6м80 Станок горизонтальный консольно-фрезерный с поворотным столом
Универсальный консольно-фрезерный станок 6м80 и горизонтальный консольно-фрезерный станок 6м80г выпускался Вильнюсским станкостроительным заводом «Жальгирис».
Первую продукцию станкостроительный завод «Жальгирис» выпустил в 1947 году. Завод специализировался сначала на производстве сверлильных и поперечно-строгальных станков, затем выпускал главным образом горизонтальные, вертикальные, универсальные фрезерные станки, фрезерные полуавтоматы, универсальные прецизионные специализированные фрезерные станки
Станки, выпускаемые Вильнюсским станкостроительным заводом «Жальгирис»
6м80 Станок горизонтальный консольно-фрезерный с поворотным столом — универсальный. Назначение и область применения
Универсально-фрезерный станок, модель 6М80, с поворотным столом и горизонтально-фрезерный станок, модель 6М80Г предназначены для фрезерования небольших деталей из стали, чугуна и цветных металлов цилиндрическими, дисковыми, фасонными, угловыми, торцовыми, концевыми и другими фрезами в условиях индивидуального и серийного производства. Возможность настройки станка на различные полуавтоматические и автоматические циклы позволяет успешно использовать станки для выполнения работ операционного характера в поточных и автоматических линиях в крупносерийном производстве.
На станке можно обрабатывать вертикальные и горизонтальные плоскости, пазы, углы, рамки, зубчатые колеса и т.д. На станке модели 6м80 можно фрезеровать всевозможные спирали, для чего стол его поворачивается вокруг своей вертикальной оси.
На станках удобно выполнять фрезерование торцов, скосов, лысок, шлицев, пазов.
В качестве инструмента могу быть использованы различные типы фрез: цилиндрические, дисковые, фасонные, а также наборы фрез. Возможно также применение торцовых и концевых фрез.
Особенности конструкции и принцип работы станка
Повышенная мощность и широкий диапазон скоростей и подач позволяет успешно работать как быстрорежущими фрезами, так и фрезами, оснащенными пластинками из твердого сплава.
Станки состоят из групп (рис.4), спецификация которых приведена выше.
В станину с задней стороны встраивается коробка скоростей. Клиновые ремни передают вращение на шпиндель, смонтированный в станине. Ременная передача исключает вибрации при работе на высоких скоростях, что выгодно отличает эти станки от станков существующих, где привод на шпиндель жесткий. В верхней части станины сделаны направляющие для хоботов.
Спереди на всей высоте станины идут направляющие для консоли. Последняя служит для размещения на ней салазок столом. С левой стороны консоли монтируется коробка подач.
Электрооборудование монтируется в легкодоступных надежно защищенных нишах станины.
Охлаждение смонтировано на основании под задним кожухом.
Класс точности станка Н по ГОСТ 8—77.
Габаритные размеры рабочего пространства фрезерного станка 6м80, 6м80г
Габарит рабочего пространства фрезерного станка 6м80
Присоединительные базы фрезерного станка 6м80, 6м80г
Присоединительные базы фрезерного станка 6м80
Общий вид горизонтального консольно-фрезерного станка 6м80

Фото фрезерного станка 6м80
Фото фрезерного станка 6м80
Фото фрезерного станка 6м80
Общий вид горизонтального консольно-фрезерного станка 6м80. Смотреть в увеличенном масштабе
Фото фрезерного станка 6м80
Общий вид горизонтального консольно-фрезерного станка 6м80. Смотреть в увеличенном масштабе
Фото фрезерного станка 6м80
Общий вид горизонтального консольно-фрезерного станка 6м80. Смотреть в увеличенном масштабе
Расположение органов управления фрезерным станком 6м80, 6м80г
Расположение органов управления фрезерным станком 6м80
Расположение органов управления фрезерным станком 6м80. Смотреть в увеличенном масштабе
Перечень органов управления фрезерным станком 6м80, 6м80г
- Упоры продольной подачи
- Винт зажима стола
- Рукоятка включения продольной подачи
- Кнопка «Стоп»
- Кнопка «Пуск»
- Маховик ручной поперечной подачи
- Рукоятка вертикального перемещения консоли
- Рукоятка включения поперечной и вертикальной подач
- Рукоятка изменения величины подачи
- Упоры поперечной подачи
- Упоры вертикальной подачи
- Пакетный выключатель «Подача»
- Пакетный выключатель «Шпиндель»
- Пакетный выключатель освещения
- Пакетный выключатель охлаждения
- Пакетный выключатель
- Рукоятка переключения скоростей
- Маховик ручной продольной подачи
- Рукоятка включения перебора
- Кнопка «Толчок»
- Зажим хобота
- Гайка зажима консоли
- Рукоятка зажима салазок на консоли
- Винт зажима салазок
- Рукоятка ускоренного хода
- I Станина 1
- II Коробка скоростей 2
- III Шпиндель 21
- IV Коробка подач 3
- V Консоль 4
- VI Салазки 5
- VII Стол 51
Кинематическая схема фрезерного станка 6м80, 6м80г
Кинематическая схема фрезерного станка 6м80
Главный привод станка
Вращение шпинделя осуществляется от фланцевого асинхронного электродвигателя мощностью 2,8 кВт через шестиступенчатую коробку скоростей, ременную передачу и перебор.
Верхние 6 ступеней чисел оборотов шпинделя получают при включении кулачковой муфты. При этом отключают шестерни перебора 13 и 14.
Таким образом, на высоких скоростях вращение шпинделя в последнем звене осуществляется ремнями, а переборный вал вообще не вращается. Для получения нижних 6 ступеней муфта выключается, переборные шестерни 13 и 14 вводятся в зацепление соответственно с шестернями 12 и 15.
Привод подач
Привод подач осуществляется от асинхронного электродвигателя мощностью 0,6 кВт, встроенного внутрь консоли.
От электродвигателя вращение передается через шестерни 16, 17, 18, 19 на вал Х 12-и ступенчатой коробки подач.
Через коробку подач (валы XI и XII) вращение передается на шестерню 56, сидящую на валу XIII.
В шестерню 56, встроена предохранительная муфта 34.
При включении кулачковой муфты 57 начинают вращаться вал XIII и шестерня 36. Последняя, находясь в зацеплении с шестерней 37, приводит во вращение валы консоли.
Цепь ускоренного хода идет, минуя валы X, XI, XII, с шестерни 19 на шестерню 35, сидящую свободно на валу ХIII. При включении фрикционной муфты 58 начинают вращаться вал ХIII и шестерня 36. Далее движение идет так же, как при рабочих подачах.
Включение продольных, поперечных и вертикальных подач производится соответственно муфтами 49, 72, 73.
Реверсирование подач выполняется посредством конических шестерен 43 и 44 для продольной подачи и паразитной шестерни 69 для поперечной и вертикальной подач.
Устройство и работа станка 6м80, 6м80г. Специфические особенности отдельных узлов станина, хобот, подвеска, поддержка
Станина
В узел «Станина» входят: основание, стойка, дверки, крышки и кожух.
На основании устанавливается стойка, кронштейн с гайкой винта подъема консоли и насос охлаждения. Внутренняя полость основания является резервуаром для охлаждающей жидкости.
Стойка коробчатой формы разделена поперечной вертикальной перегородкой на две части.
В этой перегородке имеется большое окно, через которое вставляется коробка скоростей вместе с управлением.
Небольшое квадратное окно в левой стенке служит для помещения рукоятки переключения скоростей.
Окно в правой стенке служит для монтажа насоса смазки. Передняя стенка стойки выполнена в виде направляющих профиля «ласточкин хвост» для консоли. Такой же формы направляющие выполнены на верхней стенке для хобота.
В верхней части стойки имеются расточки для шпинделя и вала перебора.
Спереди, с левой стороны станины предусмотрен платик для крепления на нем планки с упорами, ограничивающими вертикальный ход консоли.
Хобот представляет собой отливку коробчатой формы. Зажим хобота на стойке осуществляется клином при помощи винта, расположенного сзади стойки.
На хоботе крепятся подвески, которые служат опорами для фрезерных оправок. Одна из них для уменьшения потерь на трение смонтирована на подшипниках качения. Вторая подвеска обеспечивает возможность жесткого фрезерования реечными и цилиндрическими фрезами с размерами менее 75 мм. Опорой для оправки служит бронзовая втулка.
Для увеличения жесткости хобот может быть связан с консолью при помощи поддержки.
Узлы главного привода
Шестиступенчатая коробка скоростей (рис.19) представляет собой отдельный узел, встраиваемый в станину с задней стороны. Коробка привертывается к вертикальной перегородке стойки таким образом, что ее корпус помещается во внутреннем пространстве стойки.
К коробке скоростей прифланцован электродвигатель, соединенный с нижним валом коробки при помощи упругой муфты.
К верхней части коробки скоростей прикреплено натяжное устройство с ведущим шкивом ременной передаче.
При натяжении ремней шестерня 80Г 2424/ 80Г 2429, жестко связанная со шкивом, обкатывается вокруг шестерни 80Г2054, 80Г2055А, сидящей на верхнем валу коробки скоростей.
Шпиндель с перебором (рис. 20) смонтирован непосредственно в стойке. В качестве опор шпинделя применены двухрядные роликовые подшипники 5,6 с посадкой внутреннего кольца на конус. Для восприятия осевых усилий установлены упорные шарикоподшипники 7.
От шкива, находящегося на натяжном устройстве, движение передается на шкив 8, сидящий соосно со шпинделем не отдельных опорах.
На нижних шести ступенях чисел оборотов шпиндель получает вращение через шестерни перебора 10.
Для получения верхних шести скоростей нужно отключить перебор, а шпиндель соединить напрямую с помощью кулачковой муфты 9 со шкивом.
Включение перебора осуществляется посредством рычажного механизма, рукоятка 19 которого выходит на левую сторону станины (рис.4).
Механизм переключения скоростей смонтирован на самой коробке и состоит из диска с кривыми и рычагом переключения (рис.21).
Поворот диска осуществляется рукояткой 17 (рис.4), вынесенной на левую сторону станины.
Числа на лимбе, указывающие скорости при работе с перебором, окрашены в белый цвет, а числа, указывающие работу с отключенным перебором, окрашены в красный цвет. Указатели окрашены тоже в разные цвета.
При переключении следует следить, чтобы цвет указателя совпадал с цветом чисел лимба.
Во избежание возможной путаницы при переключении на левой стороне станины станка имеются таблицы, указывающие работу с перебором и без перебора.
Консоль и коробка подач
Механизмы привода подач размещены в консоли и в коробке подач (см.Рис. 22, 23, 24, 25, 26).
Спереди, в нижнюю часть консоли встроен фланцевый электродвигатель.
С левой стороны консоли присоединяется коробка подач вместе с механизмом переключения подач.
12-ступенчатая коробка подач имеет, кроме цепи рабочих подач, цепь ускоренного хода. В коробке подач есть предохранительная муфта 1, исключающая возможность поломки шестерен при чрезмерной нагрузке.
На одном валу с предохранительной муфтой смонтирована кулачковая 2 и фрикционная 3 муфты включения рабочих подач или ускоренных ходов. Последние две муфты включаются рукояткой 25 (рис.4), расположенной с правой стороны консоли.
Механизм переключения подач (рис.26) принципиально аналогичен механизму переключения скоростей. Рукоятка 8 (Рис.4) переключения подач вынесена на левую стенку консоли.
Рукоятки ручных перемещений стола в поперечном и вертикальном направлениях расположены на консоли спереди. Для включения механических подач в этих направлениях с левой стороны консоли встраивается особый механизм (рис.24).
Кулачок имеет по окружности винтовой паз, в который входит ролик 2 рычага 3. При движении рукоятки 8 вверх или вниз кулачок I поворачивается, и ролик 2 начинает перемещаться вдоль паза. Рычаг 3 поворачивается и включает кулачковую муфту вперед или назад, в зависимости от этого консоль идет или вверх, или вниз.
При перемещении в горизонтальной плоскости рукоятка 6 поворачивает рычаг 5. Одновременно поворачивается рычаг 6, включающий муфту поперечной подачи.
Направление движения рукоятки мнемонически увязано с направлением стола.
Задняя стенка консоли выполнена в виде направляющих профиля «ласточкин хвост».
С правой стороны, сзади имеется гайка 22 (рис.4) для закрепления консоли на стойке.
Салазки и стол
Салазки (рис.28) перемещаются в поперечном направлении по консоли и имеют продольные направляющие для стола.
Со столом связан винт продольной подачи I.
В салазках находятся конические шестерни 2, вращающие винт 1, рукоятка 3 (рис.4) и механизм включения продольной подачи.
Для работы методом попутного фрезерования предусмотрен механизм выборки зазоров между нитками ходового винта и гайками 3,4.
Гайка 3 не может ни поворачиваться, ни перемещаться вдоль оси ходового винта. Гайка 4 выполнена в виде червячного колеса. С этим колесом зацепляется червяк 5, один конец которого выходит на лицевую сторону салазок.
При работе обычным способом люфт выбирается в одну сторону и этим обеспечивается плавность работы. При фрезеровании по подаче люфт не выбирается, и стол идет рывками. Чтобы избежать этого, необходимо выбирать люфт в паре гайка-винт, что осуществляется путем поворота гайки 4 с помощью червяка 5.
Гайки при этом расходятся и выбирают зазоры. При фрезеровании по подаче сильно изнашивается винт, поэтому в крупносерийном производстве, когда на станке может длительное время выполняться одна работа, следует менять участок работы винта.
Наличие дополнительной плиты на станке 6М80 дает возможность осуществлять поворот стола в пределах ±45° в горизонтальной плоскости.
Схема электрическая вертикально-фрезерного станка 6м80
Электрическая схема фрезерного станка 6м80
Электрооборудование фрезерного станка 6м80
6м80 Станок горизонтальный консольно-фрезерный с поворотным столом — универсальный. Видеоролик.
Технические характеристики станков моделей 6м80
Наименование параметра | 6м80 | 6н80 | 6р80 | 6т80 |
---|---|---|---|---|
Основные параметры станка | ||||
Размеры поверхности стола, мм | 800 х 200 | 800 х 200 | 800 х 200 | 800 х 200 |
Наибольшие размеры устанавливаемой детали (длина х ширина х высота), мм | 500 х 160 х 300 | 800 х 260 х 450 | ||
Наибольшие размеры обрабатываемой детали (длина х ширина х высота), мм | 550 х 210 х 330 | |||
Наибольшая масса обрабатываемой детали, кг | 150 | 200 | ||
Расстояние от оси шпинделя до хобота, мм | 140 | 123 | 123 | |
Расстояние от оси шпинделя до поверхности стола, мм | 0..300 | 20..320 | 20..320 | 0..360 |
Расстояние от торца шпинделя до подшипника серьги, мм | 440 | 440 | 450 | |
Расстояние от задней кромки стола до вертикальных направляющих станины (вылет), мм | 80..240 | 75..235 | 80..240 | |
Шпиндель горизонтальный | ||||
Частота вращения шпинделя, об/мин | 50..2240 | 50..2240 | 50..2240 | 50..2240 |
Количество скоростей шпинделя | 12 | 12 | 12 | 12 |
Наибольший крутящий момент на шпинделе, Н*м | 158 | 155 | ||
Конец шпинделя ГОСТ 836-72 (ГОСТ 24644) | № 2 | Конус 40 | Конус 40 | |
Стол. Подачи стола | ||||
Наибольший продольный ход стола (X), мм | 500 | 500 | 500 | 560 |
Наибольший поперечный ход стола (Y), мм | 160 | 160 | 160 | 220 |
Наибольший вертикальный ход стола (Z), мм | 300 | 300 | 300 | 355 |
Угол поворота стола, град | ±45° | ±45° | ±45° | ±45° |
Пределы продольных и поперечных подач стола (X), мм/мин | 16..710 | 25..1120 | 20..1000 | |
Пределы продольных и поперечных подач стола (Y), мм/мин | 11,2..500 | 25..1120 | 20..1000 | |
Пределы вертикальных подач стола (Z), мм/мин | 5,6..250 | 12,5..560 | 10..500 | |
Количество ступеней подач стола (продольных, поперечных, вертикальных) | 12 | 12 | 12 | 18 |
Скорость быстрых перемещений (продольных, поперечных/ вертикальных) X, Y/ Z, мм/мин | 2,8/ 2,0/ 1,0 | 2,3/ 1,6/ 0,8 | 2,3/ 2,3/ 1,1 | 3,35/ 1,7 |
Перемещение стола на одно деление лимба (продольное, поперечное/ вертикальное), мм | 0,05/ 0,02 | 0,06/ 0,02 | 0,06/ 0,02 | 0,05/ 0,02 |
Перемещение стола на один оборот лимба (продольное, поперечное/ вертикальное), мм | 6/ 2 | 6/ 2 | 6/ 2 | 5/ 2 |
Наибольшее допустимое усиле резания (продольное/ поперечное/ вертикальное), кН | 700/ 500/ 500 | |||
Механика станка | ||||
Выключающие упоры подачи (продольной, поперечной, вертикальной) | Есть | Есть | Есть | Есть |
Блокировка ручной и механической подач (продольной, поперечной, вертикальной) | Есть | Есть | ||
Блокировка раздельного включения подач | Есть | Есть | ||
Торможение шпинделя | Есть | Есть | ||
Предохранительная муфта от перегрузок | Есть | Есть | Есть | Есть |
Автоматическая прерывистая подача | Есть | Есть | ||
Электрооборудование и приводы станка | ||||
Количество электродвигателей на станке | 3 | 3 | 3 | |
Электродвигатель главного движения, кВт (об/мин) | 2,8 (1420) | 3,0 | 3,0 | 3,0 |
Электродвигатель привода подач, кВт | 0,6 (1410) | 0,6 | 0,8 | 0,75 |
Электродвигатель зажима инструмента, кВт | — | — | — | |
Электродвигатель насоса СОЖ, кВт | 0,125 (2800) | 0,125 | 0,125 | |
Суммарная мощность всех электродвигателей, кВт | 3,925 | 3,87 | ||
Габариты и масса станка | ||||
Габариты станка (длина ширина высота), мм | 1720 х 1785 х 1578 | 1380 х 1860 х 1530 | 1445 х 1875 х 1730 | 1505 х 1900 х 1808 |
Масса станка, кг | 1400 | 1150 | 1300 | 1340 |
Связанные ссылки
Каталог справочник горизонтальных фрезерных станков
Паспорта и схемы к горизонтальным фрезерным станкам и оборудованию
Справочник деревообрабатывающих станков
Купить каталог, справочник, базу данных: Прайс-лист информационных изданий
stanki-katalog.ru
состав, характеристики, применение, заточка, обработка
Сталь Р6М5 является быстрорежущей и относится к одному из видов инструментальной стали. Она обладает высоким запасом прочности, который позволяет ей обрабатывать твердые материалы. Скорость работы шлифовальных, сверлильных приборов, где ее применяют, при этом превосходит в разы скорость, которую дает обычный сплав. Это не единственное преимущество быстрорежущей стали, маркированной, как Р6М5.

Основные характеристики
К виду рапидных сталей относят сплавы металлов, в которые добавлены дополнительные вещества, улучшающие их химические и физические свойства. Благодаря этому сплав металла становится крепким, износостойким, не способным контактировать с кислородом и покрываться ржавчиной. Быстрорежущая сталь Р6М5 отличается от обычных углеродных сплавов тем, что она может обрабатывать любой твердый материал на высокой скорости, обладая хорошей износостойкостью.

Микроструктура стали Р6М5
Она обладает уникальными свойствами, которые позволяют изготавливать такие инструменты, как фрезы, метчики или развертки. Изготовленные из этого сплава, они будут служить владельцу верой и правдой очень долго.
А к наиболее известным и характеристикам стали марки Р6М5 относятся:
- Твердость стали марки Р6М5 при нагреве. Обычно другие сплавы при длительном и безостановочном бурении, начинают нагреваться, а с повышением температуры, как известно, металл начинается размягчаться. И сверло теряет свои способности и становится хрупким. Эта же быстрорежущая сталь способна нагреваться до 6000 °С, сохраняя свои начальные свойства и не теряя крепости.
- Повышенное сопротивление накаливанию при достаточно высоких температурах.
- Очень хорошо держит заточку.
- Имеет высокую вязкость.
- Отлично обрабатывается на шлифовальном оборудовании.
- Держит нагрузки от удара на отлично.
Характеристики стали Р6М5, перечисленные выше, делают сплав металлов незаменимым в строительстве.
Химический состав
Химический состав стали марки Р6М5 представляет собой нижеперечисленные металлы:
- вольфрам;
- ванадий;
- кремний;
- медь;
- хром;
- марганец.

Химический состав стали Р6М5 и некоторых других быстрорежущих сталей
Сплав с добавлением кобальта, а именно сталь Р6М5К5, используют с начала двадцатого века. Содержание кобальта в изделиях, изготовленных из нее, не выше 15 процентов. Если же легируют ее ванадием и хромом, то металлическая основа ее только повышается. Из этой стали изготавливают такие изделия, как инструменты для резания кислотостойких металлов, жаропрочных, попадающие под аустенитную классификацию. В то время как обработка таких металлов изделиями из другого сплава очень затруднена. Данная сталь отличается повышенной твердостью и теплостойкостью.
Особенности заточки стали
Предметы, полученные из быстрореза, подвергаются частому затуплению. А обычные круги для заточки, которые изготовлены из электрокорунда, не помогут улучшить качество заточки.

Заточка ножа из стали Р6М5
Для того, чтобы правильно заточить инструмент применяют чашечные круги и из плоского профиля. Но, обычно, такая заточка имеет свои минусы. Поэтому, чтобы качественно наточить инструмент из данного вида сплава металла применяют два захода.
- вначале делается предварительная заточка, для которой используется круг с абразивной поверхностью зерна марки 40;
- на чистовую, для которой используется зеро марки от 25 до 16.
Применение сплава
Положительные характеристики данного сплава помогли найти применение этой стали в домашнем обиходе. Из нее изготавливают ножи. Причем, если изделие будет правильно заточено, то оно сможет резать не только плоть животного, но металлическую тонкую пластину.

Диски из стали Р6М5
Единственным минусом такого изделия является его заточка. Но, если знать все хитрости правильной заточки, то данный инструмент станет очень полезным в быту. Такими изделиями чаще всего пользуются охотники и туристы.
Несмотря на дорогую стоимость, применение сплава для ножей стало очень популярно в быту.
Мировым брендом по производству данных режущих инструментов является фирма «Rapid».
У каждого мужчины в доме имеется электроинструмент, в котором, в виде вспомогательной оснастки к нему, используются сверла из этого типа стали. К разновидностям сверл, которые изготавливаются из этой стали Р5М6 относятся:
- корончатые, которые используются для гипсокартона;
- ступенчатые;
- сверла, предназначенные для камня, дерева или металла.
Из данного материала изготавливают не только сверла и ножи. Из стали Р6М5 делают резцы долбежные, ножовочные полотна, зенковки.
Расшифровка маркировки данного сплава
Расшифровка маркировки стали Р6М5 следующая:
- Буква «Р» означает быстрорежущая или рапидная сталь, так как для маркировки бралось сокращение от английского слова «rapid» (на русском читается как рапид), которое в переводе означает «быстрый». А число, которое стоит за этой буквой обозначает процентное соотношение вольфрама в этом сплаве. В данном случае оно равняется 6 %, с небольшими отклонениями.
- Буква «М» показывает на то, что в составе этого сплава присутствует молибден. А число, которое стоит за буквой, также показывает количество его нахождения в сплаве этого металла в процентах.

Пример расшифровки маркировки
Если к этой стали больше не прибавляется никаких дополнительных элементов, то на этом обозначение ее заканчивается. Если же, к сплаву добавлен кобальт, то обозначаться она уже будет, Р6М5К5. Маркировка «Ф» — ванадий, «Т» — титан и другие добавочные элементы.
По ГОСТу сталь Р6М5 делится на следующие изделия, который принадлежит одному из межгосударственных стандартов. В нем описаны все технические требования, относящиеся к этой марке. Хоть и металлопрокат в последнее время переходит уже на твердые сплавы, эта марка все еще удерживает свои лидирующие позиции в спросе на рынке.
Ниже перечислены некоторые изделия из сплава этих металлов и соответствующий ГОСТ к ним:
- круги горячекатанные относятся к ГОСТу под номером 2590-88;
- калиброванный прут имеет ГОСТ 7417-75;
- полосы и пруты (для изготовления этих изделий используется разновидность стали Р6М5К5) – ГОСТ 19265-73;
- круги, у которых имеется специальная отделка верхнего слоя имеют ГОСТ 14955-77.
Скачать ГОСТ 2590-88
Скачать ГОСТ 7417-75
Термическая обработка стали Р6М5
Термическая обработка сплава Р6М5 имеет ряд тонкостей, которые относятся к свойствам ее. Дело в том, что она способна во время нагревания к обезуглероживанию. Чтобы этого не произошло, ее обычно нагревают с помощью медленного прогревания.
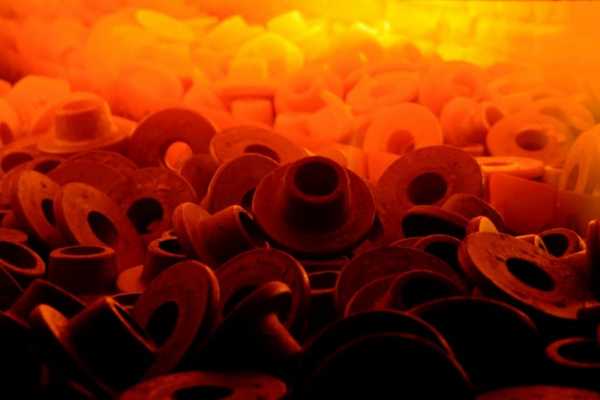
Закалка
Быстрорежущая сталь Р6М5 нагревается до 1230 градусов. Во время нагревания, работники сталелитейного завода внимательно следят за процессом. При первом прогреве температура поднимается до двухсот градусов и нагрев прекращается на час, затем производится еще один дополнительный нагрев до тридцати градусов. И снова отпуск на час. После этого, ее продолжают нагревать до 690 градусов и снова останавливают на час. И последние два нагрева доводят до температуры 860 и 1230 соответственно.
Это очень сложная процедура накаливания. Благодаря такой закалке сплав приобретает свойства, соответствующие ему, но и себестоимость его, кончено же, увеличивается.
После того, как закончится нагрев до 1230 градусов, ее охлаждают, используя селитру, воздух и масло. Затем, температура опускается до 560 градусов. Данная температура выдерживается в течении полутора часов. В это время к стали добавляют различные легирующие элементы, которые улучшают его свойства. А также они придают ему соответствующую твердость.
Перед началом такого длительного прогрева сплав металла отжигают. Это делается для того, чтобы уменьшить хрупкость будущих изделий, сохранив параметры прочности на должном уровне.
Для улучшения характеристики свойств данного сплава, для того, чтобы они обладали хорошей износостойкостью, устойчивостью от коррозии, высокой твердостью используют азотирование. Эта обработка металла проводиться в газовой среде, которая состоит из 80 процентов азота и аммиака двадцати процентов. Время, которое занимает данная процедура, около сорока минут. Температура нагревания будет колебаться от 550 градусов до 6600. Такая закалка позволит сформировать сплаву менее хрупкий слой поверхности.
Такой сплав могут дополнять еще одним элементом, а именно цинком. Оцинкование происходит в газовой или жидкой среде, которая содержит большое количество цинка. Температура нагревания в ней соответствует 5600 градусам. А время составляет около тридцати минут.
Если вы нашли ошибку, пожалуйста, выделите фрагмент текста и нажмите Ctrl+Enter.
stankiexpert.ru
Тяжёлый танк М6. США — Альтернативная История
Несмотря на то, что эта машина выпускалась во время Второй Мировой Войны, она так и не приняла активного участия в боевых действиях и поэтому известна только знатокам истории бронетанковой техники. Широкому кругу любителей истории она практически неизвестна. Хотя с технической точки зрения машина очень интересная. Но её чрезмерный вес и откровенные ошибки в проектировании предрешили её судьбу. Этот тяжёлый танк, по сути, создавался не для армии, а для того, чтобы немного, как сейчас модно говорится, «попилить бабла», лившегося широким потоком для военных заказов.
До самого начала Второй Мировой Войны руководство США не понимало значения танков и не уделяло практически никакого внимания своим таковым войскам. Что и говорить, если до 1939 года не было даже такого рода войск, а танки находились в подчинении пехотного командования.
С началом боевых действий в Европе руководство США поняло своё упущение и стало лихорадочно наверстывать упущенное время. Именно тогда и были сформированы ТТТ к танкам, которые мы знаем по Второй Мировой.
В первую очередь американские военные решили модернизировать свой единственный предвоенный средний танк – М2А1. Его перевооружили 75-мм пушкой (напомню, что у М2А1 была пушка калибром всего 37 мм), и эта машина стала хорошо известна всем любителям истории под именем – М3 Ли/Грант.
Во вторую очередь, американцы решили разработать с нуля тяжёлый танк. По заданным ТТТ его масса должна была находиться в пределах 50–80 тонн. Потом американские военные решили, что погорячились со столь большим диапазоном масс, и уточнили ТТТ, потребовав создание машины в пределах 50 тонн. В качестве бронирования американские военные потребовали установки листов толщиной не менее 75 мм. По общей архитектуре американские военные видели будущую машину многобашенной. Нечто подобное на наш Т-35.
Датой начала разработки американского тяжёлого танка принято считать 11 июля 1939 года. Именно в этот день проект получил название Heavy Tank T1 (тяжёлый танк Т1). За его разработку взялась компания Baldwin Locomotive Works.
С самого начала работы конструкторы решили отказаться от многобашенной схемы. Насколько я понимаю, они просто учли опыт боёв в Европе, в которых многобашенные танки себя полностью дискредитировали. Уже первый деревянный макет машины имел всего одну башню. В качестве основного вооружения на танке было принято применять модернизированную зенитную 75-мм пушку Т9. С ней, в качестве дополнительного вооружения, спарили 37-мм орудие М5Е1. Экипаж у машины получился в 6 человек: командир, наводчик, заряжающий, механик-водитель и помощник механика-водителя. Командир танка располагался слева от пушки, для него была предусмотрена командирская башенка, и он мог вести огонь из пулемёта. У помощника механика-водителя было в ведении сразу два пулемёта. Вероятно, правильней его будет называть просто стрелком. Также в танке было три небольших бойницы для стрельбы из личного оружия. В общей сложности для экипажа на машине предусмотрели 3 люка.
В качестве двигателя для такой тяжёлой машины был выбран двигатель Wright G-200, который развивал мощность 960 л.с. при 2300 об/мин. В качестве трансмиссии для нового танка после множества экспериментов была выбрана трансмиссия Гидроматик.
В конце лета 1940 года компания-разработчик получила добро на изготовление пробной партии танков – в 50 шт.
Первой модификацией нового танка стала машина Т1Е1. От первого прототипа она отличалась установкой на ней газоэлектрической передачи, которую разработала компания General Electric.
Следующая версия машины – Т1Е2 появилась в апреле 1941 года. Эту модель оснастили двухдисковым сцеплением модели T16001. Но в ходе испытаний в ней было обнаружено огромное количество недостатков. Плохо работала трансмиссия и тормоза, плохо работал механизм поворота башни. В ходе испытаний вышел из строя гидроусилитель рулевого управления. Но, тем не менее, машина всё же была запущена в производство. Правда, с некоторыми дополнениями и усовершенствованиями. Вероятно, большое влияние на это решение оказал день проведения испытаний – 8 декабря 1941 года. Испытания проводились как раз на следующий день после нападения на Перл-Харбор. И скорее всего Америка просто боялась входить в войну без тяжёлого танка.

Пилотный танк Т1Е2 во время показа Ordnance Department 8 декабря 1941 на заводе Baldwin Locomotive Works.
Из усовершенствований на серийной машине должны были быть следующие технические изменения: у стрелка оставили только один пулемёт вместо двух (естественно, как можно стрелять сразу из двух пулемётов), место механика-водителя было оборудовано сразу двумя перископами, ещё один перископ появился у стрелка, вместо командирской башенки решили обойтись просто двустворчатым люком. Кроме этого была внесена ещё целая гроздь менее значительных изменений. Но как ни крути, запускать в производство этот танк было ещё рано, он требовал гораздо более серьёзной доработки.
Все доработки производились по ходу производства, и поэтому эта машина обросла огромным количеством различных модификаций:
- T1 — литой корпус, двигатель Wright G-200, трансмиссия Hydromatic
- T1E1 — литой корпус, двигатель Wright G-200, электротрансмиссия GE
- T1E2 — литой корпус, двигатель Wright G-200, Twin Disc torque converter
- T1E3 — сварной корпус, двигатель Wright G-200, Twin Disc torque converter
Своё серийное название первый американский тяжёлый танк получил 26 мая 1942, он стал называться – М6, а модификация Т1Е3 получила название М6А1. Государственный заказ был оформлен на 1084 машины.

Серийный тяжёлый танк М6 на испытательном полигоне General Motors 4 августа 1943 г.

Производственный пилотный тяжёлый танк М6А1 на полигоне General Motors, 22 января 1943. Внешне почти нет отличий от серийного М6, за исключением сварного корпуса.
Но тут случилось необъяснимое: руководство танковых войск урезало заказ до смешных 115 машин. Танкистам эти машины оказались просто не нужны, из-за чрезмерного веса, они не могли их вписать в свои тактические схемы. Из-за этого работы над следующей модификацией танка – Т1Е4 – были приостановлены. Правда, служба снабжения армии США увеличила заказ до 230 машин, наметив поставку 115 танков Великобритании.
Но далее танк М6 встретил такое сопротивление в войсках, а точнее, от командующего бронетанковыми войсками Джейкоба Диверса, что не было сделано не только 230, но даже 115 танков. Реально было построено всего 40 машин.
Мне трудно оценивать, прав или не прав был Диверс, но факт остаётся фактом: когда американцы высадились в Нормандии, они испытывали огромную нужду именно в тяжёлых танках. Бороться с немецкими тяжёлыми машинами им было просто нечем. Хотя не факт, что такая противоречивая машина, как танк М6, смогла бы улучшить ситуацию. Уж очень недоработанной и сырой была её конструкция.
Разбивка выпуска по модификациям таков М6: 8 – М6, 12 – М6А1, 20 – Т1Е1. Кроме этих машин было выпущено ещё 3 танка, и в феврале 1944 года их выпуск был полностью прекращён.

Пилотный тяжёлый танк Т1Е1 с 90-мм пушкой Т7. Смотровой люк водителя и курсовые пулемёты заменены на время тестов стеклом, для удобства.

Серийный американский тяжёлый танк Т1Е1
Но, как ни странно, история первого американского тяжёлого танка на этом не закончилась. Когда в ходе боёв с немцами армия осознала огромную нужду именно в тяжёлых танках, Артиллерийский Департамент (ведомство, отвечавшее за разработку нового танка) решило всё же реанимировать проект. Правда было понятно, что в старом виде пропихнуть его не удастся, поэтому работы по модернизации и усилению М6, закипели с новой силой.
Конструкторы решили убрать лобовой люк мехвода и курсовой пулемёт, как снижающие устойчивость лобового листа брони. Также решили на лоб корпуса наварить броневые экраны, доведя толщину брони аж до 7,5 дюймов (190 мм). В качестве вооружения для танка решили взять 105-мм пушку Т5Е1. Для этого была разработана полностью новая башня, и пришлось поменять её погон с 69-дюймового на 80-дюймовый.
Да, необходимо отметить, что все эти работы велись не над новыми машинами, а над ранее выпущенными в количестве 20 штук танками Т1Е1. Причём из 20 машин 5 ушли на запчасти.
14 августа сильно обновлённый танк был готов и ему присвоили новое название – М6А2Е1. Но танковое руководство, тем не менее, даже слышать ничего не хотело о тяжёлых танках. И даже обновлённой машине так и не довелось поучаствовать в боях. Проект закрыли окончательно.
Тяжёлый танк M6A2E1, приготовленный для испытаний по программе Т29 на Абердинском полигоне, 7 июня 1945 г.
На испытаниях в Абердине Т6А2Е1 весил 77 тонн и показал, что его тактическое применение очень сильно зависело от ровной местности. Когда проект закрыли, то 2 танка Т6А2Е1 оставили для испытаний башни и вооружения для нового тяжёлого танка Т29.
14 декабря 1944 OCM 26039 классифицировал тяжёлые танки М6, М6А1 и Т1Е1, как устаревшие.
Сегодня сохранился единственный Т1Е1 в экспозиции Ordnance Museum в Абердине, США.
alternathistory.com
6М13П станок консольно-фрезерный вертикальный повышенной точностисхемы, описание, характеристики
Сведения о производителе консольно-фрезерного станка 6М13П
Производитель фрезерных станков 6М13П Горьковский завод фрезерных станков, основанный в 1931 году.
Завод специализируется на выпуске широкой гаммы универсальных фрезерных станков, а, также, фрезерных станков с УЦИ и ЧПУ, и является одним из наиболее известных станкостроительных предприятий в России.
Начиная с 1932 года, Горьковский завод фрезерных станков занимается выпуском станков и является экспертом в разработке и производстве различного металлорежущего оборудования.
Универсальные фрезерные станки серии М выпускались Горьковским заводом фрезерных станков (ГЗФС) начиная с 1961 года. Станки сходны между собой по конструкции, широко унифицированы и является дальнейшим усовершенствованием аналогичных станков серии Н.
История выпуска станков Горьковским заводом, ГЗФС
В 1937 году на Горьковском заводе фрезерных станков были изготовлены первые консольно-фрезерные станки серии 6Б моделей 6Б12 и 6Б82 с рабочим столом 320 х 1250 мм (2-го типоразмера).
В 1951 году запущена в производство серия 6Н консольно-фрезерных станков: 6Н12, 6Н13П, 6Н82, 6Н82Г. Станок 6Н13ПР получил “Гран-При” на всемирной выставке в Брюсселе в 1956 году.
В 1960 году запущена в производство серия 6М консольно-фрезерных станков: 6М12П, 6М13П, 6М82, 6М82Г, 6М83, 6М83Г, 6М82Ш.
В 1972 году запущена в производство серия 6Р консольно-фрезерных станков: 6Р12, 6Р12Б, 6Р13, 6Р13Б, 6Р13Ф3, 6Р82, 6Р82Г, 6Р82Ш, 6Р83, 6Р83Г, 6Р83Ш.
В 1975 году запущены в производство копировальные консольно-фрезерные станки: 6Р13К.
В 1978 году запущены в производство копировальные консольно-фрезерные станки 6Р12К-1, 6Р82К-1.
В 1985 году запущена в производство серия 6Т-1 консольно-фрезерных станков: 6Т12-1, 6Т13-1, 6Т82-1, 6Т83-1 и ГФ2171.
В 1991 году запущена в производство серия 6Т консольно-фрезерных станков: 6Т12, 6Т12Ф20, 6Т13, 6Т13Ф20, 6Т13Ф3, 6Т82, 6Т82Г, 6Т82ш, 6Т83, 6Т83Г, 6Т83Ш.
Классификация, обозначение и основные характеристики фрезерных станков
Классификация металлорежущих станков
Ремонт фрезерных станков
6М13П станок консольно-фрезерный вертикальный с поворотной шпиндельной головкой повышенной точности. Назначение, область применения
Вертикальные консольно-фрезерные станки моделей 6М13П и 6М12БП представляют собой электрифицированные станки, обладающие высокой точностью и жесткостью.
Станки предназначены для фрезерования всевозможных деталей из стали, чугуна и цветных металлов торцевыми, цилиндрическими, концевыми, радиусными фрезами в условиях индивидуального и серийного производства. В серийном производстве, благодаря наличию полуавтоматических и автоматических циклов, станки могут успешно использоваться на работах операционного характера в поточных и автоматических линиях.
На станках можно обрабатывать вертикальные и горизонтальные плоскости, пазы, углы, нарезать зубчатые колеса и прочее.
Фрезерование зубчатых колес, разверток, спиралей, контура кулачков и прочих деталей, требующих периодического или непрерывного поворота вокруг своей оси, производятся на данных станках о применением делительной головки или накладного круглого стола.
Благодаря наличию механизма выборки люфта в винтовой паре продольной подачи стола, на станке можно производить встречное и попутное фрезерование, как в простых режимах, так и в режимах с автоматическими циклами.
Наиболее эффективное использование станка достигается при обработке деталей методом скоростного фрезерования.
Класс точности станков Н.
Подбор аналогов к любому станку
Фото вертикального консольно-фрезерного станка 6М13П
Фото вертикального консольно-фрезерного станка 6М13П
Фото вертикального консольно-фрезерного станка 6М13П
Фото вертикального консольно-фрезерного станка 6М13П
Расположение органов управления консольно-фрезерным станком 6М13П
Расположение органов управления консольно-фрезерным станком 6М13П
Расположение органов управления консольно-фрезерным станком 6М13П
Расположение органов управления консольно-фрезерным станком 6М13П
Перечень составных частей консольно-фрезерного станка 6М13П
- Станина
- Поворотная головка
- Коробка скоростей
- Коробка подач
- Коробка переключения
- Консоль
- Стол и салазки
- Электрооборудование
Перечень органов управления консольно-фрезерным станком 6М13П
- Кран регулирования интенсивности охлаждения
- Маховичек ручного продольного перемещения стола
- Кулачки ограничения продольного хода стола в крайних положениях или реверса стола в полуавтоматическом и автоматическом циклах
- Кулачки переключения стола с подачи на быстрый ход или с быстрого хода на подачу
- Переключатель на автоматический цикл или ручное управление станка
- Кнопка «Пуск шпинделя»
- Кнопка «Стоп»
- Кнопка «Быстро»
- Рукоятка ручного насоса смазки стола
- Рукоятка включения вертикальной или поперечной подачи стола
- Рукоятка зажима консоли на направляющих станины
- Маховичек ручного поперечного перемещения стола
- Рукоятка зажима салазок на направляющих консоли
- Переключатель управления столом: автоматический цикл — ручное управление — работа с круглым столом
- Шестигранник поворота фрезерной головки
- Винты зажима стола на салазках
- Маховик перемещения гильзы шпинделя
- Переключатель освещения «Включено — выключено»
- Кнопка «Стоп шпиндель»
- Кнопка «Пуск шпинделя»
- Рукоятка и лимб для переключения скоростей шпинделя
- Кнопка «Импульс шпинделя»
- Кнопка «Быстро стол»
- Вводной переключатель «Включено — выключено»
- Переключатель насоса охлаждения «Включено — выключено»
- Переключатель направления вращения шпинделя «Влево — вправо»
- Рукоятка управления продольным перемещением стола
- Рукоятка подъема консоли
- Грибок и лимб для переключения подач стола
- Кулачки ограничения поперечного хода стола
- Рукоятка зажима гильзы шпинделя
- Кулачки ограничения вертикального хода стола
- Кнопка включения фиксации механизма переключения подач
- Гайки зажима поворотной фрезерной головки
Схема кинематическая консольно-фрезерного станка 6М13П
Кинематическая схема консольно-фрезерного станка 6М13П
Схема кинематическая консольно-фрезерного станка 6М13П. Смотреть в увеличенном масштабе
Цепь главного движения консольно-фрезерного станка 6М13П
Станок 6М13П имеет две раздельные кинематические цепи — цепь главного движения и цепь подач стола.
Шпиндель получает вращение от фланцевого электродвигателя мощностью 7 кВт, с 1440 об/мин через упругую соединительную муфту и зубчатые колеса механизма пятиваловой коробки скоростей, сообщающие шпинделю 18 различных чисел оборотов в пределах от 31,5 до 1600 об/мин.
Коробка скоростей и шпиндель консольно-фрезерного станка 6М13П
Коробка скоростей и шпиндель фрезерного станка 6М13П
Коробка скоростей консольно-фрезерного станка 6М13П
Коробка скоростей фрезерного станка 6М13П
Коробка скоростей смонтирована непосредственно в верхней части корпуса станины и управляется с помощью вставной коробки переключения скоростей, расположенной с левой стороны станины. Для осмотра коробки скоростей достаточно снять крышку, находящуюся с правой стороны станины.
Шпиндель (вал VII) станка 6М13П (см. рис. 274, б) смонтирован в поворотной головке, которая центрируется в кольцевой выточке горловины станины и крепится к ней четырьмя болтами 1 (рис. 275). Поворотная головка может быть повернута на 45° от вертикальной оси в обе стороны
Выдвижение гильзы поворотной головки производят маховичком 2. Маховичок через коническую пару 7 (см. рис. 274, б) и винт с гайкой связан с кронштейном 5, закрепленным на гильзе. На валике маховичка 2 (рис. 275) закреплен лимб, цена деления которого 0,05 мм. За полный оборот маховичка гильза выдвигается на 4 мм.
В кронштейне 5 (рис. 274, б) предусмотрено отверстие и винт для закрепления индикатора, а к корпусу поворотной головки привинчен кронштейн 8 с регулируемым упором 6 для настройки перемещения гильзы.
Для увеличения жесткости шпинделя во время работы предусмотрен зажим рукояткой 4, которая стягивает корпус поворотной головки, имеющей разрез 5 (рис. 275).
Вращение шпинделю (валу VII) передается от коробки скоростей через коническую и цилиндрическую передачи (см. рис. 274, б). Цилиндрическое зубчатое колесо 2 закреплено на втулке, смонтированной на шарикоподшипниках и имеющей шпонку, которая входит в шпоночный паз шпинделя.
Вал VI станка 6М13П смонтирован на одном радиальном и двух радиально-упорных шарикоподшипниках. Радиально-упорные шарикоподшипники расположены во фланце и стянуты шайбой, которая крепит фланец к поперечной стенке станины. Зазор в радиально-упорных подшипниках регулируется подшлифовкой промежуточных колец. Сцепление конического зубчатого колеса регулируется путем осевого перемещения всего вала VI винтами, ввернутыми во фланец (рис. 274, б).
Вал V смонтирован также на одном радиальном и двух радиально-упорных шарикоподшипниках. Регулирование зазора производится подтягиванием гайки с левого торца вала V.
Вал IV коробки скоростей у всех трех станков этой гаммы, т. е. 6М82, 6М82Г и 6М13П (рис. 274, а и б), для большей жесткости расположен на трех опорах.
Валы II, III и IV — шлицевые для возможности передвижения зубчатых блоков.
Как указывалось ранее, в коробках скоростей этих станков механизм переключения скоростей является самостоятельным узлом (рис. 276). На корпусе механизма переключения скоростей расположен лимб 1 из пластмассы, на котором нанесены значения всех 18 чисел оборотов шпинделя, стрелка указатель и кнопочная станция 2 с переключателем освещения и кнопками: «пуск шпинделя», «стоп шпинделя», «толчок шпинделя», «быстро стол». С нижней стороны коробки переключения находится рукоятка 3.
Скорости переключаются следующим образом:
- рукоятку 3 опускают вниз, при этом ее шип выводится из фиксирующего паза, и отводят на себя до отказа;
- поворачивают лимб 1 вправо или влево до совпадения выбранного числа оборотов шпинделя со стрелкой-указателем; при этом щелчок фиксатора указывает, что лимб установлен в заданном положении;
- нажимают кнопку «толчок», что дает кратковременный импульс на электродвигатель привода шпинделя для провертывания зубчатых колес коробки скоростей, во избежание того, чтобы торцы зубьев блоков колес не уперлись друг в друга при переключении скоростей;
- досылают плавным движением рукоятку 3 в первоначальное положение, при этом она обязательно должна быть заперта шипом в фиксирующем пазу.
- При этих операциях с рукояткой и лимбом блоки зубчатых колес коробки скоростей перемещаются и устанавливаются в положениях, соответствующих выбранному числу оборотов шпинделя.
Механизм подач консольно-фрезерного станка 6М13П
Механизм подач фрезерного станка 6М13П
Цепь подач консольно-фрезерного станка 6М13П
Привод подач осуществляется от отдельного фланцевого электродвигателя мощностью 1,7 кВт при 1420 об/мин, смонтированного в консоли. Через коробку подач ходовым винтам продольного и поперечного перемещений стола сообщаются 18 различных подач в пределах от 25 до 1250 мм/мин, а винту вертикального перемещения стола — 18 различных подач в пределах от 8,3 до 416,6 мм/мин.
Вал I коробки подач (см. рис. 272) приводится во вращение непосредственно электродвигателем; от него вращение передается валу II зубчатой парой 26 : 50, валу III — зубчатой парой 26 : 57, валу IV — зубчатыми парами 18 : 36, или 27 : 27, или 36 : 18, валу V — зубчатыми парами 18 : 40, или 21 : 37, или 24 : 34 и далее валу VI через перебор 13 : 45 — 18 : 40 или непосредственной зубчатой передачей 40 : 40.
Консоль фрезерного станка 6М13П
В консоли расположены все узлы цепи подач. На рис. 284 схематически показана консоль фрезерных станков 2-й гаммы с механизмами передачи движения от электродвигателя к столу, салазкам и самой консоли.
Консоль имеет чугунный корпус с развитыми направляющими профиля «ласточкин хвост» под станину и перпендикулярные к ним прямоугольные направляющие под салазки. Консоль несет на себе следующие органы управления:
Схема электрическая принципиальная фрезерного станка 6М13П
Электрическая схема принципиальная фрезерного станка 6М13П
Схема электрическая принципиальная консольно-фрезерного станка 6М13П. Скачать в увеличенном масштабе
Описание электрооборудования станка 6М13П
Электрооборудование станка предназначено для питания от сети трехфазного тока напряжением 380 В с частотой 50 Гц. По особому заказу оно может быть выполнено и на другие стандартные напряжения: 220 В или 500 В, а также на частоту сети 60 Гц.
В электрической схеме станка (рис. 50) предусмотрены: питание цепи управления от сети напряжением 127 в, питание цепи местного освещения от сети напряжением 36 В, нулевая защита всех электродвигателей, а также защита от коротких замыканий плавкими предохранителями и от перегрузок при помощи тепловых реле.
Вся пусковая электроаппаратура установлена в двух нишах станины станка.
В каждой нише имеется по две панели с электроаппаратурой; четыре панели составляют комплект панелей управления станка, имеющий общую монтажную схему (рис. 51).
Для подключения электрооборудования к сети и его отключения имеется вводный выключатель, рукоятка которого расположена на дверке левой ниши.
Управление электродвигателем шпинделя — кнопочное. Выбор направления вращения шпинделя производится реверсивным переключателем ПР, который устанавливает нужное вращение двигателя шпинделя.
Управление электродвигателем подачи производится от двух командоаппаратов.
Командоаппарат продольной подачи 1КА состоит из двух конечных выключателей: для включения правого и левого ходов стола.
Командоаппарат поперечной и вертикальной подач 2КА также состоит из двух конечных выключателей. Рукоятка командоаппарата 2КА имеет пять положений: назад, вниз, вперед, вверх и среднее нейтральное.
Для выполнения на станке разных режимов работы в электросхеме имеется переключатель ПУ на три положения рукоятки. При первом положении — «Автоматический цикл» — выполняются только автоматические циклы продольного хода стола, при втором положении — «Подача от рукояток» — производится нормальная работа станка и при третьем положении — «Круглый стол» — производится работа круглым столом, который как приспособление может быть установлен на столе станка.
Управление вращением круглого стола происходит при одностороннем вращении двигателя подачи.
Электронасос для охлаждающей жидкости управляется от выключателя ВО.
Выключатель ВМО служит для отключения местного освещения станка.
Специальный электромагнит ЭБ постоянного тока (рис. 52) служит для привода фрикционной муфты быстрого хода.
Одновременно с включением быстрого хода электромагнит отключает кулачковую муфту подачи.
Питание электромагнита ЭБ выполняется от селенового выпрямителя ВС, основное назначение которого — давать подмагничивающий ток двигателю шпинделя при торможении.
Вводный выключатель ВВ и реверсивный переключатель ПР предназначены для отключения ненагруженных цепей, поэтому при пользовании этими аппаратами электродвигатель шпинделя необходимо предварительно отключить кнопкой «Стоп».
Работа электросхемы при ручном управлении
Переключатель управления ПУ должен быть установлен в положении «Подача от рукояток».
После выбора направления вращения шпинделя переключателем ПР рукоятку вводного выключателя ВВ необходимо установить в положение «Включено». При этом будет подано напряжение сети на, клеммы магнитного пускателя ПШ.
От нажатия кнопки «Шпиндель» магнитный пускатель ПШ включается, и двигатель шпинделя будет вращаться.
При включенном пускателе ПШ рукояткой командоаппарата 1КА (или 2КА) можно включить движение стола со скоростью рабочей подачи. Для получения движения стола вправо (или назад, вниз) включается пускатель ПП, при левом ходе (или ходах вперед, вверх) работает пускатель ПЛ двигателя подачи.
Движение стола со скоростью быстрого хода происходит только при нажатой кнопке «Быстро», которая включает пускатель ПБ электромагнита быстрого хода.
Быстрым ходом стола можно пользоваться как при включенном, так и при отключенном двигателях шпинделя. При отключенном шпинделе быстрый ход осуществляется благодаря шунтированию контакта ПШ 12-28 контактом ПБ при нажатии кнопки «Быстро».
Автоматический останов двигателя подачи при движении стола (консоли или салазок) происходит при переводе концевым кулачком рукоятки командоаппарата 1КА (или 2КА) в нейтральное положение, при этом разрывается цепь питания пускателя ПП (или ПЛ), и двигатель останавливается.
Работа электросхемы при автоматическом управлении
Автоматическое управление применяется только для продольного хода стола.
На станке можно выполнять следующие автоматические циклы:
- правый скачкообразный с реверсом
- левый скачкообразный с реверсом
- маятниковый
При маятниковом цикле рабочая подача стола автоматически чередуется с быстрым ходом в каждом направлении.
Для работы на автоматическом цикле переключатель ПУ должен быть установлен в положение «Автоматический цикл».
Кроме того, необходимо также сделать механическое переключение валика, имеющегося в салазках станка, из положения «Ручное управление» в положение «Автоматический цикл». При последнем положении валика кулачковая муфта продольного хода заперта, и конечный выключатель 4КА нажат. Это обеспечивает управление продольным движением стола только от командоаппаратов 1КА и ЗКА при сблокированных поперечной и вертикальной подачах.
Для объяснения работы схемы в автоматическом цикле разберем выполнение правого скачкообразного цикла с реверсом. Этот цикл состоит из автоматических переключений:
- с быстрого хода вправо на подачу вправо
- с подачи вправо на быстрый ход влево
- с быстрого хода влево на «Стоп»
Для получения быстрого хода стола в начале цикла нужно предварительно убедиться в том, что командоаппарат ЗКА, управляющий работой пускателя ПБ при автоматических циклах, находится в не нажатом состоянии, т. е. через его контакт 43-26 происходит питание пускателя ПБ.
Если контакт ЗКА 43-26 не закрыт, то необходимо сделать поворот звездочки с восемью выступами, сидящей на валу рукоятки командоаппарата 1КА на один выступ, после чего контакт ЗКА 43-26 закроется.
При повороте рукоятки командоаппарата 1КА вправо включится быстрый ход стола вправо, так как произойдет включение пускателей /7/7 для двигателя подачи и ПБ для электромагнита.
Отключение быстрого хода происходит, когда в нужной точке пути стола откидной кулачок сделает поворот звездочки на один выступ, при этом контакт 43-26 командоаппарата ЗКА раскроется, электромагнит ЭБ будет отключен, и стол продолжит движение со скоростью рабочей подачи.
Для переключения движения в нужной точке пути с рабочей подачи вправо на быстрый ход влево в пазу стола должны быть установлены рядом два кулачка:
- кулачок № 1 для перевода рукоятки командоаппарата из положения вправо в положение влево
- кулачок № 3 (откидной) для отключения подачи вправо и включения быстрого хода
Когда кулачок № 1 переводит рукоятку командоаппарата 1КА в положение влево, то перед моментом раскрытия контакта 15-16 от нажатия кулачка № 3 на звездочку с выступами в командоаппарате ЗКА контакт 43-26 уже закрывается, что обеспечивает питание пускателя ПП по цепи 15-42-43-25-16 при раскрытом контакте 15-16 командоаппарата 1КА (см. в схеме диаграмму переключателя ЗКА).
После перевода рукоятки в положение влево кулачок 3 повернет звездочку на один выступ и в командоаппарате ЗКА раскроется контакт 43-26, отключая пускатель ПП — подача вправо. Закрытие нормально закрытого контакта пускателя ПП 22-18 замыкает цепь питания пускателя ПЛ, и двигатель реверсируется. Одновременно контакт ЗКА 43-26 включает пускатель ПБ, и стол идет быстро влево.
Остановка быстрого хода влево происходит при переводе кулачком № 2 рукоятки командоаппарата 1КА в нейтральное положение, в котором отключаются двигатель подачи и электромагнит ЭБ.
Наладку на автоматические циклы следует производить без обрабатываемой детали, так как ошибки при наладке могут привести к включению быстрого хода вместо подачи, что может вызвать поломку инструмента.
Работа схемы при остальных автоматических циклах аналогична вышеописанной.
Импульсное включение двигателей
Для получения быстрого сцепления зубьев зубчатых колес при переключениях скоростей шпинделя предусмотрен кратковременный поворот двигателя шпинделя.
Для указанной цели имеется кнопка «Толчок», при нажатии которой двигатель шпинделя получает кратковременное вращение. Кратковременность включения пускателя ПШ происходит благодаря тому, что при его включении получает питание реле РП, которое, становясь на самопитание, разрывает своим контактом 33-27 цепь питания пускателя ПШ.
При переключениях подачи также имеется возможность кратковременного включения двигателя подачи с помощью конечного выключателя KB, который включает двигатель в то время, когда ручка переключения находится в выдвинутом положении.
Торможение шпинделя
Электропривод шпинделя имеет динамическое торможение двигателя, которое благодаря плавно нарастающему тормозному моменту лучше обеспечивает сохранность механизма при эксплуатации, чем другие способы торможения.
Для выполнения динамического торможения установлено следующее электрооборудование:
- Селеновый выпрямитель ВС, соединенный со специальной обмоткой трансформатора ТУ. Эта обмотка имеет напряжение 55 В при напряжении сети 380 В и 36 В при 220 В.
- Магнитный пускатель ПТ для включения постоянного тока в обмотку статора двигателя на время торможения.
- Промежуточное реле РН, имеющее катушку для напряжения сети трехфазного тока.
При нажатии кнопки «Стоп» ее нормально закрытый контакт отключает пускатель ПШ, и статор двигателя от сети отключается. В отключенной обмотке статора затухающее поле ротора наводит напряжение, приблизительно равное напряжению сети.
Во избежание пробоя селенового выпрямителя последний включается в цепь статора только после снижения наведенного напряжения до малой величины. Контроль исчезновения наведенного напряжения выполняет реле напряжения РН.
Когда реле РН обесточивается, оно своим нормально закрытым контактом 23-41 замыкает цепь питания пускателя ПТ, который подает в обмотку статора постоянный подмагничивающий ток, чем обеспечивается торможение двигателя.
После остановки шпинделя кнопку «Стоп» отпускают, при этом пускатель ПТ отключает селеновый выпрямитель от статора.
Процесс торможения двигателя длится при наибольшей включенной скорости шпинделя 1600 об/мин 3—5 сек.
Блокировки станка
Электросхема имеет ряд блокировок, которые введены для обеспечения правильной эксплуатации станка и его электрооборудования:
- Одновременное включение рукояток командоаппаратов 1KA и 2КА вызывает остановку двигателя подачи, так как совместная работа двух подач не допускается кинематикой станка
- В положении переключателя ПУ «Автоматический цикл» исключены работа поперечной и вертикальной подач и управление от кнопки «Быстро»
- В положении переключателя ПУ «Круглый стол» работа продольной, поперечной и вертикальной подач невозможна
- В положении переключателя ПУ «Подача от рукояток» нормально замкнутые контакты в реверсивном пускателе двигателя подачи зашунтированы для получения принудительного реверсирования двигателя подачи в случае «прилипания» якоря к неподвижному сердечнику магнита в пускателе
- Не допускается рабочая подача во всех направлениях, а также вращение круглого стола при не включенном двигателе шпинделя.
6М13П станок консольно-фрезерный вертикальный с поворотной головкой. Видеоролик.
Технические характеристики консольного фрезерного станка 6М13П
Наименование параметра | 6Н13 | 6М13 | 6Р13 | 6Т13 |
---|---|---|---|---|
Основные параметры станка | ||||
Класс точности по ГОСТ 8-71 и ГОСТ 8-82 | Н, П | Н, П | Н, П | Н |
Размеры поверхности стола, мм | 400 х 1600 | 400 х 1600 | 400 х 1600 | 400 х 1600 |
Наибольшая масса обрабатываемой детали, кг | 300 | 630 | ||
Расстояние от торца шпинделя до стола, мм | 30..520 | 30..500 | 30..500 | 70..500 |
Расстояние от оси шпинделя до вертикальных направляющих станины (вылет), мм | 450 | 450 | 420 | 460 |
Рабочий стол | ||||
Наибольший продольный ход стола от руки (по оси X), мм | 900 | 800 | 1000 | 1000 |
Наибольший поперечный ход стола от руки (по оси Y), мм | 320 | 320 | 320 | 400 |
Наибольший вертикальный ход стола от руки (по оси Z), мм | 420 | 420 | 420 | 430 |
Перемещение стола на одно деление лимба (продольное, поперечное, вертикальное), мм | 0,05 | |||
Перемещение стола на один оборот лимба (продольное, поперечное/ вертикальное), мм | 6/ 2 | |||
Пределы продольных подач стола (X), мм/мин | 23,5..1180 | 25..1250 | 25..1250 | 12,5..1600 |
Пределы поперечных подач стола (Y), мм/мин | 15,6..786 | 25..1250 | 25..1250 | 12,5..1600 |
Пределы вертикальных подач стола (Z), мм/мин | 7,85..393 | 8,3..416,6 | 8,3..416,6 | 4,1..530 |
Количество подач продольных/ поперечных/ вертикальных | 18 | 18 | 18 | 22 |
Скорость быстрых продольных перемещений стола (по оси X), м/мин | 2,3 | 3 | 3 | 4 |
Скорость быстрых поперечных перемещений стола (по оси Y), м/мин | 1,540 | 3 | 3 | 4 |
Скорость быстрых вертикальных перемещений стола (по оси Z), м/мин | 0,77 | 1 | 1 | 1,33 |
Шпиндель | ||||
Частота вращения шпинделя, об/мин | 30..1500 | 31,5..1600 | 31,5..1600 | 31,5..1600 |
Количество скоростей шпинделя | 18 | 18 | 18 | 18 |
Перемещение пиноли шпинделя, мм | 85 | 85 | 80 | 80 |
Перемещение пиноли шпинделя на одно деление лимба, мм | 0,05 | 0,05 | 0,05 | 0,05 |
Конус фрезерного шпинделя | №3 ГОСТ 836-47 | №3 ГОСТ 836-62 | №3 ГОСТ 836-62 | |
Конец шпинделя ГОСТ 24644-81, ряд 4, исполнение 6 | ||||
Отверстие фрезерного шпинделя, мм | 29 | 29 | ||
Диаметр оправок, мм | 32, 50 | |||
Диаметр переднего подшипника, мм | 100 | |||
Поворот шпиндельной головки вправо и влево, град | ±45 | ±45 | ±45 | ±45 |
Механика станка | ||||
Выключающие упоры подачи (продольной, поперечной, вертикальной) | Есть | Есть | Есть | Есть |
Блокировка ручной и механической подач (продольной, поперечной, вертикальной) | Есть | Есть | Есть | Есть |
Блокировка раздельного включения подач | Есть | Есть | Есть | Есть |
Торможение шпинделя | Есть | Есть | Есть | Есть |
Предохранительная муфта от перегрузок | Есть | Есть | Есть | Есть |
Автоматическая прерывистая подача | Есть | Есть | Есть (продольная) | Есть |
Электрооборудование, привод | ||||
Количество электродвигателей на станке | 3 | 3 | 3 | 4 |
Электродвигатель привода главного движения, кВт | 10 | 10 | 10 | 11 |
Электродвигатель привода подач, кВт | 2,8 | 3,0 | 3,0 | 3,0 |
Электродвигатель зажима инструмента, кВт | нет | нет | нет | 0,25 |
Электродвигатель насоса охлаждающей жидкости, кВт | 0,125 | 0,125 | 0,125 | 0,12 |
Суммарная мощность всех электродвигателей, кВт | 12,925 | 13,125 | 14,37 | |
Габарит и масса станка | ||||
Габариты станка (длина ширина высота), мм | 2575 х 1870 х 2250 | 2565 х 2135 х 2235 | 2560 х 2260 х 2120 | 2570 х 2252 х 2430 |
Масса станка, кг | 4250 | 3120 | 4200 | 4300 |
Связанные ссылки
Каталог справочник фрезерных станков
Паспорта и руководства по эксплуатации фрезерных станков
Справочник деревообрабатывающих станков
Прайс-лист информационных изданий
stanki-katalog.ru
Американский тяжелый танк М6 » Военное обозрение
Вторая мировая война сдвинула с мертвой точки американское танкостроение. Однако упор главным образом делался на легкие танки, которые могут вести маневренную войну, глубоко прорываясь в тыл врага. При этом укрепрайоны и сильные узлы сопротивления планировалось попросту обходить. Порукой тому являлся опыт применения немецких танковых войск во французской и польской кампаниях. В результате на начало войны в танковой дивизии США два полка были вооружены легкими танками и лишь один средними танками М3. Однако даже к М3 военные США подходили достаточно осторожно, надеясь вначале испытать машину в реальных боевых условиях, до того как дать зеленый свет массовому производству и увеличению количества танковых подразделений вооруженных данной машиной. Тем не менее, некоторые сообщения об использовании тяжелого танка в Европе во время боев (например, появление в печати фотографий трехбашенных немецких тяжелых танков в Норвегии), оставить равнодушными военных США не могли. В результате командующий сухопутными войсками 20 мая 1940 года санкционировал работы по тяжелому танку весом около 50 тонн.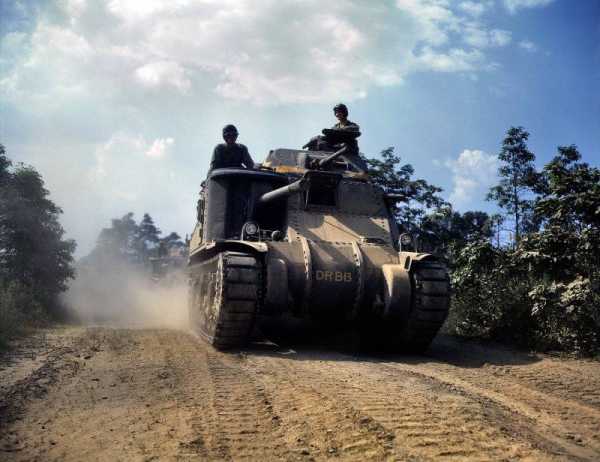
Средние танки М-3 «Генерал Ли» совершают марш на учениях на танковом полигоне в Форте Нокс
Американцы оригинальными не были, подобно многим тяжелым танкам межвоенного периода они новую боевую машину видели многобашенной: танк имел четыре башни — две оснащались 76-миллиметровыми короткоствольными пушками, одна пулеметом и 37-миллиметровой пушкой и одна пулеметом и 20- миллиметровой пушкой. Данный довольно ретроградский проект одобрили и присвоили обозначение Т1. Попытка создать макет крепости на колесах стала причиной корректировки проекта, и было принято решение оставить одну башню имеющую широкий погон, однако с длинноствольной пушкой калибра 76 мм на базе зенитного орудия Т9 выполненного в одной маске с пушкой М5Е1 калибра 37 миллиметров. На башне должны были установить командирскую башенку от М3 с пулеметом калибра 7,62 миллиметра. По бортам корпуса монтировалось два неподвижных пулемета калибра 7,62 мм. Огонь из них вел механик-водитель. Его помощник имел в распоряжении еще спарку 12,7- миллиметровых пулеметов смонтированных в подвижной установке. Кроме того, на кольцевой установке, на башне монтировался зенитный пулемет калибра 12,7 мм.
Основной проблемой при разработке машины весом 50 тонн являлся выбор силовой установки. Выбор после ряда проработок остановили на двигателе Райт G-200 мощностью 960 л.с. с гидромеханической трансмиссией и воздушным охлаждением. Правда, позже начали прорабатывать вариант с электротрансмиссией разработанной «Дженерал электрик». Машина с данной трансмиссией получила называние Т1Е1. Однако к моменту готовности первого опытного образца данные трансмиссии готовы еще не были. В результате выбор был сделан в пользу механической трансмиссии, а танк был переименован в Т1Е2. Головной компанией по сборке танков Т1Е2 стала «Бэлдвин локомотив воркс», которая в августе 41-го года начала заводские испытания первого прототипа. Одновременно компания готовила серийное производство.

Опытный танк Т1Е2
Уже на следующий день после того как на Перл-Харбор напали японцы Т1Е2 и серийный образец среднего танка М3 официально представили Департаменту вооружений. Несмотря на грозный вид, демонстрация Т1Е2 показала серьезные проблемы в части трансмиссии машины. Так, например, во время прогона по полигону у танка заклинили коробка передач и тормоз. Водителю пришлось управлять танком при помощи ручных тормозов, не переключая коробку передач. Башню также заклинило.
Танк для доработки вернули в цех. В результате модернизации система вентилятора охлаждения двигателя и выхлопа, внешний вид силового отделения значительно изменился. Машину планировали максимально унифицировать с серийным средним танком М3 и танком М4, снять командирскую башенку и один неподвижный пулемет.
Вступление Соединенных Штатов в войну заставило американских военных ускорить запуск тяжелого танка в серию. Было решено поставить Т1Е2 в производство до окончания полного цикла испытаний, подобно тому, как ранее поступили со средним М3. Выявленные недоработки планировалось исправлять на сборочных линиях. Лихорадочные работы по запуску серийного производства танка привела к решению использовать все, что имелось под рукой, например гидромеханической трансмиссии и дизеля «Дженерал моторс». При этом корпус танка выполнялся и сварным, и литым. Модель танка с литым корпусом, двигателем «Форд» и механической трансмиссией был назван Т1Е2, со сварным корпусом – Т1Е3. Было решено приобрести 1084 данных машин, которые 13 апреля 1942 года были соответственно переименованы в М6 и М6А1.

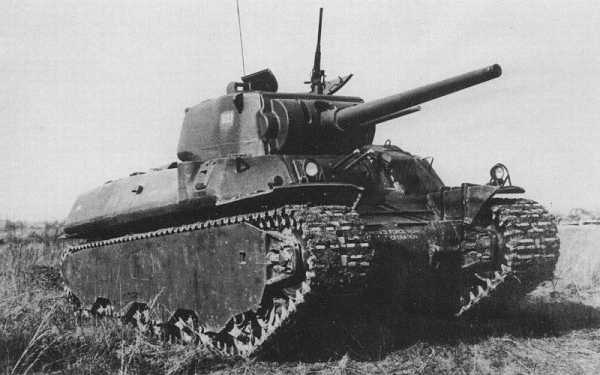




Танк М6
Бронетанковые войска к тому времени, столкнувшись с проблемой переброски танков на заморские театры военных действий, решили, что за море легче перевести два средних танка массой 30 тонн, чем один тяжелый танк массой 60 тонн – по мнению танкистов армии США два средних танка были гораздо эффективнее, чем один тяжелый. В результате заказ сократили до 115 машин.
Спешка с производством стала причиной того, что специально спроектированную гидромеханическую трансмиссию так и не установили на него. Зато танк с электротрансмиссией был успешно испытан. По результатом испытаний решили расширить заказ до 230 машин. При этом танки имеющие электротрансмиссию должны были поступать на вооружение американской армии, а с механической – поставляться по ленд-лизу союзникам. Новой модели даже планировали дать название М6А2. Однако к тому времени, танкистам удалось окончательно убедить командование американских сухопутных войск в отсутствии необходимости в тяжелых танках. Служба снабжения армии в результате решила прекратить с 40-й машины серийное производство танков М6.

Опытный танк М6А2Е1
Правда армией уже выпущенные танки испытывались на Абердинском полигоне и пришла к неутешительным итогам: машина была никуда не годной. Вооружение танка, для его массы, было слабым, пушка калибра 37 миллиметров была не нужна вообще, серьезные просчеты имелись и в компоновке боевого отделения. Исправить положение хотели установкой в танк пушки калибра 90 миллиметров, однако башня для этого была тесной.
Тем не менее, два года спустя после решения прекратить работы по тяжелому танку М6, к танкам подобного класса опять возник интерес. После высадки в Нормандии союзников уже выпущенные серийные танки хотели модифицировать за счет экранировки довода до 190 миллиметрам толщины брони лобовой детали и установки новой башни с пушкой калибра 105 миллиметров. Всего планировали переделать таким образом 15 М6А1, однако, когда запрос о необходимости в данных машинах передали Эйзенхауэру – командующему союзными войсками в Европе – он резонно заметил, что на Европейском ТВД от 15 танков будет мало толку. Данный ответ стал причиной прекращения всех работ по машине. Правда, пара образцов, получивших обозначение М6А2Е1, использовали для испытания пушки калибра 105 миллиметров в новой башне предназначенной для тяжелого танка Т29. Все танки серии Т1Е1, М6 и М6А1 в декабре 44-го года было решено сдать на слом. Одну машину оставили в Абердине в коллекции танкового музея полигона.
Тактико-технические характеристики американского тяжелого танка М6:
Длина – 8,43 м;
Ширина – 3,12 м;
Высота – 3,00 м;
Масса – 57,4 т;
Двигатель – G-200;
Мощность двигателя – 960 л.с.;
Скорость – 35 км/ч;
Запас хода – 160 км;
Преодолеваемый ров – 3,35 м;
Броня лобового листа (угол наклона) – 83 (30) мм;
Броня борта – 70 мм;
Броня башни (маска орудия) – 83 (102) мм;
Броня крыши – 25 мм;
Броня днища – 25 мм;
Орудие – 2 Гочкис;
Калибр пушки – 70 мм;
Марка пулеметов – Браунинг;
Количество пулеметов – 5;
Калибр пулеметов – 7,62 мм;
Экипаж – 6 человек.
topwar.ru
Сталь Р6М5 — расшифровка марки стали, ГОСТ, характеристика материала
Марка стали — Р6М5
Стандарт — ГОСТ 19256
В марке стали Р6М5 первая буква Р означает, что сталь быстрорежущая. Следующая за буквой цифра 6 — указывает среднюю массовую долю вольфрама (6%), М5 — указывает содержание молибдена в стали примерно 5%. Сталь легированная, быстрорежущая.
Быстрорежущая сталь Р6М5 применяется для изготовления всех видов режущего инструмента при обработке углеродистых легированных конструкционных сталей, предпочтительно для изготовления резьбонарезного инструмента, а также инструмента, работающего с ударными нагрузками.
Массовая доля основных химических элементов, % | ||||||
---|---|---|---|---|---|---|
C — углерода | Si — кремния | Mn — марганца | Cr — хрома | W — вольфрама | Mo — молибдена | V — ванадия |
0,82-0,90 | 0,20-0,50 | 0,20-0,50 | 3,80-4,40 | 5,50-6,50 | 4,80-5,30 | 1,70-2,10 |
Температура критических точек, °С | |||
---|---|---|---|
Ac1 | Ac3 | Ar1 | Ar3 |
815 | 880 | 730 | 790 |
Технологические свойства | |
---|---|
Ковка | Температура ковки, °С: начала 1160, конца 850. Охлаждение замедленное в колодце. |
Свариваемость | Не применяется для сварных конструкций. |
Обрабатываемость резанием | В отожженном состоянии при HB 255: Kv твердый сплав = 0,8 Kv быстрорежущая сталь = 0,6 |
Флокеночувств. | Не чувствительна |
Шлифуемость | Хорошая |
tekhnar.ru
6М12П станок консольно-фрезерный вертикальный повышенной точностисхемы, описание, характеристики
Сведения о производителе консольно-фрезерного станка 6М12П
Производитель фрезерных станков 6М12П Горьковский завод фрезерных станков, ГЗФС, основанный в 1931 году.
История выпуска станков Горьковским заводом, ГЗФС
В 1937 году на Горьковском заводе фрезерных станков были изготовлены первые консольно-фрезерные станки серии 6Б моделей 6Б12 и 6Б82 с рабочим столом 320 х 1250 мм (2-го типоразмера).
В 1951 году запущена в производство серия 6Н консольно-фрезерных станков: 6Н12, 6Н13П, 6Н82, 6Н82Г. Станок 6Н13ПР получил “Гран-При” на всемирной выставке в Брюсселе в 1956 году.
В 1960 году запущена в производство серия 6М консольно-фрезерных станков: 6М12П, 6М13П, 6М82, 6М82Г, 6М83, 6М83Г, 6М82Ш.
В 1972 году запущена в производство серия 6Р консольно-фрезерных станков: 6Р12, 6Р12Б, 6Р13, 6Р13Б, 6Р13Ф3, 6Р82, 6Р82Г, 6Р82Ш, 6Р83, 6Р83Г, 6Р83Ш.
В 1975 году запущены в производство копировальные консольно-фрезерные станки: 6Р13К.
В 1978 году запущены в производство копировальные консольно-фрезерные станки 6Р12К-1, 6Р82К-1.
В 1985 году запущена в производство серия 6Т-1 консольно-фрезерных станков: 6Т12-1, 6Т13-1, 6Т82-1, 6Т83-1 и ГФ2171.
В 1991 году запущена в производство серия 6Т консольно-фрезерных станков: 6Т12, 6Т12Ф20, 6Т13, 6Т13Ф20, 6Т13Ф3, 6Т82, 6Т82Г, 6Т82ш, 6Т83, 6Т83Г, 6Т83Ш.
Классификация, обозначение и основные характеристики фрезерных станков
Классификация металлорежущих станков
Ремонт фрезерных станков
6М12П станок консольно-фрезерный вертикальный с поворотной шпиндельной головкой повышенной точности. Назначение, область применения
Консольно-фрезерные станки серии М выпускались Горьковским заводом фрезерных станков (ГЗФС) начиная с 1961 года. Станки сходны между собой по конструкции, широко унифицированы и является дальнейшим усовершенствованием аналогичных станков серии Н.
Особенности конструкции и принцип работы станка
Вертикальные консольно-фрезерные станки моделей 6М12П и 6М12БП представляют собой электрифицированные станки, обладающие высокой точностью и жесткостью.
Станки предназначены для фрезерования всевозможных деталей из стали, чугуна и цветных металлов торцевыми, цилиндрическими, концевыми, радиусными фрезами в условиях индивидуального и серийного производства. В серийном производстве, благодаря наличию полуавтоматических и автоматических циклов, станки могут успешно использоваться на работах операционного характера в поточных и автоматических линиях.
На станках можно обрабатывать вертикальные и горизонтальные плоскости, пазы, углы, нарезать зубчатые колеса и прочее.
Фрезерование зубчатых колес, разверток, спиралей, контура кулачков и прочих деталей, требующих периодического или непрерывного поворота вокруг своей оси, производятся на данных станках о применением делительной головки или накладного круглого стола.
Благодаря наличию механизма выборки люфта в винтовой паре продольной подачи стола, на станке можно производить встречное и попутное фрезерование, как в простых режимах, так и в режимах с автоматическими циклами.
Наиболее эффективное использование станка достигается при обработке деталей методом скоростного фрезерования.
Класс точности станков Н.
Российские и зарубежные аналоги станка 6М12П
FSS315, FSS350MR, (FSS450MR) — 315 х 1250 (400 х 1250) — производитель Гомельский станкостроительный завод
ВМ127М — (400 х 1600) — производитель Воткинский машиностроительный завод ГПО, ФГУП
6Д12, 6К12 — 320 х 1250 — производитель Дмитровский завод фрезерных станков ДЗФС
X5032, X5040 — 320 х 1320 — производитель Shandong Weida Heavy Industries, Китай
FV321M, (FV401) — 320 х 1350 (400 х 1600) — производитель Arsenal J.S.Co. — Kazanlak, Арсенал АД, Болгария
Габаритные размеры рабочего пространства, посадочные и присоединительные базы вертикального консольно-фрезерного станка 6М12П
Габаритные размеры рабочего пространства фрезерного станка 6М12П
Фото вертикального консольно-фрезерного станка 6М12П
Фото вертикального консольно-фрезерного станка 6М12П
Фото вертикального консольно-фрезерного станка 6М12П
Фото вертикального консольно-фрезерного станка 6М12П
Расположение органов управления консольно-фрезерным станком 6М12П
Расположение органов управления консольно-фрезерным станком 6М12П
Расположение органов управления консольно-фрезерным станком 6М12П
Расположение органов управления консольно-фрезерным станком 6М12П
Перечень составных частей консольно-фрезерного станка 6М12П
- Станина
- Поворотная головка
- Коробка скоростей
- Коробка подач
- Коробка переключения
- Консоль
- Стол и салазки
- Электрооборудование
Перечень органов управления консольно-фрезерным станком 6М12П
- Кран регулирования интенсивности охлаждения
- Маховичек ручного продольного перемещения стола
- Кулачки ограничения продольного хода стола в крайних положениях или реверса стола в полуавтоматическом и автоматическом циклах
- Кулачки переключения стола с подачи на быстрый ход или с быстрого хода на подачу
- Переключатель на автоматический цикл или ручное управление станка
- Кнопка «Пуск шпинделя»
- Кнопка «Стоп»
- Кнопка «Быстро»
- Рукоятка ручного насоса смазки стола
- Рукоятка включения вертикальной или поперечной подачи стола
- Рукоятка зажима консоли на направляющих станины
- Маховичек ручного поперечного перемещения стола
- Рукоятка зажима салазок на направляющих консоли
- Переключатель управления столом: автоматический цикл — ручное управление — работа с круглым столом
- Шестигранник поворота фрезерной головки
- Винты зажима стола на салазках
- Маховик перемещения гильзы шпинделя
- Переключатель освещения «Включено — выключено»
- Кнопка «Стоп шпиндель»
- Кнопка «Пуск шпинделя»
- Рукоятка и лимб для переключения скоростей шпинделя
- Кнопка «Импульс шпинделя»
- Кнопка «Быстро стол»
- Вводной переключатель «Включено — выключено»
- Переключатель насоса охлаждения «Включено — выключено»
- Переключатель направления вращения шпинделя «Влево — вправо»
- Рукоятка управления продольным перемещением стола
- Рукоятка подъема консоли
- Грибок и лимб для переключения подач стола
- Кулачки ограничения поперечного хода стола
- Рукоятка зажима гильзы шпинделя
- Кулачки ограничения вертикального хода стола
- Кнопка включения фиксации механизма переключения подач
- Гайки зажима поворотной фрезерной головки
Схема кинематическая консольно-фрезерного станка 6М12П
Кинематическая схема консольно-фрезерного станка 6М12П
Схема кинематическая консольно-фрезерного станка 6М12П. Смотреть в увеличенном масштабе
Цепь главного движения консольно-фрезерного станка 6М12П
Станок 6М12П имеет две раздельные кинематические цепи — цепь главного движения и цепь подач стола.
Шпиндель получает вращение от фланцевого электродвигателя мощностью 7 кВт, с 1440 об/мин через упругую соединительную муфту и зубчатые колеса механизма пятиваловой коробки скоростей, сообщающие шпинделю 18 различных чисел оборотов в пределах от 31,5 до 1600 об/мин.
Коробка скоростей и шпиндель консольно-фрезерного станка 6М12П
Коробка скоростей и шпиндель фрезерного станка 6М12П
Коробка скоростей фрезерного станка 6М12П
Коробка скоростей смонтирована непосредственно в верхней части корпуса станины и управляется с помощью вставной коробки переключения скоростей, расположенной с левой стороны станины. Для осмотра коробки скоростей достаточно снять крышку, находящуюся с правой стороны станины.
Шпиндель (вал VII) станка 6М12П (см. рис. 274, б) смонтирован в поворотной головке, которая центрируется в кольцевой выточке горловины станины и крепится к ней четырьмя болтами 1 (рис. 275). Поворотная головка может быть повернута на 45° от вертикальной оси в обе стороны
Выдвижение гильзы поворотной головки производят маховичком 2. Маховичок через коническую пару 7 (см. рис. 274, б) и винт с гайкой связан с кронштейном 5, закрепленным на гильзе. На валике маховичка 2 (рис. 275) закреплен лимб, цена деления которого 0,05 мм. За полный оборот маховичка гильза выдвигается на 4 мм.
В кронштейне 5 (рис. 274, б) предусмотрено отверстие и винт для закрепления индикатора, а к корпусу поворотной головки привинчен кронштейн 8 с регулируемым упором 6 для настройки перемещения гильзы.
Для увеличения жесткости шпинделя во время работы предусмотрен зажим рукояткой 4, которая стягивает корпус поворотной головки, имеющей разрез 5 (рис. 275).
Вращение шпинделю (валу VII) передается от коробки скоростей через коническую и цилиндрическую передачи (см. рис. 274, б). Цилиндрическое зубчатое колесо 2 закреплено на втулке, смонтированной на шарикоподшипниках и имеющей шпонку, которая входит в шпоночный паз шпинделя.
Вал VI станка 6М12П смонтирован на одном радиальном и двух радиально-упорных шарикоподшипниках. Радиально-упорные шарикоподшипники расположены во фланце и стянуты шайбой, которая крепит фланец к поперечной стенке станины. Зазор в радиально-упорных подшипниках регулируется подшлифовкой промежуточных колец. Сцепление конического зубчатого колеса регулируется путем осевого перемещения всего вала VI винтами, ввернутыми во фланец (рис. 274, б).
Вал V смонтирован также на одном радиальном и двух радиально-упорных шарикоподшипниках. Регулирование зазора производится подтягиванием гайки с левого торца вала V.
Вал IV коробки скоростей у всех трех станков этой гаммы, т. е. 6М82, 6М82Г и 6М12П (рис. 274, а и б), для большей жесткости расположен на трех опорах.
Валы II, III и IV — шлицевые для возможности передвижения зубчатых блоков.
Как указывалось ранее, в коробках скоростей этих станков механизм переключения скоростей является самостоятельным узлом (рис. 276). На корпусе механизма переключения скоростей расположен лимб 1 из пластмассы, на котором нанесены значения всех 18 чисел оборотов шпинделя, стрелка указатель и кнопочная станция 2 с переключателем освещения и кнопками: «пуск шпинделя», «стоп шпинделя», «толчок шпинделя», «быстро стол». С нижней стороны коробки переключения находится рукоятка 3.
Скорости переключаются следующим образом:
- рукоятку 3 опускают вниз, при этом ее шип выводится из фиксирующего паза, и отводят на себя до отказа;
- поворачивают лимб 1 вправо или влево до совпадения выбранного числа оборотов шпинделя со стрелкой-указателем; при этом щелчок фиксатора указывает, что лимб установлен в заданном положении;
- нажимают кнопку «толчок», что дает кратковременный импульс на электродвигатель привода шпинделя для провертывания зубчатых колес коробки скоростей, во избежание того, чтобы торцы зубьев блоков колес не уперлись друг в друга при переключении скоростей;
- досылают плавным движением рукоятку 3 в первоначальное положение, при этом она обязательно должна быть заперта шипом в фиксирующем пазу.
- При этих операциях с рукояткой и лимбом блоки зубчатых колес коробки скоростей перемещаются и устанавливаются в положениях, соответствующих выбранному числу оборотов шпинделя.
Механизм подач консольно-фрезерного станка 6М12П
Механизм подач фрезерного станка 6М12П
Привод подач осуществляется от отдельного фланцевого электродвигателя мощностью 1,7 кВт при 1420 об/мин, смонтированного в консоли. Через коробку подач ходовым винтам продольного и поперечного перемещений стола сообщаются 18 различных подач в пределах от 25 до 1250 мм/мин, а винту вертикального перемещения стола — 18 различных подач в пределах от 8,3 до 416,6 мм/мин.
Вал I коробки подач (см. рис. 272) приводится во вращение непосредственно электродвигателем; от него вращение передается валу II зубчатой парой 26 : 50, валу III — зубчатой парой 26 : 57, валу IV — зубчатыми парами 18 : 36, или 27 : 27, или 36 : 18, валу V — зубчатыми парами 18 : 40, или 21 : 37, или 24 : 34 и далее валу VI через перебор 13 : 45 — 18 : 40 или непосредственной зубчатой передачей 40 : 40.
Консоль фрезерного станка 6М12П
В консоли расположены все узлы цепи подач. На рис. 284 схематически показана консоль фрезерных станков 2-й гаммы с механизмами передачи движения от электродвигателя к столу, салазкам и самой консоли.
Консоль имеет чугунный корпус с развитыми направляющими профиля «ласточкин хвост» под станину и перпендикулярные к ним прямоугольные направляющие под салазки. Консоль несет на себе следующие органы управления:
Схема электрическая принципиальная фрезерного станка 6М12П
Электрическая схема принципиальная фрезерного станка 6М12П
Схема электрическая принципиальная консольно-фрезерного станка 6М12П. Смотреть в увеличенном масштабе
Описание электрооборудования станка 6М12П
Электрооборудование станка предназначено для питания от сети трехфазного тока напряжением 380 В с частотой 50 Гц. По особому заказу оно может быть выполнено и на другие стандартные напряжения: 220 В или 500 В, а также на частоту сети 60 Гц.
В электрической схеме станка (рис. 50) предусмотрены: питание цепи управления от сети напряжением 127 в, питание цепи местного освещения от сети напряжением 36 В, нулевая защита всех электродвигателей, а также защита от коротких замыканий плавкими предохранителями и от перегрузок при помощи тепловых реле.
Вся пусковая электроаппаратура установлена в двух нишах станины станка.
В каждой нише имеется по две панели с электроаппаратурой; четыре панели составляют комплект панелей управления станка, имеющий общую монтажную схему (рис. 51).
Для подключения электрооборудования к сети и его отключения имеется вводный выключатель, рукоятка которого расположена на дверке левой ниши.
Управление электродвигателем шпинделя — кнопочное. Выбор направления вращения шпинделя производится реверсивным переключателем ПР, который устанавливает нужное вращение двигателя шпинделя.
Управление электродвигателем подачи производится от двух командоаппаратов.
Командоаппарат продольной подачи 1КА состоит из двух конечных выключателей: для включения правого и левого ходов стола.
Командоаппарат поперечной и вертикальной подач 2КА также состоит из двух конечных выключателей. Рукоятка командоаппарата 2КА имеет пять положений: назад, вниз, вперед, вверх и среднее нейтральное.
Для выполнения на станке разных режимов работы в электросхеме имеется переключатель ПУ на три положения рукоятки. При первом положении — «Автоматический цикл» — выполняются только автоматические циклы продольного хода стола, при втором положении — «Подача от рукояток» — производится нормальная работа станка и при третьем положении — «Круглый стол» — производится работа круглым столом, который как приспособление может быть установлен на столе станка.
Управление вращением круглого стола происходит при одностороннем вращении двигателя подачи.
Электронасос для охлаждающей жидкости управляется от выключателя ВО.
Выключатель ВМО служит для отключения местного освещения станка.
Специальный электромагнит ЭБ постоянного тока (рис. 52) служит для привода фрикционной муфты быстрого хода.
Одновременно с включением быстрого хода электромагнит отключает кулачковую муфту подачи.
Питание электромагнита ЭБ выполняется от селенового выпрямителя ВС, основное назначение которого — давать подмагничивающий ток двигателю шпинделя при торможении.
Вводный выключатель ВВ и реверсивный переключатель ПР предназначены для отключения ненагруженных цепей, поэтому при пользовании этими аппаратами электродвигатель шпинделя необходимо предварительно отключить кнопкой «Стоп».
Работа электросхемы при ручном управлении
Переключатель управления ПУ должен быть установлен в положении «Подача от рукояток».
После выбора направления вращения шпинделя переключателем ПР рукоятку вводного выключателя ВВ необходимо установить в положение «Включено». При этом будет подано напряжение сети на, клеммы магнитного пускателя ПШ.
От нажатия кнопки «Шпиндель» магнитный пускатель ПШ включается, и двигатель шпинделя будет вращаться.
При включенном пускателе ПШ рукояткой командоаппарата 1КА (или 2КА) можно включить движение стола со скоростью рабочей подачи. Для получения движения стола вправо (или назад, вниз) включается пускатель ПП, при левом ходе (или ходах вперед, вверх) работает пускатель ПЛ двигателя подачи.
Движение стола со скоростью быстрого хода происходит только при нажатой кнопке «Быстро», которая включает пускатель ПБ электромагнита быстрого хода.
Быстрым ходом стола можно пользоваться как при включенном, так и при отключенном двигателях шпинделя. При отключенном шпинделе быстрый ход осуществляется благодаря шунтированию контакта ПШ 12-28 контактом ПБ при нажатии кнопки «Быстро».
Автоматический останов двигателя подачи при движении стола (консоли или салазок) происходит при переводе концевым кулачком рукоятки командоаппарата 1КА (или 2КА) в нейтральное положение, при этом разрывается цепь питания пускателя ПП (или ПЛ), и двигатель останавливается.
Работа электросхемы при автоматическом управлении
Автоматическое управление применяется только для продольного хода стола.
На станке можно выполнять следующие автоматические циклы:
- правый скачкообразный с реверсом
- левый скачкообразный с реверсом
- маятниковый
При маятниковом цикле рабочая подача стола автоматически чередуется с быстрым ходом в каждом направлении.
Для работы на автоматическом цикле переключатель ПУ должен быть установлен в положение «Автоматический цикл».
Кроме того, необходимо также сделать механическое переключение валика, имеющегося в салазках станка, из положения «Ручное управление» в положение «Автоматический цикл». При последнем положении валика кулачковая муфта продольного хода заперта, и конечный выключатель 4КА нажат. Это обеспечивает управление продольным движением стола только от командоаппаратов 1КА и ЗКА при сблокированных поперечной и вертикальной подачах.
Для объяснения работы схемы в автоматическом цикле разберем выполнение правого скачкообразного цикла с реверсом. Этот цикл состоит из автоматических переключений:
- с быстрого хода вправо на подачу вправо
- с подачи вправо на быстрый ход влево
- с быстрого хода влево на «Стоп»
Для получения быстрого хода стола в начале цикла нужно предварительно убедиться в том, что командоаппарат ЗКА, управляющий работой пускателя ПБ при автоматических циклах, находится в не нажатом состоянии, т. е. через его контакт 43-26 происходит питание пускателя ПБ.
Если контакт ЗКА 43-26 не закрыт, то необходимо сделать поворот звездочки с восемью выступами, сидящей на валу рукоятки командоаппарата 1КА на один выступ, после чего контакт ЗКА 43-26 закроется.
При повороте рукоятки командоаппарата 1КА вправо включится быстрый ход стола вправо, так как произойдет включение пускателей /7/7 для двигателя подачи и ПБ для электромагнита.
Отключение быстрого хода происходит, когда в нужной точке пути стола откидной кулачок сделает поворот звездочки на один выступ, при этом контакт 43-26 командоаппарата ЗКА раскроется, электромагнит ЭБ будет отключен, и стол продолжит движение со скоростью рабочей подачи.
Для переключения движения в нужной точке пути с рабочей подачи вправо на быстрый ход влево в пазу стола должны быть установлены рядом два кулачка:
- кулачок № 1 для перевода рукоятки командоаппарата из положения вправо в положение влево
- кулачок № 3 (откидной) для отключения подачи вправо и включения быстрого хода
Когда кулачок № 1 переводит рукоятку командоаппарата 1КА в положение влево, то перед моментом раскрытия контакта 15-16 от нажатия кулачка № 3 на звездочку с выступами в командоаппарате ЗКА контакт 43-26 уже закрывается, что обеспечивает питание пускателя ПП по цепи 15-42-43-25-16 при раскрытом контакте 15-16 командоаппарата 1КА (см. в схеме диаграмму переключателя ЗКА).
После перевода рукоятки в положение влево кулачок 3 повернет звездочку на один выступ и в командоаппарате ЗКА раскроется контакт 43-26, отключая пускатель ПП — подача вправо. Закрытие нормально закрытого контакта пускателя ПП 22-18 замыкает цепь питания пускателя ПЛ, и двигатель реверсируется. Одновременно контакт ЗКА 43-26 включает пускатель ПБ, и стол идет быстро влево.
Остановка быстрого хода влево происходит при переводе кулачком № 2 рукоятки командоаппарата 1КА в нейтральное положение, в котором отключаются двигатель подачи и электромагнит ЭБ.
Наладку на автоматические циклы следует производить без обрабатываемой детали, так как ошибки при наладке могут привести к включению быстрого хода вместо подачи, что может вызвать поломку инструмента.
Работа схемы при остальных автоматических циклах аналогична вышеописанной.
Импульсное включение двигателей
Для получения быстрого сцепления зубьев зубчатых колес при переключениях скоростей шпинделя предусмотрен кратковременный поворот двигателя шпинделя.
Для указанной цели имеется кнопка «Толчок», при нажатии которой двигатель шпинделя получает кратковременное вращение. Кратковременность включения пускателя ПШ происходит благодаря тому, что при его включении получает питание реле РП, которое, становясь на самопитание, разрывает своим контактом 33-27 цепь питания пускателя ПШ.
При переключениях подачи также имеется возможность кратковременного включения двигателя подачи с помощью конечного выключателя KB, который включает двигатель в то время, когда ручка переключения находится в выдвинутом положении.
Торможение шпинделя
Электропривод шпинделя имеет динамическое торможение двигателя, которое благодаря плавно нарастающему тормозному моменту лучше обеспечивает сохранность механизма при эксплуатации, чем другие способы торможения.
Для выполнения динамического торможения установлено следующее электрооборудование:
- Селеновый выпрямитель ВС, соединенный со специальной обмоткой трансформатора ТУ. Эта обмотка имеет напряжение 55 В при напряжении сети 380 В и 36 В при 220 В.
- Магнитный пускатель ПТ для включения постоянного тока в обмотку статора двигателя на время торможения.
- Промежуточное реле РН, имеющее катушку для напряжения сети трехфазного тока.
При нажатии кнопки «Стоп» ее нормально закрытый контакт отключает пускатель ПШ, и статор двигателя от сети отключается. В отключенной обмотке статора затухающее поле ротора наводит напряжение, приблизительно равное напряжению сети.
Во избежание пробоя селенового выпрямителя последний включается в цепь статора только после снижения наведенного напряжения до малой величины. Контроль исчезновения наведенного напряжения выполняет реле напряжения РН.
Когда реле РН обесточивается, оно своим нормально закрытым контактом 23-41 замыкает цепь питания пускателя ПТ, который подает в обмотку статора постоянный подмагничивающий ток, чем обеспечивается торможение двигателя.
После остановки шпинделя кнопку «Стоп» отпускают, при этом пускатель ПТ отключает селеновый выпрямитель от статора.
Процесс торможения двигателя длится при наибольшей включенной скорости шпинделя 1600 об/мин 3—5 сек.
Блокировки станка
Электросхема имеет ряд блокировок, которые введены для обеспечения правильной эксплуатации станка и его электрооборудования:
- Одновременное включение рукояток командоаппаратов 1KA и 2КА вызывает остановку двигателя подачи, так как совместная работа двух подач не допускается кинематикой станка
- В положении переключателя ПУ «Автоматический цикл» исключены работа поперечной и вертикальной подач и управление от кнопки «Быстро»
- В положении переключателя ПУ «Круглый стол» работа продольной, поперечной и вертикальной подач невозможна
- В положении переключателя ПУ «Подача от рукояток» нормально замкнутые контакты в реверсивном пускателе двигателя подачи зашунтированы для получения принудительного реверсирования двигателя подачи в случае «прилипания» якоря к неподвижному сердечнику магнита в пускателе
- Не допускается рабочая подача во всех направлениях, а также вращение круглого стола при не включенном двигателе шпинделя.
Установочный чертеж фрезерного станка 6М12П
Установочный чертеж фрезерного станка 6М12П
6М12П станок консольно-фрезерный вертикальный с поворотной головкой. Видеоролик.
Технические характеристики консольного фрезерного станка 6М12П
Наименование параметра | 6М12П | 6Р12 | 6Т12 |
---|---|---|---|
Основные параметры станка | |||
Размеры поверхности стола, мм | 1250 х 320 | 1250 х 320 | 1250 х 320 |
Наибольшая масса обрабатываемой детали, кг | 250 | 250 | 400 |
Расстояние от торца шпинделя до стола, мм | 30..400 | 30..450 | 30..450 |
Расстояние от оси шпинделя до вертикальных направляющих станины (вылет), мм | 350 | 350 | 380 |
Рабочий стол | |||
Наибольший продольный ход стола (X), мм | 700 | 800 | 800 |
Наибольший поперечный ход стола механический/ ручной (Y), мм | 240/ 260 | 250 | 320 |
Наибольший вертикальный ход стола (Z), мм | 370 | 420 | 420 |
Пределы продольных и поперечных подач стола (X, Y), мм/мин | 25..1250 | 12,5..1600 | 12,5..1600 |
Пределы вертикальных подач стола (Z), мм/мин | 8,3..416,6 | 4,1..530 | 4,1..530 |
Количество подач продольных/ поперечных/ вертикальных | 18 | 22 | 22 |
Скорость быстрых перемещений продольных (X), поперечных (Y), м/мин | 3 | 4 | 4 |
Скорость быстрых перемещений вертикальных (Z), м/мин | 1 | 1,330 | 1,330 |
Шпиндель | |||
Мощность привода главного движения, кВт | 7,5 | 7,5 | 7,5 |
Частота вращения шпинделя, об/мин | 31,5..1600 | 40..2000 | 31,5..1600 |
Количество скоростей шпинделя | 18 | 18 | 18 |
Перемещение пиноли шпинделя, мм | 70 | 70 | |
Конус фрезерного шпинделя по ГОСТ 836-62 | № 3 | № 3 | |
Конец шпинделя ГОСТ 24644-81, ряд 4, исполнение 6 | 50 | ||
Отверстие фрезерного шпинделя, мм | 29 | 29 | |
Поворот шпиндельной головки вправо и влево, град | ±45 | ±45 | ±45 |
Механика станка | |||
Выключающие упоры подачи (продольной, поперечной, вертикальной) | Есть | Есть | Есть |
Блокировка ручной и механической подач (продольной, поперечной, вертикальной) | Есть | Есть | Есть |
Блокировка раздельного включения подач | Есть | Есть | Есть |
Торможение шпинделя | Есть | Есть | Есть |
Предохранительная муфта от перегрузок | Есть | Есть | Есть |
Автоматическая прерывистая подача | Есть | Есть | Есть |
Электрооборудование, привод | |||
Количество электродвигателей на станке | 3 | 3 | 4 |
Электродвигатель привода главного движения, кВт | 7,5 | 7,5 | 7,5 |
Электродвигатель привода подач, кВт | 2,2 | 2,2 | 3 |
Электродвигатель зажима инструмента, кВт | — | — | 0,25 |
Электродвигатель насоса охлаждающей жидкости, кВт | 0,125 | 0,12 | 0,12 |
Суммарная мощность всех электродвигателей, кВт | 9,825 | 9,825 | 10,87 |
Габарит и масса станка | |||
Габариты станка (длина ширина высота), мм | 2395 х 1745 х 2000 | 2305 х 1950 х 2020 | 2280 х 1965 х 2265 |
Масса станка, кг | 3000 | 3120 | 3250 |
Связанные ссылки
Паспорта и схемы к консольно фрезерным станкам и оборудованию
Каталог справочник консольно фрезерных станков и их аналогов
Справочник деревообрабатывающих станков
Справочник КПО
Прайс-лист информационных изданий
stanki-katalog.ru