми сплавами. Многообещающие признаки роста показывает автомобильный сектор. В системах подвесок, например, замена стальных пружин на титановые дает преимущество в виде уменьшения веса на 60%. Также титан применяют в производстве коленчатых валов, соединительных тяг и выхлопных систем. Электростанции и заводы по опреснению морской воды также являются важными областями для роста применения титана. Развивается производство титановых подложек для жестких дисков персональных компьютеров.
На российском рынке «ВСМПО-АВИСМА» полностью удовлетворяет потребности в титановой продукции авиационных, оборонных, машиностроительных предприятий. Корпорация остается надежным партнером более 1000 заказчиков в России и других странах СНГ. В числе заказчиков предприятия: «Сухой», КнААПО, НПК «Иркут», «Авиант», УМПО, «Салют», «Сатурн», ПМЗ, «Мотор Сич» и другие.
Корпорация «ВСМПО-АВИСМА» сертифицирована практически всеми мировыми производителями авиационно-космической техники. Это единственная в Российской Федерации компания, имеющая более 250 международных сертификатов качества.
РЕВОЛЮЦИЯ В АВИАСТРОЕНИИ
В настоящее время происходит принципиальная перестройка всей материаловедческой концепции формирования конструкции самолетов. Перед разработчиками авиатехники стоят задачи по снижению веса, расхода топлива и эксплуатационных затрат, увеличению дальности полета.
На дальние расстояния полет станет более комфортным, если рейс не транзитный, если люди не теряют время в промежуточных пунктах. Быстрее прибыть в пункт назначения на личные и деловые встречи – мечта каждого пассажира. Авиаперевозчики, пассажиры, летчики с нетерпением ожидают таких авиалайнеров, которые будут способны преодолевать маршруты протяженностью более 15 тысяч километров без посадок и дозаправок. Этого можно достичь, если авиатехника станет максимально эффективной в эксплуатации, точнее, сверхэкономичной.
В XXI веке эти задачи решают с помощью широкого использования композиционных материалов на основе углеволокна и титановых сплавов. Последние заменяют сталь и алюминиевые сплавы. Алюминий постепенно выводится из конструкций, поскольку активно взаимодействует с ними и коррозирует. Этим процессам не подвержен титан. Он увеличивает ресурс высоконагруженных деталей, а значит – и сроки эксплуатации самолетов. Титан обладает большими преимуществами перед другими металлами и материалами в весовой характеристике. А чем легче самолет, тем он экономичнее. В новых, буквально революционных, проектах летательных аппаратов американских и европейских авиастроителей доля титана возрастает в несколько раз.Авиалайнер В787 Dreamliner компании Boeing – лидер нового поколения самолетов – самый экономичный, один из самых комфортных. Он будет иметь дальность полета, сопоставимую с дальностью современных широкофюзеляжных самолетов. Показатель потребления топлива у В787 на 20 процентов ниже, чем у самолетов подобного класса. И он на 20 процентов состоит из титана (для сравнения: этот показатель в В777 – девять процентов).
Корпорация «ВСМПО-АВИСМА» определена ведущим и единственным за пределами США поставщиком титана для этого самолета. В новом авиалайнере, впервые в истории американского самолетостроения, применен новый высокопрочный титановый сплав, разработанный за пределами страны. Это сплав VST 5553, созданный профессионалами ВСМПО. Из него изготавливаются десятки новых наименований штамповок. В их производстве у корпорации нет равных.
Уральская корпорация является также основным поставщиком титана для конкурента американской компании Boeing – европейской авиастроительной фирмы Airbus. Самолет этой компании А380 садится на шасси, в составе которого самая большая в мире горизонтальная балка, изготовленная из салдинской титановой штамповки. Таких крупногабаритных изделий больше никто делать не может. Высокое качество обеспечивается изготовлением их на модернизированном кузнечном оборудовании, самом мощном и современном в мире. В 2007 году начинается новая работа над проектом Airbus A350, для которого корпорация будет делать штамповки.
Надеждой российского авиапрома называют региональный самолет SuperJet100 компании «Гражданские самолеты «Сухого». Это первый самолет такого класса, созданный в XXI веке. Титана в нем немного, но он содержится в самых ответственных узлах авиалайнера. И титан этот – корпорации «ВСМПО-АВИСМА».
Сегодня уральская корпорация входит практически во все новые проекты мирового авиастроения, став ведущим поставщиком титана и помогая реализовать создателям самолетов их самые смелые мечты.
Свою продукцию в составе современных летательных аппаратов корпорация «ВСМПО-АВИСМА» продемонстрирует на «МАКС-2007» в подмосковном Жуковском. Наш глаз будет любоваться легкостью и грациозностью современных летательных аппаратов. Но уже невозможно применить к ним журналистский штамп «стальные птицы». Они все более становятся титановыми. А делает их такими – легкими и экономичными – продукция корпорации «ВСМПО-АВИСМА».
Прочность ракеты-носителя «Энергия» и орбитального корабля «Буран» была достигнута благодаря продукции Верхнесалдинского металлургического завода. |
Ка-50 «Черная акула» надежна и легка как титан, который приименяется при строительстве этого вертолета. |
nvo.ng.ru
Монино, ч.2. Экспериментальный ударный самолёт Т-4: periskop — LiveJournal
Одним из наиболее поразивших меня экспонатов музея авиации в Монино был экспериментальный сверхзвуковой ударный самолет, сделанный из титана (!). По размеру он – примерно 60-70% от широко известного Ту-144, а по аэродинамике – очень похож.Это разработка ОКБ Сухого, которые обычно специализировалось на истребителях, под именем Т-4. Каюсь, я про него раньше не знал, и поэтому был особенно удивлен его видом – он и посейчас стоит как новенький, не тронутый коррозией: титан всё-таки.
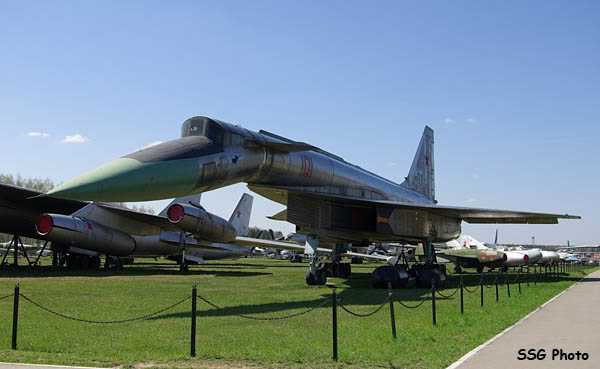
Общий вид сбоку.
А тут — спереди.
Эта машина выполнила 10 полётов, после чего, по неупомянутым на сопроводительной табличке причинам полёты прекратила.
Табличка с характеристиками.
Носовая часть покрупнее. Хорошо видно, что на сверхзвуке он (видимо) летал только вслепую, по приборам, так как нос поднимался и закрывал окна кабины.
Хвостовая часть.
Сопла двигателей.
Они же, покрупней.
Под крылом. Титан придает самолёту несколько сюрреалистичный вид. Какова цена такого самолёта, мне даже представить трудно.
Титановое покрытие, покрупнее.
Воздухозаборник двигателя.
Подкрыльевое шасси.
Монино:
1. Ла-7 Ивана Кожедуба
Внимание!
Репосты с полной трансляцией поста в сторонние ресурсы без согласования со мной не разрешаются.
При желании осуществлять трансляцию (а тем паче регулярную) — обращаться сюда.
periskop.livejournal.com
Применение титана в авиации, кораблестроении, военной технике
Применение титана в авиацииАвиационная промышленность была первым потребителем титана. Создание летательных аппаратов со скоростями близкими к скорости звука и превосходящими ее, определило ряд технических и экономических требований к конструкционным материалам, идущим на изготовление корпуса самолета и его обшивки, а также двигателей, которые невозможно было удовлетворить без применения материалов на основе титана.
Малый удельный вес и высокая прочность
(особенно при повышенных температурах) титана и его сплавов делают их весьма
ценными авиационными материалами. В области самолетостроения и производства
авиационных двигателей титан все больше вытесняет алюминий и нержавеющую сталь.
С повышением температуры алюминий быстро утрачивает свою прочность. С другой
стороны, титан обладает явным преимуществом в отношении прочности при
температуре до 430° С, а повышенные температуры такого порядка возникают при
больших скоростях благодаря аэродинамическому нагреванию. Преимущество замены
стали титаном в авиации заключается в снижении веса без потери прочности. Общее
снижение веса с повышением показателей при повышенных температурах позволяет
увеличить полезную нагрузку, дальность действия и маневренность самолетов. Этим
объясняются усилия, направленные на расширение применения титана в
самолетостроении при производстве двигателей, постройке фюзеляжей, изготовлении
обшивки и даже крепежных деталей.
При постройке реактивных двигателей титан применяется
преимущественно для изготовления лопаток компрессора, дисков турбины и многих
других штампованных деталей. Здесь титан вытесняет нержавеющую и термически
обрабатываемую легированную стали. Экономия в весе двигателя в один килограмм
позволяет сберегать до 10 кг в общем весе самолета благодаря облегчению
фюзеляжа. В дальнейшем намечено применять листовой титан для изготовления
кожухов камер сгорания двигателя.
В конструкции самолета титан находит широкое применение для
деталей фюзеляжа, работающих при повышенных температурах. Листовой титан
применяется для изготовления всевозможных кожухов, защитных оболочек кабелей и
направляющих для снарядов. Из листов легированного титана изготовляются
различные элементы жесткости, шпангоуты фюзеляжа, нервюры и т. д.
Кожухи, закрылки, защитные оболочки для кабелей и направляющие
для снарядов изготовляются из нелегированного титана. Легированный титан
применяется для изготовления каркаса фюзеляжа, шпангоутов, трубопроводов и
противопожарных перегородок.
Вращающиеся детали роторов авиадвигателей испытывают в
полете колоссальную нагрузку. Им приходится работать в условиях высоких
температур и динамических воздействий. От их надежности зависят безопасность
самолета и жизни людей, что находятся на борту воздушного судна. Следовательно,
титан, используемый в этих ответственных узлах, должен быть не просто прочным,
а суперпрочным.
Титан получает все большее применение при постройке самолетов
F-86 и F-100. В будущем из титана будут делать створки шасси, трубопроводы
гидросистем, выхлопные патрубки и сопла, лонжероны, закрылки, откидные стойки и
т. д.
Титан можно применять для изготовления броневых плит, лопастей
пропеллера и снарядных ящиков.
В настоящее время титан применяется в конструкции самолетов
военной авиации Дуглас Х-3 для обшивки, Рипаблик F-84F, Кертисс-Райт J-65 и
Боинг В-52.
Применяется титан и при постройке гражданских самолетов DC-7.
Фирма «Дуглас» заменой алюминиевых сплавов и нержавеющей стали титаном при
изготовлении мотогондолы и противопожарных перегородок уже добилась экономии в
весе конструкции самолета около 90 кг. В настоящее время вес титановых деталей
в этом самолете составляет 2%, причем эту цифру предусматривается довести до
20% общего веса самолета.
Растет потребление титана в гражданском самолетостроении. И понятно почему: титан сочетает в себе основные параметры эффективности самолета – веса, надежности, стоимости обслуживания и прибыли от эксплуатации. Это главные критерии для авиаперевозчиков.
В настоящее время разработчики авиатехники перестраивают всю материаловедческую концепцию строительства самолетов, активно привлекая и используя композиционные материалы на основе углеволокна и титановые сплавы. Первые заменяют алюминий и сталь, вторые коррозийноустойчивы и исключительно прочны.
Причин перехода на композиционные материалы несколько. Во-первых, наметился быстрый рост пассажирских и грузовых перевозок, объем которых, по прогнозам специализированной аналитической группы Airline Monitor, в период с 2008 по 2026 год увеличится втрое, что потребует в два раза увеличить парк магистральных авиалайнеров. Во-вторых, в условиях высоких цен на топливо cамолетостроительным компаниям приходится разрабатывать и готовить серийный выпуск экономичных моделей авиалайнеров.
Поскольку с композитами «уживается» только титан, спрос гражданского самолетостроения на титановые полуфабрикаты возрастет к 2015 году примерно в два раза.
В «самолете мечты» Boeing 787 – лидере нового поколения самолетов – половина применяемого титана – ВСМПО-АВИСМЫ. В самолете использован новый высокопрочный титановый сплав VST 5553, созданный профессионалами ВСМПО. Из него изготавливают десятки наименований штамповок, в производстве которых ВСМПО нет равных. А первый заказ на продукцию российской корпорации ВСМПО-АВИСМА Boeing разместил в 1997 году.
Самая большая штамповка балки шасси самолета А380 весом 3,5 тонны изготовлена из титана ВСМПО-АВИСМА. Таких крупногабаритных изделий больше никто делать не может. Изготавливают штамповки на модернизированном кузнечном оборудовании, самом мощном в мире.
В заказах такого гранда авиации, как Boeing, доля российского титана составляет 30–40%, в европейской компании Airbus – 55–60%, бразильской Embraer – 90%, в канадской Goodrich – крупнейшего в мире производителя шасси – 90%.
Применение титана в кораблестроенииКоррозионная стойкость титана и его сплавов
делает их весьма ценным материалом на море. Военно-морское министерство США
обстоятельно исследует коррозионную стойкость титана против воздействия дымовых
газов, пара, масла и морской воды. Почти такое же значение в военно-морском
деле имеет и высокое значение удельной прочности титана.
Малый удельный вес металла в сочетании с коррозионной
стойкостью повышает маневренность и дальность действия кораблей, а также
снижает расходы по уходу за материальной частью и ее ремонту.
Применение титана в военно-морском деле включает изготовление
выхлопных глушителей для дизельных двигателей подводных лодок, дисков
измерительных приборов, тонкостенных труб для конденсаторов и теплообменников.
По мнению специалистов, титан, как никакой другой металл, способен увеличить
срок службы выхлопных глушителей на подводных лодках. Применительно к дискам
измерительных приборов, работающих в условиях соприкосновения с соленой водой,
бензином или маслом, титан обеспечит лучшую стойкость. Исследуется возможность
применения титана для изготовления труб теплообменников, которые должны
обладать коррозионной стойкостью в морской воде, омывающей трубы снаружи, и
одновременно противостоять воздействию выхлопного конденсата, протекающего
внутри них. Рассматривается возможность изготовления из титана антенн и узлов
радиолокационных установок, от которых требуется стойкость к воздействию
дымовых газов и морской воды. Титан может найти применение и для производства
таких деталей, как клапаны, пропеллеры, детали турбин и т. д.
Специалисты научно-исследовательского института конструкционных материалов «Прометей» при государственной поддержке Федерального агентства по науке и инновациям (Роснаука) начали в 2009 году разработку усовершенствованных технологий производства из титановых сплавов так называемых крупногабаритных полуфабрикатов (заготовок крупных узлов и деталей) для морских судов и «оффшорной техники», предназначенной для работ на шельфах.
Такие заготовки из титановых сплавов могут применяться для изготовления сверхлёгких, прочных и стойких к коррозии деталей самых разных типов судов, например, исследующих морские глубины, или связанные с добычей углеводородного сырья.
Существенный недостаток титановых сплавов только один — высокий коэффициент трения «металл по металлу», титан попросту «задирается» при трении из-за повышенной вязкости. Поэтому для деталей из титановых сплавов (в первую очередь, для различных т. н. «узлов трения») необходимо напыление специальных покрытий, придающих необходимые антифрикционные свойства. В качестве «кандидатов» на создание таких покрытий ученые намерены всесторонне исследовать различные высокопрочные материалы на основе оксидов алюминия, циркония и хрома.
Применение титана для изготовления военной техники
Металл потребляет артиллерия, где в
настоящее время ведутся интенсивные исследования различных опытных образцов.
Тем не менее в этой области стандартизовано производство лишь отдельных деталей
и частей из титана. Весьма ограниченное использование титана в артиллерии при
большом размахе исследований объясняется его высокой стоимостью.
Были исследованы различные детали артиллерийского оборудования
с точки зрения возможности замены титаном обычных материалов при условии
снижения цен на титан. Главное внимание уделялось деталям, для которых
существенно снижение веса (детали, переносимые вручную и перевозимые по
воздуху).
Опорная плита миномета, изготовленная из титана вместо стали.
Путем такой замены и после некоторой переделки вместо стальной плиты из двух
половинок общим весом 22 кг удалось создать одну деталь весом 11 кг. Благодаря
такой замене можно уменьшить число обслуживающего персонала с трех человек до
двух. Рассматривается возможность применения титана для изготовления орудийных
пламегасителей.
Проходят испытания изготовленные из титана орудийные станки,
крестовины лафетов и цилиндры противооткатных приспособлений. Широкое
применение титан может получить при производстве управляемых снарядов и ракет.
Проведенные первые исследования титана и его сплавов показали
возможность изготовления из них броневых плит. Замена стальной брони (толщиной
12,7 мм) титановой броней одинаковой снарядостойкости (толщиной 16 мм)
позволяет получить, по данным этих исследований, экономию в весе до 25%.
Сплавы титана повышенного качества позволяют надеяться на
возможность замены стальных плит титановыми равной толщины, что дает экономию в
весе до 44%. Промышленное применение титана позволит обеспечить большую
маневренность, увеличит дальность перевозки и долговечность орудия. Современный
уровень развития воздушного транспорта делает очевидными преимущества легких
броневиков и других машин из титана. Артиллерийское ведомство намерено
снарядить в будущем пехоту касками, штыками, гранатометами и ручными
огнеметами, сделанными из титана. Первое применение в артиллерии титановый
сплав получил для изготовления поршня некоторых автоматических орудий.
Как отмечает менеджер по продажам американской компании Howmet Ti-Cast Боб Фаннелл, «…текущее состояние рынка можно рассматривать, как рост возможностей в новых областях, таких как вращающиеся части устройств турбонадува у грузовиков, ракеты и насосы. Одним из наших текущих проектов является развитие лёгких артиллерийских систем ВАЕ Ноwitzer ХМ777 калибром 155 мм». Ноwmet: поставит 17 из 28 узлов структурного титанового литья для каждой орудийной установки. «При общем весе орудия 9800 фунтов (приблизительно 4,44 тонн) в его конструкции на долю титана приходится около 2600 фунтов (приблизительно 1,18 тонн) — используется сплав 6А14У с большим количеством отливок», говорит Фрэнк Хёрстер, руководитель систем огневой поддержки ВАЕ 8у81ет8. Эта система [ХМ777] должна заменить находящуюся на вооружение систему М198 Ноwitzег, которая весит около 17000 фунтов (приблизительно 7,71 тонн).
Джон Барбер из Timet: указывает, что примерами военной техники, в конструкции которой используются значительные объёмы титана, являются танк «Абраме» и боевая машина «Брэдли». В течение уже двух лет выполняется совместная программа НАТО, США и Великобритании по интенсификации использования титана в системах вооружений и обороны.Как уже не раз отмечалось, титан очень подходит к использованию в автомобилестроении, правда, доля этого направления довольно скромна — примерно 1% от общего объёма потребляемого титана, или 500 тонн в год, по данным итальянской компании Роggipolini, производителя титановых узлов и деталей для «Формулы-1» и гоночных мотоциклов.
Построенная В 1969 г. АПЛ 661-го проекта в Северодвинске не имела мировых аналогов — она имела корпус полностью из титанового сплава и развивала скорость до 44,7 узла — рекорд, недостижимый даже для современных подлодок.
Титан в строительстве АПЛ применялся и в дальнейшем. Из-за повышенной глубины погружения материалом прочного корпуса подводной лодки «Комсомолец» был выбран титановый сплав 48-Т с пределом текучести около 720 МПа. Применение титана позволило существенно уменьшить массу корпуса. Она составила всего 39 % от нормального водоизмещения, что не превышало соответствующий показатель других АПЛ.
www.protown.ru
The New York Times о роли российского титана для Boeing
Компания Boeing пытается уменьшить вес своих самолетов, для чего ей необходим титан. За этим легким и прочным металлом американская компания отправляется в небольшой городок Верхняя Салда на Урале.
Титановый завод ВСМПО-АВИСМА во времена холодной войны был засекреченным предприятием по производству деталей для ядерных ракет. Сейчас там горой лежат титановые прутья для самолетов Boeing. В СП Boeing и ВСМПО-АВИСМА под названием Ural Boeing Manufacturing шлифуются кованые детали, предназначенные для транспортировки в Америку. Треть всех сборочных производств стоек шасси для самолетов Boeing использует титановые балки из России.
Российские детали не видны с первого взгляда, но тоже очень важны. Их применяют на таких самолетах, как Boeing 787 Dreamliner или рядовой пассажирский 737.
Boeing закупает у ВСМПО-АВИСМА настолько много титана (в будущем компания планирует выделить на закупки еще 18 миллиардов долларов), что сейчас даже принимает участие в разработке новых сплавов в России. В Москве, на тысячу километров западнее, команда из 1 400 аэрокосмических инженеров разрабатывает новые фюзеляжи и крылья, применяя российские титановые детали.
Также важен этот союз и для Boeing. Благодаря новому Dreamliner, компания освоила новые технологии и расширила мировую сеть поставщиков. Однако стратегия сильно пошатнулась из-за японских литий-ионных аккумуляторов. Риск взрыва аккумуляторов заставил Boeing на месяцы приостановить работу всей серии самолетов.
Российские же титановые технологии наоборот полностью оправдали себя. Уверенность в российском титане крепка даже несмотря на натянутые отношения между Россией и Соединенными Штатами. Геополитические риски делают легкий металл даже более экономичным, поэтому Boeing использует его все больше. Снижение веса делает самолет более экономичным в использовании и, таким образом, более привлекательным для авиакомпаний. Завод ВСМПО-АВИСМА, расположенный в чаще соснового леса, производит 35% всего титана для пассажирских самолетов Boeing.
«Существуют детали, которые кроме нас никто не производит», — заявил директор и совладелец завода Михаил Воеводин.
Титановые детали невероятно трудно производить. В главном плавильном цехе вдоль стен стоят гигантские кольцевые печи, похожие на трубы вулканического органа, высотой в шесть этажей, в церкви из преисподней. В этих вакуумных трубах электричество плавит металл.
Гигантские опоры, столбы и листы накаляются до красна и опускаются в воду, где их ударяют невероятно сильными гидравлическими молотками весом в 5 тонн.
«Россия – стратегический партнер, производящий детали для Boeing 787», – считает Сергей Кравченко, директор представительства Boeing в России. На заводе «находится самый крупный в мире пресс для титановых поковок, и Boeing полностью использует это уникальное преимущество», – написал он в своем письменном интервью.
В России титан начали использовать для изготовления кабины космического корабля «Восток», на котором в 1961 полетел Юрий Гагарин. К началу 70-х этот металл увлек советских генералов. Началась секретная программа, требующая невероятных ресурсов. В Союзе из титана строили не только самолеты, но и подводные лодки.
Из музея при заводе стало известно, что корпуса полудюжины торпедных подводных лодок класса Alfa, Mike и Papa на 30% были выполнены из титана. На производство каждой лодки требовалось более 2000 тонн титана. Легкие и прочные подлодки называли «золотыми рыбками», они могли развивать скорость под водой до 44 узлов или 80 км/ч.
Сама история уже позволяла компании Boeing быть уверенной в стабильности российских поставок. Кроме России и других бывших советских республик выплавкой титана занимаются только США, Германия, Япония и Китай.
Холодная война принесла ВСМПО-АВИСМА технологии и поразительные производственные возможности. В 70-х предприятие производило 90 000 тонн в год, больше, чем все остальные предприятия в мире вместе взятые. Сейчас там производится около 32 000 тонн, однако эта цифра растет. В целом, ВСМПО-АВИСМА производит 45% всего титана в мире, который используется в авиакосмической промышленности.
Сотрудничество Boeing и российской компании укрепилось в 2007, когда Госкорпорация Ростех приняла руководство над производством. Ростех организовал поиск клиентов для продукции двойного назначения в гражданском секторе и, таким образом, возрождения российской военной промышленности. Корпорация снабжала титаном как Boeing, так и его главного соперника Airbus, а также Embraer, Bombardier и двигателестроительные компании.
Для Boeing союз с российской аэрокосмической промышленностью не ограничивается поставками титана. В 1990-х при государственной поддержке США Boeing открыла центр проектно-конструкторских работ, так как хотела предотвратить утечку российских авиакосмических инженеров и ракетчиков в страны-изгои. Центр трудоустраивал специалистов, недавно покинувших такие российские компании, как «Илюшин», «Сухой» и «Хруничев», где создаются космические капсулы и спутники.
Большая часть стоимости создается за счет изобретения новых сплавов. Чистый титан стоит около 14 долларов за килограмм, в то время как стоимость сплавов титана с цирконием, никелем и другими металлами может достигать 300 долларов за килограмм. Московский технологический центр уже запатентовал 3 таких сплава.
ВСМПО-ВИСМА – один из немногих успешных производителей в России. В прошлом году Ростех продал контрольный пакет акций руководству компании. Акции ВСМПО-АВИСМА размещены на ММВБ, их рыночная капитализация достигает примерно 2 миллиардов долларов.
Также ВСМПО-АВИСМА снабжает российскую армию. На складе деталей для ракет и самолетов лежат огромные титановые кольца для корпуса МБР «Булава», новейшей российской разработки. Внушительная гора этих деталей похожа на порцию луковых колец, одну из таких, которые обычно подают в конце света. (Большинство потребительских товаров из титана, например, клюшки для гольфа или ледорубы делают в Китае из более дешевых металлов без сплавов.)
Три года назад на ВСМПО-АВИСМА открылось дополнительное производство титана для имплантатов. Линия быстро развивалась, и теперь компания занимает примерно четверть мирового рынка в своей сфере.
По словам Михаила Воеводина, директора предприятия, процесс особенно не изменился, детали штамповки создаются по тем же технологиям. Единственное дополнение – теперь продукция титанового гиганта становится частью человека, а не самолета.
Источник: The New York Times
rostec.ru
кабину Су-34 сваривают по новой технологии » Военное обозрение

На Новосибирском авиационном заводе им. В.П. Чкалова налажено изготовление титановых кабин для бомбардировщика Су-34 при помощи электронно-лучевой сварки. Новая технология позволила усовершенствовать один из самых сложных производственных процессов – сварку титана.
Новый российский бомбардировщик Су-34 заслуженно считается одной из самых безопасных для пилотов машин в мировой авиации. Для их защиты в боевых условиях используется титановая броня толщиной в дюйм и более.
В то же время конструкции из титана едва ли не самые трудоемкие в изготовлении. Именно поэтому обработка этого металла во всех высокотехнологичных отраслях – космосе, авиа- и судостроении – считается самой сложной операцией.
Еще несколько лет назад основные операции по сварке деталей выполнялись специалистами сварочного производства – слесарями и сварщиками – вручную. Детали соединяли при помощи аргонно-дуговой сварки. Процесс занимал длительное время. Сварка листов толщиной до трех миллиметров производилась без специальной предварительной обработки соединяемых частей, а вот при большей толщине приходилось выполнять разделку кромок под сварку.

Установка кабины на сварочную оснастку.
Параллельно с запуском нового самолета в Новосибирске разработали и внедрили первую автоматизированную установку для электронно-лучевой сварки. Из огромной камеры объемом 80 м 3 специальные насосы откачивают воздух и создают высокий вакуум порядка 10-5 мм рт. ст., необходимый для работы электронной пушки. Сварка ведется управляемым электронным лучом.
Однако для серийного производства самолетов такая установка не годилась. Чтобы сваривать швы, расположенные в разных пространственных плоскостях, кабину приходилось каждый раз выдвигать из камеры и переустанавливать в новое положение. После этого процесс создания вакуума в камере вновь повторялся. Это отнимало слишком много времени. Поэтому изготовление первых кабин занимало порядка четырех месяцев.
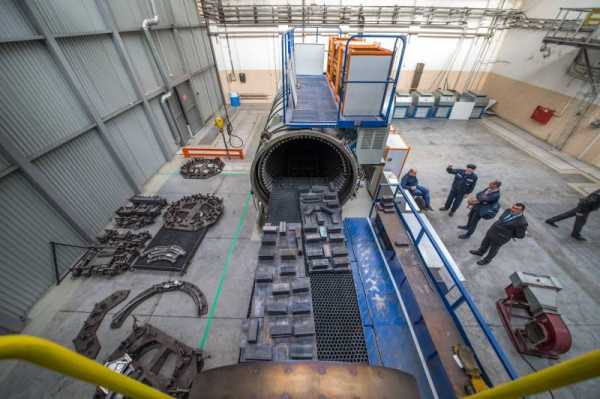
Вакуумная печь.
Специалисты компании «Сухой» и партнеры за два года создали инновационный комплекс оборудования, который кардинально изменил технологический процесс сварочного производства.
Новая установка позволяет сваривать детали толщиной от 2 до 200 мм за один проход луча. Причем сварка может производиться не по двум осям, как раньше (горизонтально и вертикально), а по шести координатам. Сваривать можно как стыковые, так и угловые соединения. Манипулятор по заданной программе обеспечивает перемещение электронной пушки по любой траектории, в любую точку камеры.
«Если проводить какую-нибудь наглядную аналогию, то представьте паука, который передвигается по потолку, — вот такой принцип конструкции использован в нашей установке», — поясняет ведущий инженер-технолог Леонид Егорнов.
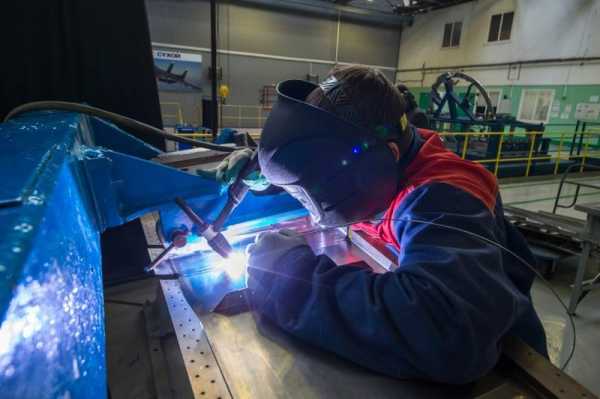
Сварка кольцевых швов бака.
С точки зрения технологии, корпус кабины представляет собой сварную конструкцию из 19 деталей, которые свариваются электронно-лучевой установкой. Суммарная длина швов — 21 метр, скорость сварки — 720 миллиметров в минуту. Теперь для изготовления титановой кабины Су-34 требуется лишь четыре операционные установки изделия в вакуумную камеру, тогда как раньше было необходимо произвести 26 установок в камеру.
В соседнем помещении расположена новая вакуумная печь для отжига, в которую помещают уже сваренную конструкцию. «Отжиг позволяет снять внутренние напряжения, полученные в процессе сварки, что необходимо для предотвращения разрушения сварных соединений», — поясняет Леонид Егорнов.
Параллельно с созданием установки (проектирование, изготовление и монтаж на НАЗ им. В.П.Чкалова) несколько молодых перспективных специалистов были направлены на учебу. Так, сварщик Александр Дырин к моменту запуска новой электронно-лучевой установки окончил кафедру «сварочное производство» Томского политехнического университета. До этого Александр занимался аргоно-дуговой сваркой, изготавливал титановые конструкции по традиционной технологии. Сейчас его основной рабочий инструмент напоминает скорее джойстик из компьютерной игры. С его помощью происходит перемещение электронно-лучевой пушки в вакуумной камере. А на операторском пульте Александр отслеживает десятки параметров работы установки.
Инженер установки Геннадий Вершинин и сварщик Павел Сусликов прошли дополнительное обучение в г. Ижевске в НИТИ «Прогресс». Начальником участка назначен грамотный специалист Алексей Пугаченко. Средний возраст команды – 30 лет.
В конструкции Су-34 применили топливные баки тоже из титана. Их сваривают на этой же установке. Конструкция баков позволяет использовать их и в качестве силовых элементов всего самолета. Технология изготовления топливных баков строится по принципу сварки готовых деталей с минимальными припусками и последующей минимальной мехобработки.
Практически все сварочное оборудование создавал отечественный поставщик — НИТИ «Прогресс» из Ижевска. В разработке новой технологии также участвовали Национальный институт авиационных технологий, специалисты ОКБ «Сухого» и НАЗ им. В.П. Чкалова.
Подобные установки для электроно-лучевой сварки планируется использовать при создании новых самолетов и отдельных агрегатов на других предприятиях ОАК.
Титан среди металлов
Титан – это легкий прочный металл серебристо-белого цвета. Он имеет высокую вязкость, при механической обработке склонен к налипанию на режущий инструмент. Поэтому требуется нанесение специальных покрытий на инструмент, различных смазок. При обычной температуре покрывается защитной пленкой оксида, благодаря этому коррозионностоек в большинстве сред.
По удельной прочности титан не имеет соперников среди промышленных металлов. Даже такой металл, как алюминий, уступил ряд позиций титану, который всего в полтора раза тяжелее алюминия, но зато в шесть раз прочнее. И что особенно важно, титан сохраняет свою прочность при высоких температурах (до +500 °С, а при добавке легирующих элементов – до +650 °С), в то время как прочность большинства алюминиевых сплавов резко падает уже при +300 °С. Титан – очень твердый металл: он в 12 раз тверже алюминия, в 4 раза – железа и меди.
Металл получил свое название в честь титанов, персонажей древнегреческой мифологии, детей Геи. Название элементу дал немецкий химик Мартин Клапрот. Он был одним из первооткрывателей этого химического элемента, обнаружив его в 1795 году в минерале рутиле, состоящем из оксида титана с примесью железа, олова, ниобия и тантала. В то время часто использовались французские названия химических элементов, отражающие их химические свойства. Клапрот предложил называть новый металл «титан». Он отметил, что невозможно определить его свойства только по его оксиду. Поэтому Клапорт выбрал для него имя из мифологии, подчеркивая «мифологичность» и непонятность элемента на тот момент времени. Ранее немец так же из мифологии выбрал название для другого открытого им элемента – урана.
Титан в виде сплавов является важнейшим конструкционным материалом в авиа- и ракетостроении. Добавление к титану других металлов или присадочных материалов, позволяет создавать сплавы с заданной макро-, микро-, кристалло-, суб-, наноструктурой, благодаря чему сам сплав и конструкции из него приобретают определенный уровень механических и эксплуатационных характеристик.
Авиастроение — наиболее титаноемкая отрасль промышленности, где титановый лист используется для изготовления винтов двигателей, корпусов, крыльев, двигателей, обшивки, трубопроводов, крепежа и многого другого. В планере (планер — несущая конструкция летательного средства) современного гражданского самолета применяется 15 — 20% титановых деталей. Например, Ил-76 и Ил-76Т имеют 15% титановых деталей от общей массы планера, а при производстве Boeing нового типа 787 Dreamliner титановые прутки ВТ16 из России используются в 30% сборочных узлов посадочных устройств самолета. Это объясняется тем, что в современных сверхзвуковых самолетах требуются материалы, которые способны гарантировать надежную работу узлов под воздействием мощных силовых и температурных полей, излучений, высоких давлений. Кроме того, с увеличением в конструкциях самолетов доли композиционных материалов, требуется материал, который не корродирует при взаимодействии с ними. Титановые сплавы ВТ23, ВТ23М идеально отвечают всем этим требованиям, обеспечивают авиалайнерам снижение веса и стоимости конструкции на 20-30%, в сравнении с другими материалами, а так же повышает их эксплуатационную надежность на 25-35%.
topwar.ru
Русский титан для самолетов Airbus
Самолетостроение
Журнал «Крылья Родины»в социальных сетях
![]() |
Компания Airbus подписала соглашение с корпорацией ВСМПО-АВИСМА на поставку трех новых штамповок для самолета А350-1000 в рамках долгосрочного партнерского соглашения сроком до 2020 года. Контракт включает в себя поставку титановых штамповок для элементов крыла и основных стоек шасси самолёта А350-1000. Подписанное соглашение является дополнением к существующему контракту между компаниями, в рамках которого корпорация ВМСПО-АВИСМА поставляет такие же штамповки для самолета A350-900.
“Данное соглашение — новый шаг в укреплении наших отношений с корпорацией ВСМПО-Ависма. В этом году мы отмечаем важную дату: 20-летний юбилей сотрудничества с нашим стратегическим партнером в России, что в очередной раз свидетельствует о серьезности наших намерений развивать долгосрочное партнерство, ” – отметил Оливье Кокиль, старший Вице-президент по закупкам и материалам Airbus.
ВМСПО-АВИСМА является ключевым поставщиком титана для Airbus, обеспечивая свыше 60% потребностей компании в этом материале. Компании начали сотрудничество в 90-х годах, когда были подписаны первые соглашения на поставку необработанных материалов. Со временем номенклатура закупаемых изделий значительно изменилась и стала включать обработанные детали более высокой добавочной стоимости.
Важным шагом в укреплении партнёрства стало подписание в 2009 самого крупного и долгосрочного контракта в истории сотрудничества двух компаний. Подписанное соглашение стоимость 4 млрд долларов , предусматривает поставку плоского и круглого проката из титановых сплавов, а также штампованных изделий Airbus и другим подразделениям EADS до 2020 года. В настоящий момент ВСМПО-АВИСМА поставляет Airbus титановые штамповки для всех программ компании, включая недавно запущенную программу А320neo.
Между тем программа летных испытаний А350 XWB идет полным ходом. Самолет совершил свой первый полет 14 июня . Ввод лайнера в коммерческую эксплуатацию намечен на вторую половину 2014 года.
Источник: информационные материалы Airbus
Поделиться с друзьям |
kr-media.ru
Cessna 404 Titan. Фото. Видео. Салон. Характеристики. Отзывы.
26.02.1975 года в компании «Cessna» повился прототип двухмоторного нового самолета Model404, названного впоследствии Titan. Регулярные поставки начались в 1976 году. Новый тип внешне был похож на снабженный турбовинтовыми моторами самолет Conquest. Общим отличием этих двух самолетов был стабилизатор с большим углом поперечного V. Вначале появились две вариации: Titan Ambassador пассажирский, производившийся с разными вариантами внутреннего убранства салона, и многозадачная версия Titan Courier для курьерской службы или для перевозки десяти пассажиров.
В 1982 году предлагалось семь вариантов Titan Ambassador, Titan AmbassadorII и Titan AmbassadorIII. Они имели добавочные комплексы оборудования. Вариация Titan Courier II снабжалась тем же приборным оборудованием, что и AmbassadorII. Выпускались также вариации TitanFreighter и TitanFreighterII с похожей приборной комплектацией. TitanFreighter был грузовым вариантом с ударопрочной отделкой внутреннего убранства из поликарбоната для защиты от повреждений сместившимся грузом фюзеляжа.
Салон Cessna 404 Titan
К моменту, когда производство самолетов Titan прекратилось (1982 год) продали 378 самолетов.
Многоцелевой легкий самолет Cessna404 Titan (Цессна404 Титан) спроектирован в США в 1970-х годах и является развитием меньшего Cessna 402. Серийное изготовление самолета продолжалось в период 1976-1982 годы., построили 378 экземпляров.
Cessna404 производился в пассажирской вариации TitanAmbassador, грузопассажирском конвертируемом TitanCourier и грузовом TitanFreighter.
Авиакомпании, эксплуатирующие самолет: Salmon Air, RVL Aviation, Vincent Aviation.
Характеристики Cessna 404 Titan :
Длина: 12.04м.
Высота: 4.04м.
Вес пустого: 2192кг.
Размах крыла: 14.23м.
Площадь крыла: 22.50кв.м.
Максимальная скорость: 430км./ч.
Крейсерская скорость: 402км./ч.
Потолок: 7925м.
Дальность полета с максимальной загрузкой: 3410км.
Двигатели: 2хПД ContinentalGTSIO520M.
Тяга: 2х375л.с.
Экипаж: 2человека.
Количество пассажирских мест: 8мест.
Максимальная взлетная масса: 3810кг.
Экономичная скорость: 302км/ч.
Максимальная скороподъемность: 591м/мин.
Остальные самолеты
avia.pro