Секреты булата. Загадка булатного узора
Секреты булата
После того как разработана технология получения булатных слитков, показаны приемы получения рисунков различных сортов узорчатой стали и оценены ее свойства, представляет интерес еще раз проанализировать данные, которые накопила история и наука о производстве этой замечательной стали, ее термической обработке и отделке.
Наши разработки теории и производства булата убедительно показали, что булатный узор и необыкновенные свойства этой стали являются следствием не только макро-, но и микронеоднородности металла. Если макронеоднородность зависит от физической неоднородности, обусловленной сохранением в объеме жидкой стальной ванны недорасплавленных частиц с небольшим содержанием углерода, то микронеоднородность возникает вследствие диффузии углерода из слоя в слой при нагревах изделий и тщательного «перемешивания» слоев металла во время пластической деформации.
Таким образом, с одной стороны, правильна расшифровка работ П. П. Аносова профессором А. П. Виноградовым; с другой — Д. К. Чернов, Н. И. Беляев и их последователи совершенно верно указывали на необычную микронеоднородность булата. В связи с этим экспериментально полученные А. П. Виноградовым узоры на образцах низкоуглеродистой стали являются только имитацией булата, поскольку в микроструктуре такой стали не наблюдаются выделения цементита (карбидов).
Очевидно, и наши разработки не могут претендовать на полное воспроизведение свойств булата, качество которого, как уже неоднократно указывалось, зависело от многих факторов: чистоты и состава исходных материалов, способов деформации и термической обработки, отделки, шлифовки и полировки готовых изделий.
В наше время хорошо известно: чистота и свойства железа и стали зависят не только от содержания в них таких вредных примесей, как кислород, сера и фосфор, но и от загрязненности металла неметаллическими включениями, представляющими собой главным образом мельчайшие частицы оксидов тугоплавких элементов. Применяемое нами мягкое железо, например, было получено путем окисления в жидкой стали ненужных примесей и перевода их в шлаковую фазу. Поэтому наше «чистое» по кремнию и марганцу железо обязательно содержало включения оксидов этих элементов.
В древние времена железо получали путем восстановления чистых по сере и фосфору руд древесным углем при температурах 800–1200 °C. При этих температурах кремний, марганец и многие другие элементы не восстанавливались, а их твердые оксиды растворялись в жидком шлаке. Железо в крице, очищенной от шлака, практически не содержало включений оксидов тугоплавких элементов. Таким образом, сыродутный и кричный процессы получения железа обеспечивали высокую чистоту металла не только по сере, фосфору и другим примесям, но и по неметаллическим включениям. Такое железо и приготовленные на его основе сталь и чугун могли обладать необыкновенной пластичностью и высокими механическими свойствами.
Есть еще одна возможная причина высокой пластичности и вязкости булатной стали. Недавно советским металлургом С. М. Барановым зарегистрировано открытие, связанное с «явлениями изменения структуры к свойств стали, обусловленных присутствием моноокиси кремния». Оказывается, наличие окиси кремния в сталях сильно снижает их пластичность и вязкость при низких температурах. Поэтому на заводе им. И. А. Лихачева, например, кузова автомобилей, предназначенных для северных районов, изготовляли из углеродистых сталей, отлитых методом бескремнистого раскисления. Эти стали обладают также повышенной коррозионной стойкостью в атмосферных условиях. С. М. Баранов считает, что при сыродутном способе получения железа и стали условий для образования моноокиси кремния не существовало, и поэтому булатные стали хорошо ковались при низких температурах, были прочными и пластичными.
Действительно, в большей части клинков из булата обнаружено очень мало кремния, а содержание фосфора высокое (0,8–0,25 %). Мы уже отмечали благоприятное действие фосфора на коррозионную стойкость стали в атмосферных условиях. С другой стороны, фосфор усиливает междендритную ликвацию углерода при кристаллизации стали и делает феррит более устойчивым. В связи с тем что растворимость фосфора в аустените — гораздо меньше, чем в феррите, при охлаждении стали ниже 1400 °C из пересыщенного фосфором аустенита выделяются не фосфиды, а возникают ферритные участки с более высоким содержанием этого элемента. Такие участки устойчивы при дальнейшем охлаждении стадии они становятся зародышами при образовании феррита при низких температурах. Последнее приводит к тому, что в микроструктуре стали появляется неоднородность в виде светлых полосок или пятен. Такая неоднородность была выявлена нами в прокатанной на лист низкоуглеродистой стали, содержащей 0,11 % фосфора. Таким образом, фосфор мог усиливать микронеоднородность булата.
Если тайны булатных узоров и природы структурной неоднородности булата больше не существует, то в технологии приготовления булатных изделий — их ковке, термообработке и отделке — есть еще много белых пятен.
Многие булаты по содержанию углерода ближе к чугуну, чем к стали, поэтому булат — сталь сверхуглеродистая. Длительное время считали, что ковать чугун и сверхуглеродистые стали нельзя, они хрупкие и рассыпаются под ударами молота. Между тем булат надо было не просто проковать, а проковать так, чтобы сталь приобрела мелкозернистую структуру.
Совершенно прав металлург А. Герчиков, который замечает, что острота и стойкость острия зависят от того, насколько мелки зерна основной твердой фазы стали. Современную сталь для режущего инструмента подвергают специальной ковке, чтобы измельчить зерно. У булата же зерно должно было быть чрезвычайно мелким. Правда, зерно булатной стали мелкое уже в слитке, поскольку твердые частицы включений обеспечивали объемную кристаллизацию жидкой стали и затрудняла рост дендритов. При ковке слитка зерно еще более измельчалось. Теперь мы знаем, что одна из причин мелкозернистости и высокой пластичности сплавов железа с высоким содержанием углерода — их особая чистота. А если ее нет?
В последнее время появились работы, показывающие, что при определенных температурах деформации сверхуглеродистая сталь, содержащая 1,2–2,0 % углерода, может обладать высокой пластичностью и по другим причинам. Главным условием высокой пластичности и даже сверхпластичности является не только дисперсность зерен, но и постоянство их размеров при температуре деформации. Последнее обеспечивается, если в стали образуются очень тонкие частицы цементита (карбидов железа).
Подготовка стали к сверхпластичному состоянию осуществляется сравнительно недавно вновь открытыми методами термомеханической обработки. Сталь нагревают немного выше температуры перлито-аустенитного превращения и выдерживают необходимое время для растворения всех карбидов в аустените. Затем ее непрерывно деформируют, одновременно охлаждая. Это приводит к сильному измельчению аустенита, образованию субзерен и созданию значительного количества рассеянных дислокации. Выпадающие из аустенита по мере его охлаждения тонкие частицы карбидов (цементита) оседают на дислокациях и субзернах.
При температуре 727 °C (см. рис. 2) аустенит начинает превращаться в феррито-цементитную смесь. Дальнейшая непрерывная деформация приводит к образованию сверхтонких зерен феррита с однородным распределением субмикронных частиц цементита. Именно такой материал и обладает сверхпластичностью при 600–650 °C. Так, например, сталь, содержащая 1,6 % углерода, при этих температурах удлиняется перед разрушением более чем на 1000 %. После охлаждения до комнатных температур эта сталь обладала примерно в 2 раза большей прочностью, чем малолегированные инструментальные стали, и не уступала им в пластичности!
Еще выше поднимаются свойства стали после закалки. Мартенсит сверхуглеродистой стали имеет твердость и прочность на излом при сжатии, соизмеримые с карбидом вольфрама — одного из самых прочных и твердых после алмаза материалов. Но карбид вольфрама имеет нулевую пластичность при сжатии, и поэтому разрушается хрупко, в то время как сталь до излома пластически деформируется почти на 10 % и разрушается вязко. Таким образом, высокоуглеродистые заэвтектоидные стали при должной термомеханической обработке могут обладать высокой твердостью, прочностью и достаточно большой вязкостью. Мы уже знаем, что эти качества позволяют затачивать лезвие клинка до необыкновенной остроты.
Высокодисперсные зерна феррита, полученные в результате термомеханической обработки высокоуглеродистых заэвтектоидных сталей, обладают необыкновенно высокой подвижностью атомов на своих границах. При 650–800 °C диффузия атомов железа на поверхность зерна проходит в миллион раз быстрее, чем в его основу. Такие свойства стали должны хорошо обеспечивать ее сварку в процессе ковки. О. Д. Щерби экспериментально показал возможность сравнительно быстрой диффузионной сварки высокоуглеродистой заэвтектоидной стали с мягким железом и низкоуглеродистыми сталями при 800 °C. Им получен слоистый материал, аналогичный сварочному булату (дамасская сталь).
Знаменательно, что не так давно советские ученые А. Бочвар, В. Давыдов и Л. Лушников показали: при определенных условиях обычный чугун также становится сверхпластичным. Оказывается, при определенной температуре и достаточно быстрой деформации опасные изломы и трещины в чугуне не образуются. Зарождавшиеся очаги разрушения быстро «затягиваются». Механизм «затягивания» микротрещин связывают с большой скоростью диффузии, которая достигается лишь тогда, когда зерна металла очень мелкие и имеют круглую форму. Эксперименты с мелкозернистым белым чугуном, содержащим углерода 3,5 %, свидетельствуют, что при 70 °C удлинение образцом достигало 150 %!
Использовали ли древние кузнецы термомеханическую обработку стали для получения ее высоких свойств? Установленные факты позволяют положительно ответить на этот вопрос. Известно, что дамасские оружейники построили между двумя высокими горами мастерскую и вывешивали на сильном ветре раскаленные докрасна после ковки клинки. Подобным образом закаливали сталь и в древней Грузии. Только что откованый горячий клинок кузнец передавал подручному, и тот, мчась верхом на разгоряченном коне, размахивал ям над головой. Эти способы закалки булата непосредственно после ковки в потоке ветра кажутся сегодня романтичными; между тем они как раз и являются своеобразными приемами термомеханической обработки стали.
Совмещение ковки, закалки и отпуска — закономерный прием в технологии производства изделий с мелкозернистой структурой, высокой твердостью и упругостью. Для получения высокой твердости стали ее отпуск после закалки должен быть как можно более низким — при температуре 150 °C. При таком отпуске нельзя получить высокой упругости. Отпуск же при 300 °C обеспечивает высокую упругость, но при этом резко снижается вязкость стали вследствие развития необратимой хрупкости. Более высокая температура отпуска стали повышает вязкость, но снижает упругость.
Благоприятное сочетание всех этих свойств — твердости, упругости и вязкости — может быть получено при определенном температуре отпуска, только после термомеханической обработки, подавляющей хрупкость. Поэтому клинок, закаленный после ковочного нагрева, непосредственно после ковки должен обладать максимально благоприятным сочетанием всех указанных свойств. Похоже на то, что в древности это знали…
Кузнецу мало было владеть достаточно сложными приемами ковки булата, он должен уметь нагреть сталь до строго определенной, оптимальной температуры и прекратить деформацию металла в нужный момент. Как читатель уже убедился, отклонения от заданной температуры отрицательно сказывались на строении стали и могли значительно ухудшить свойства клинка.
Древние кузнецы, конечно, не могли измерять температуру металла, они судили о ней по цветам каления и побежалости на его поверхности при нагреве. Острые глаза кузнецов различали целую гамму цветов нагретой стали. Вот она. Бело-матовый — 1250 °C, светло-желтый — 1200, желтый — 1100, светло-красный — 950, красный — 850, светло-вишневый — 800, вишнево-красный — 750, темно-вишнево-красный — 650, темно-красный — 600, слабосветящийся — 550, серый — 330, светло-синий — 320, темно-синий — 300, фиолетовый — 285, коричнево-красный — 265, темно-желтый — 220 °C.
Древние манускрипты повествуют, что в давние времена мастера перед ковкой и закалкой булата плотно завешивали окна и работали в полной темноте. Как теперь ясно, это отнюдь не таинственный обряд. В темноте натренированному глазу легче проследить гамму цветов раскаленного металла. И все-таки надо иметь большой навык, чтобы не ошибиться во всех этих цветах и оттенках; да и не каждому дано такое зрение. Поэтому мастера постоянно искали более совершенные и простые способы определения температуры.
Особенно точно надо было определять температуру при закалке и отпуске изделий. Изменение температуры нагрева под закалку на 10–20 °C может заметно изменить свойства стали. Еще более важно точно зафиксировать температуру при отпуске. Даже несколько градусов отклонения от необходимой температуры отпуска для стали данного состава приводит к значительному ухудшению ее упругости.
Случай, о котором я сейчас расскажу, произошел не так давно. Приближалось начало осенней охоты, и охотники приводили в порядок свои ружья. Особенно важно восстановить упругость пружины бойка. Для этого пружину следует закалить и, главное, правильно отпустить. Делать это лучше всех умел один старый мастер. И делал, но с одним условием: никто не должен наблюдать за его работой. Заперся как-то этот мастер в термичке после конца рабочей смены, принялся за работу. Но какой-то парень все-таки подсмотрел его секреты. Увидеть увидел, а понять ничего не смог. Нагрел мастер пружину в печи и начал к ней прикладывать какие-то палочки: то одну приложит, то другую. Прикладывал, прикладывал и вдруг резко бросил пружину в воду. После этих манипуляций пружина стала необыкновенно упругой. Не знал этот парень, что «волшебник» пользовался старинным способом определения температуры стали при отпуске по воспламенению различных сортов дерева…
А способ этот применяется в металлургии и поныне. Американский инженер Р. Акофф рассказывает, что совсем недавно, когда на одном из металлургических заводов начали устанавливать термопару для определения температуры футеровки электропечи, старый сталевар спросил: «А зачем вы это делаете, можно же гораздо проще!» Он разжевал табак, плюнул в печь и по времени его воспламенения достаточно точно определил температуру футеровки.
Закалку стали применяли с незапамятных времен. Ее знали мастера Древнего Египта за несколько веков до нашей эры. Знаменитые Лейденские папирусы, найденные в Фивских гробницах, содержат описание способов получения и закалки металлов, относящихся к III веку. Лезвия древнеримских мечей из сварочного булата были закалены на мартенсит. На некоторых клинках мартенситная структура чередовалась с трооститом, причем в отдельных местах выступал феррит. Последнее свидетельствует о небольшом, менее 0,8 %, содержании углерода в сварочном булате. Интересно также, что в средней части клинков закалки не обнаружено.
Мартенсит в структуре лезвий очень древних мечей находят не часто, поэтому вещественных доказательств применения в глубокой древности термообработки не так уж много. Это объясняется тем, что, с одной стороны, большинство найденного холодного оружия подвергалось действию огня, а с другой — за многие сотни лет мартенситная структура стали, полученная закалкой, могла превратиться в перлитные структуры отпуска.
Широко применяли термическую обработку стали в Киевской Руси. Из исследованных Б. А. Колчиным более 200 цельностальных или со стальными лезвиями древнерусских клинков и наконечников стрел термическую обработку сохранило более 90 % изделий.
Древние кузнецы эмпирически владели почти всеми тонкостями технологии закалки и отпуска стали. Они знали, что чем быстрее охладить сталь после нагрева под закалку, тем она тверже и износоустойчивей. В. Шекспир так описывает меч Отелло:
Был в комнате другой в запасе меч,
Он закален в ручье, как лед, холодном.
Температура воды и растворимые в ней соли оказывают большое влияние на скорость охлаждения. Поэтому в древности пользовались для закалки родниковой водой, водой из минеральных источников, росой и так далее. Температуру воды и место ее отбора держали в строгом секрете. Сохранилась легенда о том, как один подмастерье захотел узнать, при каком жаре идет закалка. Когда мастер опустил в воду раскаленный клинок, тот сунул в сосуд палец. Рука подмастерья, проявившего излишнее любопытство, была отрублена ретивым мастером.
О том, какое значение имела температура воды и растворимые в ней соли, свидетельствует случай, который произошел уже в наши дни. На заводе вдруг пошел повальный брак по механическим свойствам деталей после термообработки. Причину установили не сразу; оказалось, что кто-то в закалочной воде помыл руки с мылом…
В древности искали и умели находить среды, в которых сталь охлаждается быстрее, чем в простой воде. Вот как Теофил описывает закалку стали, которая режет «стекло и мягкие камни»: «Берут трехлетнего барана, привязывают его и в течение трех дней его не кормят. На четвертый день его кормят только папоротником. Спустя два дня такой кормежки его ставят на следующую ночь в бочонок с пробитыми снизу дырами. Под эти дыры ставят сосуд, в который собирается моча барана. Собранная таким образом за две-три ночи в достаточном количестве моча барана изымается, и в указанной моче закаливают инструмент».
Когда кузнецы научились получать стали с большим содержанием углерода, они обнаружили, что клинки, закаленные в холодной воде, легко ломаются от удара. Поэтому в Персии, например, начали закаливать холодное оружие в мокром холсте. Известен также метод закалки, при котором клинок до термической обработки обмазывался для тепловой изоляции толстым слоем особой глины с разными примесями. Состав удалялся только с лезвия, подлежащего закалке в воде. Образовавшейся при этом демаркационной линии в каждой мастерской придавали своеобразный оригинальный рисунок, по которому можно отличить мастера, изготовившего холодное оружие.
Древние кузнецы знали и способы предохранения металла от окисления в период нагрева под закалку. Кузнец брал бычьи рога, сжигал их на огне, в полученный пепел примешивал соли и посыпал этой смесью изделия, шепча заклинание. После этого изделия нагревались и закаливались в воде или сале. Если не говорить о заклинании, то все это, как ясно теперь, являлось необходимым условием безокислительного нагрева стали.
Чтобы обеспечить необходимые свойства лезвию и обуху, закаленные клинки нужно было уметь отпускать при разных температурах. Делалось это путем нагрева клинка над раскаленными углями. Так при отпуске сабельного клинка различные его части отпускались следующим образом: у ручки клинок нагревали до зеленого цвета, у конца — до синего, в середине — до фиолетового, а лезвие — до желтого.
Применялась в древности и химико-термическая обработка стали. Цементацию стали делали так. Изделия смазывали свиным салом, обматывали ремешками, нарезанными из козлиной кожи, обвязывали льняными нитками, покрывали слоем влажной глины, сушили и помещали в горн. Поверхность стали науглероживалась, становилась твердой после закалки в воде, в то время как сердцевина оставалась вязкой, пластичной.
Кто не читал о варварском способе закалки стали в теле человека? В Древней Сирии, повествует легенда, клинок нагревали до цвета вечерней зари и шесть раз вонзали в ягодицы молодого раба. Известны приемы подобной закалки стали охлаждением в теле свиньи, барана или теленка. Был ли смысл в этом страшном ритуале? Оказывается, как это ни крамольно звучит, был. Он связан с химико-термической обработкой стали, которая называется цианированием.
Под цианированием понимают процесс насыщения поверхности стали одновременно углеродом и азотом. По сравнению с цементированным цианированный слой обладает более высоким сопротивлением износу, немалой твердостью, хорошей устойчивостью против атмосферной коррозии.
Твердое цианирование — процесс, аналогичный цементации. Он состоит во взаимодействии стали при нагреве с цианистыми солями. Основным компонентом солей является группа (СN), которая снабжает поверхность стали углеродом и азотом одновременно. Таким образом, цианирование — это совмещенный процесс цементации и азотирования. Для цианирования применяют чаще всего желтую кровяную соль К4Fе(CN)6 (. Если посыпать такой солью поверхность детали и нагреть ее до температуры 500–600 °C, то в результате диффузии углерода и азота в тонкий поверхностный слой детали произойдет цианирование.
Но почему желтую соль К4Fе(СN)6 называют кровяной? Оказывается, потому что ее длительное время получали сплавлением обугленной животной крови с поташом и железом. Не исключено, что древние воины после битвы обмывали свои клинки водой и сушили на кострах. На клинках оставалась кровь, а в озерной воде часто бывает много растворенного поташа (К2СО3). Так, совершенно случайно в древности осуществляли цианирование стали. Между тем воины замечали, что после применения в сражениях поверхность их клинков становится твердой, износостойкой. Это и могло послужить основой «кровавого способа» термообработки холодного оружия.
После ковки и термической обработки клинки обтачивались на точильных камнях, шлифовались и полировались. Эта работа включала ряд технологических операций и тоже требовала навыков, опыта и знания целого ряда ремесленных секретов.
Черновая шлифовка осуществлялась обычно на небольшом широком камне. Клинок заворачивался в предохраняющую ткань, обнажался только участок который подвергался шлифовке. Затем ткань передвигалась, и шлифовался следующий участок. Чистовая шлифовка делалась мелкозернистыми камнями различных сортов: корундом, наждаком, песчаником и другими. Доводка производилась на 4–8 камнях, а лучших клинков — на 15. Сохранилась миниатюра XII века, изображающая процесс изготовления мечей. Точило укреплено на деревянной колоде, наполненной водой. Подмастерье крутит ручку точила, а мастер шлифует клинок.
После обработки на камне клинки шлифовались различными тканями. В Индии нередко мастер заканчивал полировку пальцами своей руки. Советский филолог Н. Р. Гусева, прожившая несколько лет в Индии, так описывает процесс полировки изделий, который согласно преданиям был в ходу у древних индийцев: «Полировка осуществлялась при помощи трех компонентов: песка, наждака и пальца. Так вот, пальцем день за днем, с утра до ночи, месяц за месяцем, год за годом, поколение за поколением. И получали идеальную гладкую поверхность…».
Необыкновенное умение и титанический труд требовались, чтобы изготовить булатный клинок. Один клинок делался не часы, не дни, не месяцы, а годы…
Теперь совершенно ясно, что секрет булата был не один — их было несколько. Первая группа секретов относится к особенностям технологии получения слитка булатной стали с присущей ему неравновесной структурой, физической и химической неоднородностью. Эти секреты теперь расшифрованы, получен булатный слиток.
Вторая группа секретов относится к искусству ковки и получению булатных узоров. Многие приемы ковки булата сегодня осмыслены и познаны, воспроизведены почти все известные булатные узоры. Но тут еще последнее слово не сказано, работы в этой области продолжаются.
Третья группа секретов касается чистоты исходных материалов, обеспечивавшей особый химический и фазовый состав углеродистой стали, вырабатываемой в древности. Эти секреты современная наука также постепенно раскрывает.
Четвертая группа секретов включает термическую и химико-термическую обработку стали. Многовековой опыт металлообрабатывающего ремесла позволил оружейникам найти оптимальные режимы термомеханической обработки, цементации, закалки и отпуска стали, которые они держали в секрете. За время, прошедшее с тех пор, термическая обработка стали превратилась в стройную науку. Пользуясь современными теоретическими и экспериментальными методами анализа, можно раскрыть многие секреты, касающиеся термообработки древнего булата.
Наконец, пятая группа секретов касается отделки булатного оружия. Здесь следует решительно признать: воспроизведение методов шлифовки и полировки древних клинков — дело для нас чрезвычайно трудное. Поэтому пока еще никому не удалось достичь легендарной упругости булатных клинков.
Исходя из секретов производства булатной стали сегодня можно достаточно убедительно ответить на вопрос: что такое булат? Но ответ этот будет не прост.
Булат — это углеродистая заэвтектоидная сталь. Булат не только углеродистая сталь, булат — сталь сверхуглеродистая, близкая по составу к чугуну. Булат не только сверхуглеродистая сталь, булат — сталь особо чистая, без посторонних примесей. И наконец, булат — высокоуглеродистая сталь, обладающая неравновесной структурой, с ярко выраженной макро- и микронеоднородностью. Булат — слоистая сталь. Очень твердые слои с высоким содержанием углерода чередуются в булате со слоями, мало насыщенными углеродом и поэтому пластичными. В процессе ковки все слои переплетаются, образуя характерный естественный рисунок. Булат — узорчатая сталь. Структура булата после применения специальных методов ковки, термомеханической обработки и отделки обеспечивает ему необычайно высокие механические свойства. Булат — сталь, обладающая одновременно высокой твердостью, прочностью, вязкостью и упругостью. Чередование мягких и очень твердых участков на лезвии клинка превращает его в микропилу и обеспечивает самозатачиваемость. Булат — сталь, обеспечивающая необычайную остроту лезвия клинка и его самозатачиваемость. Таким образом, в понятие «булат» вкладывается целый ряд характерных особенностей этой замечательной стали.
Поделитесь на страничкеСледующая глава >
tech.wikireading.ru
Открытие секрета булата
Pаботы Аносова создали новую технику, новые методы производства качественной, «совершенной стали».
При «отыскивании тайны приготовления булатов» Аносовым были разработаны четыре метода производства качественной стали главным образом за счет усовершенствования тигельной плавки.
Первый метод — «сплавление железных руд с графитом, или восстановление и соединение железа с углеродом»93, то есть метод непосредственного восстановления железа из руды. Этот способ Аносов и считал подлинным методом производства булатов на Востоке. «Древние,— говорил он,— скорее могли напасть на способ простой, нежели сложный» благодаря тому, что «употребление тиглей столь же древне, как и известность золота; ничего не могло быть ближе для древних алхимиков, как испытание плавкою всех тел, похожих по наружному виду на металл»94.
Однако этот метод не мог удовлетворить Аносова. Для применения метода были нужны чистейшие руды, не содержащие посторонних примесей, особенно серы. Кроме того, он был невыгоден экономически. «Дороговизна делает сей способ недоступным для введения в большом виде»,— замечает Аносов.
Разработка этого метода, раскрывая секрет производства булатной стали, в то же время не отвечала общей задаче, поставленной исследователем,— массовому производству качественной стали. Поэтому Аносов продолжал изыскания, стремясь найти метод, более приемлемый.
Второй метод — «сплавление железа при доступе углей или соединение его предварительно с углеродом и восстановление его посредством закиси железа» (то-есть переплавка чугуна с окалиной)
Этот способ также оказался непригодным для массового производства стали. Получаемый металл содержал много углерода и с трудом подвергался ковке. По мнению Аносова, это происходило оттого, что круглое железо было недостаточно чистым, плохо очищалось при тигельной плавке.
Открыв второй метод, Аносов положил им начало процессу передела чугуна в сталь, широко известному теперь под названием скрап-процесса, намного опередив французов братьев Мартен.
Второй метод также не был использован Аносовым, но впоследствии оказался полезным известному новатору
Фиг. 12. Отрывок из труда П. П. Аносова «О булатах» о преимуществе златоустовской стали перед английской.
русской техники инженеру А. А. Износкову, который, используя его, сумел в 1869 г. сравнительно легко и быстро организовать передел чугуна в сталь в первой мартеновской печи в России, на Сормовском заводе.
Третий метод — получение литого булата (сталь отливалась в форму) при продолжительном отжиге без доступа ©оздуха (в засыпке). Этот способ был использован Аносовым на Златоустовском заводе для получения литых булатов, «годных на выделку дешевых изделий».
Сущность метода состояла в том, что стали, приготовленной в тигле, не давали °атвердевать в тигле, а отливали ее в формы. «Отливка стали в форму,— писал Аносов,— хотя нарушает наклонность к кристаллованию (то есть создает иные условия кристаллизации, чем при застывании большого ее количества в тигле), но она необходима для облегчения проковки больших сплавок и составляет единственное средство к удешевлению булатов до ценности стали.
Литая сталь подвергалась длительному отжигу в специальной печи, сконструированной Аносовым, без доступа воздуха, будучи тщательно закупоренной в ящике. Преимущество отожженной стали заключалось в том, что она «удобно куется, мягче в опиловке, менее повреждается в закалке и стойчее после оной». На отожженной стали обнаруживались узоры: на мягкой — мелкие, на твердой -крупные. Чем лучше было качество стали, тем скорее она приобретала крупнозернистое строение. «Отожженная сталь, как имеющая узоры, подобные булатным, должна нести и одинаковое с ней название. Для отличия от настоящего булата я называю ее литым булатом»,— говорил Аносов.
При определении технологии отжига Аносов обратил внимание на различный характер изменения свойств стали. Неправильный отжиг, связанный с доступом воздуха в коробку, вызывал обезуглероживание поверхности, характерное «зернистым сложением на поверхности», которое создавало «особый кант белого цвета по -краям бруска». Пережог брусков («повреждение стали») характеризовался «удобным разламыванием их без закалки». Хорошо отожженная сталь имела чистую поверхность без следов окалины, хорошую вязкость и «ровное крупнозернистое сложение в изломе».
По наблюдениям Аносова, части, соответствующие верху отлитой болванки, «почти никогда не имели крупнозернистого строения, а следовательно, и узора — рисунка. Это обстоятельство позволило Аносову сделать заключение, что ясность узора связана не только с кристаллическим строением, но и с чистотой стали. Аносов широко использовал отжиг не только на литых сталях, но и как предварительную операцию, отжигая сталь, идущую в шихту.
Применение отжига значительно повысило качество златоустовской стали, поставило ее выше лучшей английской тигельной стали. К тому же найденный Аносовым способ получения качественной стали был «много проще английского. «Подобного улучшения не было достигнуто в Англии помощью отжигания,— писал Аносов,— мне кажется потому, что тамошние мастера недовольно обращали внимание на изменения в стали при различных условиях отжигания, а приписывали улучшение ее более влиянию посторонних тел, -при отжигании обыкновенно применяемых».
Здесь Аносов также поднимается выше своих современников — иностранных ученых, отдавая должное превращениям в самой стали, а не внешним факторам, например, влиянию засыпки и ее «магическому» действию.
Ироническое отношение Аносова к качеству английской стали и устаревшему с его точки зрения способу Гэнстмана — методу тигельной переплавки предварительно цементованной стали, очень хорошо выражено им в следующих словах: «Бритва из хорошего булата, без ошибок приготовленная, выбреет, по крайней мере, вдвое больше бород, нежели лучшая английская».
Четвертый метод — «сплавление железа «непосредственно с графитом, или соединение его прямо с углеродом»101 — Аносов считал наилучшим из всех разработанных им и экономически наиболее выгодным «к получений) настоящих булатов».
Эту точку зрения разделяли и русские ученые. Один из современников Аносова — проф. П. П. Эйнбродт,— восхищенный его трудом «О булатах», в личном письме к нему подчеркивал значение четвертого способа, заявляя, что им исследователь «справедливо может гордиться».
Для четвертого метода Аносов разработал полную технологию. Эту интересную технологию мы приводим в сокращенном виде.
Плавка. В тигель загружали 12 фунтов (около 5 кг железа). Если же необходимо было получить более твердый металл, количество железа уменьшалось до 10 или 8 фунтов. Железо засыпалось смесью графита, железной окалины и флюса. В качестве флюса Аносов рекомендовал доломит.
После загрузки тигля его закрывали глиняной крышкой и пускали дутье для достижения «сильного жара». Дутье регулировалось «ртутным духомером». По истечении трех с половиной часов металл расплавлялся и покрывался тонким слоем шлака с плавающим в нем графитом, всплывшим частично в шлак.
Потери графита составляли за этот промежуток времени 100 г. После плавки в течение четырех с половиной часов они повышались до 200 г, а при плавке в течение пяти с половиной часов до 400 г. По окончании плавки тигель оставляли в печи до полного остывания. Затем отбивали крышку тигля, высыпали остатки графита, а шлак разбивали. Металл извлекался из тигля в форме «сплавка, имеющего вид хлебца» и при медленном охлаждении постепенно затвердевал.
Поверхность застывшего металла получалась либо ровной, либо с некоторым углублением около середины, «в котором кристаллы булата более видимы и между собой перепутаны». «Это,— говорил Аносов,— составляет усадку». Она была сильнее для более твердой стали. Отсутствие усадки свидетельствовало о том, что «усадочная раковина находится внутри», и показывало, что «такой булат скорее остывает снаружи, нежели внутри». Подобные слитки не ковались и давали плохой сорт булата. Такое совершенно правильное толкование явления усадки, насколько нам известно, было впервые отмечено также Аносовым.
От длительности плавки зависел характер рисунка стали. После плавки в течение трех с половиной часов металл имел слабые продольные узоры, светлый грунт. После плавки в течение четырех с половиной часов узоры на металле получались волнистые, средней величины. Наконец, после плавки в течение пяти с половиной часов, при хорошем качестве графита, металл выходил с крупными узорами,— се тчатыми, «а иногда и с коленами». Все это подтверждало точку зрения Аносова о влиянии углерода на характер и ясность рисунка.
«Наибольшее время плавки и медленное охлаждение тигля» служили гарантией качества стали.
Шихтовка описана Аносовым в «Журнале опытам по приготовлению литой стали и булатов с краткими замечаниями».
Вот два примера шихтовки, взятые из этого журнала (табл. 1 и 2):
Таблица 1
Фиг. 13. Первая страница «Журнала опытам го приготовлению литой стали и булатов» П. П. Аносова.
Ковка105. Ковка производилась тюд хвостовым молотом, весом в два с половиной пуда (40 кг). «Сплавок нагревался в горне досветлокрасного каления и укладывался под молот широким основанием. Проковка велась при слабом обжатии при поворотах «кругом в одну сторону». Промежуточные нагревы проводились пять-девять раз.
Чем медленнее проковывался булат, тем лучше было его качество. После ковки металл разрубали. Разрубленные части снова проковывались под молотом сначала в бруски, а затем в полосы. Лучшие булаты, несмотря на твердость, проковывались из брусков в полосы с двух нагревов.
При ковке тщательно соблюдалась температура нагрева, та «степень жара», при которой «узор не теряется». Сталь нельзя было перегреть. «Потеря узора во время ковки — есть порча металла».
Полосы имели неровности и плены, обтачивались и клеймились для обозначения нижней части, которая шла на изготовление лезвий. Чистовая ковка проводилась при малом нагреве не сильнее «мяснокрасного цвета».
Закалка106. Операция нагрева и быстрого охлаждения стали называлась закалкой. Закаленная сталь обладала высокой твердостью, но вместе с тем и хрупкостью, «подобною стеклу». Для понижения хрупкости и для «сохранения, по возможности, твердости, приобретенной закалкой,— указывал Аносов,— искусство нашло средство в нагревании закаленной стали, но гораздо слабейшем, нежели при закалке». Далее он писал: «Предназначение изделия определяет меру нагревания, а появляющиеся на металле цветы (цветы побежалости) служат признаками для определения самой меры. Нагревание закаленной стали называется отпуском и главнейшие степени его по цветам суть: желтый, фиолетовый, синий и зеленый. Желтый цвет означает самую малую, а зеленый самую большую степень отпуска, при которой упругость металла начинает теряться».
Эти высказывания Аносова показывают, что он совершенно правильно определял понятие закалки и отпуска стали; также правильно характеризовал он свойства, изменяющиеся при отпуске.
Булаты закаливались в зависимости от назначения или в сале, или в воде, причем «самые твердые из них преимущественно в сале».
Аносов считал, что «оружие всякого рода достаточно закаливать в сале, «предварительно нагретом почти до точки кипения, ибо дознано из опытов, что в горячем сале закалка бывает тверже, в сем случае сало скорее ее охлаждает».
Таким образом, Аносов впервые дал метод закалки в «горячей среде» и объяснил ее действие.
Булаты закаливались путем нагрева откованного лезвия «докрасна» с последующим погружением в сало. После остывания лезвие обтиралось и для удобства наблюдения за цветами побежалости при отпуске зачищалось точильным камнем. Отпуск требовал большого искусства, так как нагрев производился «над углями» и при отпуске сабельного клинка различные части отпускались по-разному: у ручки — до зеленого цвета, у конца — до синего, в середине — до фиолетового, на месте «удара у лезвия» — до желтого. Отпущенный клинок .правился молотом и охлаждался в воде. Если же был необходим более упругий клинок, отпуск всего изделия проводился до синего цвета.
Аносов указывал также на возможность воздушной закалки тонких изделий «в быстрой струе воздуха».
Прсле закалки клинки подвергались точке и полировке. И для этой, казалось бы, простой операции Аносов дал ряд указаний, направленных на сохранение твердости. Он указывал, в частности, на недопустимость применения сухих точил, точение на которых вызывало нагрев и приводило к потере упругости; рекомендовал применять мокрые точила с соблюдением необходимых предосторожностей.
Впервые в истории металловедения Аносов описал и правильно объяснил также явление прижога закаленной стали при шлифовании.
Травление — «вытравка». Операция травления была необходима для выявления рисунка и определения качества булата. При разработке методов травления Аносов показал разное действие отдельных кислот.
Понятие о макроструктуре, как о показателе качества металла, выявление макроструктуры травлением, равно как и применение микроскопа для изучения макроструктуры как метода исследования, впервые были введены и Распространены Аносовым. Это — огромный вклад Аносова в металловедение.
Аносов дал также ясное описание строения стали, узоры которой похожи на виноградные гроздья, иногда расположенные рядами, сходные между собой. Правда, он не дал понятия о дендритах, позднее введенного Д. К. Черновым, но он наблюдал их, и его «виноградные грозды» дают точное описание дендритного (древовидного) строения стали. Этим он в известной мере предвосхитил дендритную теорию Д. К. Чернова.
К сожалению, до наших дней не сохранилось документального материала о макроструктурах сталей Аносова. Представление о макроструктуре и микроструктуре булатной стали дают фотографии начала нашего столетия, сделанные последователями Аносова (фиг. 14—15).
Первый клинок из -булатной стали был изготовлен Аносовым в 1837 г.109. Но об открытии Аносова еще долго не знали ни в России, ни заграницей. При состоянии связи того времени сведения с далекого Урала с трудом доходили до общественности столиц, а правительственные круги, преклонявшиеся перед английской литой сталью, которым было известно о блестящем успехе Аносова, его замалчивали. Не удивительно поэтому, что в то время, когда на одном конце России — на Урале секрета булата не стало, на другом — в Грузии попреж-нему считали искусство булатной стали тайной. Тайна закалки булата еще в 1838 г. служила средством для поэтических образов великому русскому поэту М. Ю. Лермонтову. Будучи в это время в ссылке на Кавказе, он посвятил булату известные стихотворные строки:
«Отделкой золотой блистает мой кинжал; Клинок надежный, без порока; Булат его хранит таинственный закал — Наследье бранное Востока
Сам Аносов, проводивший свои опыты с булатной сталью с исключительной научной тщательностью и с такой же тщательностью обобщавший их, не мог скоро подытожить их результаты.
На это у него ушло четыре года. И только в 1841 г., с появлением в печати его труда «О булатах», передовая общественность России широко заговорила об его открытии. «Сочинение Аносова «О булатах» возбудило общее внимание» — писала в июле 1841 г. газета «Мануфактурные и горнозаводские известия»
В октябре того же года «Горный журнал» заявлял: «Открытие способа приготовления булата, не уступающего качествами лучшим булатам азиатским, принадлежит, бесспорно, к числу важнейших открытий, которыми обогатилась наша промышленность в последние годы, и мы этим обязаны трудам Корпуса горных инженеров г.-м. Аносова.
Превосходные качества изделий, приготовленных из златоустовского булата, при необыкновенной дешевизне их, ручаются за прочность открытия».
Изделия, изготовляемые из булатной стали Аносова, отличались высоким качеством. С ними не могли соперничать изделия, изготовленные из любой стали, известной в то время. Например, «шпажный клинок из хорошего булата, правильно выточенный и соответственно закаленный, как оказалось по моим опытам,— говорил сам Аносов,— не может быть при гнутье ни сломан, ни согнут до такой степени, чтобы потерять упругость; при обыкновенном гнутье он выскакивает и сохраняет прежний вид; при усиленном (например, будучи загнут под прямым углом) не сломается и, будучи выпрямлен, не потеряет прежней упругости.
При этой связи в частях булатный клинок может быть тверже всякого другого, приготовленного из стали. Это и есть, без сомнения, предел совершенства в упругости, которая в стали не встречается»112.
Отмечая качества аносовской булатной пластинки, «Горный журнал» свидетельствовал: «она сгибалась без малейшего повреждения, издавала чистый и высокий звон. Отполированный и закаленный конец ее крошил лучшие английские зубила, тогда как отпущенный конец легко принимал впечатления и отсекался чисто и ровно».
Изделия из булатной стали демонстрировались на отечественных и зарубежных промышленных выставках и везде вызывали общее восхищение.
Обозреватели 3-й Московской мануфактурной выставки 1843 г. писали: «теперь Россия представляет единственный в целом мире источник нового булата лучших качеств. Булаты наши ценятся между азиатцами по крайней мере в десять раз дороже против здешней (-московской И. Б.) цены их. Сталь златоустовских заводов известна по отличному качеству вырабатываемого из нее белого оружия… Должно отдать справедливость их булатным кинжалам, которые оказались отличнейшего достоинства».
Иностранцы, поставленные Аносовым перед фактом, вынуждены были признать высокое качество его булатной стали, несмотря на свое скептическое отношение к русской промышленности. Рецензент английской газеты «Морнинг пост», обозревавший русское отделение на Лондонской всемирной выставке 1851 г. в отчете, составленном в довольно сдержанном тоне, все же отмечал, что «замечательный успех этой отрасли русской промышленности (выделка булатной стали), без сомнения, относить можно высокому качеству употребляемой стали».
«Было бы несправедливо,— заявлял он при этом,— не воздать должной почести и хвалы усердию, энергии и знаниям того ученого Корпуса инженеров (речь шла о П. П. Аносове И. Б.), на который возложено великое призвание распространять ремесленность и промышленность… в глубине лесов Урала и Алтая»115.
И в то же время иностранцы на русской службе пытались принизить роль Аносова в сталелитейном деле.
По случаю открытия Аносова перед Российской Академией наук был поставлен вопрос о присуждении ему Демидовской премии. Его способ производства булатной стали был передан на заключение академикам-иноземцам (непременный секретарь Фус и др.).
Фиг. 17. Чертежи устройства печей П. II. Аносова для производства булата. Устройство печи (чертежи AB—план и разрез): а — топило; b — колосники; с — пролеты из топила под основанием свода; d—чугунный ящик; е —кирпичи, поставленные на ребро, на которые становился ящик; f —обратные пролеты, под ящиком; стены по сторонам ящика; х — свод; i—пролеты; выведенные с одной стороны до высоты свода, в которые обращалось из него пламя; h — дымовая труба.
Не признать высоких качеств аносовских булатов было нельзя — они были слишком очевидны и слава о булатах шла далеко. Поэтому иностранцы на русской службе постарались запутать дело. Дав в общем высокую оценку булатной стали, они решили поставить под сомнение способ ее производства, разработанный Аносовым.
В своем заключении эксперты заявляли: «Если бы в сочинении Аносова было указано, каким образом можно всегда с удачею изготовлять эту (булатную И. Б.) сталь, то не колеблясь должно было признать это открытие одним из полезнейших обогащений промышленности, и в особенности отечественной. Но в описании столь мало сказано о способе приготовления этого булата, что надобно думать, не представляет ли Аносов себе самому этой тайны, или может быть и ему самому только временем и случайно выдается изготовлять такую сталь
При таковом положении дела академики не решаются представить Академии о присуждении Аносову демидовской награды за изобретение, которое не содержалось еще общим достоянием и о котором даже неизвестно, основано ли оно на приемах верных и доступных для всех и каждого».
Вопреки истине, вопреки тому, что Аносов дал вполне ясное представление о своем способе в сочинении «О булатах»,— Академия отклонила предложение о присуждении ему премии. Такое позорное событие могло иметь место только в условиях крепостнической, а позднее и капиталистической России, где раболепие правящих классов и низкопоклонство «официальной» науки перед иностранщиной не знало границ.
Однако ни общие условия того времени, ни отдельные реакционные попытки не могли подорвать значения открытия Аносова. Начатое им прогрессивное дело, знаменовавшее новый этап в развитии металлургии, упорно прокладывало себе путь вперед усилиями самого Аносо-на, а после него его последователями.
К ОГЛАВЛЕНИЮ
www.himikatus.ru
Булат и дамасская сталь — загадки и история
Булат – одна из самых интересных и загадочных страниц в истории металлургии.
Сейчас хорошо известно, как в древние времена делали каменные топоры, бронзовую утварь, варили железо и плавили чугун, но до нашего времени остаются нераскрытыми многие секреты производства булатного оружия.
Впервые Европа познакомилась с булатом при столкновении армии Александра Македонского с войсками индийского царя Пора. Особенно поразил македонцев панцирь захваченного в плен царя. Он был сделан из необыкновенно прочного белого металла, на котором македонское оружие не смогло сделать ни вмятины, ни царапины. Из булата были изготовлены и широкие индийские мечи, которые легко рассекали пополам македонское железо.
По свидетельству историков, древнее европейское железное оружие было настолько мягкое, что после двух-трех ударов уже гнулось, и воины вынуждены были отходить, чтобы выпрямить клинок. Естественно, что индийские мечи македонцам казались чудом.
Индия, XIX век. Булатная сталь. Клинок изготовлен из булатной стали. Рукоять стальная, украшена растительными мотивами, выполнеными насечкой серебром по стали.
Ковка, насечка серебром по стали. Клинок изготовлен из двух слитков булатной стали, место соединения фрагментов хорошо различимо. Общая длина: 93,7 см., длина клинка: 80,5 см., ширина клинка у рукояти: 3,7 см
Задолго до этого с Гималайских гор в Пенджаб (древнейшее княжество в Индии) спустилась каста кузнецов, хорошо знающих железное дело и умеющих изготовлять железное оружие с необычайными свойствами. Из Пенджаба индийское железо и способы его обработки распространились в Сиам и Японию.
«Никогда не будет народа, который лучше разбирался бы в отдельных видах мечей и в их названиях, чем жители Индии!» — писал средневековый ученый Аль-Бируни. Он также поведал, что клинки в Индии делались разных цветов. Мечи, например, изготовлялись зелеными, синими, могли они и иметь узор, напоминающий рисунок ткани. Индийская сталь отличалась узорами, которые были видны на клинке.
А свойствами клинки обладали действительно удивительными. Будучи твердыми и прочными, они одновременно обладали большой упругостью и вязкостью. Клинки перерубали железные гвозди и в то же время свободно сгибались в дугу. Нет ничего удивительного в том, что индийские мечи крошили европейские, которые в древности часто делались из недостаточно упругих и мягких низкоуглеродистых сортов стали.
Лезвие индийского клинка после заточки приобретало необыкновенно высокие режущие способности. Хороший клинок легко перерезал в воздухе газовый платок, в то время как даже современные клинки из самой лучшей стали могут перерезать только плотные виды шелковых тканей. Правда, и обычный стальной клинок можно закалить до твердости булата, но он будет хрупким, как стекло, и разлетится на куски при первом же ударе. Поэтому позднее, когда европейские сабли начали изготовлять из прочных и твердых сортов углеродистых сталей, они ломались при ударе индийского оружия.
«Искусство Блистательной порты — выставка Музеев Кремля. Шапка Ерихонская (Шлем) князя Федора Ивановича Мстиславского.
Турция, XVI в., Булатная сталь, серебро, рубины, бирюза, ткань; ковка, чеканка, насечка золотом, резьба.»
Основное назначение булата – изготовление клинков. Главное достоинство клинка – острота его лезвия. Лезвие булатного клинка можно было заточить до почти неправдоподобной остроты и сохранить эту остроту надолго. У клинков из обычной углеродистой стали заостренное лезвие выкрашивается уже при заточке – как бритву, его заточить нельзя, а булат затачивали до остроты бритвы, и он сохранял свои режущие свойства после того, как побывал в деле. Такое возможно лишь тогда, когда сталь обладает одновременно высокой твердостью, вязкостью и упругостью – и в этом случае лезвие клинка способно самозатачиваться. Булатная сабля легко сгибалась на 90-120 градусов, не ломаясь. Есть сведения, будто настоящий булатный клинок носили вместо пояса, обматывая им талию.
Слитки литого булата в виде разрубленных лепешек «вутцев» привозились из Индии в Сирию, где в городе Дамаске из них выковывали эти сказочные клинки. Но индийская булатная сталь стоила очень дорого, и сирийские кузнецы изобрели сварной булат, правильно определив, что булат — первый созданный человеком композит, состоит из частиц твердой углеродистой стали в матрице из мягкой и упругой низкоуглеродистой стали. Дамасская сталь получалась путем многократных проковок в разных направлениях пучка из стальных прутков разной твердости. Качество клинков из сварной дамасской стали было по тем временам очень высокое, но такого сочетания прочности и упругости, как в оружии из литого индийского булата, сирийским кузнецам добиться не удалось.
Еще один центр производства качественных клинков образовался в средние века в Японии. Японский булат обладал каким-то необыкновенным качеством железа, которое после целого ряда проковок приобретало даже более высокую твердость и прочность, чем дамасская сталь. Мечи и сабли, приготовленные из этого железа, отличались удивительной вязкостью и необыкновенной остротой.
ДАМАССКИЙ УЗОР на персидской сабле (вверху и в центре) обусловлен неравномерным содержанием углерода в сверхвысокоуглеродистой стали: светлые участки «дамаска» состоят из карбида железа (цементита), а темный фон образован железом, содержащим значительно меньше углерода. Узор проявляется только после полировки готового клинка и его протравливания кислотой. На микрофотографии образца современной сверхвысокоуглеродистой стали (внизу, х 200) хорошо видна сетка цементита; фоновая структура также состоит из чередующихся слоев цементита и железа.
Дамасские стали становились более вязкими после ковки, которая разрушала цементитную сетку и придавала поверхностному узору окончательный вид. Влияние ковки можно видеть на персидской сабле: удары молота оставили вертикальные метки, образовавшие необычный дамасский узор — «лестницу Магомета». Сабля относится к XVII в. или, возможно, к более позднему времени; хранится в Метрополитен-музее в Нью-Йорке.
Уже в наше время был сделан химический анализ стали, из которой изготовлено японское оружие XI-XIII веков. И древнее оружие раскрыло свою тайну: в стали был найден молибден. Сегодня хорошо известно, что сталь, легированная молибденом, обладает высокой твердостью, прочностью и вязкостью. Молибден – один из немногих легирующих элементов, добавка которого в сталь вызывает повышение ее вязкости и твердости одновременно. Все другие элементы, увеличивающие твердость и прочность стали, способствуют повышению ее хрупкости.
Естественно, что в сравнении с дамасскими клинками, сделанными из железа и стали, японские легированные мечи и сабли казались чудом. Но значит ли это, что японцы умели в то далекое время делать легированную сталь? Конечно, нет. Что такое легированная сталь, они даже не знали, так же как и не знали, что такое молибден. Руда, из которой древние японские мастера выплавляли железо, содержала значительную примесь окиси молибдена. Выплавленное из обогащенных молибденом «песков» кричное железо проковывалось в прутья и закапывалось в болотистую землю. Время от времени прутья вынимали и снова зарывали, и так на протяжении 8-10 лет.
Насыщенная солями и кислотами болотная вода разъедала пруток и делала его похожим на кусок сыра. Тем самым из заготовки удалялись вредные примеси, быстрее разъедаемые болотной водой. Затем разогретую заготовку японский кузнец проковывал в тонкую полосу, сгибал, опять проковывал и так несколько тысяч раз! Но и японские клинки при всей их выдающейся остроте и прочности не обладали качествами индийского булата, особенно упругостью.
Сабля Мазепы, Эрмитаж
Арабский ученый XII века Едриза сообщает, что в его время индийцы еще славились производством железа, индийской сталью и выковкой знаменитых мечей. В Дамаске из этой стали изготовляли клинки, славу о которых крестоносцы разнесли по всей Европе. К сожалению, в Древней Индии так тщательно прятали секреты выплавки вутца, что в конце концов потеряли их совсем. Уже в конце XII века клинки из литого булата высшего качества «табан» не могли делать ни в Индии, ни в Сирии, ни в Персии.
После того как Тимур покорил Сирию и вывез оттуда всех мастеров, искусство изготовления оружия из литого булата переместилось в Самарканд; однако вскоре оно везде пришло в упадок. Потомки вывезенных мастеров, рассеявшись по всему Востоку, окончательно потеряли способы изготовления булатного оружия. В XIV – XV веках секрет производства литого булата и изготовления из него холодного оружия был окончательно потерян. Европейские кузнецы не смогли до конца разгадать секрет производства даже дамасской сварной стали и больше преуспели в производстве клинков из однородной (гомогенной) стали с имитацией рисунка булата на поверхности клинка. Особенно широко развернулось производство подделок под булат в XVIII-XIX веках. В это время в Европе научились производить высокоуглеродистую литую сталь, и западноевропейские мастера, оставив попытки раскрыть секреты производства сварочного булата, начали изготовлять из нее довольно хорошее холодное оружие. В Италии (Милан), в Испании (Толедо), в Германии (Золинген), во Франции (Льеж) и даже в Англии стали широко производить «ложный булат». «Ложные булаты», особенно золингеновские и толедские, приобрели известность благодаря высокой степени полировки и красивыми узорами, которые наносились на клинки различными методами. Ремесленники, рисующие декоративные узоры на металле, назывались «дамаскировщиками», а клинки «ложного булата» — «дамаскированными». Многие «дамаскированные» клинки были не очень высокого качества, поскольку они изготовлялись из обычной шведской или английской углеродистой стали.
Не одно столетие металлурги всех стран и народов пытались выплавить булатную сталь, но злополучная тайна никому не давалась. В XIX веке учеными-металлургами предпринималось множество попыток раскрыть секрет литого булата, даже великий английский ученый Фарадей безуспешно бился над решением этой задачи. Но получить литой булат, не уступающий по свойствам индийскому вутцу, удалось только русскому ученому, горному начальнику златоустовских заводов П.П. Аносову в 40-ых годах XIX века. Сохранившийся до наших дней аносовский булатный клинок, перерубает гвозди, гнется в дугу и на лету перерубает газовый платок. Секрет древних индийских мастеров открыт? И да и нет. После смерти П.П. Аносова, несмотря на оставленный им подробный рецепт, воспроизвести литой булат не удается никому!
Уже в наше время златоустовские металлурги вновь попытались воскресить технологию производства булата. Сложны и длительны были эти поиски, но узорчатая сталь вновь была получена, хотя полностью повторить аносовский булат не удалось. Легендарная упругость клинков достигнута не была.
Современные качественные легированные стали превосходят булат по всем показателям: прочности, упругости, режущим свойствам, но добиться таких выдающихся свойств в одном образце не удается и сейчас.
Тайна индийского литого булата ждет своей разгадки!
Автор: Santa-Maria7lostworlds.ru
Открытие секрета булата — Блог Златоуста
Работы Аносова создали новую технику, нозые методы производства качественной, «совершенной стали».
При «отыскивании тайны приготовления булатов» Аносовым были разработаны четыре метода производства качественной стали главным образом за счет усовершенствования тигельной плавки.
Первый метод — «сплавление железных руд с графитом, или восстановление и соединение железа с углеродом», то есть метод непосредственного восстановления железа из руды. Этот способ Аносов и считал подлинным методом производства булатов на Востоке. «Древние,— говорил он,— скорее могли напасть на способ простой, нежели сложный» благодаря тому, что «употребление тиглей столь же древне, как и известность золота; ничего не могло быть ближе для древних алхимиков, как испытание плавкою всех тел, похожих по наружному виду на металл».
Однако этот метод не мог удовлетворить Аносова. Для применения метода были нужны чистейшие руды, не содержащие посторонних примесей, особенно серы. Кроме того, он был невыгоден экономически. «Дороговизна делает сей способ недоступным для введения в большом виде»,— замечает Аносов.
Разработка этого метода, раскрывая секрет производства булатной стали, в то же время не отвечала общей задаче, поставленной исследователем,— массовому производству качественной стали. Поэтому Аносов продолжал изыскания, стремясь найти метод, более приемлемый.
Второй метод — «сплавление железа при доступе углей или соединение его предварительно с углеродом и восстановление его посредством закиси железа» (то-есть
Отрывок из труда П.П. Аносова «О булатах» о преимуществе златоустовской стали перед английской
переплавка чугуна с окалиной). Этот способ также оказался непригодным для массового производства стали. Получаемый металл содержал много углерода и с трудом подвергался ковке. По мнению Аносова, это происходило оттого, что круглое железо было недостаточно чистым, плохо очищалось при тигельной плавке.
Открыв второй метод, Аносов положил им начало процессу передела чугуна в сталь, широко известному теперь под названием скрап-процесса, намного опередив французов братьев Мартен.
Второй метод также не был использован Аносовым, но впоследствии оказался полезным известному новатору русской техники инженеру А. А. Износкову, который, используя его, сумел в 1869 г. сравнительно легко и быстро организовать передел чугуна в сталь в первой мартеновской печи в России, на Сормовском заводе.
Третий метод — получение литого булата (сталь отливалась в форму) при продолжительном отжиге без доступа воздуха (в засыпке). Этот способ был использован Аносовым на Златоустовском заводе для получения литых булатов, «годных на выделку дешевых изделий».
Сущность метода состояла в том, что стали, приготовленной в тигле, не давали атвердевать в тигле, а отливали ее в формы. «Отливка стали в форму,— писал Аносов,— хотя нарушает наклонность к кристаллованию (то есть создает иные условия кристаллизации, чем при застывании большого ее количества в тигле И.Б.), но она необходима для облегчения проковки больших сплавок и составляет единственное средство к удешевлению булатов до ценности стали».
Литая сталь подвергалась длительному отжигу в специальной печи, сконструированной Аносовым, без доступа воздуха, будучи тщательно закупоренной в ящике. Преимущество отожженной стали заключалось в том, что она «удобно куется, мягче в опиловке, менее повреждается в закалке и стойчее после оной». На отожженной стали обнаруживались узоры: на мягкой — мелкие, на твердой — крупные. Чем лучше было качество стали, тем скорее она приобретала крупнозернистое строение. «Отожженная сталь, как имеющая узоры, подобные булатным, должна нести и одинаковое с ней название. Для отличия от настоящего булата я называю ее литым булатом»,— говорил Аносов.
При определении технологии отжига Аносов обратил внимание на различный характер изменения свойств стали. Неправильный отжиг, связанный с доступом воздуха в коробку, вызывал обезуглероживание поверхности, характерное «зернистым сложением на поверхности», которое создавало «особый кант белого цвета по краям бруска». Пережог брусков («повреждение стали») характеризовался «удобным разламыванием их без закалки». Хорошо отожженная сталь имела чистую поверхность без следов окалины, хорошую вязкость и «ровное крупнозернистое сложение в изломе».
По наблюдениям Аносова, части, соответствующие верху отлитой болванки, почти никогда не имели крупнозернистого строения, а следовательно, и узора — рисунка. Это обстоятельство позволило Аносову сделать заключе-ние, что ясность узора связана не только с кристаллическим строением, но и с чистотой стали. Аносов широко использовал отжиг не только на литых сталях, но и как предварительную операцию, отжигая сталь, идущую в шихту.
Применение отжига значительно повысило качество златоустовской стали, поставило ее выше лучшей английской тигельной стали. К тому же найденный Аносовым способ получения качественной стали был одного проще английского. «Подобного улучшения не было достигнуто в Англии помощью отжигания,— писал Аносов,— мне кажется потому, что тамошние мастера недовольно обращали внимание на изменения в стали при различных условиях отжигания, а приписывали улучшение ее более влиянию посторонних тел, при отжигании обыкновенно применяемых».
Здесь Аносов также поднимается выше своих современников — иностранных ученых, отдавая должное превращениям в самой стали, а не внешним факторам, например, влиянию засыпки и ее «магическому» действию.
Ироническое отношение Аносова к качеству английской стали и устаревшему с его точки зрения способу Гэнстмана — методу тигельной переплавки предварительно цементованной стали, очень хорошо выражено им в следующих словах: «Бритва из хорошего булата, без ошибок приготовленная, выбреет, по крайней мере, вдвое больше бород, нежели лучшая английская».
Четвертый метод — «сплавление железа «непосредственно с графитом, или соединение его прямо с углеродом» — Аносов считал наилучшим из всех разработанных им и экономически наиболее выгодным «к получений) настоящих булатов». Эту точку зрения разделяли и русские ученые. Один из современников Аносова — проф. П. П. Эйнбродт,— восхищенный его трудом «О булатах», в личном письме к нему подчеркивал значение четвертого способа, заявляя, что им исследователь «справедливо может гордиться».
Для четвертого метода Аносов разработал полную технологию. Эту интересную технологию мы приводим в сокращенном виде.
Плавка. В тигель загружали 12 фунтов (около 5 кг железа). Если же необходимо было получить более твердый металл, количество железа уменьшалось до 10 или 8 фунтов. Железо засыпалось смесью графита, железной окалины и флюса. В качестве флюса Аносов рекомендовал доломит.
После загрузки тигля его закрывали глиняной крышкой и пускали дутье для достижения «сильного жара». Дутье регулировалось «ртутным духомером». По истечении трех с половиной часов металл расплавлялся и покрывался тонким слоем шлака с плавающим в нем графитом, всплывшим частично в шлак.
Потери графита составляли за этот промежуток времени 100 г. После плавки в течение четырех с половиной часов они повышались до 200 г, а при плавке в течение пяти с половиной часов до 400 г. По окончании плавки тигель оставляли в печи до полного остывания. Затем отбивали крышку тигля, высыпали остатки графита, а шлак разбивали. Металл извлекался из тигля в форме «сплавка, имеющего вид хлебца» и при медленном охлаждении постепенно затвердевал.
Поверхность застывшего металла получалась либо ровной, либо с некоторым углублением около середины, «в котором кристаллы булата более видимы и между собой перепутаны». «Это,— говорил Аносов,— составляет усадку». Она была сильнее для более твердой стали. Отсутствие усадки свидетельствовало о том, что «усадочная раковина находится внутри», и показывало, что «такой булат скорее остывает снаружи, нежели внутри». Подобные слитки не ковались и давали плохой сорт булата. Такое совершенно правильное толкование явления усадки, насколько нам известно, было впервые отмечено также Аносовым.
От длительности плавки зависел характер рисунка стали. После плавки в течение трех с половиной часов металл имел слабые продольные узоры, светлый грунт. После плавки в течение четырех с половиной часов узоры на металле получались волнистые, средней величины. Наконец, после плавки в течение пяти с половиной часов, при хорошем качестве графита, металл выходил с крупными узорами,— сетчатыми, «а иногда и с коленами». Все это подтверждало точку зрения Аносова о влиянии углерода на характер и ясность рисунка.
«Наибольшее время плавки и медленное охлаждение тигля» служили гарантией качества стали.
Шихтовка описана Аносовым в «Журнале опытам по приготовлению литой стали и булатов с краткими замечаниями». Вот два примера шихтовки, взятые из этого журнала (табл. 1 и 2):
Первая страница «Журнала опытам по приготовлению литой стали и булатов» П.П. Аносова
Ковка. Ковка производилась тюд хвостовым молотом, весом в два с половиной пуда (40 кг). «Сплавок нагревался в горне до светлокрасного каления и укладывался под молот широким основанием. Проковка велась при слабом обжатии при поворотах «кругом в одну сторону». Промежуточные нагревы проводились пять-девять раз.
Чем медленнее проковывался булат, тем лучше было его качество. После ковки металл разрубали. Разрубленные части снова проковывались под молотом сначала в бруски, а затем в полосы. Лучшие булаты, несмотря на твердость, проковывались из брусков в полосы с двух нагревов.
При ковке тщательно соблюдалась температура нагрева, та «степень жара», при которой «узор не теряется». Сталь нельзя было перегреть. «Потеря узора во время ковки — есть порча металла».
Полосы имели неровности и плены, обтачивались и клеймились для обозначения нижней части, которая шла на изготовление лезвий. Чистовая ковка проводилась при малом нагреве не сильнее «мяснокрасного цвета».
Закалка. Операция нагрева и быстрого охлаждения стали называлась закалкой. Закаленная сталь обладала высокой твердостью, но вместе с тем и хрупкостью, «подобною стеклу». Для понижения хрупкости и для «сохранения, по возможности, твердости, приобретенной закалкой,— указывал Аносов,— искусство нашло средство в нагревании закаленной стали, но гораздо слабейшем, нежели при закалке». Далее он писал: «Предназначение изделия определяет меру нагревания, а появляющиеся на металле цветы (цветы побежалости) служат признаками для определения самой меры. Нагревание закаленной стали называется отпуском и главнейшие степени его по цветам суть: желтый, фиолетовый, синий и зеленый. Желтый цвет означает самую малую, а зеленый самую большую степень отпуска, при которой упругость металла начинает теряться».
Эти высказывания Аносова показывают, что он совершенно правильно определял понятие закалки и отпуска стали; также правильно характеризовал он свойства, изменяющиеся при отпуске.
Булаты закаливались в зависимости от назначения или в салё, или в воде, причем «самые твердые из них преимущественно в сале».
Аносов считал, что «оружие всякого рода достаточно закаливать в сале, «предварительно нагретом почти до точки кипения, ибо дознано из опытов, что в горячем сале закалка бывает тверже, в сем случае сало скорее ее охлаждает».
Таким образом, Аносов впервые дал метод закалки в «горячей среде» и объяснил ее действие.
Булаты закаливались путем нагрева откованного лезвия «докрасна» с последующим погружением в сало. После остывания лезвие обтиралось и для удобства наблюдения за цветами побежалости при отпуске зачищалось точильным камнем. Отпуск требовал большого искусства, так как нагрев производился «над углями» и при отпуске сабельного клинка различные части отпускались по-разному: у ручки — до зеленого цвета, у конца — до синего, в середине — до фиолетового, на месте «удара у лезвия» — до желтого. Отпущенный клинок «правился молотом и охлаждался в воде. Если же был необходим более упругий клинок, отпуск всего изделия проводился до синего цвета.
Аносов указывал также на возможность воздушной закалки тонких изделий «в быстрой струе воздуха».
Прсле закалки клинки подвергались точке и полировке. И для этой, казалось бы, простой операции Аносов дал ряд указаний, направленных на сохранение твердости. Он указывал, в частности, на недопустимость применения сухих точил, точение на которых вызывало нагрев и приводило к потере упругости; рекомендовал применять мокрые точила с соблюдением необходимых предосторожностей.
Впервые в истории металловедения Аносов описал и правильно объяснил также явление прижога закаленной стали при шлифовании.
Травление — «вытравка». Операция травления была необходима для выявления рисунка и определения качества булата. При разработке методов травления Аносов показал разное действие отдельных кислот.
Понятие о макроструктуре, как о показателе качества металла, выявление макроструктуры травлением, равно как и применение микроскопа для изучения макроструктуры как метода исследования, впервые были введены и Распространены Аносовым. Это — огромный вклад Аносова в металловедение.
Макроструктура булатной стали
Микроструктура булатной стали
Аносов дал также ясное описание строения стали, узоры которой похожи на виноградные гроздья, иногда расположенные рядами, сходные между собой. Правда, он не дал понятия о дендритах, позднее введенного Д. К. Черновым, но он наблюдал их, и его «виноградные грозды» дают точное описание дендритного (древовидного) строения стали. Этим он в известной мере предвосхитил дендритную теорию Д. К. Чернова.
К сожалению, до наших дней не сохранилось документального материала о макроструктурах сталей Аносова. Представление о макроструктуре и микроструктуре булатной стали дают фотографии начала нашего столетия, сделанные последователями Аносова.
Первый клинок из булатной стали был изготовлен Аносовым в 1837 г. Но об открытии Аносова еще долго не знали ни в России, ни заграницей. При состоянии связи того времени сведения с далекого Урала с трудом доходили до общественности столиц, а правительственные круги, преклонявшиеся перед английской литой сталью, которым было известно о блестящем успехе Ано: сова, его замалчивали. Не удивительно поэтому, что в то время, когда на одном конце России — на Урале секрета булата не стало, на другом — в Грузии попреж-нему считали искусство булатной стали тайной. Тайна закалки булата еще в 1838 г. служила средством для поэтических образов великому русскому поэту М. Ю. Лермонтову. Будучи в это время в ссылке на Кавказе, он по святил булату известные стихотворные строки:
Отделкой золотой блистает мой кинжал;
Клинок надежный, без порока;
Булат его хранит таинственный закал —
Наследье бранное Востока.
Сам Аносов, проводивший свои опыты с булатной сталью с исключительной научной тщательностью и с такой же тщательностью обобщавший их, не мог скоро-подытожить их результаты. На это у него ушло четыре года. И только в 1841 г., с появлением в печати его труда «О булатах», передовая общественность России широко заговорила об его открытии. «Сочинение Аносова «О булатах» возбудило общее внимание» — писала в июле 1841 г. газета «Мануфактурные и горнозаводские известия».
В октябре того же года «Горный журнал» заявлял: «Открытие способа приготовления булата, не уступающего качествами лучшим булатам азиатским, принадлежит, бесспорно, к числу важнейших открытий, которыми обогатилась наша промышленность в последние годы, и мы этим обязаны трудам Корпуса горных инженеров г-м. Аносова. Превосходные качества изделий, приготовленных из златоустовского булата, при необыкновенной дешевизне их, ручаются за прочность открытия».
Последний абзац труда П.П. Аносова «О булатах»
Изделия, изготовляемые из булатной стали Аносова, отличались высоким качеством. С ними не могли соперничать изделия, изготовленные из любой стали, известной в то время. Например, «шпажный клинок из хорошего булата, правильно выточенный и соответственно закаленный, как оказалось по моим опытам,— говорил сам Аносов,— не может быть при гнутье ни сломан, ни согнут до такой степени, чтобы потерять упругость; при обыкновенном гнутье он выскакивает и сохраняет прежний вид; при усиленном (например, будучи загнут под прямым углом) не сломается и, будучи выпрямлен, не потеряет прежней упругости. При этой связи в частях булатный клинок может быть тверже всякого другого, приготовленного из стали. Это и есть, без сомнения, предел совершенства в упругости, которая в стали не встречается».
Отмечая качества аносовской булатной пластинки, «Горный журнал» свидетельствовал: «она сгибалась без малейшего повреждения, издавала чистый и высокий звон. Отполированный и закаленный конец ее крошил лучшие английские зубила, тогда как отпущенный конец легко принимал впечатления и отсекался чисто и ровно».
Изделия из булатной стали демонстрировались на отечественных и зарубежных промышленных выставках и везде вызывали общее восхищение.
Обозреватели 3-й Московской мануфактурной выставки 1843 г. писали: «теперь Россия представляет единственный в целом мире источник нового булата лучших качеств. Булаты наши ценятся между азиатцами по крайней мере в десять раз дороже против здешней (московской Я. Б.) цены их. Сталь златоустовских заводов известна по отличному качеству вырабатываемого из нее белого оружия… Должно отдать справедливость их булатным кинжалам, которые оказались отличнейшего достоинства».
Иностранцы, поставленные Аносовым перед фактом, вынуждены были признать высокое качество его булатной стали, несмотря на свое скептическое отношение к русской промышленности. Рецензент английской газеты «Морнинг пост», обозревавший русское отделение на Лондонской всемирной выставке 1851 г. в отчете, составленном в довольно сдержанном тоне, все же отмечал, что «замечательный успех этой отрасли русской промышленности (выделка булатной стали И.Б.), без сомнения, относить можно высокому качеству употребляемой стали». «Было бы несправедливо,— заявлял он при этом,— не воздать должной почести и хвалы усердию, энергии и знаниям того ученого Корпуса инженеров (речь шла о П. П. Аносове И.Б.), на который возложено великое призвание распространять ремесленность и промышленность… в глубине лесов Урала и Алтая».
И в то же время иностранцы на русской службе пытались принизить роль Аносова в сталелитейном деле.
По случаю открытия Аносова перед Российской Академией наук был поставлен вопрос о присуждении ему Демидовской премии. Его способ производства булатной стали был передан на заключение академикам-иноземцам (непременный секретарь Фус и др.).
Чертежи устройства печей П.П. Аносова для производства булата
Не признать высоких качеств аносовских булатов было нельзя — они были слишком очевидны и слава о булатах шла далеко. Поэтому иностранцы на русской службе постарались запутать дело. Дав в общем высокую оценку булатной стали, они решили поставить под сомнение способ ее производства, разработанный Аносовым. В своем заключении эксперты заявляли: «Если бы в сочинении Аносова было указано, каким образом можно всегда с удачею изготовлять эту (булатную И. Б.) сталь, то не колеблясь должно было признать это открытие одним из полезнейших обогащений промышленности, и в особенности отечественной. Но в описании столь мало сказано о способе приготовления этого булата, что надобно думать, не представляет ли Аносов себе самому этой тайны, или может быть и ему самому только временем и случайно выдается изготовлять такую сталь…
При таковом положении дела академики не решаются представить Академии о присуждении Аносову демидовской награды за изобретение, которое не соде-лалось еще общим достоянием и о котором даже неизвестно, основано ли оно на приемах верных и доступных для всех и каждого».
Вопреки истине, вопреки тому, что Аносов дал вполне ясное представление о своем способе в сочинении «О булатах»,— Академия отклонила предложение о присуждении ему премии. Такое позорное событие могло иметь место только в условиях крепостнической, а позднее и капиталистической России, где раболепие правящих классов и низкопоклонство «официальной» науки перед иностранщиной не знало границ.
Однако ни общие условия того времени, ни отдельные реакционные попытки не могли подорвать значения открытия Аносова. Начатое им прогрессивное дело, знаменовавшее новый этап в развитии металлургии, упорро прокладывало себе путь вперед усилиями самого Аносова, а после него его последователями.
Материал взят из книги: Богачев, И.Н. П.П. Аносов и секрет булата // МАШГИЗ. — 1952. — 143 с.
zlatblog.ru
Дамасская сталь и грузинский булат. Загадка булатного узора
Дамасская сталь и грузинский булат
Дамаск — древнейший город на Ближнем Востоке. По преданию, его именовали «четвертым раем». На рынках города продавалось лучшее оружие, чеканка, самые дорогие ткани, редкостные пряности. В 284–305 годах римский император Диоклетиан повелел построить в Дамаске оружейные заводы. Это были уже не первые кузницы, где выковывалась узорчатая сталь.
Поскольку в древности оружие из индийского и сиамского железа делалось и продавалось чаше всего на базаре в Дамаске, очень трудно выяснить, какой булат делали в Дамаске, а какой в Индии. П. П. Аносов и другие историки металлургии различают старую настоящую индийскую сталь, которую называют еще «Дамаск» или «чистый Дамаск», и новую — «наварной дамаск» или «дамасскую сталь». «Чистый дамаск», так же как индийский «вутц» и древнеперсидский «пулад», являйся литой сталью. Клинок изготовляли из цельного куска такой стали, полученного плавкой. Он имел естественные узоры. Сегодня булатом называют литую сталь, имеющую естественный узор. Только оружие, полученное путем ковки литой булатной стали (лепешки, или «вутца») и имеющее естественные узоры, обладало очень высокими механическими свойствами. Именно о нем складывались легенды.
В древности, конечно, не могли знать о химическом составе булата и не умели связывать строение стали с ее свойствами. Следовательно, объяснить, почему тем или иным свойствам соответствует определенная форма булатного узора, никто не мог. Этим пользовались древние мастера. Чтобы дороже продать клинок, они стремились искусственно воспроизвести на нем узоры, свойственные хорошему булату.
Искусственные способы воспроизведения узора появились, очевидно, вначале в Дамаске. В этом городе производились знаменитые узорчатые ткани, которые еще и сейчас известны под названием «Дамаск» (во Франции — дамасье, в Голландии — дамаст). Советский исследователь А. К. Антейн не исключает возможности, что искусственную узорчатую сталь называли «дамасской» из-за сходства рисунка поверхности клинков с узорами дамасских тканей. Это подтверждается тем, что на западе до сих пор слово «дамаск» трактуют как «цветастая», или «сталь с цветным узором». Термин «дамасская сталь» получил настолько широкое распространение, что им еще и в наше время иногда неправильно называют настоящие индийские булаты. Между тем искусственный узор дамасской стали отличить от естественного булатного сравнительно нетрудно. Рисунок на дамасской стали повторяется в соседних фрагментах, как на обоях, а линии узора короче и постоянны по толщине. Встречаются простые и сложные узоры. Последние представляют собой глазки или агатовидные фигуры, состоящие из ряда замкнутых концентрических линий, напоминающих лучшие сорта литого булата (фото 1).
Существовало много способов изготовления узорчатых клинков. Например, скручивали в виде каната полосы или куски проволоки, имеющие различное содержание углерода и потому разную твердость. Такая «плетенка» проковывалась, а точнее, сваривалась под молотом после нагревания. Поскольку куски были разного состава, на клинке при травлении проявлялся узор. Варьируя способы сплетения проволоки или полос, можно было получить различные узоры на поверхности клинка.
Оружие, приготовленное этим и подобными способами, и получило название «дамасская сталь», или «наварной дамаск». Последнее время «наварной дамаск» чаще всего называют сварочным булатом. Настоящий сварочный булат отличался особенно красивым, строго повторяющимся по длине клинка, цветным извилистым узором.
Есть предположение, что способ изготовления сварочного булата мог возникнуть случайно: из-за отсутствия нового материала мастера часто сваривали старые куски железа. Это со временем и могло привести к способу получения сварных клинков.
Изобретатели холодного оружия из сварочного булата быстро обнаружили, что, хотя его качество и уступает оружию из настоящего булата, но является несравненно более высоким, чем качество клинков из обычной стали. Поэтому ножи, кинжалы и сабли из сварочного булата также ценились очень высоко. Есть сведения, что в XVIII–XIX веках сабельный клинок из сварочной дамасской стали в Хоросане стоил огромных денег — 7000–8500 имперских талеров.
Некоторые способы изготовления клинков из сварочного булата появились еще в глубокой древности. Во всяком случае они восходят к эпохе поздней Римской империи. В 1859–1863 годах около селения Нидам (Дания) вблизи побережья Альзензунда в торфяниках были обнаружены три римских корабля с грузом. Корабли, очевидно, потерпели крушение во время бури. Два из них затонули, а третий сел на песчаную отмель. Среди корабельного груза оказалось свыше ста мечей, утварь и монеты. На мечах были обнаружены римские пометки, монеты оказались динарами, выпущенными в III веке.
Исследование металла клинков мечей показало, что они имеют структуру сварочного булата, изготовленного старинными способами «наварного Дамаска». Известны три разновидности этого способа, которые отличают по узорам на клинке: полосатый дамаск, наварной дамаск и цветочный дамаск. Цветочный называют также «розовым Дамаском».
Полосатый дамаск изготовляли простой сваркой разных по твердости стальных полос, наложенных друг на друга, причем полосы с большим содержанием углерода чередовались с полосами, содержащими очень мало углерода. Угловой дамаск делали следующим образом. Брали полосу полосатого Дамаска, нагревали и скручивали под молотом, после чего сплющивали и вновь вытягивали в полосу. К полученной полосе приваривали такую же полосу, но скрученную в противоположную сторону. В результате получали рисунок, напоминающий угольник или римскую букву V, посередине которой хорошо была видна осевая линия. Сваркой двух V-образных полос получали рисунок, напоминающий букву W. К методам получения розового Дамаска мы еще вернемся.
На проржавевших обломках найденных мечей обнаружили рисунки всех перечисленных видов сварочного Дамаска. Интересно, что после того, как сняли ржавчину и просмотрели структуру поперечного сечения мечей, обнаружили, что рисунок («дамасское переплетение») не проходит через всю массу металла. При исследовании прежде всего бросалась в глаза разница структуры дамаска на одной стороне клинка и на другой. После шлифовки, полировки и протравки кислотой поперечного сечения клинков на них появились темные прослойки — это были твердые куски стали с высоким содержанием углерода. Они были умышленно вварены в мягкую основу. Из этого следует, что при выработке мечей сначала ковался остов, а затем на него с двух сторон насаживались прокованные дамасские полосы.
Лезвия у мечей были гладкие, без рисунка, следовательно, они приваривались отдельно. На отдельных мечах лезвие представляло собой сваренные полоски углеродистой стали и Дамаска. Таким образом, все найденные мечи отличались по качеству и структуре (рисунку) железа, использованного для лезвия и тела меча.
Химическим анализом металла римских мечей обнаружено следующее содержание элементов в стали (в процентах): углерод — 0,6; кремний — 0,15; марганец — 0,363; фосфор — 0,054 и сера — 0,073. Содержание углерода от оси меча к лезвию увеличивалось.
Известны и другие способы приготовления сварочного булата. Один из них заключался в том, что полосу сваривали из 20 слоев более твердой и более мягкой стали, расположенных различным образом в зависимости от цели употребления изделия, после чего полосу перегибали и сваривали вторично 40 слоев, еще перегибали и сваривали 80 слоев, еще раз перегибали и сваривали 160 слоев, и еще раз перегибали и сваривали 320 слоев! После вытяжки из нее делали заготовки для клинка. Если такой клинок нагреть и быстро охладить, то более твердые стальные слои становятся отчетливо видны на поверхности мягкого железа, образуя характерный древовидный рисунок, Специальной ковкой, последующей шлифовкой и травкой добивались «коленчатого» узора.
В более поздние времена из сварочных булатов на Востоке особенно ценился амузгинский, представлявший собой крупнорисунчатую дамасскую сталь. Клинок изготовляли следующим образом. Брали три пластины: одну из среднеуглеродистой «крепкой» стали, так называемой «антушки», вторую — из низкоуглеродистой и «мягкой» стали («дугалалы») и третью — из высокоуглеродистой «очень крепкой» стали («альхана»). Из каждой пластины вначале выковывались тонкие полосы, после чего они сваривались. Обычно из сварочных полос выковывали четырехгранный стальной стержень, который затем вытягивался и уплощался. Из такой заготовки выходило два клинка.
Анализом способов изготовления клинков мечей из дамасской стали и узоров сварочного булата занимались многие известные металлурги у нас в стране и за рубежом. А. К. Антейн и А. Льестол (на которого Антейн ссылался в своей работе) провели широкое исследование узоров мечей из дамасской стали путем моделирования способа их приготовления на пластилине и пластинах из мягкой и твердой сталей.
Методика моделирования состоит в следующем: сначала берут три (или больше) стальные пластинки (черный пластилин), между ними прокладывают две железные пластинки (белый пластилин) такой же толщины. После этого с внешних сторон помещают две железные пластины потолще. Срезая лишний пластилин, блоку придают цилиндрическую форму и скручивают его несколько раз вокруг продольной оси. Разрезы на разных расстояниях от центра дают узоры различных видов.
Если такой крученый брусок разрезать по осевой линии, получается крестовидный узор; если разрезать ближе к краю — узор из косых линий. Из таких линий легко сделать V и W — образные узоры. Разрезы между указанными выше плоскостями дают промежуточные узоры. Один из промежуточных разрезов позволяет получить узор в виде розы: для этого сваривают два крученых прутика с полукруглыми узорами так, чтобы из двух полукругов разных прутиков получился один круг. Подобные узоры получены также на железе и стали методом ковки и скручивания (рис. 1).
Холодное оружие из дамасской стали, дошедшее до наших дней, свидетельствует о том, что в древности существовали два способа использования сварочного булата при изготовлении клинков. Первый состоял в том, что вся средняя часть клинка изготовлялась из сварочного булата, а к ней приваривалось лезвие из углеродистой стали (0,6–0,8 % углерода). При втором способе слой сварочного булата наваривался на основной металл клинка поверх дола. Клинки, сделанные по первому способу, старше. Они, как правило, относятся к IX–XI векам.
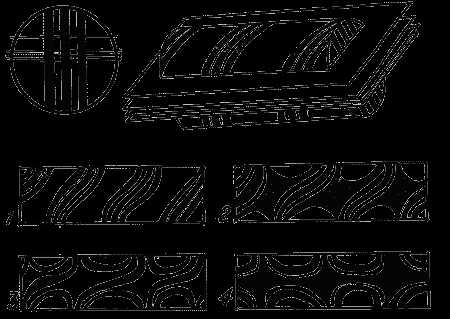
Рис. 1. Схема получения узоров сварочного булата на модели блока из трех пластин.
Вплоть до конца XIV века в Дамаске изготовляли лучшее оружие в мире. В 1370 году в Самарканде к власти пришел великий эмир Тимур. Для того чтобы упрочить свою власть и удержать феодалов и кочевую знать от внутренних мятежей и междоусобиц, он начал большие завоевательные войны. В начале XV века (1401 год) Тимур покорил Сирию и взял Дамаск. Город был сожжен, а мастера, владеющие искусством изготовления оружия, были увезены в Самарканд. В этот и другие города Средней Азии переселялись десятки тысяч ремесленников из завоеванных стран.
Чтобы подорвать военную мощь Золотой Орды, Тимур старался ликвидировать ее транзитную торговлю. Он разрушил такие большие города, как Сарай-Берке, Астрахань, Азов, а также Ургенч. В результате вся средиземноморско-азиатская торговля направлялась только по караванным путям, проходившим через Иран, Турцию, Армению, Грузию, Бухару, Самарканд. С этого времени начинается широкое распространение разнообразных способов изготовления сварочного булата в Средней Азии, на Кавказе и особенно в Турции.
Поскольку донские казаки постоянно участвовали в русско-турецких войнах, их оружие претерпевало «естественный» отбор: в их вооружении оказывались наиболее стойкие сабли и шашки. В джигитовках и состязаниях выявлялись не только боевые качества всадников, но и крепость булата. Советские металлурги О. Жолондковский и И. Ильчук пишут, что на Кубани и Тереке арсенал казаков представлял такую оригинальную мозаику, такую смесь оружия всех времен и стилей, что специалисты могли только диву даваться. Часть этого оружия из литого турецкого шама, дамасского сварочного булата и лучших сортов дамаскированной стали и ныне можно увидеть в Новочеркасском музее истории донского казачества и других музеях страны.
Основное количество сабель было отбито казаками у горцев. Это оружие изготовлено прославленными мастерами Кавказа — из местечка Кубачи, знаменитыми братьями-оружейниками Исди-Кардаш, кинжальных дел мастером Магометом Муртазалиевым.
Очень ценились уникальные шашки терс-маймуны и калдыны, называемые иногда волчками. Калдын — широкий почти прямой клинок с изображением волка на одной его стороне и круга с крестом — на другой. Терс-маймун очень похож на калдын, но бегущий зверь изображен схематично, а кресты на клинке дополняются лагинскими буквами NМ, обозначающими, по-видимому, либо название местности, либо имя изготовителя. Точных сведений о происхождении этих клинков до сих пор нет.
Лучшей на Кавказе считалась шашка гурда. С ней можно было вступать в бой с противником, закованным в латы. О сказочных качествах гурды красноречиво рассказывает старинная легенда: «Один горец научился ковать чудо-шашку. Но вот прослышал он, что живет на свете другой такой же мастер. Захотелось ему испытать, чей клинок крепче. Встретились кузнецы, выхватил шашки. «Смотри, «гурда», — крикнул первый, — и ударил по шашке соперника. Перерубил булат, а вместе с ним и мастера». Гурда до нас дошла лишь в отдельных экземплярах и сегодня является музейной редкостью.
Не меньшей славой пользовалось оружие старого Калмыцкого мастера Басалая и его многочисленных потомков в Дагестане. Изготовленные ими кинжалы так и назывались «басалаи». Утверждали, что их лезвием можно было высечь из камня искру, а потом побриться.
Необычный сварочный булат найден в прибалтийском бассейне. На лезвие средневековых мечей выводили не твердую стальную, а мягкую полоску железа и только после нее делали твердое острие. Долго металлурги не могли понять, зачем это делалось… Объяснение такой конструкции средневековых мечей дал профессор из Владимирского политехнического института Г. П. Иванов.
Однажды адмирал С. О. Макаров присутствовал на полигоне при испытании броневых плит, цементованых и закаленных по методу Гарвея. Плиты эти на поверхности имели большое содержание углерода, и после закалки поверхность плиты приобретала высокую твердость. Однако по мере углубления содержание углерода уменьшалось, и материал становился мягче и мягче.
При испытаниях по недосмотру одну из броневых плит установили к орудию обратной, мягкой стороной. Началась стрельба, и снаряды без труда пробивали плиту, считавшуюся неуязвимой. Случай этот произошел на глазах у многих специалистов, но правильный вывод сделал только адмирал Макаров.
«Если закаленную поверхность плиты легко пробить обратной стороны, — подумал адмирал, — то нельзя ли эту самую «изнанку» насадить на головную часть снаряда?» «Макаровские» мягкие колпачки на броневых снарядах насквозь прошивали гарвеевскую броню… Так для того ли, чтобы пробивать стальные латы противника древние кузнецы нашивали мягкую полоску стали на закаленное очень твердое лезвие средневекового меча?
Широко известен грузинский сварочный булат. По мнению П. П. Аносова, он близок к индийскому и дамасскому. Павел Петрович считал, что лучшие сварочные булаты делали в Индии, Турции, Сирии и Персии (Иране). Их, возможно, начинали готовить мастера, знакомые с выделкой настоящего литого булата. Традиции приготовления булата в Грузии были непосредственно связаны с производством оружия в Индии и странах Ближнего Востока.
Как уже было отмечено, холодное оружие делали главным образом в горной части Грузии, но сварочный булат умели делать лишь в нескольких городах. Оружие тифлисского производства славилось далеко за пределами Кавказа. Есть сведения, что в XVIII веке горским народам Кавказа и Ирана сабли и кинжалы поставлялись из Тифлиса. В XIX веке Тифлис продолжает оставаться центром изготовления оружия из сварочного булата. Это хорошо известно А. С. Пушкину, который писал, что тифлисское оружие дорого ценится на всем Востоке.
Десятилетия славилась своим булатом семья Элиазарошвили. Исследователь истории производства стали в Грузии К. К. Чолокашвили установил, «что эта семья секрет изготовления булата унаследовала от предков». Но собенно популярным был мастер булатного оружия Георгий Элиазарошвили, которого упоминает даже М. Ю. Лермонтов в одном из вариантов стихотворения «Поэт»:
В серебряных ножнах блистает мой кинжал,
Геурга старого изделье.
Булат его хранит таинственный закал,
Для нас давно утраченное зелье.
Сын Георгия — Карамон Элиазарошвили продолжил дело отца. Он знал, что в былые времена грузинские мастера изготовляли булатные клинки из индийского железа — вутца. Карамон объясняет: «Вутц — слиток стали в виде толстой лепешки. Одни полагали, что это смесь стали и железа, другие — железа и чистого графита, а третьи — что это «особая сталь».
Но вутца давным-давно нет, и Карамон Элиазарошвили делает булатное оружие из грузинских подков, опилок из турецкой стали, чугуна и полос сварочного железа. «Се же оружие из грузинского булата обладало столь высоким качеством, что при испытании клинков ими отсекали одним ударом голову быка или коровы.» Правда, как правильно заметил П. П. Аносов, для такой работы, кроме качества клинка, еще требовалась сила его обладателя…
Известный историк кавказских походов русский генерал В. Патто писал в XIX столетии: «Безусловно, русские кавалеристы за счет своей отваги и богатырской силы успешно противостоят восточным конникам, но крепость и острота ятаганов и шашек, сделанных из дамасской стали, значительно превосходят крепость сабель наших солдат. Для того чтобы успешно владеть настоящим булатным клинком, не нужна особая физическая сила он страшен даже в руках ребенка».
Итак, к началу XIX века русская армия, считавшая одной из сильнейших в мире, не имела на вооружении хороших клинков. Необходимо было обратить серьезное внимание на производство холодного оружия в России. Начальник оружейных заводов и министр финансов Е. Ф. Канкрин поручил организовать изготовление булатных клинков. Обратились к Элиазарошвили, искусство которого было широко известно. Сохранились сведения, что Карамон Элиазарошвили в 1828 году раскрыл рецепт изготовления грузинской сабельной стали. К. К. Чолокашвили нашел этот рецепт в старых «Актах Кавказской архивной компании». Позволю себе привести его целиком — из этого описания даже неспециалисту ясно, как непрост был метод.
«Для одной сабли или шашки взять 5 фунтов полосового железа, положить в кузнечный горн, в котором довести его до такой степени (т. е. раскалить), чтобы можно было разрубить на три части по длине полосы, после чего перерубить каждую часть на два куска, из чего образуется 6 равных частей, длиною каждая в четверть аршина. Потом взять два фунта стали, вываренной и, сырцовой, положить также в ковш, раскалив ее так, что бы можно было разрубить оную на три части по длине полосы, равные по величине железным частям.
Затем, взяв два куска означенного выше железа, вложив в них один кусок прописанной стали, сварить песком и обыкновенным порядком тоже с прочими железными частями и сталью. Когда таким образом железо со сталью сварено, должно выковать сваренный кусок длиною вдвое, т. е. в пол-аршина, шириною в три четверти вершка и толщиною в одну восьмую вершка. Потом каждый сей кусок, раскалив в горне, обсыпать сверху и снизу посредством железной лопатки, толченым чугуном (который должен быть приготовлен наперед подобно песку). Всего же потребно чугуна из 6 кусков, означеного выше железа один фунт. После сего выковать вновь каждый кусок вдвое, т. е. в один аршин длиною, шириною в полвершка. Окончив, согнуть каждый кусок 5 раз взяв оные в клещи, сварить вместе в горне с песком; потом, вытянув посредством кожи из сего материала прут длиною в пол-аршина, перерубить на две части, сварить оный с песком и, вытянув из него вновь пол-аршина, перерубить пополам. После сего вложить в середину оных полуфунтовую полосу стали, длиною и шириною подобно сим кускам перерубленного железа, сварить с песком вместе, выковать полосу, подобную сабле, но, однако, короче двумя вершками. Сию полосу должно насечь зубилом с обеих сторон, подобно крупному напильнику, потом насечку сию сточить или спилить и тогда вытянуть о произволу саблю или шашку, после чего положить в клинок, а через четверть часа, вынув и вычистив в одном каком-нибудь месте пыль, смотреть, если струя на нем кажется хороша или по желанию, тогда вычистить тем же самым из пыли порошком и употреблять».
Известно, что в 30-е годы XIX века в Тифлис были направлены русские ученики. В 1832 году Элиазарошвили ссылает с ними императору Николаю I сабли своего изготовления. Это оружие сейчас хранится в Эрмитаже в Ленинграде и в Историческом музее в Москве. К. К. Чолокашвили приводит также архивные документы 1888 года, в которых указывается, что «лучшими клинками в кавалерии считались те, которые были изготовлены учениками Элиазарошвили».
Рецепт Элиазарошвили весьма похож на сохранившиеся описания производства мечей в Северной Индии с искусственно науглероженной поверхностью. Полосу обычного кричного железа многократно обсыпали чугунными опилками, а затем последующей многократной проковкой при «сварочном жаре» создавали на ней нацементованную поверхность. Такие клинки обладали острым лезвием, имели некоторую продольную упругость и вязкость. Они уступали по качеству только булату…
Приведенные сведения о сварочном булате — наиболее поздние. К концу XIX века в мире уже почти не делали холодное оружие из сварочного булата. Секрет его производства был вскоре окончательно утерян. Интересно, что в эти времена и в Индии, и в Дамаске изготовляли холодное оружие из обычных сортов английской или шведской стали.
Производство сварочного булата было самостоятельным промыслом со своими секретами и традициями. Очень трудно сварить полосы или проволоки разнородной стали в один цельный кусок, получить определенный узор, да еще обеспечить твердость, гибкость и остроту выкованному клинку. Дело в том, что после нагрева в горне полосы стали или проволоки поверхность металла окисляется, и пленка окислов препятствует его сварке. Чтобы сварка происходила, надо очень точно выдерживать температуру и удалять окислы с поверхности стали. Способы удаления окислов, температура сварки, скорость ковки, порядок соединения полос с различным содержанием углерода и составляли, очевидно, главные секреты мастеров, делавших оружие из сварочного булата.
Недаром в имеющихся описаниях изготовления амизгинского сварочного Дамаска обычно говорится, что, когда наступала пора сваривать пластины, мастер выгонял всех из кузницы, тщательно оберегая тайну порядка соединения пластин и способа их сварки. Если же мастер допускал посторонних, то применял такие приемы, которые отвлекали любопытных: совершал над полосой самые необыкновенные ритуалы, например, посыпал полосу пеплом заживо сожженного животного или другими неведомыми опилками и порошками. Между тем главный предмет тайны составляли, по всей вероятности, порошки, которые применялись для сварки в качестве флюсов.
Теперь совершенно понятно, что это были флюсы, которые, с одной стороны, имели достаточно низкую температуру плавления, были жидкотекучи и легко выдавливались под молотом, а с другой — быстро растворяли окислы железа, обнажая чистую поверхность металла, необходимую для сварки. Мастера использовали разные флюсующие порошки, но каждый свято хранил в секрете состав «камней», им применяемый. Поэтому, возможно, и в рецепте Элиазарошвили нет самого главного — состава флюса для сварки полос. Мастер подробнейшим образом рассказывает о порядке сварки полос, а флюс упоминает между прочим, называет его песком, не открывая секрета его состава и способа приготовления.
В Западной Европе до XV–XVI веков не знали о существовании литого булата. Поэтому возникающие здесь центры по изготовлению холодного оружия старались использовать секреты сварочного булата. Так, пример, испанские оружейники заимствовали приемы производства дамасской стали у арабов, живших на Пиренейском полуострове. В Толедо, который стал одним центров производства холодного оружия, впоследствии делали высококачественные клинки из обычной стали. Чтобы рекламировать их высокое качество, на поверхности клинка литографическим способом наносили дамасский узор. Такие клинки специалисты называют «ложными булатами».
Особенно широко развернулось производство подделок под булат в XVIII–XIX веках. В это время в Европе научились производить высокоуглеродистую литую сталь, и западноевропейские мастера, оставив попытки раскрыть секреты производства сварочного булата, начали изготовлять из нее довольно хорошее холодное оружие. В Италии (Милан), в Испании (Толедо), в Германии (Золинген), во Франции и Бельгии (Льеж), даже в Англии стали широко производить «ложный булат».
«Ложные булаты», особенно золингеновские и толедские, приобрели известность благодаря высокой степени полировки и красивым узорам, которые наносились на клинки различными методами. Ремесленники, рисующие декоративные узоры на металле, назывались «дамаскировщиками», а клинки «ложного булата» — «дамаскированными». Многие «дамаскированные» клинки были не очень высокого качества, поскольку они изготовлялись из обычной шведской или английской углеродистой стали. Поверхность металла полировали, тщательно очищали от грязи и покрывали раствором специального состава в терпентиновом масле. Узоры булата выводили кистью или резцом, а потом протравливали рисунок соляной кислотой. Особенно преуспевали мастеровые из немецкого городка Клименталя: они получали узоры на клинках не только описанным способом, но часто его просто гравировали.
Сходство рисунков на литом булате, сварочном булате и «дамаскированной» стали нередко приводило ко всяким недоразумениям. В частности, описание личного оружия Вильгельма I, Бисмарка и Наполеона сделано таким образом, что совершенно непонятно — то ли оно изготовлено из сварочного булата, то ли из «дамаскированной» стали.
В Новочеркасске в музее истории донского казачества экспонируется сабля атамана М. И. Платова. Сабля сделана в 1814 году из лучшей английской стали в честь победы союзников в войне с Наполеоном Бонапартом. Сабля еще до Октябрьской революции была передана в музей родственниками Платова; но во время гражданской войны была украдена белогвардейцами и вывезена в Чехословакию, откуда в 1946 году со многими экспонатами старинного оружия возвращена на родину.
На клинке сабли надпись, свидетельствующая о том, что Лондонский городской совет, заседавший 8 июня 1814 г., единогласно решает: «Сабля стоимостью 200 гиней преподносится атаману графу Платову в знак высокого уважения, которое совет питает к непревзойденному мастерству, блестящим талантам и неустрашимому мужеству, проявленному им во время длительных конфликтов, в которых он принимал участие для обеспечения свободы, мира и счастья Европы».
Есть сведения, что аналогичные сабли были преподнесены русскому полководцу М. Б. Барклаю-де-Толли и командующим союзными войсками Артуру Уэлсли Веллингтону и Герберту Лебрехту Блюхеру. Несмотря на высокую стоимость, сабля представляет собой всего лишь неплохой образец «дамаскированной» стали. На ее поверхности выгравирован рисунок, похожий на булатный узор. Подобных образцов в музеях можно найти немало, гораздо больше, чем настоящих сварочных булатов.
В нашей стране многие секреты сварочного булата стали известны благодаря работам грузинского ученого-этнографа К. К. Чолокашвили, который расшифровал ряд способов его производства. Найденный рецепт изготовления грузинского булата был им передан в Институт металлургии Академии наук Грузинской ССР, где был тщательно изучен. В результате в одном из цехов Руставского металлургического завода под руководством академика АН Грузинской ССР Ф. Тавадзе в современных условиях были получены опытные образцы сварочного булата, достаточно хорошо повторяющие узоры и свойства музейных экспонатов.
Как мы уже неоднократно замечали, в сварочном булате чередуются участки пластичного мягкого (низкоуглеродистого) железа и сравнительно твердой (углеродистой) стали — такие клинки обладали гораздо более высокой упругостью и вязкостью по сравнению с клинками из обычной углеродистой стали. А вот почему именно сварочный булат отличался высокой прочностью и дамасские сабли были значительно тверже и крепче других стальных сабель, долгое время оставалось загадкой. Лишь современная наука о металлах смогла это объяснить. Но прежде чем привести это объяснение, сделаем небольшую экскурсию в физику металлов.
В 1784 году монах Р. Гаюи выдвинул гипотезу, что кристаллы состоят из совершенно одинаковых «кирпичиков» постоянной формы.
Через 130 лет с помощью рентгеноструктурного анализа было выяснено, что металлы имеют такое же кристаллическое строение, как и минералы. Атомы металлов располагаются в пространстве определенным образом, образуя кристаллическую решетку. Кристаллическая решетка складывается из элементарных кристаллических ячеек. Кристаллической ячейкой удобно изображать расположение атомов в кристалле. Например, в кубической объемно-центрированной решетке 8 атомов расположены в каждой из вершин куба и один — на пересечении его пространственных диагоналей. В идеальной кристаллической решетке все узлы заполнены атомами, вернее, ионами, а в междоузлиях расположен только электронный газ.
Прочность металлов определяется их атомно-кристаллической структурой. В 1926 году выдающийся советский физик Я. И. Френкель подсчитал, что прочность реальных металлов во много раз меньше теоретической. В чем же дело? Физики немало лет ломали голову над этим вопросом. Оказалось, что реальные металлические изделия состоят из большого числа кристаллов, которые имеют разную ориентацию кристаллической решетки, В таком поликристаллическом агрегате кристаллы принимают неправильную форму — их называют зернами или кристаллитами. Кусок металла, представляющий собой один кристалл, называют монокристаллом.
В отличие от строения монокристалла строение кристаллитов несовершенно, в частности из-за наличия незанятых мест в узлах кристаллической решетки — атомных «дырок», называемых вакансиями. Недостатком кристаллитов являются и дислокации. Дислокацией, буквально — смещением, в геологии называют нарушение первоначального залегания пластов земной коры, в результате которых образуется складка или сдвиг. В кристаллической решетке дислокация — это также смещение или сдвиг, приводящий к образованию лишнего ряда атомов. Дислокация образует в кристаллической решетке «лишнюю» неполную плоскость или полуплоскость, которая получила название экстраплоскости.
Многочисленные экстраплоскости не проходят через все сечение кристалла, они обрываются внутри него. Экстраплоскость образует линейный дефект решетки — краевую дислокацию. Краевая дислокация может простираться в длину на многие тысячи ячеек решетки, может быть прямой, а может, как нитка, выгибаться в ту или другую сторону. В пределе она может закрутиться в спираль, образуя винтовую дислокацию. Вокруг дислокации возникает зона упругого искажения решетки, вызванная отталкиванием дислоцированных (внедренных в междоузлия) атомов экстраплоскости.
Помните, дислокация — это «складка»? Теперь представьте себе, что нужно передвинуть по полу ковер. Тащить его за край довольно тяжело. Сделайте на ковре складку, и вы значительно облегчите его передвижение. Если ковер передвигать по полу постепенно, по мере волнообразного передвижения складки, то для его движения потребуется совсем немного усилий. В металле дислокации играют роль примерно таких же «складок». Вследствие искажения решетки в районе дислокации последняя под действием небольших напряжений легко смещается, и дислоцированные атомы занимают положенное им место в узлах кристаллической решетки. Но вслед за ними смещается соседняя плоскость атомов, занимая место дислоцированных, то есть превращаясь в экстраплоскость и вновь образуя краевую дислокацию.
Что же заставляет дислокацию перемещаться? Оказывается, ее «толкают» атомы, расположенные непосредственно за ней. У них в результате искажения решетки появляется избыточная энергия, и чтобы избавиться от нее и занять новое стабильное положение, они сталкивают дислокацию на новое место. Поскольку дислокация испытывает давление с обеих сторон, суммарное воздействие на нее равно нулю. Поэтому «толкачи» начинают работать лишь тогда, когда они сами испытывают давление от внешних сил.
Таким образом, дислокации могут сравнительно легко перемещаться под действием небольших напряжений. Это значит, что реальные металлы и сплавы деформируются постепенно за счет небольших смещений атомных слоев в области дислокации. Говорят, что движение дислокации напоминает движение гусеницы. При движении лишь у ограниченного количества атомов нарушаются связи.
Механизм деформации идеального кристалла состоит в сдвиге одних атомных плоскостей относительно других. Для такого сдвига требуются значительные усилия — этим и объясняется высокая теоретическая прочность монокристаллов по сравнению с поликристаллами реальных металлов и сплавов.
Пока под влиянием приложенной к металлу силы движутся дислокации, сопротивление металла деформации невелико. Раз так, то и прочность металла небольшая. А если движение дислокации затруднено, если поставленный им заслон вообще мешает им перемещаться? Скажется ли это на прочности металла? Да, конечно, металл в этом случае будет тяжелее поддаваться деформации, и прочность его возрастет. Следовательно, для повышении прочности металла необходимо либо устранить дислокации вообще, либо повысить сопротивление их перемещению.
При деформации дислокации движутся подобно нитке — они способны изгибаться, цепляться за препятствия, образовывать клубки и даже уничтожать друг друга. В клубках плотность дислокации достигает значительной величины, им становится очень трудно перемещаться. Значит, образование клубков дислокации приводит к упрочнению металла или сплава.
Но где взять ту преграду, которая остановит движение дислокации? Оказывается, такое препятствие можно найти, и даже не одно. Существует несколько способов торможения дислокации. Один из них — уменьшение размеров зерен. Границы зерна являются препятствиями для перемещения дислокации. Добавление в кристаллическую решетку атомов других элементов также приводит к торможению дислокации. Чужеродные атомы окружают дефекты, блокируют их, не дают возможности дислокациям перемещаться. Теперь хорошо известно, что легированне стали хромом, вольфрамом, марганцем, ванадием и другими легирующими элементами значительно повышает ее прочность. Прочность легированной стали намного выше прочности булата.
Препятствием для перемещения дислокации являются также любые искажения кристаллической решетки и «инородные» включения, соизмеримые с кристаллическими ячейками. В качестве таких упрочнителем применяют высокодисперсные карбиды, нитриды, окислы, интерметаллиды. Стали и сплавы, изготовленные таким образом, обладают чрезвычайно высокой прочностью. Самый простой способ упрочнения металла — это пластическая деформация. С увеличением степени деформации растет количество дислокации и уменьшается их подвижность. Это приводит к увеличению плотности дислокации.
Итак, прочность металла повышается в двух случаях: когда в кристаллической решетке совершенно нет дефектов или когда плотность дислокации достаточно большая. Конечно, увеличение плотности дислокации ведет к упрочнению металла до определенного предела. При слишком большой плотности дислокации образуются микроскопические трещины и металл разрушается.
Так вот, сварочный булат отличался высокой прочностью, значительно превышающей прочность стали такого же состава, потому что степень деформации при сварке стальных полос или проволоки с различным содержанием углерода была колоссальной. Не так давно металловеды сделали рентгеноструктурный анализ сварочного булата. Рентгенограммы показали, что из кристаллов металла выпали чуть ли не целые группы атомов — так велика у него оказалась плотность дислокации. Таким образом, древние кузнецы эмпирически нашли способ приготовления очень прочного оружия. И не случайно сварочный булат (дамасская сталь) ценился не только за свои красивые цветные узоры.
Поделитесь на страничкеСледующая глава >
tech.wikireading.ru
Булатная броня — что это такое? Булатная сталь: характеристики. Тайна древнего булата
Новости и общество 7 января 2015Рождается сверкающий булат
Из мягкого железа, твёрдой стали.
И крепче меч становится стократ,
И на клинке — узорные спирали.
(Александр Симонов, «Булатный меч»)
Родом из сказки
Всем известно, что сказки — это не просто интересные истории, которыми можно занять детишек, но и кладезь мудрости, сплетающей хитрый узор с историческими событиями и былинами.
В сказках о могучих богатырях и благородных рыцарях частенько встречается такой термин, как «булатная броня». Самые сильные и смелые герои совершали свои подвиги с оружием из булатной стали. Что же это за металл такой? Чем он так хорош? Почему так дорого стоил и был столь ценен? И вообще, булатная броня — что это? Доспехи, щит, забрало? А может, этот металл — секретная разработка канувших в Лету кузнецов, эксперимент инопланетян или дар свыше?
Существует ли в наше время и ценится ли так, как в древности, булатная броня? Значение слова «булат», происхождение и использование этого металла описаны в данной статье. Мы раскроем все секреты поистине сказочной стали, которая на самом деле вполне реальна.
Оружие прославленных героев
Булатная броня — это устаревшее название холодного оружия. И вовсе не доспехов, как может показаться на первый взгляд. Для сравнения: аналоги слова «броня» в языках-побратимах польском (bron) и чешском (zbrane) означают именно оружие из стали, такое как булатный клинок, меч, нож, кинжал или сабля.
Такие известные сказочные персонажи, как богатыри Илья Муромец и Добрыня Никитич, король Артур и Святогор, обладали несокрушимым оружием из булатной стали, благодаря которому считались непобедимыми воинами. Значение слова «булат» простое — это упрочнённая сталь.
Тайна из космоса
Тайна древнего булата кроется в далёком прошлом, а точнее в 1421 году, когда на Землю близ русского города Ярославля упал железный метеорит. Огромный кусок металла, обрушившийся с неба, считался даром богов и расходовался только на уникальное оружие. Доступ к внеземному металлу имели лишь немногие именитые кузнецы, а клинки и ножи из булатной стали ковались для избранных воинов.
Легендарная уникальность
Мечи, выкованные из обычного железа, ломались и гнулись после первых 2-3 ударов, булатные же служили вечно. Ими можно было легко перерубить железный щит или распороть кольчугу врага. Удивительно и то, что, несмотря на свою невероятную прочность, булатные клинки были очень упругими и сгибались на 90-120 градусов, не теряя своей целостности. Таким образом, простое холодное оружие врага в бою если не тупилось, то разлеталось на куски, как разбитое стекло, в то время как булатная броня оставалась целой и острой. Если верить легенде, за булатный меч давали столько золота, сколько весил клинок, а весил он немало!
Сказочный металл
Несмотря на то что метеорит был велик, а кузнецы крайне бережливы, запасы уникального металла исчерпались. Булатная броня со временем превратилась в легендарное оружие из прошлого, благодаря которому было одержано множество великих побед. Сведения о чудесном оружии передавались из уст в уста, от стариков к молодым.
С того времени прошло много лет, но героическая булатная броня, значение которой с годами лишь возвысилось, не давала людям покоя. Узорчатые клинки, выкованные из стали, воспевались в былинах, мифах, сказаниях. Вот лишь несколько примеров того, как в сказках упоминается булат и броня из него:
- в книге о Владимире Красно Солнышко один из витязей, сверкая булатной броней, сражается с «врагом окаянным»;
- в «Сказке о царе Салтане», написанной Пушкиным, купцы, помимо золота и серебра, привозили булат;
- крестьянский сын Иван побеждает неведомое Чудо-Юдо, снеся ему головы булатным мечом;
- в сказке о приключениях находчивого босяка Аладдина путешественников пугают ядом и булатом;
- братец Иванушка, испивший воды из лужицы и обращённый в козлёнка, зовёт сестрицу Алёнушку на помощь словами: «Ножи точат булатные, хотят меня зарезати…»;
- Финли-охотника в одноименной сказке добрая фея предупреждает о том, что его хотят убить острым булатным мечом;
- в книге «Хозяйка Заколдованного Леса» главный герой Велимир в поисках злобной ведьмы мечом из булата прорубает себе путь в ветвях и зарослях;
- великий и могучий богатырь Еруслан Лазаревич отсекает булатным мечом голову коварному Змею.
Помимо старинных сказок и преданий, в современных стихах и прозе часто встречается словосочетание «булатная броня». Значение слова неоценимо в литературе, соответственно, благодаря современным авторам булат существует и поныне. Вот современники, усилиями которых сохраняются знания о сверхостром оружии:
- Виктор Прищепенко («И вооружены зело»).
- Андрей Шабельников («Меч булатный храброго тевтона»).
- Сергей Семёнов («Верхом на Горыныче»).
- Нинель Кошкина («Знает ли Тень своё место?»).
- Сергей Степанов («Ярость норманнов»).
Сокровище из Индии
Первыми искусственно созданный булат научились делать в Индии. Затем секрет производства высокопрочного металла просочился в Иран и Среднюю Азию. Правда, в тех краях булатная сталь, характеристики которой превосходили все самые смелые ожидания, называлась по-другому. В Индии это был «вуц», а в Азии и Иране — «фаранд», «табан», «хорасан».
Персидский учёный-энциклопедист Аль Бируни, живший в средневековье и владевший знаниями практически во всех научных сферах того времени, написал о булате целый трактат. Он сохранился в древних архивах до наших дней. Аль Бируни написал: «Булатная броня получается путём расплавления двух веществ, которые плавятся неравномерно и не смешиваются между собой до однородности. В результате получаются двухцветные клинки, которые ценятся необычайно высоко».
Булатная броня легко узнаваема по характерному узорчатому рисунку. Он получается в результате кристаллизации углеродов и является своеобразным знаком отличия таких изделий. Помимо этого, клинки из булатной стали были невероятно острыми. Например, они легко рассекали наброшенный на острие платок из тончайшей газовой ткани.
Мастерство дамасских кузнецов
Больше всего булатной брони производили в сирийском Дамаске. Круглые слитки булата в Сирию привозили из Индии, а дамасские кузнецы уже ковали великолепное, сказочное оружие. Кинжалы, сабли и клинки стоили дороже золота и являлись символом богатства и процветания.
Цена на индийский булат росла в геометрической прогрессии. И сирийские умельцы путём компонования разных видов стали и многократной проковки создали сварной булат, который по сей день называется дамасской сталью и очень высоко ценится.
После того как Сирия была захвачена одним из военачальников хана Тоглука — Тамерланом, он вывез из покорённой страны всех кузнецов и поселил их в Самарканде. Однако в неволе мастера работали из рук вон плохо. И со временем кузнечное дело захирело. Потомки сирийских мастеров расселились по всему миру, и способ изготовления булата и брони из него был окончательно забыт.
По следам древних торговцев
Есть сведения, что сталь, весьма похожую на булат, изготавливали в Японии. Клинки, привезенные из этой страны, обладали такой же гибкостью и прочностью, как оружие из космического материала.
При расширении торговых путей восточный металл, а также сабли, кинжалы и ножи из булатной стали оказались на Руси. В исторических источниках имеются сведения о том, что русские кузнецы закупали данный материал для изготовления весьма дорогостоящего оружия.
Булатная броня, значение которой было необычайно высоким в тех странах, с которыми Восток вёл торговлю, очень ценилась в Англии. Об этом свидетельствуют сообщения Английской Королевской Академии, датированные 1795 годом и сохранившиеся до наших дней. В них описываются события, связанные с закупкой слитков клинковой стали для исследований.
Однако секрет изготовления чудо-металла хранился за семью печатями. И это неудивительно: ведь в давние времена ещё не было химических лабораторий и анализов, поэтому вывести формулу идеального булата было попросту невозможно. Всё делалось на глаз, а приблизительные пропорции и состав держались в строжайшем секрете. Мало кто достоверно знал и то, как правильно изготавливается булатная броня. Значение слова «булат» тем не менее ассоциировалось с наилучшим качеством оружия и приводило воинов в благоговейный трепет.
Распространение подделки
Спустя годы кузнецы Европы пытались воссоздать хотя бы дамасскую сталь, но потерпели неудачу. Им ничего не оставалось, как научиться изготавливать ложный металл, оружие из которого внешне выглядело как булатное, но по остальным качествам не шло ни в какое сравнение с истинной броней из мифов.
В 18-19-м веках производство поддельного булата было широко распространено в Италии, Германии, Испании, Болгарии и Франции. Оружие из него, особенно германское и испанское, пользовалось бешеной популярностью благодаря красивому внешнему виду, сочетающему в себе зеркальную полировку и красивые узоры. Качество же ложной булатной брони оставляло желать лучшего. Потому что оружие делали из обычной углеродистой стали низкого качества.
Воссозданный из тьмы веков
Прошло несколько веков, прежде чем в России создали булатную сталь, которая по своему составу была почти копией восточных образцов. Воспроизведением легендарного двухцветного металла занимался лично горный инженер, учёный-металлург и по совместительству генерал-майор — Павел Петрович Аносов. Он, талантливый россиянин, патриот своей Родины, выросший на сказках о богатырях, был уверен, что булатная броня — это несокрушимое оружие.
Всё началось в 1828 году, когда Горное ведомство поручило начальнику Златоустовского завода (Челябинская область) Аносову раскрыть секрет сверхпрочной стали и разработать формулу булата. Разработки и опыты, череда удач и неудач продолжались больше 10 лет. В процессе исследований учёный впервые использовал для изучения металлов микроскоп, а также заменил золочение клинков гальванизацией.
Аносов смешивал железную руду и графит, соединял разные виды железа, плавил металлы на воздухе и в вакууме — одним словом, экспериментировал.
В конце 1838 года Павлу Петровичу всё-таки удалось получить узорчатую сталь — литой булат, ничуть не уступающий по качеству древним восточным образцам. В 1839 году слитки металла и изделия из него отправились на выставку в Санкт-Петербург. И уже в 1841 году Аносов написал одну из своих самых крупных работ — «О булатах», которая была номинирована на Демидовскую премию.
Благодаря этому умнейшему человеку булатная броня, значение которой воспевалось в древних сказаниях, перестала быть недостижимой мечтой.
Аносовский булат
Что же представлял собой булат, воссозданный Аносовым? По своим химическим свойствам этот металл отличался от стали увеличенным количеством содержания различных углеродов и по параметрам был очень схож с чугуном. Однако, в отличие от нековкого, хрупкого чугуна, булат был более мягким и податливым и при этом невероятно твёрдым и крепким. Чтобы получить качественный булат, нужно было чётко соблюдать технологию производства. В противном случае неправильная обработка способна превратить этот крепкий металл в обыкновенную сталь.
После смерти Аносова секрет изготовления качественного булата вновь был утерян. Возможно, его просто спрятали от лишних глаз, а может, это случилось в результате халатного отношения. Однако спустя некоторое время воссоздать аносовский булат вознамерился изобретатель и металлург Дмитрий Константинович Чернов.
Он провёл великое множество опытов, смешивая низкосерное железо и серебристый графит в разных пропорциях. В результате Чернов получил прекрасный узорчатый металл, но обнаружил, что при ковке рисунок исчезает. Учёный пришёл к выводу, что главное условие для создания булатной брони — верно выбранная температура при ковке. Несмотря на предпринятые попытки, получить тот самый прославленный металл ему так и не удалось.
Всё дело в молибдене?
Сравнительно недавно во время очередных раскопок был найден клинок из японского булата, сделанный в 12-м веке. Химический анализ оружия раскрыл одну из тайн уникальных качеств этого материала. Учёные обнаружили в стали молибден — ковкий переходной тугоплавкий металл, который в естественном виде не встречается. В современной оружейной промышленности молибден давно используют как легирующую добавку к различным видам стали. Это увеличивает прочность и вязкость оружия.
Вряд ли древние японцы знали о молибдене. Вероятнее всего, железная руда, из которой они изготавливали оружие, содержала в себе большое количество этого химического элемента.
Тайна не разгадана!
На сегодняшний день современные виды стали значительно превосходят булат. И тем не менее он до сих пор является одним из самых совершенных металлов для производства холодного оружия.
Если задаться целью, можно найти умельца-кузнеца, который способен выковать булатный нож. В конце концов, в жизни всегда есть место сказке…
Узор клинка всегда неповторим,
С другими он не схож, как личность.
Меч воину – и друг, и побратим…
В нём – боль войны и мира поэтичность.
(Александр Симонов, «Булатный меч»)
Источник: fb.rumonateka.com