ΠΡΠ½ΠΎΠ²Π½ΡΠ΅ Π±Π°Π·ΠΎΠ²ΡΠ΅ ΠΌΠΎΠ΄Π΅Π»ΠΈ Π°Π²ΡΠΎΠΌΠΎΠ±ΠΈΠ»Π΅ΠΉ ΠΠ°ΠΌΠΠ
ΠΠ°ΠΊΠΎΠΏΠ»Π΅Π½Π½ΡΠΉ ΠΎΠΏΡΡ ΡΠΊΡΠΏΠ»ΡΠ°ΡΠ°ΡΠΈΠΈ ΠΌΠ°ΡΠΈΠ½, ΠΏΠΎΡΡΠΎΡΠ½Π½ΠΎΠ΅ ΡΠΎΠ²Π΅ΡΡΠ΅Π½ΡΡΠ²ΠΎΠ²Π°Π½ΠΈΠ΅ ΠΈΡ ΠΊΠΎΠ½ΡΡΡΡΠΊΡΠΈΠΈ ΠΠ°ΠΌΡΠΊΠΈΠΌ ΠΎΠ±ΡΠ΅Π΄ΠΈΠ½Π΅Π½ΠΈΠ΅ΠΌ ΠΏΠΎ ΠΏΡΠΎΠΈΠ·Π²ΠΎΠ΄ΡΡΠ²Ρ Π±ΠΎΠ»ΡΡΠ΅Π³ΡΡΠ·Π½ΡΡ Π°Π²ΡΠΎΠΌΠΎΠ±ΠΈΠ»Π΅ΠΉ ΠΏΠΎΠ·Π²ΠΎΠ»ΡΠ΅Ρ ΡΠ΄Π΅Π»Π°ΡΡ Π΄ΠΎΡΡΠ°ΡΠΎΡΠ½ΠΎ ΠΎΠ±ΡΠ΅ΠΊΡΠΈΠ²Π½ΡΠ΅ Π²ΡΠ²ΠΎΠ΄Ρ ΠΎ Π²ΡΡΠΎΠΊΠΎΠΉ Π½Π°Π΄Π΅ΠΆΠ½ΠΎΡΡΠΈ Π°Π²ΡΠΎΠΌΠΎΠ±ΠΈΠ»Π΅ΠΉ ΠΠ°ΠΌΠΠ. ΠΠ°Π΄Π΅ΠΆΠ½Π°Ρ ΡΠ°Π±ΠΎΡΠ° ΠΌΠ°ΡΠΈΠ½ ΠΈ ΠΈΡ ΡΠΎΡΡΠ°Π²Π½ΡΡ ΡΠ°ΡΡΠ΅ΠΉ, Π²ΠΊΠ»ΡΡΠ°Ρ Π²ΡΠ΅ ΠΈΠ·Π³ΠΎΡΠΎΠ²Π»Π΅Π½Π½ΡΠ΅ Π΄ΡΡΠ³ΠΈΠΌΠΈ Π·Π°Π²ΠΎΠ΄Π°ΠΌΠΈ ΠΈΠ·Π΄Π΅Π»ΠΈΡ, ΠΊΡΠΎΠΌΠ΅ ΡΠΈΠ½ ΠΈ Π°ΠΊΠΊΡΠΌΡΠ»ΡΡΠΎΡΠ½ΡΡ Π±Π°ΡΠ°ΡΠ΅ΠΉ, Π³Π°ΡΠ°Π½ΡΠΈΡΡΠ΅ΡΡΡ ΠΠ°ΠΌΡΠΊΠΈΠΌ ΠΎΠ±ΡΠ΅Π΄ΠΈΠ½Π΅Π½ΠΈΠ΅ΠΌ. ΠΠ°ΡΠ°Π½ΡΠΈΠΉΠ½ΡΠ΅ ΡΡΠΎΠΊΠΈ ΠΈΡΡΠΈΡΠ»ΡΡΡΡΡ:
- ΠΏΡΠΈ ΠΏΠΎΠ»ΡΡΠ΅Π½ΠΈΠΈ Π°Π²ΡΠΎΠΌΠΎΠ±ΠΈΠ»Ρ Π½Π΅ΠΏΠΎΡΡΠ΅Π΄ΡΡΠ²Π΅Π½Π½ΠΎ Π½Π° Π·Π°Π²ΠΎΠ΄Π΅-ΠΈΠ·Π³ΠΎΡΠΎΠ²ΠΈΡΠ΅Π»Π΅ β Ρ ΠΌΠΎΠΌΠ΅Π½ΡΠ° ΠΏΠ΅ΡΠ΅Π΄Π°ΡΠΈ Π°Π²ΡΠΎΠΌΠΎΠ±ΠΈΠ»Ρ ΠΏΠΎΡΡΠ΅Π±ΠΈΡΠ΅Π»Ρ;
- ΠΏΡΠΈ Π΄ΠΎΡΡΠ°Π²ΠΊΠ΅ ΠΏΠΎΡΡΠ΅Π±ΠΈΡΠ΅Π»Ρ Π°Π²ΡΠΎΠΌΠΎΠ±ΠΈΠ»Π΅ΠΉ ΠΆΠ΅Π»Π΅Π·Π½ΠΎΠ΄ΠΎΡΠΎΠΆΠ½ΡΠΌ ΠΈΠ»ΠΈ Π²ΠΎΠ΄Π½ΡΠΌ ΡΡΠ°Π½ΡΠΏΠΎΡΡΠΎΠΌ β ΡΠΎ Π΄Π½Ρ ΠΎΡΠ³ΡΡΠ·ΠΊΠΈ Ρ Π·Π°Π²ΠΎΠ΄Π°, Π½Π΅ ΡΡΠΈΡΠ°Ρ Π²ΡΠ΅ΠΌΠ΅Π½ΠΈ Π½Π°Ρ ΠΎΠΆΠ΄Π΅Π½ΠΈΡ Π² ΠΏΡΡΠΈ ΡΠ»Π΅Π΄ΠΎΠ²Π°Π½ΠΈΡ ΠΊ ΠΌΠ΅ΡΡΡ Π½Π°Π·Π½Π°ΡΠ΅Π½ΠΈΡ.
Π ΡΠ΅ΡΠ΅Π½ΠΈΠ΅ Π³Π°ΡΠ°Π½ΡΠΈΠΉΠ½ΠΎΠ³ΠΎ ΡΡΠΎΠΊΠ° Π·Π°Π²ΠΎΠ΄-ΠΈΠ·Π³ΠΎΡΠΎΠ²ΠΈΡΠ΅Π»Ρ Π±Π΅Π·Π²ΠΎΠ·ΠΌΠ΅Π·Π΄Π½ΠΎ ΠΏΡΠΎΠΈΠ·Π²ΠΎΠ΄ΠΈΡ Π·Π°ΠΌΠ΅Π½Ρ Π²ΡΠ΅Ρ Π΄Π΅ΡΠ°Π»Π΅ΠΉ, ΡΠ·Π»ΠΎΠ² ΠΈ Π°Π³ΡΠ΅Π³Π°ΡΠΎΠ², ΠΏΡΠ΅ΠΆΠ΄Π΅Π²ΡΠ΅ΠΌΠ΅Π½Π½ΠΎ Π²ΡΡΠ΅Π΄ΡΠΈΡ ΠΈΠ· ΡΡΡΠΎΡ ΠΏΠΎ Π²ΠΈΠ½Π΅ Π·Π°Π²ΠΎΠ΄Π°. ΠΠ°ΡΠ°Π½ΡΠΈΠΈ Π½Π° ΡΠΈΠ½Ρ ΠΈ Π°ΠΊΠΊΡΠΌΡΠ»ΡΡΠΎΡΠ½ΡΠ΅ Π±Π°ΡΠ°ΡΠ΅ΠΈ Π΄Π°ΡΡΡΡ Π·Π°Π²ΠΎΠ΄Π°ΠΌΠΈ-ΠΈΠ·Π³ΠΎΡΠΎΠ²ΠΈΡΠ΅Π»ΡΠΌΠΈ ΡΠΊΠ°Π·Π°Π½Π½ΡΡ ΠΈΠ·Π΄Π΅Π»ΠΈΠΉ Π² ΡΠΎΠΎΡΠ²Π΅ΡΡΡΠ²ΠΈΠΈ Ρ ΡΡΠ²Π΅ΡΠΆΠ΄Π΅Π½Π½ΡΠΌΠΈ Π½Π° Π½ΠΈΡ ΡΡΠ°Π½Π΄Π°ΡΡΠ°ΠΌΠΈ ΠΈΠ»ΠΈ ΡΠ΅Ρ Π½ΠΈΡΠ΅ΡΠΊΠΈΠΌΠΈ ΡΡΠ»ΠΎΠ²ΠΈΡΠΌΠΈ. ΠΡΠΈ ΡΠΊΡΠΏΠ»ΡΠ°ΡΠ°ΡΠΈΠΈ Π°Π²ΡΠΎΠΌΠΎΠ±ΠΈΠ»Π΅ΠΉ Ρ Π½Π°ΡΡΡΠ΅Π½ΠΈΡΠΌΠΈ Π·Π°Π²ΠΎΠ΄ΡΠΊΠΎΠΉ ΠΈΠ½ΡΡΡΡΠΊΡΠΈΠΈ ΠΈ Π²Π½Π΅ΡΠ΅Π½ΠΈΠΈ ΠΊΠ°ΠΊΠΈΡ -Π»ΠΈΠ±ΠΎ ΠΊΠΎΠ½ΡΡΡΡΠΊΡΠΈΠ²Π½ΡΡ ΠΈΠ·ΠΌΠ΅Π½Π΅Π½ΠΈΠΉ Π² Π½ΠΈΡ Π±Π΅Π· ΡΠΎΠ³Π»Π°ΡΠΎΠ²Π°Π½ΠΈΡ Ρ Π·Π°Π²ΠΎΠ΄ΠΎΠΌ-ΠΈΠ·Π³ΠΎΡΠΎΠ²ΠΈΡΠ΅Π»Π΅ΠΌ (ΠΠ°ΠΌΡΠΊΠΈΠΌ ΠΎΠ±ΡΠ΅Π΄ΠΈΠ½Π΅Π½ΠΈΠ΅ΠΌ) ΡΠ΅ΠΊΠ»Π°ΠΌΠ°ΡΠΈΠΈ ΠΏΠΎΡΠ»Π΅Π΄ Π½ΠΈΠΌ Π½Π΅ ΠΏΡΠΈΠ½ΠΈΠΌΠ°ΡΡΡΡ ΠΈ Π½Π΅ ΡΠ°ΡΡΠΌΠ°ΡΡΠΈΠ²Π°ΡΡΡΡ. ΠΠ²ΡΠΎΠΌΠΎΠ±ΠΈΠ»ΠΈ ΠΠ°ΠΌΠΠ ΠΏΠΎ ΡΡΠ°Π²Π½Π΅Π½ΠΈΡ Ρ Π΄ΡΡΠ³ΠΈΠΌΠΈ ΠΌΠ°ΡΠΊΠ°ΠΌΠΈ Π°Π²ΡΠΎΠΌΠΎΠ±ΠΈΠ»Π΅ΠΉ ΠΈΠΌΠ΅ΡΡ Π±ΠΎΠ»Π΅Π΅ ΠΏΡΠΎΠ΄ΠΎΠ»ΠΆΠΈΡΠ΅Π»ΡΠ½ΡΠΉ ΠΎΠ±ΠΊΠ°ΡΠΎΡΠ½ΡΠΉ ΠΏΠ΅ΡΠΈΠΎΠ΄. ΠΠΊΡΠΏΠ»ΡΠ°ΡΠ°ΡΠΈΠΎΠ½Π½Π°Ρ ΠΎΠ±ΠΊΠ°ΡΠΊΠ° ΡΠΎΡΡΠ°Π²Π»ΡΠ΅Ρ 4000 ΠΊΠΌ. Π£ΡΡΠ°Π½ΠΎΠ²Π»Π΅Π½Π° ΡΠ»Π΅Π΄ΡΡΡΠ°Ρ ΠΏΠ΅ΡΠΈΠΎΠ΄ΠΈΡΠ½ΠΎΡΡΡ ΡΠ΅Ρ Π½ΠΈΡΠ΅ΡΠΊΠΈΡ ΠΎΠ±ΡΠ»ΡΠΆΠΈΠ²Π°Π½ΠΈΠΉ: Π’Π-1000 ΠΏΡΠΎΠ²ΠΎΠ΄ΠΈΡΡΡ ΡΠ΅ΡΠ΅Π· 500β 1000 ΠΊΠΌ; Π’Π-1 β ΡΠ΅ΡΠ΅Π· 2400β4000 ΠΊΠΌ; Π’Π-2 β ΡΠ΅ΡΠ΅Π· 7200β12000 ΠΊΠΌ ΠΏΡΠΎΠ±Π΅Π³Π°. Π‘Π΅Π·ΠΎΠ½Π½ΠΎΠ΅ ΡΠ΅Ρ Π½ΠΈΡΠ΅ΡΠΊΠΎΠ΅ ΠΎΠ±ΡΠ»ΡΠΆΠΈΠ²Π°Π½ΠΈΠ΅ (Π‘Π) Π²ΡΠΏΠΎΠ»Π½ΡΠ΅ΡΡΡ 2 ΡΠ°Π·Π° Π² Π³ΠΎΠ΄ β Π²Π΅ΡΠ½ΠΎΠΉ ΠΈ ΠΎΡΠ΅Π½ΡΡ. Π Π°ΡΡΠ΅ΡΠ½Π°Ρ ΠΏΠ΅ΡΠΈΠΎΠ΄ΠΈΡΠ½ΠΎΡΡΡ Π’Π 24000 ΠΊΠΌ. Π‘ΠΎΠ±Π»ΡΠ΄Π΅Π½ΠΈΠ΅ ΡΡΠ΅Π±ΠΎΠ²Π°Π½ΠΈΠΉ ΡΠΊΡΠΏΠ»ΡΠ°ΡΠ°ΡΠΈΠΈ Π°Π²ΡΠΎΠΌΠΎΠ±ΠΈΠ»Π΅ΠΉ Π² ΠΎΠ±ΠΊΠ°ΡΠΎΡΠ½ΡΠΉ ΠΏΠ΅ΡΠΈΠΎΠ΄ ΠΈ ΡΠ²ΠΎΠ΅Π²ΡΠ΅ΠΌΠ΅Π½Π½ΠΎΠ΅ Π²ΡΠΏΠΎΠ»Π½Π΅Π½ΠΈΠ΅ ΡΠ΅Ρ Π½ΠΈΡΠ΅ΡΠΊΠΈΡ ΠΎΠ±ΡΠ»ΡΠΆΠΈΠ²Π°Π½ΠΈΠΉ ΠΎΠ±Π΅ΡΠΏΠ΅ΡΠΈΠ²Π°ΡΡ ΠΏΡΠΎΠ±Π΅Π³ΠΈ Π°Π²ΡΠΎΠΌΠΎΠ±ΠΈΠ»Π΅ΠΉ ΠΠ°ΠΌΠΠ-5320 ΠΈ Π΅Π³ΠΎ ΠΌΠΎΠ΄ΠΈΡΠΈΠΊΠ°ΡΠΈΠΉ Π±Π΅Π· ΠΊΠ°ΠΏΠΈΡΠ°Π»ΡΠ½ΠΎΠ³ΠΎ ΡΠ΅ΠΌΠΎΠ½ΡΠ° Π±ΠΎΠ»Π΅Π΅ 300 ΡΡΡ. ΠΊΠΌ. ΠΠ°ΡΠ°Π½ΡΠΈΠΉΠ½ΡΠΉ ΡΡΠΎΠΊ ΡΠ°Π±ΠΎΡΡ, Π²ΠΈΠ΄Ρ ΡΠ΅Ρ Π½ΠΈΡΠ΅ΡΠΊΠΈΡ ΠΎΠ±ΡΠ»ΡΠΆΠΈΠ²Π°Π½ΠΈΠΉ Π°Π²ΡΠΎΠΌΠΎΠ±ΠΈΠ»Π΅ΠΉ ΠΠ°ΠΌΠΠ, Π²ΡΠΏΠΎΠ»Π½ΡΠ΅ΠΌΡΡ Π² ΠΏΠ΅ΡΠΈΠΎΠ΄ ΠΎΡ Π½Π°ΡΠ°Π»Π° ΡΠΊΡΠΏΠ»ΡΠ°ΡΠ°ΡΠΈΠΈ Π΄ΠΎ ΠΊΠ°ΠΏΠΈΡΠ°Π»ΡΠ½ΠΎΠ³ΠΎ ΡΠ΅ΠΌΠΎΠ½ΡΠ°, ΠΏΠΎΠΊΠ°Π·Π°Π½Ρ Π½Π° ΡΠΈΡ. 4. ΠΠΎΠ»ΠΈΡΠ΅ΡΡΠ²ΠΎ ΡΠ΅Ρ Π½ΠΈΡΠ΅ΡΠΊΠΈΡ ΠΎΠ±ΡΠ»ΡΠΆΠΈΠ²Π°Π½ΠΈΠΉ, Π²ΡΠΏΠΎΠ»Π½ΡΠ΅ΠΌΠΎΠ΅ Π·Π° ΠΌΠ΅ΠΆΡΠ΅ΠΌΠΎΠ½ΡΠ½ΡΠΉ ΠΏΠ΅ΡΠΈΠΎΠ΄ ΡΠΊΡΠΏΠ»ΡΠ°ΡΠ°ΡΠΈΠΈ (300 ΡΡΡ. ΠΊΠΌ), ΡΠ»Π΅Π΄ΡΡΡΠ΅Π΅: Π’Π-1000 β 1; Π’Π-4000 β 1; Π’Π-1 β 50; Π’Π-2 β 24.
ΠΠΎΠ½ΡΡΡΡΠΊΡΠΈΠ²Π½ΠΎ Π°Π²ΡΠΎΠΌΠΎΠ±ΠΈΠ»Ρ ΠΌΠΎΠΆΠ½ΠΎ ΡΠ°Π·Π΄Π΅Π»ΠΈΡΡ Π½Π° ΠΎΡΠ½ΠΎΠ²Π½ΡΠ΅ ΡΠ°ΡΡΠΈ: Π΄Π²ΠΈΠ³Π°ΡΠ΅Π»Ρ, ΡΠ°ΡΡΠΈ, ΠΊΠ°Π±ΠΈΠ½Ρ ΠΈ ΠΏΠ»Π°ΡΡΠΎΡΠΌΡ. Π‘Ρ Π΅ΠΌΠ° ΡΡΡΡΠΎΠΉΡΡΠ²Π° Π°Π²ΡΠΎΠΌΠΎΠ±ΠΈΠ»Ρ ΠΏΠΎΠΊΠ°Π·Π°Π½Π° Π½Π° ΡΠΈΡ. 1. ΠΠ²ΠΈΠ³Π°ΡΠ΅Π»Ρ ΡΠ²Π»ΡΠ΅ΡΡΡ ΠΈΡΡΠΎΡΠ½ΠΈΠΊΠΎΠΌ ΠΌΠ΅Ρ Π°Π½ΠΈΡΠ΅ΡΠΊΠΎΠΉ ΡΠ½Π΅ΡΠ³ΠΈΠΈ, ΠΏΡΠΈΠ²ΠΎΠ΄ΡΡΠ΅ΠΉ Π°Π²ΡΠΎΠΌΠΎΠ±ΠΈΠ»Ρ Π² Π΄Π²ΠΈΠΆΠ΅Π½ΠΈΠ΅. Π¨Π°ΡΡΠΈ ΡΠΎΡΡΠΎΠΈΡ ΠΈΠ· Π½Π΅ΡΠΊΠΎΠ»ΡΠΊΠΈΡ ΡΠΎΡΡΠ°Π²Π½ΡΡ ΡΠ°ΡΡΠ΅ΠΉ, ΠΏΡΠ΅Π΄Π½Π°Π·Π½Π°ΡΠ΅Π½Π½ΡΡ Π΄Π»Ρ ΠΊΡΠ΅ΠΏΠ»Π΅Π½ΠΈΡ Π²ΡΠ΅Ρ Π°Π³ΡΠ΅Π³Π°ΡΠΎΠ² ΠΈ ΠΌΠ΅Ρ Π°Π½ΠΈΠ·ΠΌΠΎΠ², ΠΏΠ΅ΡΠ΅Π΄Π°ΡΠΈ ΠΊΡΡΡΡΡΠ΅Π³ΠΎ ΠΌΠΎΠΌΠ΅Π½ΡΠ° ΠΎΡ Π΄Π²ΠΈΠ³Π°ΡΠ΅Π»Ρ ΠΊ Π²Π΅Π΄ΡΡΠΈΠΌ ΠΊΠΎΠ»Π΅ΡΠ°ΠΌ, ΠΎΠ±Π΅ΡΠΏΠ΅ΡΠ΅Π½ΠΈΡ Π΄Π²ΠΈΠΆΠ΅Π½ΠΈΡ, ΡΠΏΡΠ°Π²Π»Π΅Π½ΠΈΡ ΠΈ ΡΠΎΡΠΌΠΎΠΆΠ΅Π½ΠΈΡ. Π ΠΎΡΠ½ΠΎΠ²Π½ΡΠΌ ΡΠ°ΡΡΡΠΌ ΡΠ°ΡΡΠΈ ΠΎΡΠ½ΠΎΡΡΡΡΡ:
- ΡΠΈΠ»ΠΎΠ²Π°Ρ ΠΏΠ΅ΡΠ΅Π΄Π°ΡΠ°, Π½Π΅ΠΎΠ±Ρ ΠΎΠ΄ΠΈΠΌΠ°Ρ Π΄Π»Ρ ΠΏΠ΅ΡΠ΅Π΄Π°ΡΠΈ ΠΊΡΡΡΡΡΠ΅Π³ΠΎ ΠΌΠΎΠΌΠ΅Π½ΡΠ° ΠΎΡ Π΄Π²ΠΈΠ³Π°ΡΠ΅Π»Ρ ΠΊ Π²Π΅Π΄ΡΡΠΈΠΌ ΠΊΠΎΠ»Π΅ΡΠ°ΠΌ Π°Π²ΡΠΎΠΌΠΎΠ±ΠΈΠ»Ρ;
- Ρ ΠΎΠ΄ΠΎΠ²Π°Ρ ΡΠ°ΡΡΡ, ΡΠ»ΡΠΆΠ°ΡΠ°Ρ Π΄Π»Ρ ΠΊΡΠ΅ΠΏΠ»Π΅Π½ΠΈΡ Π²ΡΠ΅Ρ Π°Π³ΡΠ΅Π³Π°ΡΠΎΠ² ΠΈ ΠΌΠ΅Ρ Π°Π½ΠΈΠ·ΠΌΠΎΠ² Π½Π° ΡΠ°ΠΌΠ΅ ΠΈ ΠΎΠ±Π΅ΡΠΏΠ΅ΡΠ΅Π½ΠΈΡ Π΄Π²ΠΈΠΆΠ΅Π½ΠΈΡ Π°Π²ΡΠΎΠΌΠΎΠ±ΠΈΠ»Ρ;
- ΠΌΠ΅Ρ Π°Π½ΠΈΠ·ΠΌΡ ΡΠΏΡΠ°Π²Π»Π΅Π½ΠΈΡ, ΠΎΠ±Π΅ΡΠΏΠ΅ΡΠΈΠ²Π°ΡΡΠΈΠ΅ ΡΠΏΡΠ°Π²Π»Π΅Π½ΠΈΠ΅ Π΄Π²ΠΈΠΆΠ΅Π½ΠΈΠ΅ΠΌ Π°Π²ΡΠΎΠΌΠΎΠ±ΠΈΠ»Ρ, Π΅Π³ΠΎ ΡΠΎΡΠΌΠΎΠΆΠ΅Π½ΠΈΠ΅ ΠΈ ΠΎΡΡΠ°Π½ΠΎΠ²ΠΊΡ.
Π ΠΈΡ. 1. Π‘Ρ Π΅ΠΌΠ° ΠΎΠ±ΡΠ΅Π³ΠΎ ΡΡΡΡΠΎΠΉΡΡΠ²Π° Π°Π²ΡΠΎΠΌΠΎΠ±ΠΈΠ»Ρ ΠΠ°ΠΌΠ°Π·:
1 β Π΄Π²ΠΈΠ³Π°ΡΠ΅Π»Ρ; 2 β ΡΡΠ΅ΠΏΠ»Π΅Π½ΠΈΠ΅; 3 β ΠΊΠΎΡΠΎΠ±ΠΊΠ° ΠΏΠ΅ΡΠ΅Π΄Π°Ρ; 4 β ΠΊΠ°ΡΠ΄Π°Π½Π½Π°Ρ ΠΏΠ΅ΡΠ΅Π΄Π°ΡΠ°; 5 β ΡΡΠ΅Π΄Π½ΠΈΠΉ ΠΌΠΎΡΡ; 6 β ΡΠ°ΠΌΠ°; 7 β Π·Π°Π΄Π½ΡΡ ΠΏΠΎΠ΄Π²Π΅ΡΠΊΠ°; Π‘ΠΈΠ»ΠΎΠ²Π°Ρ ΠΏΠ΅ΡΠ΅Π΄Π°ΡΠ° Π°Π²ΡΠΎΠΌΠΎΠ±ΠΈΠ»Ρ Π²ΠΊΠ»ΡΡΠ°Π΅Ρ ΡΠ»Π΅Π΄ΡΡΡΠΈΠ΅ Π°Π³ΡΠ΅Π³Π°ΡΡ ΠΈ ΠΌΠ΅Ρ Π°Π½ΠΈΠ·ΠΌΡ: ΡΡΠ΅ΠΏΠ»Π΅Π½ΠΈΠ΅, ΠΊΠΎΡΠΎΠ±ΠΊΡ ΠΏΠ΅ΡΠ΅Π΄Π°Ρ, ΠΊΠ°ΡΠ΄Π°Π½Π½ΡΡ ΠΏΠ΅ΡΠ΅Π΄Π°ΡΡ, Π³Π»Π°Π²Π½ΡΡ ΠΏΠ΅ΡΠ΅Π΄Π°ΡΡ, Π΄ΠΈΡΡΠ΅ΡΠ΅Π½ΡΠΈΠ°Π» ΠΈ ΠΏΠΎΠ»ΡΠΎΡΠΈ. Π‘ΡΠ΅ΠΏΠ»Π΅Π½ΠΈΠ΅ ΠΏΡΠ΅Π΄Π½Π°Π·Π½Π°ΡΠ΅Π½ΠΎ Π΄Π»Ρ ΡΠΎΠ΅Π΄ΠΈΠ½Π΅Π½ΠΈΡ Π΄Π²ΠΈΠ³Π°ΡΠ΅Π»Ρ Ρ ΡΡΠ°Π½ΡΠΌΠΈΡΡΠΈΠ΅ΠΉ ΠΏΡΠΈ ΡΡΠΎΠ³Π°Π½ΠΈΠΈ Π°Π²ΡΠΎΠΌΠΎΠ±ΠΈΠ»Ρ Ρ ΠΌΠ΅ΡΡΠ° ΠΈ ΠΏΠ΅ΡΠ΅Π΄Π°ΡΠΈ ΠΊΡΡΡΡΡΠ΅Π³ΠΎ ΠΌΠΎΠΌΠ΅Π½ΡΠ° ΠΏΡΠΈ Π΅Π³ΠΎ Π΄Π²ΠΈΠΆΠ΅Π½ΠΈΠΈ, ΠΎΡΡΠΎΠ΅Π΄ΠΈΠ½Π΅Π½ΠΈΡ Π΄Π²ΠΈΠ³Π°ΡΠ΅Π»Ρ ΠΎΡ ΡΡΠ°Π½ΡΠΌΠΈΡΡΠΈΠΈ ΠΏΡΠΈ ΠΏΠ΅ΡΠ΅ΠΊΠ»ΡΡΠ΅Π½ΠΈΠΈ ΠΏΠ΅ΡΠ΅Π΄Π°Ρ ΠΈ ΠΊΡΠ°ΡΠΊΠΎΠ²ΡΠ΅ΠΌΠ΅Π½Π½ΠΎΠΉ ΠΎΡΡΠ°Π½ΠΎΠ²ΠΊΠΈ. ΠΠΎΡΠΎΠ±ΠΊΠ° ΠΏΠ΅ΡΠ΅Π΄Π°Ρ ΠΎΠ±Π΅ΡΠΏΠ΅ΡΠΈΠ²Π°Π΅Ρ ΠΈΠ·ΠΌΠ΅Π½Π΅Π½ΠΈΠ΅ ΠΊΡΡΡΡΡΠ΅Π³ΠΎ ΠΌΠΎΠΌΠ΅Π½ΡΠ° Π½Π° Π²Π΅Π΄ΡΡΠΈΡ ΠΊΠΎΠ»Π΅ΡΠ°Ρ , ΠΈΠ·ΠΌΠ΅Π½Π΅Π½ΠΈΠ΅ ΡΠΊΠΎΡΠΎΡΡΠΈ Π΄Π²ΠΈΠΆΠ΅Π½ΠΈΡ Π°Π²ΡΠΎΠΌΠΎΠ±ΠΈΠ»Ρ, Π·Π°Π΄Π½ΠΈΠΉ Ρ ΠΎΠ΄ Π°Π²ΡΠΎΠΌΠΎΠ±ΠΈΠ»Ρ ΠΈ ΠΎΡΡΠΎΠ΅Π΄ΠΈΠ½Π΅Π½ΠΈΠ΅ ΡΡΠ°Π½ΡΠΌΠΈΡΡΠΈΠΈ ΠΎΡ Π΄Π²ΠΈΠ³Π°ΡΠ΅Π»Ρ Π½Π° ΡΡΠΎΡΠ½ΠΊΠ°Ρ ΠΏΡΠΈ ΡΠ°Π±ΠΎΡΠ°ΡΡΠ΅ΠΌ Π΄Π²ΠΈΠ³Π°ΡΠ΅Π»Π΅. ΠΠ°ΡΠ΄Π°Π½Π½Π°Ρ ΠΏΠ΅ΡΠ΅Π΄Π°ΡΠ° ΡΠ»ΡΠΆΠΈΡ Π΄Π»Ρ ΠΏΠ΅ΡΠ΅Π΄Π°ΡΠΈ ΡΡΠΈΠ»ΠΈΡ ΠΎΡ ΠΊΠΎΡΠΎΠ±ΠΊΠΈ ΠΏΠ΅ΡΠ΅Π΄Π°Ρ ΠΊ Π³Π»Π°Π²Π½ΠΎΠΉ ΠΏΠ΅ΡΠ΅Π΄Π°ΡΠ΅ ΠΏΡΠΈ ΠΏΠ΅ΡΠ΅ΠΌΠ΅Π½Π½ΡΡ ΡΠ³Π»Π°Ρ Π½Π°ΠΊΠ»ΠΎΠ½Π° Π²Π°Π»Π°. ΠΠ»Π°Π²Π½Π°Ρ ΠΏΠ΅ΡΠ΅Π΄Π°ΡΠ° ΠΏΡΠ΅Π΄Π½Π°Π·Π½Π°ΡΠ΅Π½Π° Π΄Π»Ρ ΠΏΠΎΠ²ΡΡΠ΅Π½ΠΈΡ ΡΡΠ³ΠΎΠ²ΠΎΠ³ΠΎ ΡΡΠΈΠ»ΠΈΡ Π½Π° Π²Π΅Π΄ΡΡΠΈΡ ΠΊΠΎΠ»Π΅ΡΠ°Ρ Π°Π²ΡΠΎΠΌΠΎΠ±ΠΈΠ»Ρ ΠΈ ΠΏΠ΅ΡΠ΅Π΄Π°ΡΠΈ ΡΡΠΈΠ»ΠΈΠΉ Ρ Π²Π΅Π΄ΡΡΠ΅Π³ΠΎ Π²Π°Π»Π° Π½Π° ΠΏΠΎΠ»ΡΠΎΡΠΈ ΠΏΠΎΠ΄ ΡΠ³Π»ΠΎΠΌ 90Β°. ΠΠΈΡΡΠ΅ΡΠ΅Π½ΡΠΈΠ°Π» Ρ ΠΏΠΎΠ»ΡΠΎΡΡΠΌΠΈ ΠΏΠΎΠ·Π²ΠΎΠ»ΡΠ΅Ρ ΠΏΡΠΈ ΠΏΠΎΠ²ΠΎΡΠΎΡΠ°Ρ Π°Π²ΡΠΎΠΌΠΎΠ±ΠΈΠ»Ρ Π²Π΅Π΄ΡΡΠΈΠΌ ΠΊΠΎΠ»Π΅ΡΠ°ΠΌ Π²ΡΠ°ΡΠ°ΡΡΡΡ Ρ ΡΠ°Π·Π»ΠΈΡΠ½ΠΎΠΉ ΡΠ°ΡΡΠΎΡΠΎΠΉ Π²ΡΠ°ΡΠ΅Π½ΠΈΡ. ΠΠ»Π°Π²Π½Π°Ρ ΠΏΠ΅ΡΠ΅Π΄Π°ΡΠ° ΠΈ Π΄ΠΈΡΡΠ΅ΡΠ΅Π½ΡΠΈΠ°Π» Ρ ΠΏΠΎΠ»ΡΠΎΡΡΠΌΠΈ, Π·Π°ΠΊΠ»ΡΡΠ΅Π½Π½ΡΠ΅ Π² ΠΊΠΎΠΆΡΡ , ΠΈΠ·Π³ΠΎΡΠΎΠ²Π»Π΅Π½Π½ΡΠΉ ΠΈΠ· ΠΊΠΎΠ²ΠΊΠΎΠ³ΠΎ ΡΡΠ³ΡΠ½Π°, ΠΏΠΎΠ»ΡΡΠΈΠ»ΠΈ Π½Π°Π·Π²Π°Π½ΠΈΠ΅ Π²Π΅Π΄ΡΡΠΈΠΉ ΠΌΠΎΡΡ. ΠΠ΅Π΄ΡΡΠΈΠ΅ ΠΌΠΎΡΡΡ, ΠΎΠ±Π΅ΡΠΏΠ΅ΡΠΈΠ²Π°ΡΡΠΈΠ΅ ΠΏΠ΅ΡΠ΅Π΄Π°ΡΡ ΠΊΡΡΡΡΡΠ΅Π³ΠΎ ΠΌΠΎΠΌΠ΅Π½ΡΠ° ΠΎΡ ΠΊΠ°ΡΠ΄Π°Π½Π½ΠΎΠ³ΠΎ Π²Π°Π»Π° ΠΊ Π²Π΅Π΄ΡΡΠΈΠΌ ΠΊΠΎΠ»Π΅ΡΠ°ΠΌ, Π²Ρ ΠΎΠ΄ΡΡ Π² ΡΠΎΡΡΠ°Π² ΡΠ΅Π»Π΅ΠΆΠΊΠΈ Π°Π²ΡΠΎΠΌΠΎΠ±ΠΈΠ»Ρ. Π‘ΠΈΠ»ΠΎΠ²Π°Ρ ΠΏΠ΅ΡΠ΅Π΄Π°ΡΠ° Π°Π²ΡΠΎΠΌΠΎΠ±ΠΈΠ»Π΅ΠΉ Π²ΡΡΠΎΠΊΠΎΠΉ ΠΏΡΠΎΡ ΠΎΠ΄ΠΈΠΌΠΎΡΡΠΈ ΠΈΠΌΠ΅Π΅Ρ Π²ΠΌΠ΅ΡΡΠΎ ΠΏΠ΅ΡΠ΅Π΄Π½Π΅ΠΉ ΠΎΡΠΈ Π²Π΅Π΄ΡΡΠΈΠΉ ΠΈ ΡΠΏΡΠ°Π²Π»ΡΠ΅ΠΌΡΠΉ ΠΌΠΎΡΡΡ, Π° ΡΠ°ΠΊΠΆΠ΅ ΡΠ°Π·Π΄Π°ΡΠΎΡΠ½ΡΡ ΠΊΠΎΡΠΎΠ±ΠΊΡ ΠΈ Π΄Π²Π° ΠΊΠ°ΡΠ΄Π°Π½Π½ΡΡ Π²Π°Π»Π°, ΠΏΠ΅ΡΠ΅Π΄Π°ΡΡΠΈΡ ΠΊΡΡΡΡΡΠΈΠΉ ΠΌΠΎΠΌΠ΅Π½Ρ ΠΎΡ ΠΊΠΎΡΠΎΠ±ΠΊΠΈ ΠΏΠ΅ΡΠ΅Π΄Π°Ρ ΠΊ ΡΠ°Π·Π΄Π°ΡΠΎΡΠ½ΠΎΠΉ ΠΊΠΎΡΠΎΠ±ΠΊΠ΅ ΠΈ ΠΎΡ Π½Π΅Π΅ ΠΊ ΠΏΠ΅ΡΠ΅Π΄Π½Π΅ΠΌΡ ΠΌΠΎΡΡΡ. Π₯ΠΎΠ΄ΠΎΠ²Π°Ρ ΡΠ°ΡΡΡ Π°Π²ΡΠΎΠΌΠΎΠ±ΠΈΠ»Ρ ΡΠΎΡΡΠΎΠΈΡ ΠΈΠ· ΡΠ°ΠΌΡ, ΠΊΠΎΠ»Π΅Ρ, ΠΏΠ΅ΡΠ΅Π΄Π½Π΅ΠΉ ΠΎΡΠΈ (ΠΌΠΎΡΡΠ°), Π·Π°Π΄Π½Π΅Π³ΠΎ ΠΌΠΎΡΡΠ° (ΠΌΠΎΡΡΠΎΠ²) ΠΈ ΠΏΠΎΠ΄Π²Π΅ΡΠΊΠΈ, Π² ΠΊΠΎΡΠΎΡΡΡ Π²Ρ ΠΎΠ΄ΡΡ ΡΠ΅ΡΡΠΎΡΡ ΠΈ Π°ΠΌΠΎΡΡΠΈΠ·Π°ΡΠΎΡΡ. ΠΠ΅ΡΠ΅Π΄Π½ΠΈΠΉ ΠΈ Π·Π°Π΄Π½ΠΈΠ΅ ΠΌΠΎΡΡΡ Ρ ΠΊΠΎΠ»Π΅ΡΠ°ΠΌΠΈ, ΡΠΎΠ΅Π΄ΠΈΠ½Π΅Π½Π½ΡΠ΅ Ρ ΡΠ°ΠΌΠΎΠΉ, ΠΎΠ±ΡΠ°Π·ΡΡΡ ΡΠ΅Π»Π΅ΠΆΠΊΡ Π°Π²ΡΠΎΠΌΠΎΠ±ΠΈΠ»Ρ. Π’Π΅Π»Π΅ΠΆΠΊΠ° Π°Π²ΡΠΎΠΌΠΎΠ±ΠΈΠ»Ρ ΠΌΠΎΠΆΠ΅Ρ ΠΈΠΌΠ΅ΡΡ Π΄Π²Π°, ΡΡΠΈ ΠΈ Π±ΠΎΠ»Π΅Π΅ ΡΡΠ΅Ρ ΠΌΠΎΡΡΠΎΠ². ΠΠ²ΡΠΎΠΌΠΎΠ±ΠΈΠ»ΠΈ Ρ Π΄Π²ΡΠΌΡ ΠΌΠΎΡΡΠ°ΠΌΠΈ, ΠΈΠΌΠ΅ΡΡΠΈΠ΅ ΠΏΡΠΈΠ²ΠΎΠ΄ ΠΎΡ Π΄Π²ΠΈΠ³Π°ΡΠ΅Π»Ρ Π½Π° Π·Π°Π΄Π½ΠΈΠ΅ ΠΊΠΎΠ»Π΅ΡΠ°, Π° ΠΏΠ΅ΡΠ΅Π΄Π½ΠΈΠ΅ ΠΊΠΎΠ»Π΅ΡΠ° β ΡΠΏΡΠ°Π²Π»ΡΠ΅ΠΌΡΠ΅, Π½Π°Π·ΡΠ²Π°ΡΡΡΡ Π°Π²ΡΠΎΠΌΠΎΠ±ΠΈΠ»ΡΠΌΠΈ ΠΎΠ±ΡΡΠ½ΠΎΠΉ Π΄ΠΎΡΠΎΠΆΠ½ΠΎΠΉ ΠΏΡΠΎΡ ΠΎΠ΄ΠΈΠΌΠΎΡΡΠΈ. Π’Π°ΠΊΠΈΠ΅ Π°Π²ΡΠΎ- ΠΌΠΎΠ±ΠΈΠ»ΠΈ ΠΎΠ±ΠΎΠ·Π½Π°ΡΠ°ΡΡΡΡ ΠΊΠΎΠ»Π΅ΡΠ½ΠΎΠΉ ΡΠΎΡΠΌΡΠ»ΠΎΠΉ 4X2. ΠΠ΅ΡΠ²Π°Ρ ΡΠΈΡΡΠ° ΡΠΊΠ°Π·ΡΠ²Π°Π΅Ρ Π½Π° ΠΊΠΎΠ»ΠΈΡΠ΅ΡΡΠ²ΠΎ ΠΊΠΎΠ»Π΅Ρ Π½Π° ΠΌΠΎΡΡΠ°Ρ , Π° Π²ΡΠΎΡΠ°Ρ β Π½Π° ΠΊΠΎΠ»ΠΈΡΠ΅ΡΡΠ²ΠΎ Π²Π΅Π΄ΡΡΠΈΡ ΠΊΠΎΠ»Π΅Ρ. ΠΡΠΈ ΡΡΠΎΠΌ ΡΠΏΠ°ΡΠ΅Π½Π½ΡΠ΅ ΡΠΈΠ½Ρ Π½Π° ΠΌΠΎΡΡΠ°Ρ ΡΡΠΈΡΠ°ΡΡΡΡ ΠΎΠ΄Π½ΠΈΠΌ ΠΊΠΎΠ»Π΅ΡΠΎΠΌ. ΠΠ²ΡΠΎΠΌΠΎΠ±ΠΈΠ»ΠΈ Ρ Π΄Π²ΡΠΌΡ Π²Π΅Π΄ΡΡΠΈΠΌΠΈ ΠΌΠΎΡΡΠ°ΠΌΠΈ (ΠΏΠ΅ΡΠ΅Π΄Π½ΠΈΠΌ ΠΈ Π·Π°Π΄Π½ΠΈΠΌ), Ρ. Π΅. ΡΠΎ Π²ΡΠ΅ΠΌΠΈ Π²Π΅Π΄ΡΡΠΈΠΌΠΈ ΠΊΠΎΠ»Π΅ΡΠ°ΠΌΠΈ, ΠΎΠ±ΠΎΠ·Π½Π°ΡΠ°ΡΡΡΡ ΠΊΠΎΠ»Π΅ΡΠ½ΠΎΠΉ ΡΠΎΡΠΌΡΠ»ΠΎΠΉ 4X4. ΠΠ²ΡΠΎΠΌΠΎΠ±ΠΈΠ»ΠΈ Ρ ΡΡΠ΅ΠΌΡ ΠΌΠΎΡΡΠ°ΠΌΠΈ, ΠΈΠΌΠ΅ΡΡΠΈΠ΅ Π΄Π²Π° Π·Π°Π΄Π½ΠΈΡ Π²Π΅Π΄ΡΡΠΈΡ ΠΌΠΎΡΡΠ°, Ρ. Π΅. ΡΠΎ Π²ΡΠ΅ΠΌΠΈ Π²Π΅Π΄ΡΡΠΈΠΌΠΈ ΠΊΠΎΠ»Π΅ΡΠ°ΠΌΠΈ Π½Π° Π·Π°Π΄Π½Π΅ΠΉ ΡΠ΅Π»Π΅ΠΆΠΊΠ΅, ΠΈ ΡΠΏΡΠ°Π²Π»ΡΠ΅ΠΌΡΠΉ ΡΠΎΠ»ΡΠΊΠΎ ΠΏΠ΅ΡΠ΅Π΄Π½ΠΈΠΉ ΠΌΠΎΡΡ, Π½Π°Π·ΡΠ²Π°ΡΡΡΡ Π°Π²ΡΠΎΠΌΠΎΠ±ΠΈΠ»ΡΠΌΠΈ ΠΏΠΎΠ²ΡΡΠ΅Π½Π½ΠΎΠΉ ΠΏΡΠΎΡ ΠΎΠ΄ΠΈΠΌΠΎΡΡΠΈ ΠΈ ΠΎΠ±ΠΎΠ·Π½Π°ΡΠ°ΡΡΡΡ ΠΊΠΎΠ»Π΅ΡΠ½ΠΎΠΉ ΡΠΎΡΠΌΡΠ»ΠΎΠΉ 6X4. ΠΠ²ΡΠΎΠΌΠΎΠ±ΠΈΠ»ΠΈ Ρ ΡΡΠ΅ΠΌΡ Π²Π΅Π΄ΡΡΠΈΠΌΠΈ ΠΌΠΎΡΡΠ°ΠΌΠΈ Π½Π°Π·ΡΠ²Π°ΡΡΡΡ Π°Π²ΡΠΎΠΌΠΎΠ±ΠΈΠ»ΡΠΌΠΈ Π²ΡΡΠΎΠΊΠΎΠΉ ΠΏΡΠΎΡ ΠΎΠ΄ΠΈΠΌΠΎΡΡΠΈ ΠΈ ΠΎΠ±ΠΎΠ·Π½Π°ΡΠ°ΡΡΡΡ ΠΊΠΎΠ»Π΅ΡΠ½ΠΎΠΉ ΡΠΎΡΠΌΡΠ»ΠΎΠΉ 6X6. ΠΠ΅Ρ Π°Π½ΠΈΠ·ΠΌ ΡΠΏΡΠ°Π²Π»Π΅Π½ΠΈΡ ΡΠΎΡΡΠΎΠΈΡ ΠΈΠ· ΡΡΠ»Π΅Π²ΠΎΠ³ΠΎ ΡΠΏΡΠ°Π²Π»Π΅Π½ΠΈΡ ΠΈ ΡΠΎΡΠΌΠΎΠ·Π½ΠΎΠΉ ΡΠΈΡΡΠ΅ΠΌΡ. Π ΡΠ»Π΅Π²ΠΎΠ΅ ΡΠΏΡΠ°Π²Π»Π΅Π½ΠΈΠ΅ ΡΠ²ΡΠ·Π°Π½ΠΎ Ρ ΠΏΠ΅ΡΠ΅Π΄Π½ΠΈΠΌΠΈ ΠΊΠΎΠ»Π΅ΡΠ°ΠΌΠΈ ΠΈ ΡΠ»ΡΠΆΠΈΡ Π΄Π»Ρ ΠΈΠ·ΠΌΠ΅Π½Π΅Π½ΠΈΡ Π½Π°ΠΏΡΠ°Π²Π»Π΅Π½ΠΈΡ Π΄Π²ΠΈΠΆΠ΅Π½ΠΈΡ Π°Π²ΡΠΎΠΌΠΎΠ±ΠΈΠ»Ρ. ΠΠ½ΠΎ ΠΎΠ±ΠΎΡΡΠ΄ΠΎΠ²Π°Π½ΠΎ Π΄Π»Ρ Π»Π΅Π³ΠΊΠΎΡΡΠΈ ΡΠΏΡΠ°Π²Π»Π΅Π½ΠΈΡ Π³ΠΈΠ΄ΡΠΎΡΡΠΈΠ»ΠΈΡΠ΅Π»ΡΠΌΠΈ. Π’ΠΎΡΠΌΠΎΠ·Π½Π°Ρ ΡΠΈΡΡΠ΅ΠΌΠ° ΠΎΠ±Π΅ΡΠΏΠ΅ΡΠΈΠ²Π°Π΅Ρ ΡΠΌΠ΅Π½ΡΡΠ΅Π½ΠΈΠ΅ ΡΠΊΠΎΡΠΎΡΡΠΈ Π΄Π²ΠΈΠΆΠ΅Π½ΠΈΡ, Π±ΡΡΡΡΡΡ ΠΎΡΡΠ°Π½ΠΎΠ²ΠΊΡ Π°Π²ΡΠΎΠΌΠΎΠ±ΠΈΠ»Ρ ΠΈ Π·Π°ΡΠΎΡΠΌΠ°ΠΆΠΈΠ²Π°Π½ΠΈΠ΅ Π΅Π³ΠΎ Π½Π° ΠΌΠ΅ΡΡΠ΅. Π£ Π±ΠΎΡΡΠΎΠ²ΡΡ Π°Π²ΡΠΎΠΌΠΎΠ±ΠΈΠ»Π΅ΠΉ ΠΈ ΡΠ°ΠΌΠΎΡΠ²Π°Π»ΠΎΠ² ΠΈΠΌΠ΅Π΅ΡΡΡ ΠΎΡΠ΄Π΅Π»ΡΠ½Π°Ρ ΠΊΠ°Π±ΠΈΠ½Π° Π΄Π»Ρ Π²ΠΎΠ΄ΠΈΡΠ΅Π»Ρ ΠΈ Π΄Π²ΡΡ ΠΏΠ°ΡΡΠ°ΠΆΠΈΡΠΎΠ², Π° ΡΠ°ΠΊΠΆΠ΅ ΠΏΠ»Π°ΡΡΠΎΡΠΌΠ° Π΄Π»Ρ ΡΠ°Π·ΠΌΠ΅ΡΠ΅Π½ΠΈΡ Π³ΡΡΠ·Π°. ΠΠ° ΡΠ΅Π΄Π΅Π»ΡΠ½ΡΡ ΡΡΠ³Π°ΡΠ°Ρ Π²ΠΌΠ΅ΡΡΠΎ ΠΏΠ»Π°ΡΡΠΎΡΠΌΡ ΡΡΡΠ°Π½Π°Π²Π»ΠΈΠ²Π°Π΅ΡΡΡ ΡΠ΅Π΄Π΅Π»ΡΠ½ΠΎΠ΅ ΡΡΡΡΠΎΠΉΡΡΠ²ΠΎ, ΠΏΡΠ΅Π΄Π½Π°Π·Π½Π°ΡΠ΅Π½Π½ΠΎΠ΅ Π΄Π»Ρ Π±ΡΠΊΡΠΈΡΠΎΠ²ΠΊΠΈ ΠΏΠΎΠ»ΡΠΏΡΠΈΡΠ΅ΠΏΠ°.
ΠΠΎΡΡΠΎΠ²ΡΠ΅ Π°Π²ΡΠΎΠΌΠΎΠ±ΠΈΠ»ΠΈ-ΡΡΠ³Π°ΡΠΈ Ρ Π²Π΅Π΄ΡΡΠΈΠΌΠΈ ΠΊΠΎΠ»Π΅ΡΠ°ΠΌΠΈ Π·Π°Π΄Π½Π΅ΠΉ ΡΠ΅Π»Π΅ΠΆΠΊΠΈ (6X4) β ΠΠ°ΠΌΠΠ-5320 Π³ΡΡΠ·ΠΎΠΏΠΎΠ΄ΡΠ΅ΠΌΠ½ΠΎΡΡΡΡ 8 Ρ, ΠΠ°ΠΌΠΠ-53202 Π³ΡΡΠ·ΠΎΠΏΠΎΠ΄ΡΠ΅ΠΌΠ½ΠΎΡΡΡΡ 10 Ρ Ρ ΡΠ²Π΅Π»ΠΈΡΠ΅Π½Π½ΠΎΠΉ ΠΊΠΎΠ»Π΅ΡΠ½ΠΎΠΉ Π±Π°Π·ΠΎΠΉ, ΠΠ°ΠΌΠΠ-53212 Π³ΡΡΠ·ΠΎΠΏΠΎΠ΄ΡΠ΅ΠΌΠ½ΠΎΡΡΡΡ 10 Ρ ΠΈ ΠΠ°ΠΌΠΠ-53222 Π³ΡΡΠ·ΠΎΠΏΠΎΠ΄ΡΠ΅ΠΌΠ½ΠΎΡΡΡΡ 12 Ρ Ρ ΡΠ²Π΅Π»ΠΈΡΠ΅Π½Π½ΠΎΠΉ ΠΊΠΎΠ»Π΅ΡΠ½ΠΎΠΉ Π±Π°Π·ΠΎΠΉ ΠΈ ΡΡΠ΅Ρ ΠΌΠ΅ΡΡΠ½ΠΎΠΉ ΠΊΠ°Π±ΠΈΠ½ΠΎΠΉ ΡΠΎ ΡΠΏΠ°Π»ΡΠ½ΡΠΌ ΠΌΠ΅ΡΡΠΎΠΌ ΠΏΡΠ΅Π΄Π½Π°Π·Π½Π°ΡΠ΅Π½Ρ Π΄Π»Ρ Π±ΡΠΊΡΠΈΡΠΎΠ²ΠΊΠΈ ΠΏΡΠΈΡΠ΅ΠΏΠΎΠ², ΠΏΠΎΠ»Π½Π°Ρ ΠΌΠ°ΡΡΠ° ΠΊΠΎΡΠΎΡΡΡ ΡΠ°Π²Π½Π° ΡΠΎΠΎΡΠ²Π΅ΡΡΡΠ²Π΅Π½Π½ΠΎ 11,5; 14 ΠΈ 16 Ρ. ΠΡΠ΅ ΠΌΠ°ΡΠΈΠ½Ρ ΠΈ ΠΏΡΠΈΡΠ΅ΠΏΡ ΠΎΠ±ΠΎΡΡΠ΄ΠΎΠ²Π°Π½Ρ ΠΌΠ΅ΡΠ°Π»Π»ΠΈΡΠ΅ΡΠΊΠΈΠΌΠΈ ΠΏΠ»Π°ΡΡΠΎΡΠΌΠ°ΠΌΠΈ, Π±ΠΎΡΡΠ°ΠΌΠΈ Ρ ΡΠ°Π·Π±ΠΎΡΠ½ΡΠΌ ΠΊΠ°ΡΠΊΠ°ΡΠΎΠΌ ΠΈ ΡΠ΅Π½ΡΠ°ΠΌΠΈ.
Π‘Π΅Π΄Π΅Π»ΡΠ½ΡΠ΅ ΡΡΠ³Π°ΡΠΈ Ρ Π²Π΅Π΄ΡΡΠΈΠΌΠΈ ΠΊΠΎΠ»Π΅ΡΠ°ΠΌΠΈ Π·Π°Π΄Π½Π΅ΠΉ ΡΠ΅Π»Π΅ΠΆΠΊΠΈ (6Π₯4) β ΠΠ°ΠΌΠΠ-5410, ΠΠ°ΠΌΠΠ-54112 ΠΈ ΠΠ°ΠΌΠΠ-54122 β ΠΏΡΠ΅Π΄Π½Π°Π·Π½Π°ΡΠ΅Π½Ρ Π΄Π»Ρ Π±ΡΠΊΡΠΈΡΠΎΠ²ΠΊΠΈ ΠΏΠΎΠ»ΡΠΏΡΠΈΡΠ΅ΠΏΠΎΠ², ΠΏΠΎΠ»Π½Π°Ρ ΠΌΠ°ΡΡΠ° ΠΊΠΎΡΠΎΡΡΡ ΡΠ°Π²Π½Π° ΡΠΎΠΎΡΠ²Π΅ΡΡΡΠ²Π΅Π½Π½ΠΎ 19,1; 26 ΠΈ 29,5 Ρ. ΠΡΠ΅ ΡΠ΅Π΄Π΅Π»ΡΠ½ΡΠ΅ ΡΡΠ³Π°ΡΠΈ ΠΎΠ±ΠΎΡΡΠ΄ΠΎΠ²Π°Π½Ρ ΡΡΠ΅Ρ ΠΌΠ΅ΡΡΠ½ΠΎΠΉ ΠΊΠ°Π±ΠΈΠ½ΠΎΠΉ, Π° Ρ Π°Π²ΡΠΎΠΌΠΎΠ±ΠΈΠ»Π΅ΠΉ ΠΠ°ΠΌΠΠ-54112 ΠΈ ΠΠ°ΠΌΠΠ-54122 ΡΠ°Π·ΠΌΠ΅ΡΡ ΠΊΠ°Π±ΠΈΠ½ ΡΠ²Π΅Π»ΠΈΡΠ΅Π½Ρ Π½Π° Π²Π΅Π»ΠΈΡΠΈΠ½Ρ ΡΠΏΠ°Π»ΡΠ½ΠΎΠ³ΠΎ ΠΌΠ΅ΡΡΠ°. ΠΠ½Π΅ΡΠ½ΠΈΠΉ Π²ΠΈΠ΄ ΡΠ΅Π΄Π΅Π»ΡΠ½ΠΎΠ³ΠΎ ΡΡΠ³Π°ΡΠ° ΠΠ°ΠΌΠΠ-5410 ΠΏΠΎΠΊΠ°Π·Π°Π½ Π½Π° ΡΠΈΡ. 2.
Π ΠΈΡ. 2. ΠΠ½Π΅ΡΠ½ΠΈΠΉ Π²ΠΈΠ΄ ΡΠ΅Π΄Π΅Π»ΡΠ½ΠΎΠ³ΠΎ ΡΡΠ³Π°ΡΠ° ΠΠ°ΠΌΠΠ-5410
Π ΠΈΡ. 3. ΠΠ½Π΅ΡΠ½ΠΈΠΉ Π²ΠΈΠ΄ Π°Π²ΡΠΎΠΌΠΎΠ±ΠΈΠ»Ρ-ΡΠ°ΠΌΠΎΡΠ²Π°Π»Π° ΠΠ°ΠΌΠΠ-5511
ΠΠ²ΡΠΎΠΌΠΎΠ±ΠΈΠ»ΠΈ-ΡΠ°ΠΌΠΎΡΠ²Π°Π»Ρ Ρ Π²Π΅Π΄ΡΡΠΈΠΌΠΈ ΠΊΠΎΠ»Π΅ΡΠ°ΠΌΠΈ Π·Π°Π΄Π½Π΅ΠΉ ΡΠ΅Π»Π΅ΠΆΠΊΠΈ (6X4) ΠΠ°ΠΌΠΠ-5511 Π³ΡΡΠ·ΠΎΠΏΠΎΠ΄ΡΠ΅ΠΌΠ½ΠΎΡΡΡΡ 10 Ρ ΠΎΠ±ΠΎΡΡΠ΄ΠΎΠ²Π°Π½Ρ ΠΎΠΏΡΠΎΠΊΠΈΠ΄ΡΠ²Π°ΡΡΠΈΠΌΡΡ Π½Π°Π·Π°Π΄ ΠΊΠΎΠ²ΡΠ΅ΠΎΠ±ΡΠ°Π·Π½ΡΠΌ ΠΊΡΠ·ΠΎΠ²ΠΎΠΌ Π±Π΅Π· Π·Π°Π΄Π½Π΅Π³ΠΎ Π±ΠΎΡΡΠ° ΠΈ ΠΏΡΠ΅Π΄Π½Π°Π·Π½Π°ΡΠ΅Π½Ρ Π΄Π»Ρ ΠΏΠ΅ΡΠ΅Π²ΠΎΠ·ΠΊΠΈ ΠΏΡΠΎΠΌΡΡΠ»Π΅Π½Π½ΡΡ , ΡΡΡΠΎΠΈΡΠ΅Π»ΡΠ½ΡΡ ΠΈ ΡΠ΅Π»ΡΡΠΊΠΎΡ ΠΎΠ·ΡΠΉΡΡΠ²Π΅Π½Π½ΡΡ Π³ΡΡΠ·ΠΎΠ² (ΡΠΈΡ. 3).
1. Π’Π΅Ρ Π½ΠΈΡΠ΅ΡΠΊΠ°Ρ Ρ Π°ΡΠ°ΠΊΡΠ΅ΡΠΈΡΡΠΈΠΊΠ° Π°Π²ΡΠΎΠΌΠΎΠ±ΠΈΠ»Π΅ΠΉ ΠΠ°ΠΌΠΠ
ΠΠ°ΡΠ°ΠΌΠ΅ΡΡΡ |
ΠΠ΄ΠΈΠ½ΠΈΡΠ° ΠΈΠ·ΠΌΠ΅ΡΠ΅Π½ΠΈΡ |
ΠΠΎΠ΄Π΅Π»ΠΈ Π°Π²ΡΠΎΠΌΠΎΠ±ΠΈΠ»Π΅ΠΉ ΠΠ°ΠΌΠΠ |
||||
ΠΠΎΡΡΠΎΠ²ΡΠ΅ Π°Π²ΡΠΎΠΌΠΎΠ±ΠΈΠ»ΠΈ-ΡΡΠ³Π°ΡΠΈ |
Π‘Π΅Π΄Π΅Π»ΡΠ½ΡΠ΅ ΡΡΠ³Π°ΡΠΈ |
Π‘Π°ΠΌΠΎΡΠ²Π°Π»Ρ-5511 |
||||
5320 |
53212 |
5410 |
54112 |
|||
I. Π’Π΅Ρ Π½ΠΈΡΠ΅ΡΠΊΠΈΠ΅ |
||||||
ΠΠΎΠ»Π½Π°Ρ Π½Π°Π³ΡΡΠ·ΠΊΠ° |
ΠΊΠ³ |
8 000 |
10 000 |
β |
β |
10 000 |
ΠΠ°Π³ΡΡΠ·ΠΊΠ° Π½Π° ΡΠ΅Π΄Π΅Π»ΡΠ½ΠΎΠ΅ ΡΡΡΡΠΎΠΉΡΡΠ²ΠΎ |
ΠΊΠ³ |
β |
β |
8 100 |
11 350 |
β |
ΠΠ°ΡΡΠ° Π°Π²ΡΠΎΠΌΠΎΠ±ΠΈΠ»Ρ: |
||||||
Π½Π΅ΡΠ½Π°ΡΡΠΆΠ΅Π½Π½ΠΎΠ³ΠΎ |
ΠΊΠ³ |
6 735 |
7 795 |
6 390 |
6 690 |
8 630 |
ΡΠ½Π°ΡΡΠΆΠ΅Π½Π½ΠΎΠ³ΠΎ |
ΠΊΠ³ |
7 080 |
8 200 |
6 800 |
7 100 |
9 000 |
ΠΏΠΎΠ»Π½Π°Ρ |
ΠΊΠ³ |
15 305 |
18 425 |
15 125 |
18 675 |
19 150 |
ΠΠ°ΡΡΠ° ΠΏΡΠΈΡΠ΅ΠΏΠ° (ΠΏΠΎΠ»ΡΠΏΡΠΈΡΠ΅ΠΏΠ°) |
ΠΊΠ³ |
11 500 |
14 000 |
19 100 |
26 000 |
β |
ΠΠ°ΡΡΠ° Π°Π²ΡΠΎΠΏΠΎΠ΅Π·Π΄Π° |
ΠΊΠ³ |
26 805 |
32 425 |
26 125 |
33 825 |
β |
ΠΠ°Π±Π°ΡΠΈΡΠ½ΡΠ΅ ΡΠ°Π·ΠΌΠ΅ΡΡ: |
||||||
Π΄Π»ΠΈΠ½Π° |
ΠΌΠΌ |
7 435 |
8 530 |
6 180 |
6 180 |
7 130 |
ΡΠΈΡΠΈΠ½Π° |
ΠΌΠΌ |
2 500 |
2 500 |
2 500 |
2 500 |
2 500 |
Π²ΡΡΠΎΡΠ° ΠΏΠΎ ΠΊΠ°Π±ΠΈΠ½Π΅ |
ΠΌΠΌ |
2 630 |
2 630 |
2 630 |
2 630 |
2 630 |
ΠΠΎΠ»Π΅Ρ ΠΊΠΎΠ»Π΅Ρ: |
||||||
ΠΏΠ΅ΡΠ΅Π΄Π½ΠΈΡ |
ΠΌΠΌ |
2 026 |
2 026 |
2 026 |
2 026 |
2 026 |
Π·Π°Π΄Π½ΠΈΡ |
ΠΌΠΌ |
1 850 |
1 850 |
1 850 |
1 850 |
1 850 |
II. ΠΠΊΡΠΏΠ»ΡΠ°ΡΠ°ΡΠΈΠΎΠ½Π½ΡΠ΅ |
||||||
ΠΠ°ΠΊΡΠΈΠΌΠ°Π»ΡΠ½Π°Ρ ΡΠΊΠΎΡΠΎΡΡΡ Π΄Π²ΠΈΠΆΠ΅Π½ΠΈΡ |
ΠΊΠΌ/Ρ |
80β100 |
80β100 |
80β100 |
80β100 |
80β100 |
Π Π°Π΄ΠΈΡΡ ΠΏΠΎΠ²ΠΎΡΠΎΡΠ° |
ΠΌ |
8,5 |
9 |
8 |
8 |
8 |
ΠΠ²ΡΠΎΠΌΠΎΠ±ΠΈΠ»ΠΈ ΠΠ°ΠΌΠΠ-5315 ΠΈ ΠΠ°ΠΌΠΠ-5325 Π³ΡΡΠ·ΠΎΠΏΠΎΠ΄ΡΠ΅ΠΌΠ½ΠΎΡΡΡΡ 9 Ρ ΠΈΠΌΠ΅ΡΡ Π²ΠΌΠ΅ΡΡΠΎ Π΄Π²ΡΡ Π²Π΅Π΄ΡΡΠΈΡ ΠΌΠΎΡΡΠΎΠ² Π½Π° Π·Π°Π΄Π½Π΅ΠΉ ΡΠ΅Π»Π΅ΠΆΠΊΠ΅ ΠΎΠ΄ΠΈΠ½. ΠΡΠΏΠΎΠ»ΡΠ·ΡΡΡΡΡ ΡΠ°ΠΊΠΈΠ΅ Π°Π²ΡΠΎΠΌΠΎΠ±ΠΈΠ»ΠΈ Π΄Π»Ρ Π±ΡΠΊΡΠΈΡΠΎΠ²ΠΊΠΈ ΠΏΡΠΈΡΠ΅ΠΏΠΎΠ² ΠΌΠ°ΡΡΠΎΠΉ 12 Ρ.
ΠΠ° ΠΎΡΠ½ΠΎΠ²Π΅ Π±Π°Π·ΠΎΠ²ΡΡ Π°Π²ΡΠΎΠΌΠΎΠ±ΠΈΠ»Π΅ΠΉ ΡΠΎΠ·Π΄Π°Π½Ρ ΠΈ ΡΠΎΠ·Π΄Π°ΡΡΡΡ Π½ΠΎΠ²ΡΠ΅ ΠΌΠΎΠ΄Π΅Π»ΠΈ ΠΈ ΠΌΠΎΠ΄ΠΈΡΠΈΠΊΠ°ΡΠΈΠΉ, ΠΎΡΠ»ΠΈΡΠ°ΡΡΠΈΠ΅ΡΡ ΠΌΠΎΡΠ½ΠΎΡΡΡΠΌΠΈ, ΠΌΠ°ΡΡΠΎΠΉ, Π³Π°Π±Π°ΡΠΈΡΠ°ΠΌΠΈ, ΡΠΈΠΏΠ°ΠΌΠΈ ΠΊΠ°Π±ΠΈΠ½, Π²Π°ΡΠΈΠ°Π½ΡΠ°ΠΌΠΈ ΠΊΡΠ·ΠΎΠ²ΠΎΠ² ΠΈ ΠΎΠ±ΠΎΡΡΠ΄ΠΎΠ²Π°Π½ΠΈΡ. Π ΠΊΠΎΠ½ΡΡΡΡΠΊΡΠΈΠΈ Π°Π²ΡΠΎΠΌΠΎΠ±ΠΈΠ»Π΅ΠΉ ΠΈ ΡΠ΅Ρ Π½ΠΎΠ»ΠΎΠ³ΠΈΠΈ ΠΈΡ ΠΏΡΠΎΠΈΠ·Π²ΠΎΠ΄ΡΡΠ²Π° Π·Π°Π»ΠΎΠΆΠ΅Π½Ρ ΠΏΡΠΎΠ³ΡΠ΅ΡΡΠΈΠ²Π½ΡΠ΅ ΡΠ΅Ρ Π½ΠΈΡΠ΅ΡΠΊΠΈΠ΅ ΡΠ΅ΡΠ΅Π½ΠΈΡ, ΡΠΎΠΎΡΠ²Π΅ΡΡΡΠ²ΡΡΡΠΈΠ΅ ΡΠΎΠ²ΡΠ΅ΠΌΠ΅Π½Π½ΠΎΠΌΡ ΡΡΠΎΠ²Π½Ρ ΠΌΠΈΡΠΎΠ²ΠΎΠ³ΠΎ Π°Π²ΡΠΎΠΌΠΎΠ±ΠΈΠ»Π΅ΡΡΡΠΎΠ΅Π½ΠΈΡ ΠΈ ΠΎΠ±Π΅ΡΠΏΠ΅ΡΠΈΠ²Π°ΡΡΠΈΠ΅ Π²ΡΡΠΎΠΊΠΈΠ΅ ΡΠΊΡΠΏΠ»ΡΠ°ΡΠ°ΡΠΈΠΎΠ½Π½ΡΠ΅ ΠΊΠ°ΡΠ΅ΡΡΠ²Π°. Π’Π΅Ρ Π½ΠΈΡΠ΅ΡΠΊΠ°Ρ Ρ Π°ΡΠ°ΠΊΡΠ΅ΡΠΈΡΡΠΈΠΊΠ° Π±Π°Π·ΠΎΠ²ΡΡ Π°Π²ΡΠΎΠΌΠΎΠ±ΠΈΠ»Π΅ΠΉ ΠΠ°ΠΌΠΠ ΠΏΡΠ΅Π΄ΡΡΠ°Π²Π»Π΅Π½Π° Π² ΡΠ°Π±Π». 1. ΠΠ½Π°Π½ΠΈΠ΅ ΠΏΠ°ΡΠ°ΠΌΠ΅ΡΡΠΎΠ² ΠΏΠΎΠ·Π²ΠΎΠ»ΡΠ΅Ρ ΠΈΡ ΠΈΡΠΏΠΎΠ»ΡΠ·ΠΎΠ²Π°ΡΡ ΠΏΡΠΈ ΠΊΠΎΠ½ΡΡΠΎΠ»Π΅ ΡΠ΅Ρ Π½ΠΈΡΠ΅ΡΠΊΠΎΠ³ΠΎ ΡΠΎΡΡΠΎΡΠ½ΠΈΡ Π°Π²ΡΠΎΠΌΠΎΠ±ΠΈΠ»Ρ ΠΏΠΎΡΠ»Π΅ ΡΠ΅ΠΌΠΎΠ½ΡΠ° ΠΈ ΡΠ΅Ρ Π½ΠΈΡΠ΅ΡΠΊΠΎΠ³ΠΎ ΠΎΠ±ΡΠ»ΡΠΆΠΈΠ²Π°Π½ΠΈΡ.
ΠΠ²ΡΠΎΠΌΠΎΠ±ΠΈΠ»ΠΈ ΠΠ°ΠΌΠΠ ΠΈΠΌΠ΅ΡΡ ΠΊΡΠ°ΡΠΈΠ²ΡΠΉ Π²Π½Π΅ΡΠ½ΠΈΠΉ Π²ΠΈΠ΄. ΠΠ°ΠΆΠ΄ΡΠΉ ΡΠΈΠΏ ΠΈΠΌΠ΅Π΅Ρ ΡΠ²ΠΎΡ ΠΎΠΊΡΠ°ΡΠΊΡ: Π±ΠΎΡΡΠΎΠ²ΡΠ΅ ΡΡΠ³Π°ΡΠΈ β Π³ΠΎΠ»ΡΠ±ΡΡ, ΡΠ΅Π΄Π΅Π»ΡΠ½ΡΠ΅ β ΠΊΡΠ°ΡΠ½ΡΡ, ΡΠ°ΠΌΠΎΡΠ²Π°Π»Ρ β ΠΎΡΠ°Π½ΠΆΠ΅Π²ΡΡ.
everest-autokam.ru
Π£ΡΡΡΠΎΠΉΡΡΠ²ΠΎ Π°Π²ΡΠΎΠΌΠΎΠ±ΠΈΠ»Ρ ΠΠ°ΠΌΠΠ
Π‘ΠΎΠ΄Π΅ΡΠΆΠ°Π½ΠΈΠ΅
1. ΠΡΠΈΠ²ΠΎΡΠΈΠΏΠ½ΠΎ-ΡΠ°ΡΡΠ½Π½ΡΠΉ ΠΌΠ΅Ρ Π°Π½ΠΈΠ·ΠΌ
1.1 ΠΠ°Π·Π½Π°ΡΠ΅Π½ΠΈΠ΅, ΠΊΠΎΠ½ΡΡΡΡΠΊΡΠΈΡ ΠΈ ΠΌΠ°ΡΠ΅ΡΠΈΠ°Π» ΠΏΠΎΡΡΠ½Π΅Π²ΡΡ ΠΏΠ°Π»ΡΡΠ΅Π²
1.2 ΠΠ°ΠΊ ΡΠΈΠΊΡΠΈΡΡΡΡΡΡ ΠΏΠ°Π»ΡΡΡ ΠΎΡ ΠΎΡΠ΅Π²ΡΡ ΡΠΌΠ΅ΡΠ΅Π½ΠΈΠΉ
2. ΠΠ°ΡΠΎΡ ΡΠΈΡΡΠ΅ΠΌΡ ΠΎΡ Π»Π°ΠΆΠ΄Π΅Π½ΠΈΡ ΠΠ°ΠΌΠΠ-740
2.1 Π£ΡΡΡΠΎΠΉΡΡΠ²ΠΎ ΠΈ ΠΏΡΠΈΠ½ΡΠΈΠΏ Π΄Π΅ΠΉΡΡΠ²ΠΈΡ
2.2 ΠΠΏΠΈΡΠΈΡΠ΅ ΡΠΏΠ»ΠΎΡΠ½Π΅Π½ΠΈΡ Π²Π°Π»Π°
2.3 ΠΡΡΠ΅ΡΡΠΈΡΠ΅ ΡΡ Π΅ΠΌΡ ΡΠΏΠ»ΠΎΡΠ½Π΅Π½ΠΈΡ
3. Π‘ΠΈΡΡΠ΅ΠΌΠ° ΡΠΌΠ°Π·ΠΊΠΈ ΠΠΠ-4062
3.1 ΠΠ°Π·Π½Π°ΡΠ΅Π½ΠΈΠ΅ ΠΈ ΡΡΡΡΠΎΠΉΡΡΠ²ΠΎ
3.2 ΠΡΡΡ ΠΌΠ°ΡΠ»Π° ΠΎΡ Π½Π°ΡΠΎΡΠ° ΠΊ ΠΊΠ»Π°ΠΏΠ°Π½Π½ΠΎΠΌΡ ΡΠ·Π»Ρ ΠΠ Π
3.3 Π‘Ρ Π΅ΠΌΠ° ΡΠΌΠ°Π·ΠΊΠΈ Π½Π° ΠΏΠΎΠΏΠ΅ΡΠ΅ΡΠ½ΠΎΠΌ ΡΠ°Π·ΡΠ΅Π·Π΅ Π΄Π²ΠΈΠ³Π°ΡΠ΅Π»Ρ
4. ΠΠ°ΡΠ±ΡΡΠ°ΡΠΎΡ Π-151, ΡΠΈΡΡΠ΅ΠΌΠ° ΡΡΠΊΠΎΡΠΈΡΠ΅Π»ΡΠ½ΠΎΠ³ΠΎ Π½Π°ΡΠΎΡΠ°
4.1 ΠΠ°Π·Π½Π°ΡΠ΅Π½ΠΈΠ΅ ΠΈ ΡΡΡΡΠΎΠΉΡΡΠ²ΠΎ ΡΠΈΡΡΠ΅ΠΌΠ° ΡΡΠΊΠΎΡΠΈΡΠ΅Π»ΡΠ½ΠΎΠ³ΠΎ Π½Π°ΡΠΎΡΠ°
4.2 ΠΡΠΈΠ½ΡΠΈΠΏ Π΄Π΅ΠΉΡΡΠ²ΠΈΡ ΡΠΈΡΡΠ΅ΠΌΡ
4.3 ΠΠΎΠ·ΠΌΠΎΠΆΠ½ΡΠ΅ ΡΠ΅Π³ΡΠ»ΠΈΡΠΎΠ²ΠΊΠΈ ΡΠΈΡΡΠ΅ΠΌΡ
5. Π‘ΡΠ°ΡΡΠ΅ΡΠ½Π°Ρ Π°ΠΊΠΊΡΠΌΡΠ»ΡΡΠΎΡΠ½Π°Ρ Π±Π°ΡΠ°ΡΠ΅Ρ
5.1 ΠΠ΅ΡΠ΅ΡΠΈΡΠ»ΠΈΡΠ΅ ΠΎΡΠ½ΠΎΠ²Π½ΡΠ΅ Ρ Π°ΡΠ°ΠΊΡΠ΅ΡΠΈΡΡΠΈΠΊΠΈ Π±Π°ΡΠ°ΡΠ΅ΠΈ
5.2 ΠΠΌΠΊΠΎΡΡΡ Π±Π°ΡΠ°ΡΠ΅ΠΈ ΠΈ ΡΠ΅Ρ Π½ΠΎΠ»ΠΎΠ³ΠΈΡΠ΅ΡΠΊΠΈΠ΅ ΠΌΠ΅ΡΠΎΠΏΡΠΈΡΡΠΈΡ Π½Π° ΡΠ²Π΅Π»ΠΈΡΠ΅Π½ΠΈΠ΅ Π΅ΠΌΠΊΠΎΡΡΠΈ
Π‘ΠΏΠΈΡΠΎΠΊ ΠΈΡΠΏΠΎΠ»ΡΠ·ΠΎΠ²Π°Π½Π½ΠΎΠΉ Π»ΠΈΡΠ΅ΡΠ°ΡΡΡΡ
1. ΠΡΠΈΠ²ΠΎΡΠΈΠΏΠ½ΠΎ-ΡΠ°ΡΡΠ½Π½ΡΠΉ ΠΌΠ΅Ρ Π°Π½ΠΈΠ·ΠΌ
ΠΡΠΈΠ²ΠΎΡΠΈΠΏΠ½ΠΎ-ΡΠ°ΡΡΠ½Π½ΡΠΉ ΠΌΠ΅Ρ Π°Π½ΠΈΠ·ΠΌ (ΠΠ¨Π) ΡΠ»ΡΠΆΠΈΡ Π΄Π»Ρ ΠΏΡΠ΅ΠΎΠ±ΡΠ°Π·ΠΎΠ²Π°Π½ΠΈΡ ΠΏΠΎΡΡΡΠΏΠ°ΡΠ΅Π»ΡΠ½ΠΎΠ³ΠΎ Π΄Π²ΠΈΠΆΠ΅Π½ΠΈΡ ΠΏΠΎΡΡΠ½Ρ Π²ΠΎ Π²ΡΠ°ΡΠ°ΡΠ΅Π»ΡΠ½ΠΎΠ΅ Π΄Π²ΠΈΠΆΠ΅Π½ΠΈΠ΅ ΠΊΠΎΠ»Π΅Π½ΡΠ°ΡΠΎΠ³ΠΎ Π²Π°Π»Π°, ΠΈ Π½Π°ΠΎΠ±ΠΎΡΠΎΡ. ΠΠ΅ΡΠ°Π»ΠΈ ΠΠ¨Π Π΄Π΅Π»ΡΡ Π½Π° Π΄Π²Π΅ Π³ΡΡΠΏΠΏΡ, ΡΡΠΎ ΠΏΠΎΠ΄Π²ΠΈΠΆΠ½ΡΠ΅ ΠΈ Π½Π΅ΠΏΠΎΠ΄Π²ΠΈΠΆΠ½ΡΠ΅ Π΄Π΅ΡΠ°Π»ΠΈ:
β ΠΏΠΎΠ΄Π²ΠΈΠΆΠ½ΡΠ΅: ΠΏΠΎΡΡΠ΅Π½Ρ Ρ ΠΊΠΎΠ»ΡΡΠ°ΠΌΠΈ, ΠΏΠΎΡΡΠ½Π΅Π²ΠΎΠΉ ΠΏΠ°Π»Π΅Ρ , ΡΠ°ΡΡΠ½, ΠΊΠΎΠ»Π΅Π½ Π²Π°Π», ΠΌΠ°Ρ ΠΎΠ²ΠΈΠΊ.
β Π½Π΅ΠΏΠΎΠ΄Π²ΠΈΠΆΠ½ΡΠ΅: Π±Π»ΠΎΠΊ ΡΠΈΠ»ΠΈΠ½Π΄ΡΠΎΠ² β ΡΠ²Π»ΡΠ΅ΡΡΡ ΠΎΡΡΠΎΠ²ΠΎΠΌ Π΄.Π².Ρ., Π³ΠΎΠ»ΠΎΠ²ΠΊΠ° Π±Π»ΠΎΠΊΠ°, ΠΏΡΠΎΠΊΠ»Π°Π΄ΠΊΠ°, ΠΏΠΎΠ΄Π΄ΠΎΠ½ (ΠΊΠ°ΡΡΠ΅Ρ).
1.1 ΠΠ°Π·Π½Π°ΡΠ΅Π½ΠΈΠ΅, ΠΊΠΎΠ½ΡΡΡΡΠΊΡΠΈΡ ΠΈ ΠΌΠ°ΡΠ΅ΡΠΈΠ°Π» ΠΏΠΎΡΡΠ½Π΅Π²ΡΡ ΠΏΠ°Π»ΡΡΠ΅Π²
ΠΠΎΡΡΠ½Π΅Π²ΠΎΠΉ ΠΏΠ°Π»Π΅Ρ ΡΠΎΠ΅Π΄ΠΈΠ½ΡΠ΅Ρ ΠΏΠΎΡΡΠ΅Π½Ρ Ρ Π²Π΅ΡΡ Π½Π΅ΠΉ Π³ΠΎΠ»ΠΎΠ²ΠΊΠΎΠΉ ΡΠ°ΡΡΠ½Π° (ΡΠΈΡ.1).
ΠΠΎΡΡΠ½Π΅Π²ΠΎΠΉ ΠΏΠ°Π»Π΅Ρ ΡΠ»ΡΠΆΠΈΡ ΠΎΡΡΡ Π² ΡΠ°ΡΠ½ΠΈΡΠ½ΠΎΠΌ ΡΠΎΠ΅Π΄ΠΈΠ½Π΅Π½ΠΈΠΈ ΠΏΠΎΡΡΠ½Ρ Ρ ΡΠ°ΡΡΠ½ΠΎΠΌ ΠΈ Π²ΠΎΡΠΏΡΠΈΠ½ΠΈΠΌΠ°Π΅Ρ, ΠΏΠΎΡΡΠΎΠΌΡ Π²ΡΠ΅ ΠΏΠ΅ΡΠ΅Π΄Π°ΡΡΠΈΠ΅ΡΡ ΠΌΠ΅ΠΆΠ΄Ρ Π½ΠΈΠΌΠΈ ΡΠΈΠ»ΠΎΠ²ΡΠ΅ Π½Π°Π³ΡΡΠ·ΠΊΠΈ. Π ΡΠ΅ΡΡΡΠ΅Ρ ΡΠ°ΠΊΡΠ½ΡΡ Π΄Π²ΠΈΠ³Π°ΡΠ΅Π»ΡΡ ΡΠΈΠ»ΠΎΠ²ΡΠ΅ Π½Π°Π³ΡΡΠ·ΠΊΠΈ Π½Π° ΠΏΠΎΡΡΠ½Π΅Π²ΠΎΠΉ ΠΏΠ°Π»Π΅Ρ ΡΠ΅Π·ΠΊΠΎ ΠΈΠ·ΠΌΠ΅Π½ΡΡΡΡΡ ΠΊΠ°ΠΊ ΠΏΠΎ Π²Π΅Π»ΠΈΡΠΈΠ½Π΅, ΡΠ°ΠΊ ΠΈ ΠΏΠΎ Π½Π°ΠΏΡΠ°Π²Π»Π΅Π½ΠΈΡ, Π° Π² Π΄Π²ΡΡ ΡΠ°ΠΊΡΠ½ΡΡ β ΡΠΎΠ»ΡΠΊΠΎ ΠΏΠΎ Π²Π΅Π»ΠΈΡΠΈΠ½Π΅. ΠΠ΄Π½Π°ΠΊΠΎ Π² ΠΎΠ±ΠΎΠΈΡ ΡΠ»ΡΡΠ°ΡΡ ΠΏΠΎΡΡΠ½Π΅Π²ΡΠ΅ ΠΏΠ°Π»ΡΡΡ ΠΈΡΠΏΡΡΡΠ²Π°ΡΡ ΡΠ΄Π°ΡΠ½ΡΠΉ Ρ Π°ΡΠ°ΠΊΡΠ΅Ρ Π½Π°Π³ΡΡΠ·ΠΊΠΈ ΠΈ ΡΠ°Π±ΠΎΡΠ°ΡΡ Π² ΡΡΠ»ΠΎΠ²ΠΈΡΡ ΠΎΠ³ΡΠ°Π½ΠΈΡΠ΅Π½Π½ΠΎΠΉ ΡΠΌΠ°Π·ΠΊΠΈ.
Π°) Β«ΡΡΠ°ΠΊΠ°Π½Β» Π² Β«ΡΡΠ°ΠΊΠ°Π½Π΅Β» Π±) ΠΏΠΎΠΏΠ΅ΡΠ΅ΡΠ½ΡΠΉ ΡΠ°Π·ΡΠ΅Π·
Π ΠΈΡΡΠ½ΠΎΠΊ 1 β ΠΠ΄Π½ΠΎΡΠΈΠ»ΠΈΠ½Π΄ΡΠΎΠ²ΡΠΉ ΠΊΠ°ΡΠ±ΡΡΠ°ΡΠΎΡΠ½ΡΠΉ Π΄Π²ΠΈΠ³Π°ΡΠ΅Π»Ρ Π²Π½ΡΡΡΠ΅Π½Π½Π΅Π³ΠΎ ΡΠ³ΠΎΡΠ°Π½ΠΈΡ
1 β Π³ΠΎΠ»ΠΎΠ²ΠΊΠ° ΡΠΈΠ»ΠΈΠ½Π΄ΡΠ°; 2 β ΡΠΈΠ»ΠΈΠ½Π΄Ρ; 3 β ΠΏΠΎΡΡΠ΅Π½Ρ; 4 β ΠΏΠΎΡΡΠ½Π΅Π²ΡΠ΅ ΠΊΠΎΠ»ΡΡΠ°; 5 β ΠΏΠΎΡΡΠ½Π΅Π²ΠΎΠΉ ΠΏΠ°Π»Π΅Ρ;
6 β ΡΠ°ΡΡΠ½; 7 β ΠΊΠΎΠ»Π΅Π½ΡΠ°ΡΡΠΉ Π²Π°Π»; 8 β ΠΌΠ°Ρ ΠΎΠ²ΠΈΠΊ; 9 β ΠΊΡΠΈΠ²ΠΎΡΠΈΠΏ; 10 β ΡΠ°ΡΠΏΡΠ΅Π΄Π΅Π»ΠΈΡΠ΅Π»ΡΠ½ΡΠΉ Π²Π°Π»;
11 β ΠΊΡΠ»Π°ΡΠΎΠΊ ΡΠ°ΡΠΏΡΠ΅Π΄Π΅Π»ΠΈΡΠ΅Π»ΡΠ½ΠΎΠ³ΠΎ Π²Π°Π»Π°; 12 β ΡΡΡΠ°Π³; 13 β ΠΊΠ»Π°ΠΏΠ°Π½; 14 β ΡΠ²Π΅ΡΠ° Π·Π°ΠΆΠΈΠ³Π°Π½ΠΈΡ
Π ΠΊΡΠΈΠ²ΠΎΡΠΈΠΏΠ½ΠΎΠΌ ΠΌΠ΅Ρ Π°Π½ΠΈΠ·ΠΌΠ΅ Π±ΡΡΡΡΠΎΡ ΠΎΠ΄Π½ΡΡ Π΄Π²ΠΈΠ³Π°ΡΠ΅Π»Π΅ΠΉ ΠΏΠΎΡΡΠ½Π΅Π²ΡΠ΅ ΠΏΠ°Π»ΡΡΡ Π΄ΠΎΠ»ΠΆΠ½Ρ ΠΈΠΌΠ΅ΡΡ, Π²ΠΎΠ·ΠΌΠΎΠΆΠ½ΠΎ, ΠΌΠ΅Π½ΡΡΡΡ ΠΌΠ°ΡΡΡ, Π° ΠΏΠΎ ΠΊΠΎΠ½ΡΡΡΡΠΊΡΠΈΠ²Π½ΡΠΌ ΡΠΎΠΎΠ±ΡΠ°ΠΆΠ΅Π½ΠΈΡΠΌ ΠΈΡ Π²ΡΠΏΠΎΠ»Π½ΡΡΡ Ρ ΠΎΠ³ΡΠ°Π½ΠΈΡΠ΅Π½Π½ΡΠΌ ΠΏΠΎΠΏΠ΅ΡΠ΅ΡΠ½ΡΠΌ ΡΠ΅ΡΠ΅Π½ΠΈΠ΅ΠΌ ΠΈ ΠΌΠ°Π»ΡΠΌΠΈ ΠΎΠΏΠΎΡΠ½ΡΠΌΠΈ ΠΏΠΎΠ²Π΅ΡΡ Π½ΠΎΡΡΡΠΌΠΈ. ΠΡΠΎ ΠΏΠΎΡΠΎΠΆΠ΄Π°Π΅Ρ Π±ΠΎΠ»ΡΡΠΈΠ΅ Π½Π°ΠΏΡΡΠΆΠ΅Π½ΠΈΡ ΠΈ Π·Π½Π°ΡΠΈΡΠ΅Π»ΡΠ½ΡΠ΅ ΡΠ΄Π΅Π»ΡΠ½ΡΠ΅ Π΄Π°Π²Π»Π΅Π½ΠΈΡ Π½Π° ΠΎΠΏΠΎΡΠ½ΡΡ ΠΏΠΎΠ²Π΅ΡΡ Π½ΠΎΡΡΡΡ ΡΠ°ΡΡΠΌΠ°ΡΡΠΈΠ²Π°Π΅ΠΌΠΎΠ³ΠΎ ΡΠ°ΡΠ½ΠΈΡΠ½ΠΎΠ³ΠΎ ΡΠΎΠ΅Π΄ΠΈΠ½Π΅Π½ΠΈΡ, ΠΏΠΎΡΡΠΎΠΌΡ ΠΏΠΎΡΡΠ½Π΅Π²ΠΎΠΉ ΠΏΠ°Π»Π΅Ρ Π΄ΠΎΠ»ΠΆΠ΅Π½ ΠΎΠ±Π»Π°Π΄Π°ΡΡ Π²ΡΡΠΎΠΊΠΎΠΉ ΠΈΠ·Π½ΠΎΡΠΎΡΡΠΎΠΉΠΊΠΎΡΡΡΡ ΠΈ ΠΎΠ΄Π½ΠΎΠ²ΡΠ΅ΠΌΠ΅Π½Π½ΠΎ Ρ ΠΎΡΠΎΡΠΎ ΠΏΡΠΎΡΠΈΠ²ΠΎΡΡΠΎΡΡΡ Π΄Π΅ΠΉΡΡΠ²ΠΈΡ ΡΠ΄Π°ΡΠ½ΡΡ Π½Π°Π³ΡΡΠ·ΠΎΠΊ ΠΏΡΠΈ ΠΎΠ±ΡΠ΅ΠΉ ΠΎΠ³ΡΠ°Π½ΠΈΡΠ΅Π½Π½ΠΎΠΉ ΠΌΠ°ΡΡΠ΅.
Π§ΡΠΎΠ±Ρ ΡΠ΄ΠΎΠ²Π»Π΅ΡΠ²ΠΎΡΠΈΡΡ ΡΡΠΈΠΌ ΠΆΠ΅ΡΡΠΊΠΈΠΌ ΡΡΠ΅Π±ΠΎΠ²Π°Π½ΠΈΡΠΌ, ΠΏΠΎΡΡΠ½Π΅Π²ΡΠ΅ ΠΏΠ°Π»ΡΡΡ ΠΈΠ·Π³ΠΎΡΠΎΠ²Π»ΡΡΡ Π² Π²ΠΈΠ΄Π΅ ΠΏΠΎΠ»ΠΎΠ³ΠΎ ΡΠΈΠ»ΠΈΠ½Π΄ΡΠ° Ρ Π½Π΅Π±ΠΎΠ»ΡΡΠΎΠΉ ΡΠΎΠ»ΡΠΈΠ½ΠΎΠΉ ΡΡΠ΅Π½ΠΎΠΊ ΠΎΠ΄ΠΈΠ½Π°ΠΊΠΎΠ²ΠΎΠ³ΠΎ ΠΈΠ»ΠΈ ΠΏΠ΅ΡΠ΅ΠΌΠ΅Π½Π½ΠΎΠ³ΠΎ (ΠΏΡΠΈ Π½Π΅ΠΎΠ±Ρ ΠΎΠ΄ΠΈΠΌΠΎΡΡΠΈ) ΡΠ΅ΡΠ΅Π½ΠΈΡ ΠΏΠΎ ΠΎΡΠΈ (ΡΠΈΡ. 2) ΠΈ ΠΏΠΎΠ΄Π²Π΅ΡΠ³Π°ΡΡ ΠΈΡ ΡΠΎΠΎΡΠ²Π΅ΡΡΡΠ²ΡΡΡΠ΅ΠΉ ΡΠ΅ΡΠΌΠΈΡΠ΅ΡΠΊΠΎΠΉ ΠΎΠ±ΡΠ°Π±ΠΎΡΠΊΠ΅.
ΠΠΎΡΡΠ½Π΅Π²ΠΎΠΉ ΠΏΠ°Π»Π΅Ρ Π΄ΠΎΠ»ΠΆΠ΅Π½ Π±ΡΡΡ ΠΏΡΠΎΡΠ½ΡΠΌ, Π»Π΅Π³ΠΊΠΈΠΌ ΠΈ ΠΈΠ·Π½ΠΎΡΠΎΡΡΠΎΠΉΠΊΠΈΠΌ, ΡΠ°ΠΊ ΠΊΠ°ΠΊ Π²ΠΎ Π²ΡΠ΅ΠΌΡ ΡΠ°Π±ΠΎΡΡ ΠΏΠΎΠ΄Π²Π΅ΡΠ³Π°Π΅ΡΡΡ ΡΡΠ΅Π½ΠΈΡ ΠΈ Π±ΠΎΠ»ΡΡΠΈΠΌ ΠΌΠ΅Ρ Π°Π½ΠΈΡΠ΅ΡΠΊΠΈΠΌ Π½Π°Π³ΡΡΠ·ΠΊΠ°ΠΌ, ΠΏΠ΅ΡΠ΅ΠΌΠ΅Π½Π½ΡΠΌ ΠΏΠΎ Π²Π΅Π»ΠΈΡΠΈΠ½Π΅ ΠΈ Π½Π°ΠΏΡΠ°Π²Π»Π΅Π½ΠΈΡ. ΠΠ°Π»ΡΡΡ ΠΈΠ·Π³ΠΎΡΠΎΠ²Π»ΡΡΡ ΠΈΠ· Π²ΡΡΠΎΠΊΠΎΠΊΠ°ΡΠ΅ΡΡΠ²Π΅Π½Π½ΠΎΠΉ ΡΡΠ°Π»ΠΈ Π² Π²ΠΈΠ΄Π΅ ΠΏΡΡΡΠΎΡΠ΅Π»ΡΡ ΡΡΡΠ±ΠΎΠΊ. ΠΠ»Ρ ΠΏΠΎΠ²ΡΡΠ΅Π½ΠΈΡ Π½Π°Π΄Π΅ΠΆΠ½ΠΎΡΡΠΈ Π½Π°ΡΡΠΆΠ½ΡΡ ΠΏΠΎΠ²Π΅ΡΡ Π½ΠΎΡΡΡ ΠΏΠ°Π»ΡΡΠ° ΡΠ΅ΠΌΠ΅Π½ΡΠΈΡΡΡΡ ΠΈΠ»ΠΈ Π·Π°ΠΊΠ°Π»ΠΈΠ²Π°ΡΡ, Π° Π·Π°ΡΠ΅ΠΌ ΡΠ»ΠΈΡΡΡΡ ΠΈ ΠΏΠΎΠ»ΠΈΡΡΡΡ. ΠΠ°ΡΠ΅ΡΠΈΠ°Π»ΠΎΠΌ Π΄Π»Ρ ΠΏΠΎΡΡΠ½Π΅Π²ΡΡ ΠΏΠ°Π»ΡΡΠ΅Π² ΡΠ»ΡΠΆΠ°Ρ ΡΠ³Π»Π΅ΡΠΎΠ΄ΠΈΡΡΡΠ΅ ΡΡΠ°Π»ΠΈ ΠΌΠ°ΡΠΎΠΊ 15, 20 ΠΈΠ»ΠΈ 45, Π° Π² ΠΎΡΠΎΠ±Π΅Π½Π½ΠΎ Π½Π°ΠΏΡΡΠΆΠ΅Π½Π½ΡΡ Π΄Π²ΠΈΠ³Π°ΡΠ΅Π»ΡΡ ΠΏΡΠΈΠΌΠ΅Π½ΡΡΡ Ρ ΡΠΎΠΌΠΈΡΡΡΠ΅ β 20Π₯, 40Π₯, 12Π₯ΠΠΠ ΠΈ Π΄ΡΡΠ³ΠΈΠ΅ Π»Π΅Π³ΠΈΡΠΎΠ²Π°Π½Π½ΡΠ΅ ΡΡΠ°Π»ΠΈ.
Π ΠΈΡΡΠ½ΠΎΠΊ 2 β ΠΠΎΡΡΠ½Π΅Π²ΡΠ΅ ΠΏΠ°Π»ΡΡΡ
ΠΠ°Π»ΡΡΡ, ΠΈΠ·Π³ΠΎΡΠΎΠ²Π»Π΅Π½Π½ΡΠ΅ ΠΈΠ· ΠΌΠ°Π»ΠΎΡΠ³Π»Π΅ΡΠΎΠ΄ΠΈΡΡΡΡ ΡΡΠ°Π»Π΅ΠΉ, ΡΠΎΠ΄Π΅ΡΠΆΠ°ΡΠΈΡ Π΄ΠΎ 0,2% ΡΠ³Π»Π΅ΡΠΎΠ΄Π°, ΡΠ΅ΠΌΠ΅Π½ΡΠΈΡΡΡΡ, Ρ. Π΅. Π½Π°ΡΠ³Π»Π΅ΡΠΎΠΆΠΈΠ²Π°ΡΡ ΠΏΠΎΠ²Π΅ΡΡ Π½ΠΎΡΡΠ½ΡΠΉ ΠΈΡ ΡΠ»ΠΎΠΉ, ΠΈ ΠΏΠΎΠ΄Π²Π΅ΡΠ³Π°ΡΡ Π·Π°ΠΊΠ°Π»ΠΈΠ²Π°Π½ΠΈΡ. ΠΠ°Π»ΡΡΡ ΠΈΠ· ΡΡΠ΅Π΄Π½Π΅ΡΠ³Π»Π΅ΡΠΎΠ΄ΠΈΡΡΡΡ ΡΡΠ°Π»Π΅ΠΉ Π·Π°ΠΊΠ°Π»ΠΈΠ²Π°ΡΡ, Π½Π°Π³ΡΠ΅Π²Π°Ρ ΠΈΡ ΠΏΠΎΠ²Π΅ΡΡ Π½ΠΎΡΡΠ½ΡΠΉ ΡΠ»ΠΎΠΉ ΡΠΎΠΊΠ°ΠΌΠΈ Π²ΡΡΠΎΠΊΠΎΠΉ ΡΠ°ΡΡΠΎΡΡ. Π’ΠΎΠ»ΡΠΈΠ½Π° Π·Π°ΠΊΠ°Π»Π΅Π½Π½ΠΎΠ³ΠΎ ΡΠ»ΠΎΡ ΡΠΎΡΡΠ°Π²Π»ΡΠ΅Ρ 1β¦1,5 ΠΌΠΌ, Π° ΡΠ²Π΅ΡΠ΄ΠΎΡΡΡ HRC 55β¦62.
ΠΠΎΡΠ»Π΅ ΡΠ°ΠΊΠΎΠΉ ΡΠ΅ΡΠΌΠΈΡΠ΅ΡΠΊΠΎΠΉ ΠΎΠ±ΡΠ°Π±ΠΎΡΠΊΠΈ ΠΌΠ°ΡΠ΅ΡΠΈΠ°Π» ΠΏΠ°Π»ΡΡΠ° Ρ Π²Π½ΡΡΡΠ΅Π½Π½Π΅ΠΉ ΡΡΠΎΡΠΎΠ½Ρ ΡΡΠ΅Π½ΠΎΠΊ ΡΠΎΡ ΡΠ°Π½ΡΠ΅Ρ ΡΠ²ΠΎΠΈ Π²ΡΠ·ΠΊΠΈΠ΅ ΡΠ²ΠΎΠΉΡΡΠ²Π° ΠΈ Ρ ΠΎΡΠΎΡΠΎ ΡΠΎΠΏΡΠΎΡΠΈΠ²Π»ΡΠ΅ΡΡΡ ΡΠ΄Π°ΡΠ½ΡΠΌ Π½Π°Π³ΡΡΠ·ΠΊΠ°ΠΌ, Π° Π½Π°ΡΡΠΆΠ½ΡΠΉ Π·Π°ΠΊΠ°Π»Π΅Π½Π½ΡΠΉ ΡΠ»ΠΎΠΉ ΠΈΡ ΠΏΡΠΈΠΎΠ±ΡΠ΅ΡΠ°Π΅Ρ ΠΏΠΎΠ²ΡΡΠ΅Π½Π½ΡΡ ΠΈΠ·Π½ΠΎΡΠΎΡΡΠΎΠΉΠΊΠΎΡΡΡ. ΠΠ°Π»ΡΡΡ ΡΡΠ°ΡΠ΅Π»ΡΠ½ΠΎ ΡΠ»ΠΈΡΡΡΡ ΠΈ ΠΏΠΎΠ»ΠΈΡΡΡΡ, Ρ ΡΠ΅ΠΌ, ΡΡΠΎΠ±Ρ Π½Π° ΡΠ°Π±ΠΎΡΠ΅ΠΉ ΠΏΠΎΠ²Π΅ΡΡ Π½ΠΎΡΡΠΈ Π½Π΅ ΠΎΡΡΠ°Π²Π°Π»ΠΎΡΡ ΠΊΠ°ΠΊΠΈΡ -Π»ΠΈΠ±ΠΎ ΡΠΈΡΠΎΠΊ ΠΈΠ»ΠΈ ΡΠ»Π΅Π΄ΠΎΠ² ΠΎΠ±ΡΠ°Π±ΠΎΡΠΊΠΈ, Π²ΡΠ·ΡΠ²Π°ΡΡΠΈΡ ΠΊΠΎΠ½ΡΠ΅Π½ΡΡΠ°ΡΠΈΡ ΠΎΠΏΠ°ΡΠ½ΡΡ Π΄Π»Ρ ΠΏΡΠΎΡΠ½ΠΎΡΡΠΈ ΠΌΠ΅ΡΡΠ½ΡΡ Π½Π°ΠΏΡΡΠΆΠ΅Π½ΠΈΠΉ.
Π§ΡΠΎΠ±Ρ Π² ΠΏΡΠΎΡΠ΅ΡΡΠ΅ ΡΠ°Π±ΠΎΡΡ ΠΏΠΎΡΡΠ½Π΅Π²ΡΠ΅ ΠΏΠ°Π»ΡΡΡ Π½Π΅ Π²ΡΡ ΠΎΠ΄ΠΈΠ»ΠΈ ΠΈΠ· ΠΎΡΠ²Π΅ΡΡΡΠΈΠΉ Π±ΠΎΠ±ΡΡΠ΅ΠΊ ΠΈ Π½Π΅ ΠΌΠΎΠ³Π»ΠΈ ΠΏΠΎΠ²ΡΠ΅Π΄ΠΈΡΡ Π·Π΅ΡΠΊΠ°Π»ΠΎ ΡΠΈΠ»ΠΈΠ½Π΄ΡΠ°, ΠΈΡ ΡΠΈΠΊΡΠΈΡΡΡΡ Π² ΡΡΡΠΎΠ³ΠΎ Π·Π°Π΄Π°Π½Π½ΠΎΠΌ ΠΏΠΎΠ»ΠΎΠΆΠ΅Π½ΠΈΠΈ ΠΎΡΠ½ΠΎΡΠΈΡΠ΅Π»ΡΠ½ΠΎ ΡΠ°ΡΡΠ½Π° ΠΈΠ»ΠΈ ΠΏΠΎΡΡΠ½Ρ.
Π Π±ΠΎΠ±ΡΡΠΊΠ°Ρ ΠΏΠΎΡΡΠ½Ρ ΠΏΠ°Π»Π΅Ρ ΡΠΊΡΠ΅ΠΏΠ»Π΅Π½ ΡΡΠΎΠΏΠΎΡΠ½ΡΠΌΠΈ ΠΊΠΎΠ»ΡΡΠ°ΠΌΠΈ, ΡΠ΄Π΅ΡΠΆΠΈΠ²Π°ΡΡΠΈΠΌΠΈ Π΅Π³ΠΎ ΠΎΡ ΠΎΡΠ΅Π²ΠΎΠ³ΠΎ ΡΠΌΠ΅ΡΠ΅Π½ΠΈΡ. Π’Π°ΠΊΠΎΠΉ ΠΏΠ°Π»Π΅Ρ Π½Π°Π·ΡΠ²Π°ΡΡ ΠΏΠ»Π°Π²Π°ΡΡΠΈΠΌ, ΡΠ°ΠΊ ΠΊΠ°ΠΊ ΠΎΠ½ ΠΏΡΠΈ ΡΠ°Π±ΠΎΡΠ΅ Π΄Π²ΠΈΠ³Π°ΡΠ΅Π»Ρ ΠΌΠΎΠΆΠ΅Ρ ΠΏΠΎΠ²Π΅ΡΡΡΠ²Π°ΡΡΡΡ Π² Π²Π΅ΡΡ Π½Π΅ΠΉ Π³ΠΎΠ»ΠΎΠ²ΠΊΠ΅ ΡΠ°ΡΡΠ½Π° ΠΈ Π±ΠΎΠ±ΡΡΠΊΠ°Ρ ΠΏΠΎΡΡΠ½Ρ. ΠΠ»Π°Π²Π°ΡΡΠΈΠ΅ ΠΏΠΎΡΡΠ½Π΅Π²ΡΠ΅ ΠΏΠ°Π»ΡΡΡ ΡΠ°Π²Π½ΠΎΠΌΠ΅ΡΠ½Π΅Π΅ ΠΈΠ·Π½Π°ΡΠΈΠ²Π°ΡΡΡΡ ΠΈ ΠΏΠΎΡΡΠΎΠΌΡ Π΄ΠΎΠ»Π³ΠΎΠ²Π΅ΡΠ½Π΅Π΅.
Π£ ΡΠ°Π±ΠΎΡΠ°ΡΡΠ΅Π³ΠΎ Π΄Π²ΠΈΠ³Π°ΡΠ΅Π»Ρ ΠΏΠΎΡΡΠ΅Π½Ρ ΠΈΠ· Π°Π»ΡΠΌΠΈΠ½ΠΈΠ΅Π²ΠΎΠ³ΠΎ ΡΠΏΠ»Π°Π²Π° ΡΠ°ΡΡΠΈΡΡΠ΅ΡΡΡ Π±ΠΎΠ»ΡΡΠ΅, ΡΠ΅ΠΌ ΡΡΠ°Π»ΡΠ½ΠΎΠΉ ΠΏΠ°Π»Π΅Ρ, ΠΏΠΎΡΡΠΎΠΌΡ Π²ΠΎΠ·ΠΌΠΎΠΆΠ΅Π½ Π΅Π³ΠΎ ΡΡΡΠΊ Π² Π±ΠΎΠ±ΡΡΠΊΠ°Ρ ΠΏΠΎΡΡΠ½Ρ. ΠΠ»Ρ ΡΡΡΡΠ°Π½Π΅Π½ΠΈΡ ΡΡΠΎΠ³ΠΎ ΡΠ²Π»Π΅Π½ΠΈΡ ΠΏΠΎΡΡΠ΅Π½Ρ ΠΏΠ΅ΡΠ΅Π΄ ΡΠ±ΠΎΡΠΊΠΎΠΉ Ρ ΡΠ°ΡΡΠ½ΠΎΠΌ Π½Π°Π³ΡΠ΅Π²Π°ΡΡ Π΄ΠΎ 70-80Β° Π‘, Π° Π·Π°ΡΠ΅ΠΌ Π² ΠΏΠΎΡΡΠ΅Π½Ρ ΠΈ ΡΠ°ΡΡΠ½ Π²ΡΡΠ°Π²Π»ΡΡΡ ΠΏΠ°Π»Π΅Ρ. ΠΠΎΠ³Π΄Π° ΠΏΠΎΡΡΠ΅Π½Ρ ΠΎΡΡΡΠ½Π΅Ρ, ΠΏΠ°Π»Π΅Ρ Π² Π±ΠΎΠ±ΡΡΠΊΠ°Ρ ΠΎΠΊΠ°ΠΆΠ΅ΡΡΡ Π·Π°ΠΊΡΠ΅ΠΏΠ»Π΅Π½Π½ΡΠΌ Π½Π΅ΠΏΠΎΠ΄Π²ΠΈΠΆΠ½ΠΎ, Π° Π²Π΅ΡΡ Π½ΡΡ Π³ΠΎΠ»ΠΎΠ²ΠΊΠ° ΡΠ°ΡΡΠ½Π° Π±ΡΠ΄Π΅Ρ ΠΈΠΌΠ΅ΡΡ ΡΠ³Π»ΠΎΠ²ΠΎΠ΅ ΡΠΌΠ΅ΡΠ΅Π½ΠΈΠ΅ ΠΎΡΠ½ΠΎΡΠΈΡΠ΅Π»ΡΠ½ΠΎ Π½Π΅ΠΏΠΎΠ΄Π²ΠΈΠΆΠ½ΠΎΠ³ΠΎ ΠΏΠ°Π»ΡΡΠ°.
ΠΡΠΈ ΡΠ°Π±ΠΎΡΠ΅ Π΄Π²ΠΈΠ³Π°ΡΠ΅Π»Ρ ΠΏΠΎΡΡΠ΅Π½Ρ Π½Π°Π³ΡΠ΅Π²Π°Π΅ΡΡΡ ΠΈ ΠΏΠ°Π»Π΅Ρ ΠΏΠΎΠ»ΡΡΠ°Π΅Ρ Π²ΠΎΠ·ΠΌΠΎΠΆΠ½ΠΎΡΡΡ ΠΏΠΎΠ²Π΅ΡΡΡΠ²Π°ΡΡΡΡ Π²ΠΎΠΊΡΡΠ³ ΡΠ²ΠΎΠ΅ΠΉ ΠΎΡΠΈ. ΠΡΠΈΠΌΠ΅Π½ΡΡΡ ΠΏΠ°Π»ΡΡΡ, Π·Π°ΠΏΡΠ΅ΡΡΠΎΠ²Π°Π½Π½ΡΠ΅ Π² Π²Π΅ΡΡ Π½ΠΈΠ΅ Π³ΠΎΠ»ΠΎΠ²ΠΊΠΈ ΡΠ°ΡΡΠ½ΠΎΠ² (Π΄Π²ΠΈΠ³Π°ΡΠ΅Π»ΠΈ Π°Π²ΡΠΎΠΌΠΎΠ±ΠΈΠ»Π΅ΠΉ Β«ΠΠΈΠ³ΡΠ»ΠΈΒ»), Π’Π°ΠΊΠΈΠ΅ ΠΏΠ°Π»ΡΡΡ ΠΌΠΎΠ³ΡΡ ΠΏΠΎΠ²Π΅ΡΡΡΠ²Π°ΡΡΡΡ ΡΠΎΠ»ΡΠΊΠΎ Π² Π±ΠΎΠ±ΡΡΠΊΠ°Ρ ΠΏΠΎΡΡΠ½Ρ.
1.2 ΠΠ°ΠΊ ΡΠΈΠΊΡΠΈΡΡΡΡΡΡ ΠΏΠ°Π»ΡΡΡ ΠΎΡ ΠΎΡΠ΅Π²ΡΡ ΡΠΌΠ΅ΡΠ΅Π½ΠΈΠΉ?
ΠΠΎ ΡΠΏΠΎΡΠΎΠ±Ρ ΡΠΈΠΊΡΠ°ΡΠΈΠΈ ΠΈΡ ΠΏΠΎΠ΄ΡΠ°Π·Π΄Π΅Π»ΡΡΡ Π½Π° ΠΏΠ»Π°Π²Π°ΡΡΠΈΠ΅ ΠΈ Π·Π°ΠΊΡΠ΅ΠΏΠ»Π΅Π½Π½ΡΠ΅ . ΠΠΎΡΠ»Π΅Π΄Π½ΠΈΠ΅ Π½Π΅ΠΏΠΎΠ΄Π²ΠΈΠΆΠ½ΠΎ ΡΠΈΠΊΡΠΈΡΡΡΡ Π² Π³ΠΎΠ»ΠΎΠ²ΠΊΠ΅ ΡΠ°ΡΡΠ½Π° ΠΈΠ»ΠΈ Π² Π±ΠΎΠ±ΡΡΠΊΠ°Ρ ΠΏΠΎΡΡΠ½Ρ, ΠΏΠΎΡΡΠΎΠΌΡ ΡΠ³Π»ΠΎΠ²ΠΎΠ΅ ΠΏΠ΅ΡΠ΅ΠΌΠ΅ΡΠ΅Π½ΠΈΠ΅ ΠΎΠ½ΠΈ ΡΠΎΡ ΡΠ°Π½ΡΡΡ ΡΠΎΠ»ΡΠΊΠΎ Π² Π±ΠΎΠ±ΡΡΠΊΠ°Ρ (ΡΠΈΡ. 2, Π±) ΠΈΠ»ΠΈ Π² Π³ΠΎΠ»ΠΎΠ²ΠΊΠ΅ ΡΠ°ΡΡΠ½Π° (ΡΠΈΡ. 2, Π²).
Π ΡΠΎΠ²ΡΠ΅ΠΌΠ΅Π½Π½ΡΡ ΠΊΠΎΠ½ΡΡΡΡΠΊΡΠΈΡΡ Π½Π΅ΠΏΠΎΠ΄Π²ΠΈΠΆΠ½ΠΎΡΡΡ ΠΏΠ°Π»ΡΡΠ° ΠΎΡΠ½ΠΎΡΠΈΡΠ΅Π»ΡΠ½ΠΎ Π³ΠΎΠ»ΠΎΠ²ΠΊΠΈ ΡΠ°ΡΡΠ½Π° Π΄ΠΎΡΡΠΈΠ³Π°ΡΡ ΠΏΡΡΠ΅ΠΌ Π·Π°ΠΏΡΠ΅ΡΡΠΎΠ²ΠΊΠΈ ΠΏΠ°Π»ΡΡΠ° Π² Π³ΠΎΠ»ΠΎΠ²ΠΊΡ Ρ Π·Π°Π΄Π°Π½Π½ΡΠΌ Π½Π°ΡΡΠ³ΠΎΠΌ (Π½Π°ΠΏΡΠΈΠΌΠ΅Ρ, Π² Π΄Π²ΠΈΠ³Π°ΡΠ΅Π»ΡΡ ΠΠΠ Π½Π°ΡΡΠ³ ΡΠΎΡΡΠ°Π²Π»ΡΠ΅Ρ 0,01β¦0,042 ΠΌΠΌ ΠΏΡΠΈ Π΄ΠΈΠ°ΠΌΠ΅ΡΡΠ΅ ΠΏΠ°Π»ΡΡΠ° 22 ΠΌΠΌ).
ΠΡΠΈ Π½Π΅ΠΏΠΎΠ΄Π²ΠΈΠΆΠ½ΠΎΠΉ ΡΠΈΠΊΡΠ°ΡΠΈΠΈ ΠΏΠΎΡΡΠ½Π΅Π²ΡΡ ΠΏΠ°Π»ΡΡΠ΅Π² Π² ΡΠ°ΡΡΠ½Π΅ ΠΈΠ»ΠΈ Π±ΠΎΠ±ΡΡΠΊΠ°Ρ ΠΏΠΎΡΡΠ½Ρ ΠΎΡΠ΄Π΅Π»ΡΠ½ΡΠ΅ ΡΡΠ°ΡΡΠΊΠΈ ΠΈΡ Π½Π°Π³ΡΡΠΆΠ°ΡΡΡΡ Π½Π΅ΡΠ°Π²Π½ΠΎΠΌΠ΅ΡΠ½ΠΎ, Π°, ΡΠ»Π΅Π΄ΠΎΠ²Π°ΡΠ΅Π»ΡΠ½ΠΎ, ΠΈ Π½Π΅ΡΠ°Π²Π½ΠΎΠΌΠ΅ΡΠ½ΠΎ ΠΈΠ·Π½Π°ΡΠΈΠ²Π°ΡΡΡΡ. Π§ΡΠΎΠ±Ρ ΡΡΡΡΠ°Π½ΠΈΡΡ ΡΡΠΎΡ Π½Π΅Π΄ΠΎΡΡΠ°ΡΠΎΠΊ, ΠΏΡΠΈΠΌΠ΅Π½ΡΡΡ ΡΠ°ΠΊ Π½Π°Π·ΡΠ²Π°Π΅ΠΌΡΠ΅ ΠΏΠ»Π°Π²Π°ΡΡΠΈΠ΅ ΠΏΠ°Π»ΡΡΡ, ΠΊΠΎΡΠΎΡΡΠ΅ ΡΠΈΠΊΡΠΈΡΡΡΡ ΡΠΎΠ»ΡΠΊΠΎ ΠΎΡ ΠΎΡΠ΅Π²ΠΎΠ³ΠΎ ΡΠΌΠ΅ΡΠ΅Π½ΠΈΡ, ΠΊΠ°ΠΊ ΠΏΠΎΠΊΠ°Π·Π°Π½ΠΎ Π½Π° ΡΠΈΡ. 2, Π°, Π³.
Π ΠΏΡΠΎΡΠ΅ΡΡΠ΅ ΡΠ°Π±ΠΎΡΡ ΠΎΠ½ΠΈ ΠΌΠΎΠ³ΡΡ ΡΠ²ΠΎΠ±ΠΎΠ΄Π½ΠΎ ΠΏΠΎΠ²ΠΎΡΠ°ΡΠΈΠ²Π°ΡΡΡΡ, ΠΊΠ°ΠΊ Π² Π³ΠΎΠ»ΠΎΠ²ΠΊΠ΅ ΡΠ°ΡΡΠ½Π°, ΡΠ°ΠΊ ΠΈ Π² Π±ΠΎΠ±ΡΡΠΊΠ°Ρ ΠΏΠΎΡΡΠ½Ρ, ΡΡΠΎ ΡΠΏΠΎΡΠΎΠ±ΡΡΠ²ΡΠ΅Ρ Π±ΠΎΠ»Π΅Π΅ ΡΠ°Π²Π½ΠΎΠΌΠ΅ΡΠ½ΠΎΠΌΡ ΠΈΡ ΠΈΠ·Π½ΠΎΡΡ. Π Ρ ΠΎΠ»ΠΎΠ΄Π½ΠΎΠΌ ΡΠΎΡΡΠΎΡΠ½ΠΈΠΈ ΠΏΠ°Π»Π΅Ρ Π΄ΠΎΠ»ΠΆΠ΅Π½ ΠΏΠ»ΠΎΡΠ½ΠΎ Π±Π΅Π· ΠΊΠ°ΡΠΊΠΈ Π²Ρ ΠΎΠ΄ΠΈΡΡ Π² ΠΎΡΠ²Π΅ΡΡΡΠΈΠ΅ Π²ΡΡΠ»ΠΊΠΈ Π²Π΅ΡΡ Π½Π΅ΠΉ Π³ΠΎΠ»ΠΎΠ²ΠΊΠΈ ΡΠ°ΡΡΠ½Π°, Π° ΠΏΠΎ ΠΎΡΠ²Π΅ΡΡΡΠΈΡΠΌ Π² Π±ΠΎΠ±ΡΡΠΊΠ°Ρ ΠΏΠΎΡΡΠ½Ρ ΠΈΠ· Π°Π»ΡΠΌΠΈΠ½ΠΈΠ΅Π²ΡΡ ΡΠΏΠ»Π°Π²ΠΎΠ² Π΅Π³ΠΎ ΠΏΠΎΠ΄Π±ΠΈΡΠ°ΡΡ Ρ ΡΡΠ³ΠΎΠΉ ΠΏΠΎΡΠ°Π΄ΠΊΠΎΠΉ. ΠΠ΅ΠΎΠ±Ρ ΠΎΠ΄ΠΈΠΌΠΎΡΡΡ ΡΡΠΎΠ³ΠΎ ΠΎΠ±ΡΡΠ»ΠΎΠ²Π»ΠΈΠ²Π°Π΅ΡΡΡ ΡΠ°Π·Π½ΠΈΡΠ΅ΠΉ Π² ΠΊΠΎΡΡΡΠΈΡΠΈΠ΅Π½ΡΠ°Ρ Π»ΠΈΠ½Π΅ΠΉΠ½ΠΎΠ³ΠΎ ΡΠ°ΡΡΠΈΡΠ΅Π½ΠΈΡ Ρ Π°Π»ΡΠΌΠΈΠ½ΠΈΠ΅Π²ΡΡ ΠΏΠΎΡΡΠ½Π΅ΠΉ ΠΈ ΡΡΠ°Π»ΡΠ½ΡΡ ΠΏΠ°Π»ΡΡΠ΅Π².
ΠΠΏΡΡ ΠΏΠΎΠΊΠ°Π·ΡΠ²Π°Π΅Ρ, ΡΡΠΎ Π² ΠΏΡΠΎΠ³ΡΠ΅ΡΠΎΠΌ Π΄Π²ΠΈΠ³Π°ΡΠ΅Π»Π΅ Π·Π°Π·ΠΎΡΡ ΠΌΠ΅ΠΆΠ΄Ρ ΠΏΠΎΡΡΠ½Π΅Π²ΡΠΌ ΠΏΠ°Π»ΡΡΠ΅ΠΌ ΠΈ ΠΎΡΠ²Π΅ΡΡΡΠΈΡΠΌΠΈ Π² Π±ΠΎΠ±ΡΡΠΊΠ°Ρ ΠΈ Π³ΠΎΠ»ΠΎΠ²ΠΊΠ΅ ΡΠ°ΡΡΠ½Π° Π²ΡΡΠ°Π²Π½ΠΈΠ²Π°ΡΡΡΡ. ΠΠ»Ρ ΠΎΠ±Π»Π΅Π³ΡΠ΅Π½ΠΈΡ ΡΠ±ΠΎΡΠΊΠΈ Π°Π»ΡΠΌΠΈΠ½ΠΈΠ΅Π²ΡΠ΅ ΠΏΠΎΡΡΠ½ΠΈ ΡΠ΅ΠΊΠΎΠΌΠ΅Π½Π΄ΡΠ΅ΡΡΡ ΠΏΠΎΠ΄ΠΎΠ³ΡΠ΅Π²Π°ΡΡ Π΄ΠΎ 60β¦80 Β°Π‘ ΠΏΡΡΠ΅ΠΌ ΠΏΠΎΠ³ΡΡΠΆΠ΅Π½ΠΈΡ Π² Π³ΠΎΡΡΡΡΡ ΠΆΠΈΠ΄ΠΊΠΎΡΡΡ.
ΠΡΠ΅Π²ΡΡ ΡΠΈΠΊΡΠ°ΡΠΈΡ ΠΏΠ»Π°Π²Π°ΡΡΠΈΡ ΠΏΠ°Π»ΡΡΠ΅Π² ΠΎΡΡΡΠ΅ΡΡΠ²Π»ΡΡΡ Ρ ΠΏΠΎΠΌΠΎΡΡΡ ΡΡΠΎΠΏΠΎΡΠ½ΡΡ ΠΏΡΡΠΆΠΈΠ½Π½ΡΡ ΠΊΠΎΠ»Π΅Ρ ΠΊΡΡΠ³Π»ΠΎΠ³ΠΎ ΠΈΠ»ΠΈ ΠΏΡΡΠΌΠΎΡΠ³ΠΎΠ»ΡΠ½ΠΎΠ³ΠΎ ΡΠ΅ΡΠ΅Π½ΠΈΡ (ΡΠΈΡ. 2, Π°) ΠΈ ΡΠ΅ΠΆΠ΅ Π΄Π»Ρ ΡΡΠΎΠΉ ΡΠ΅Π»ΠΈ ΠΈΡΠΏΠΎΠ»ΡΠ·ΡΡΡ Π³ΡΠΈΠ±ΠΊΠΈ ΠΈΠ· ΠΌΡΠ³ΠΊΠΎΠ³ΠΎ ΠΌΠ΅ΡΠ°Π»Π»Π° (ΡΠΈΡ. 2, Π³).
Π‘ΡΠΎΠΏΠΎΡΠ½ΡΠ΅ ΠΊΠΎΠ»ΡΡΠ° ΡΡΡΠ°Π½Π°Π²Π»ΠΈΠ²Π°ΡΡ Π² ΠΊΠ°Π½Π°Π²ΠΊΠ°Ρ , ΠΏΡΠΎΡΠΎΡΠ΅Π½Π½ΡΡ Π΄Π»Ρ Π½ΠΈΡ Π² ΠΎΡΠ²Π΅ΡΡΡΠΈΡΡ Π±ΠΎΠ±ΡΡΠ΅ΠΊ, Π½Π΅ΡΡΡΠΈΡ ΠΏΠΎΡΡΠ½Π΅Π²ΠΎΠΉ ΠΏΠ°Π»Π΅Ρ. ΠΠ· ΠΊΠ°Π½Π°Π²ΠΎΠΊ ΠΈΡ Π²ΡΠ½ΠΈΠΌΠ°ΡΡ Ρ ΠΏΠΎΠΌΠΎΡΡΡ ΠΎΡΠΎΠ³Π½ΡΡΡΡ Π²Π½ΡΡΡΡ ΠΊΠΎΠ½ΡΠΎΠ² ΠΈΠ»ΠΈ ΠΈΠΌΠ΅ΡΡΠΈΡ ΡΡ Ρ Π½ΠΈΡ ΠΎΡΠ²Π΅ΡΡΡΠΈΠΉ (ΡΠΈΡ. 2, Π°). ΠΡΠΈΠ±ΠΊΠΈ, ΠΈΠ»ΠΈ Π·Π°Π³Π»ΡΡΠΊΠΈ, ΠΈΠ· ΠΌΡΠ³ΠΊΠΎΠ³ΠΎ ΠΌΠ΅ΡΠ°Π»Π»Π° (ΠΎΠ±ΡΡΠ½ΠΎ ΠΈΠ· Π°Π»ΡΠΌΠΈΠ½ΠΈΡ) Π·Π°ΠΏΡΠ΅ΡΡΠΎΠ²ΡΠ²Π°ΡΡ Ρ Π΄Π²ΡΡ ΡΡΠΎΡΠΎΠ½ Π² ΠΎΡΠ²Π΅ΡΡΡΠΈΡ ΠΏΠΎΡΡΠ½Π΅Π²ΠΎΠ³ΠΎ ΠΏΠ°Π»ΡΡΠ°.
ΠΡΠΈ ΠΎΡΠ΅Π²ΠΎΠΌ ΠΏΠ΅ΡΠ΅ΠΌΠ΅ΡΠ΅Π½ΠΈΠΈ Π³ΡΠΈΠ±ΠΊΠΈ ΠΏΠΎΡΡΠ½Π΅Π²ΠΎΠ³ΠΎ ΠΏΠ°Π»ΡΡΠ° ΡΠΎΠΏΡΠΈΠΊΠ°ΡΠ°ΡΡΡΡ Ρ Π·Π΅ΡΠΊΠ°Π»ΠΎΠΌ ΡΠΈΠ»ΠΈΠ½Π΄ΡΠ°, Π½ΠΎ Π½Π΅ ΡΠ°Π·ΡΡΡΠ°ΡΡ ΡΡΠ΅Π½ΠΎΠΊ. ΠΠΎΡΡΠ½Π΅Π²ΡΠ΅ ΠΏΠ°Π»ΡΡΡ Π΄Π²ΡΡ ΡΠ°ΠΊΡΠ½ΡΡ Π΄Π²ΠΈΠ³Π°ΡΠ΅Π»Π΅ΠΉ Ρ ΡΠΎΡΡΠΎΠ² Π·Π°ΠΊΡΡΠ²Π°ΡΡΡΡ ΠΈΠ½ΠΎΠ³Π΄Π° Π·Π°Π³Π»ΡΡΠΊΠ°ΠΌΠΈ, ΠΏΡΠ΅Π΄ΠΎΡΠ²ΡΠ°ΡΠ°ΡΡΠΈΠΌΠΈ Π²ΠΎΠ·ΠΌΠΎΠΆΠ½ΠΎΠ΅ ΠΏΠ΅ΡΠ΅ΡΠ΅ΠΊΠ°Π½ΠΈΠ΅ Π³Π°Π·ΠΎΠ² ΠΌΠ΅ΠΆΠ΄Ρ Π²ΠΏΡΡΠΊΠ½ΡΠΌΠΈ ΠΈ Π²ΡΠΏΡΡΠΊΠ½ΡΠΌΠΈ ΠΎΠΊΠ½Π°ΠΌΠΈ. ΠΡ ΠΎΡΠ΅Π²ΠΎΠ³ΠΎ ΠΏΠ΅ΡΠ΅ΠΌΠ΅ΡΠ΅Π½ΠΈΡ ΠΏΠ°Π»ΡΡΡ Π² ΡΡΠΈΡ Π΄Π²ΠΈΠ³Π°ΡΠ΅Π»ΡΡ ΡΠΈΠΊΡΠΈΡΡΡΡ ΡΡΠΎΠΏΠΎΡΠ½ΡΠΌΠΈ ΠΊΠΎΠ»ΡΡΠ°ΠΌΠΈ (ΡΠΈΡ. 2, Π΄).
Π’Π°ΠΊΠΈΠΌ ΠΎΠ±ΡΠ°Π·ΠΎΠΌ, ΠΏΠΎΡΡΠ½Π΅Π²ΡΠ΅ ΠΏΠ°Π»ΡΡΡ ΠΈΠ·Π³ΠΎΡΠΎΠ²Π»Π΅Π½Ρ ΠΈΠ· Ρ ΡΠΎΠΌΠΎΠ½ΠΈΠΊΠ΅Π»Π΅Π²ΠΎΠΉ ΡΡΠ°Π»ΠΈ Π² Π²ΠΈΠ΄Π΅ ΠΏΡΡΡΠΎΡΠ΅Π»ΡΡ ΡΠΈΠ»ΠΈΠ½Π΄ΡΠΈΡΠ΅ΡΠΊΠΈΡ ΡΡΠ΅ΡΠΆΠ½Π΅ΠΉ ΠΈ ΡΠΏΡΠΎΡΠ½Π΅Π½Ρ ΡΠ΅ΠΌΠ΅Π½ΡΠ°ΡΠΈΠ΅ΠΉ ΠΈ Π·Π°ΠΊΠ°Π»ΠΊΠΎΠΉ. ΠΡΠ΅Π²ΠΎΠ΅ ΠΏΠ΅ΡΠ΅ΠΌΠ΅ΡΠ΅Π½ΠΈΠ΅ ΠΏΠ°Π»ΡΡΠ° Π² ΠΏΠΎΡΡΠ½Π΅ ΠΎΠ³ΡΠ°Π½ΠΈΡΠ΅Π½ΠΎ ΡΡΠΎΠΏΠΎΡΠ½ΡΠΌΠΈ ΠΊΠΎΠ»ΡΡΠ°ΠΌΠΈ.
2. ΠΠ°ΡΠΎΡ ΡΠΈΡΡΠ΅ΠΌΡ ΠΎΡ Π»Π°ΠΆΠ΄Π΅Π½ΠΈΡ ΠΠ°ΠΌΠΠ-740.10
2.1 Π£ΡΡΡΠΎΠΉΡΡΠ²ΠΎ ΠΈ ΠΏΡΠΈΠ½ΡΠΈΠΏ Π΄Π΅ΠΉΡΡΠ²ΠΈΡ
Π ΡΠΈΡΡΠ΅ΠΌΡ ΠΎΡ Π»Π°ΠΆΠ΄Π΅Π½ΠΈΡ ΠΠ°ΠΌΠΠ-740 (ΡΠΈΡ.3) Π²Ρ ΠΎΠ΄ΡΡ Π²ΠΎΠ΄ΡΠ½ΡΠ΅ ΡΡΠ±Π°ΡΠΊΠΈ Π±Π»ΠΎΠΊΠ° ΠΈ Π³ΠΎΠ»ΠΎΠ²ΠΎΠΊ 26 ΡΠΈΠ»ΠΈΠ½Π΄ΡΠΎΠ², Π²ΠΎΠ΄ΡΠ½ΠΎΠΉ Π½Π°ΡΠΎΡ 27, ΡΠ°Π΄ΠΈΠ°ΡΠΎΡ 4, Π²Π΅Π½ΡΠΈΠ»
mirznanii.com
Π£ΡΡΡΠΎΠΉΡΡΠ²ΠΎ ΡΠ°ΠΌΠΎΠ³ΠΎ ΠΈΠ·Π²Π΅ΡΡΠ½ΠΎΠ³ΠΎ ΠΠ°ΠΌΠΠΠ° Π²ΠΎ Π²ΡΠ΅ΠΌ ΠΌΠΈΡΠ΅! (7 ΡΠΎΡΠΎ)
Π ΡΠΏΠΎΡΡΠΈΠ²Π½ΡΡ
Π³ΡΡΠ·ΠΎΠ²ΠΈΠΊΠ°Ρ
ΠΊΠΎΠΌΠ°Π½Π΄Ρ Β«ΠΠ°ΠΌΠ°Π·-ΠΠ°ΡΡΠ΅ΡΒ» ΠΈΠ·Π²Π΅ΡΡΠ½ΠΎ Π½Π΅ΠΌΠ½ΠΎΠ³ΠΎΠ΅: ΠΊΠ°ΠΊΠΎΠΉ Π΄Π²ΠΈΠ³Π°ΡΠ΅Π»Ρ ΡΡΡΠ°Π½ΠΎΠ²Π»Π΅Π½? Π΄ΠΎ ΠΊΠ°ΠΊΠΎΠΉ
ΡΠΊΠΎΡΠΎΡΡΠΈ ΡΠ°Π·Π³ΠΎΠ½ΡΡΡΡΡ? ΠΊΠ°ΠΊΠΈΠ΅ Π΄Π΅ΡΠ°Π»ΠΈ ΠΈΠΌΠΏΠΎΡΡΠ½ΡΠ΅, Π° ΠΊΠ°ΠΊΠΈΠ΅ ΠΎΡΠ΅ΡΠ΅ΡΡΠ²Π΅Π½Π½ΡΠ΅? Π ΡΡΠΎΠΉ ΡΡΠ°ΡΡΠ΅ Π²Ρ Π½Π°ΠΉΠ΄Π΅ΡΠ΅ Π²ΡΠ΅
ΠΎΡΠ²Π΅ΡΡ!
Π 1988 Π³ΠΎΠ΄Ρ, ΠΊΠΎΠ³Π΄Π° ΡΠΎΡΡΠΈΠΉΡΠΊΠΈΠ΅ Π³ΠΎΠ½ΡΠΈΠΊΠΈ ΡΠΎΠ»ΡΠΊΠΎ Π½Π°ΡΠ°Π»ΠΈ Π²ΡΡΡΡΠΏΠ°ΡΡ Π½Π° Π³ΡΡΠ·ΠΎΠ²ΠΈΠΊΠ°Ρ
Β«ΠΠ°ΠΌΠΠΒ», ΡΠ΅Ρ
Π½ΠΈΠΊΠ° Π±ΡΠ»Π°
ΡΠ°ΠΊΡΠΈΡΠ΅ΡΠΊΠΈ ΡΠ΅ΡΠΈΠΉΠ½ΠΎΠΉ: Π² ΠΊΠ°ΡΠ΅ΡΡΠ²Π΅ ΠΎΡΠ½ΠΎΠ²Ρ ΡΠΏΠΎΡΡΡΠΌΠ΅Π½Ρ Π²ΡΠ±ΡΠ°Π»ΠΈ ΡΡΠ΅Ρ
ΠΎΡΠ½ΡΠΉ ΠΏΠΎΠ»Π½ΠΎΠΏΡΠΈΠ²ΠΎΠ΄Π½ΠΈΠΊ Β«ΠΠ°ΠΌΠΠ-4310Β»,
ΠΊΠΎΡΠΎΡΠΎΠΌΡ ΡΠΎΡΡΠΈΡΠΎΠ²Π°Π»ΠΈ Π΄Π²ΠΈΠ³Π°ΡΠ΅Π»Ρ Π΄ΠΎ 290 Π».Ρ. (ΡΠ΅ΡΠΈΠΉΠ½Π°Ρ Β«Π²ΠΎΡΡΠΌΠ΅ΡΠΊΠ°Β» Π²ΡΠ΄Π°Π²Π°Π»Π° 210 Β«Π»ΠΎΡΠ°Π΄Π΅ΠΉΒ»), Π½Π΅ΠΌΠ½ΠΎΠ³ΠΎ
Π΄ΠΎΡΠ°Π±ΠΎΡΠ°Π»ΠΈ ΡΠΈΡΡΠ΅ΠΌΡ ΠΎΡ
Π»Π°ΠΆΠ΄Π΅Π½ΠΈΡ ΠΈ ΡΠΌΠ°Π·ΠΊΠΈ, ΡΡΡΠ°Π½ΠΎΠ²ΠΈΠ»ΠΈ ΠΊΠ°ΡΠΊΠ°Ρ Π±Π΅Π·ΠΎΠΏΠ°ΡΠ½ΠΎΡΡΠΈ, Π±ΠΎΠ»Π΅Π΅ ΠΆΠ΅ΡΡΠΊΠΈΠ΅ ΡΠ΅ΡΡΠΎΡΡ, Π½ΠΎΠ²ΡΠ΅
Π°ΠΌΠΎΡΡΠΈΠ·Π°ΡΠΎΡΡ ΠΈβ¦ Π²ΡΠ΅! Π ΡΠ°ΠΊΠΎΠΌ ΠΈΡΠΏΠΎΠ»Π½Π΅Π½ΠΈΠΈ Β«ΠΠ°ΠΌΠΠ-Π‘4310Β» (Β«Π‘Β» β ΡΠΏΠΎΡΡΠΈΠ²Π½ΡΠΉ) Π΄Π΅Π±ΡΡΠΈΡΠΎΠ²Π°Π» Π½Π° Π΅Π²ΡΠΎΠΏΠ΅ΠΉΡΠΊΠΎΠΌ
ΡΠ°Π»Π»ΠΈ Β«ΠΠ»ΡΡΒ», Π³Π΄Π΅ ΠΊΠ°ΠΌΠ°Π·ΠΎΠ²ΡΡ Π·Π°Π²ΠΎΠ΅Π²Π°Π»ΠΈ 2 ΠΈ 4 ΠΌΠ΅ΡΡΠ° Π»ΠΈΡΠ½ΠΎΠ³ΠΎ Π·Π°ΡΠ΅ΡΠ° ΠΈ 1 ΠΌΠ΅ΡΡΠΎ ΠΊΠΎΠΌΠ°Π½Π΄Π½ΠΎΠ³ΠΎ.
ΠΠ°Π»ΡΡΠ΅ Π½Π°ΡΠ°Π»Π°ΡΡ ΡΠ΅ΡΠ΅Π΄Π° ΠΏΠ΅ΡΠ΅Π΄Π΅Π»ΠΎΠΊ: ΠΊΠ°ΠΊΠΈΠ΅ ΡΠΎΠ»ΡΠΊΠΎ ΠΌΠΎΡΠΎΡΡ Π½Π΅ ΠΏΡΠΈΠΌΠ΅ΡΡΠ»ΠΈ Π³ΠΎΠ½ΠΎΡΠ½ΡΠ΅ Π³ΡΡΠ·ΠΎΠ²ΠΈΠΊΠΈ! Π 1989-ΠΌ β
ΡΠΎΡΡΠΈΡΠΎΠ²Π°Π½Π½ΡΠΉ Π΄ΠΎ 400 Β«Π»ΠΎΡΠ°Π΄Π΅ΠΉΒ» ΠΊΠ°ΠΌΠ°Π·ΠΎΠ²ΡΠΊΠΈΠΉ Π°Π³ΡΠ΅Π³Π°Ρ, Π² 1989-ΠΌ β ΠΎΠΏΡΡΠ½ΡΠΉ 10-ΡΠΈΠ»ΠΈΠ½Π΄ΡΠΎΠ²ΡΠΉ Π΄Π²ΠΈΠ³Π°ΡΠ΅Π»Ρ (ΠΎΠ½
ΠΎΠΊΠ°Π·Π°Π»ΡΡ ΡΠ»ΠΈΡΠΊΠΎΠΌ Π½Π΅Π½Π°Π΄Π΅ΠΆΠ½ΡΠΌ), Π² 1991-ΠΌ, Π½Π°ΠΊΠΎΠ½Π΅Ρ, ΠΏΠΎΡΠ²ΠΈΠ»Π°ΡΡ ΡΠΏΠ΅ΡΠΈΠ°Π»ΡΠ½ΠΎ ΡΠ°Π·ΡΠ°Π±ΠΎΡΠ°Π½Π½Π°Ρ Β«Π²ΠΎΡΡΠΌΠ΅ΡΠΊΠ°Β»
ΠΌΠΎΡΠ½ΠΎΡΡΡΡ 430 Π».Ρ. ΠΡΡΠ΅ΡΡΠ²Π΅Π½Π½ΠΎ, ΠΌΠΎΡΠ½ΡΠΉ Π΄Π²ΠΈΠ³Π°ΡΠ΅Π»Ρ ΠΏΠΎΡΡΠ΅Π±ΠΎΠ²Π°Π» ΡΡΡΠ΅ΡΡΠ²Π΅Π½Π½ΠΎΠΉ ΠΏΠ΅ΡΠ΅Π΄Π΅Π»ΠΊΠΈ ΡΡΠ°Π½ΡΠΌΠΈΡΡΠΈΠΈ: Π½Π°
Π·Π°Π²ΠΎΠ΄Π΅ ΠΈΠ·Π³ΠΎΡΠΎΠ²ΠΈΠ»ΠΈ ΡΠΊΡΠΏΠ΅ΡΠΈΠΌΠ΅Π½ΡΠ°Π»ΡΠ½ΡΡ ΠΊΠΎΡΠΎΠ±ΠΊΡ ΠΏΠ΅ΡΠ΅Π΄Π°Ρ ΠΈ Π½ΠΎΠ²ΡΡ ΡΠ°Π·Π΄Π°ΡΠΎΡΠ½ΡΡ ΠΊΠΎΡΠΎΠ±ΠΊΡ. Π’Π°ΠΊΠΆΠ΅ ΠΈΠ½ΠΆΠ΅Π½Π΅ΡΡ
ΡΡΠΎΠ²Π΅ΡΡΠ΅Π½ΡΡΠ²ΠΎΠ²Π°Π»ΠΈ ΠΏΠΎΠ΄Π²Π΅ΡΠΊΡ ΠΈ Π³ΠΈΠ΄ΡΠΎΡΡΠΈΠ»ΠΈΡΠ΅Π»Ρ, ΡΠ°Π·ΡΠ°Π±ΠΎΡΠ°Π»ΠΈ ΠΈ ΡΡΡΠ°Π½ΠΎΠ²ΠΈΠ»ΠΈ ΡΠΈΡΡΠ΅ΠΌΡ ΠΏΠΎΠ΄ΠΊΠ°ΡΠΊΠΈ ΡΠΈΠ½.
ΠΠ°ΠΌΠ΅ΡΠΈΠΌ, ΡΡΠΎ ΠΏΠ΅ΡΠ²ΡΠΌ ΠΈΠ½ΠΎΡΡΡΠ°Π½Π½ΡΠΌ ΠΊΠΎΠΌΠΏΠΎΠ½Π΅Π½ΡΠΎΠΌ, ΠΊΠΎΡΠΎΡΡΠΉ ΠΏΡΠΎΠΏΠΈΡΠ°Π»ΡΡ Π½Π° ΡΠΎΡΡΠΈΠΉΡΠΊΠΎΠΌ ΡΠΏΠΎΡΡΠΈΠ²Π½ΠΎΠΌ Π³ΡΡΠ·ΠΎΠ²ΠΈΠΊΠ΅
ΡΡΠ°Π»ΠΎ ΡΡΠ΅ΠΏΠ»Π΅Π½ΠΈΠ΅ Π±ΡΠΈΡΠ°Π½ΡΠΊΠΎΠ³ΠΎ ΠΏΡΠΎΠΈΠ·Π²ΠΎΠ΄ΡΡΠ²Π°, Ρ
ΠΎΡΡ Π΄Π°Π»ΡΡΠ΅ ΠΊΠ°ΠΌΠ°Π·ΠΎΠ²ΡΡ ΠΈΡΠΏΠΎΠ»ΡΠ·ΠΎΠ²Π°Π»ΠΈ Π±ΠΎΠ»ΡΡΠ΅ ΠΈ Π±ΠΎΠ»ΡΡΠ΅ ΠΈΠΌΠΏΠΎΡΡΠ½ΡΡ
Π·Π°ΠΏΡΠ°ΡΡΠ΅ΠΉβ¦ ΠΠ°ΠΏΡΠΈΠΌΠ΅Ρ, ΡΠ»Π΅Π΄ΡΡΡΠ΅Π΅ ΠΏΠΎΠΊΠΎΠ»Π΅Π½ΠΈΠ΅ Π³ΠΎΠ½ΠΎΡΠ½ΡΡ
Π³ΡΡΠ·ΠΎΠ²ΠΈΠΊΠΎΠ² (ΡΠΆΠ΅ Π΄Π²ΡΡ
ΠΎΡΠ½ΡΡ
!) ΠΏΠΎΠ»ΡΡΠΈΠ»ΠΎ Π°ΠΌΠ΅ΡΠΈΠΊΠ°Π½ΡΠΊΠΈΠΉ
Π΄Π²ΠΈΠ³Π°ΡΠ΅Π»Ρ Cummins ΠΌΠΎΡΠ½ΠΎΡΡΡΡ 520 Π».Ρ. ΠΠΏΡΠΎΡΠ΅ΠΌ, ΠΊΠΎΠ³Π΄Π° ΡΡΠΎΡΠ»Π°Π²ΡΠΊΠΈΠ΅ ΠΌΠΎΡΠΎΡΠΎΡΡΡΠΎΠΈΡΠ΅Π»ΠΈ ΠΏΡΠ΅Π΄Π»ΠΎΠΆΠΈΠ»ΠΈ ΡΠΈΠ»ΠΎΠ²ΠΎΠΉ
Π°Π³ΡΠ΅Π³Π°Ρ Π―ΠΠ-7Π846, ΠΊΠ°ΠΌΠ°Π·ΠΎΠ²ΡΡ Π²ΡΠ±ΡΠ°Π»ΠΈ ΡΠΎΡΡΠΈΠΉΡΠΊΠΈΠΉ ΡΡΡΠ±ΠΎΠ΄ΠΈΠ·Π΅Π»Ρ: ΠΎΠ½ ΠΏΠΎΠΊΠΎΡΠΈΠ» Π±ΠΎΠ»ΡΡΠΈΠΌ ΠΊΡΡΡΡΡΠΈΠΌ ΠΌΠΎΠΌΠ΅Π½ΡΠΎΠΌ Π½Π°
Π½ΠΈΠ·ΠΊΠΈΡ
ΠΎΠ±ΠΎΡΠΎΡΠ°Ρ
ΠΈ Ρ
ΠΎΡΠΎΡΠ΅ΠΉ ΡΠ°Π±ΠΎΡΠΎΠΉ Π½Π° Π½ΠΈΠ·ΠΊΠΎΡΠΎΡΡΠ½ΠΎΠΌ ΡΠΎΠΏΠ»ΠΈΠ²Π΅.
Π‘ ΡΠ°ΠΊΠΈΠΌ Π΄Π²ΠΈΠ³Π°ΡΠ΅Π»Π΅ΠΌ ΡΡΠ΅Π΄Π½Π΅ΠΌΠΎΡΠΎΡΠ½ΡΠΉ Β«ΠΠ°ΠΌΠΠ-49252Β» Π²ΡΠ½Π΅Ρ ΠΊΠ°ΠΌΠ°Π·ΠΎΠ²ΡΠ΅Π² Π½Π° ΠΏΠΎΠ±Π΅Π΄Π½ΡΠΉ ΠΏΠΎΠ΄ΠΈΡΠΌ ΠΌΠ°ΡΠ°ΡΠΎΠ½Π°
Β«ΠΠ°ΡΠΈΠΆ-ΠΠΎΡΠΊΠ²Π°-ΠΠ΅ΠΊΠΈΠ½Β» ΠΈ ΠΏΠΎΠ·Π²ΠΎΠ»ΠΈΠ» Π·Π°Π²ΠΎΠ΅Π²Π°ΡΡ Π·ΠΎΠ»ΠΎΡΠΎΠ³ΠΎ Π±Π΅ΡΠ±Π΅ΡΠ° Π½Π° Β«ΠΠ°ΠΊΠ°ΡΠ΅β96Β». ΠΠΎ Π·Π°ΡΠ΅ΠΌ Π³ΡΡΠ·ΠΎΠ²ΠΈΠΊΡ ΡΠ½ΠΎΠ²Π°
ΠΈΠΌΠΏΠ»Π°Π½ΡΠΈΡΠΎΠ²Π°Π»ΠΈ Π½ΠΎΠ²ΠΎΠ΅ ΡΠ΅ΡΠ΄ΡΠ΅: 12-ΡΠΈΠ»ΠΈΠ½Π΄ΡΠΎΠ²ΠΎΠ΅ ΠΌΠΎΡΠ½ΠΎΡΡΡΡ Π±ΠΎΠ»ΡΡΠ΅ ΡΡΡΡΡΠΈ Β«Π»ΠΎΡΠ°Π΄Π΅ΠΉΒ»! ΠΠ° Β«ΠΠ°ΠΊΠ°ΡΠ΅β98Β» ΡΠ°ΠΊΠΎΠΉ
Β«ΠΠ°ΠΌΠΠΒ» Π²ΡΡΡΡΠΏΠΈΠ» Π½Π΅ΡΠ΄Π°ΡΠ½ΠΎ, ΠΏΠΎΡΠΊΠΎΠ»ΡΠΊΡ ΠΎΠ³ΡΠΎΠΌΠ½ΡΡ ΠΌΠΎΡΠ½ΠΎΡΡΡ Π½Π΅ ΡΠΌΠΎΠ³Π»Π° Β«ΠΏΠ΅ΡΠ΅Π²Π°ΡΠΈΡΡΒ» ΡΡΠ°Π½ΡΠΌΠΈΡΡΠΈΡβ¦ ΠΡΠΎΡ
ΠΏΡΠΎΡΠΎΡΠΈΠΏ ΡΡΠ°Π» ΠΏΠΎΡΠ»Π΅Π΄Π½ΠΈΠΌ ΠΊΠ°ΠΌΡΠΊΠΈΠΌ Π³ΡΡΠ·ΠΎΠ²ΠΈΠΊΠΎΠΌ, Π³Π΄Π΅ Π΄Π²ΠΈΠ³Π°ΡΠ΅Π»Ρ ΡΠ°Π·ΠΌΠ΅ΡΠ°Π»ΡΡ ΠΏΠΎΡΠ΅ΡΠ΅Π΄ΠΈΠ½Π΅: Π½ΠΎΠ²ΡΠ΅ ΠΏΡΠ°Π²ΠΈΠ»Π°
ΠΌΠ°ΡΠ°ΡΠΎΠ½ΠΎΠ² Π·Π°ΡΡΠ°Π²ΠΈΠ»ΠΈ ΠΈΠ½ΠΆΠ΅Π½Π΅ΡΠΎΠ² ΡΠΏΠ΅ΡΠ½ΠΎ ΡΠΎΠ·Π΄Π°Π²Π°ΡΡ ΠΈ ΠΈΡΠΏΡΡΡΠ²Π°ΡΡ Π½ΠΎΠ²ΡΡ ΠΌΠ°ΡΠΈΠ½Ρ β Β«ΠΠ°ΠΌΠΠ-49256Β».
ΠΠΎΡΠ»Π΅ ΡΠΎΠ·Π΄Π°Π½Π½ΠΎΠΉ Π²ΠΏΠΎΠΏΡΡ
Π°Ρ
ΠΌΠΎΠ΄Π΅Π»ΠΈ 49256 ΠΏΠΎΡΠ²ΠΈΠ»ΡΡ ΡΠ½ΠΈΠΊΠ°Π»ΡΠ½ΡΠΉ Β«ΠΠ°ΠΌΠΠ-4911 ExtremeΒ» β ΠΌΠ°ΡΠΈΠ½Π°, ΠΊΠΎΡΠΎΡΠ°Ρ Π½Π΅
ΠΈΠΌΠ΅Π»Π° Π°Π½Π°Π»ΠΎΠ³ΠΎΠ² ΠΏΠΎ ΠΏΡΠΎΡ
ΠΎΠ΄ΠΈΠΌΠΎΡΡΠΈ, ΠΌΠ°Π½Π΅Π²ΡΠ΅Π½Π½ΠΎΡΡΠΈ ΠΈ Π΄ΠΈΠ½Π°ΠΌΠΈΠΊΠ΅. Β«Π‘ΠΎΡΠΎΠΊ Π΄Π΅Π²ΡΡΡ ΠΎΠ΄ΠΈΠ½Π½Π°Π΄ΡΠ°ΡΡΒ» ΡΡΠΏΠ΅Π»ΠΈ ΠΎΠΊΡΠ΅ΡΡΠΈΡΡ
Β«Π»Π΅ΡΠ°ΡΡΠΈΠΌ Π³ΡΡΠ·ΠΎΠ²ΠΈΠΊΠΎΠΌΒ»: ΡΡΠΎΡ ΠΌΠΎΠ½ΡΡΡ, ΠΎΡΡΠ°Π»ΠΊΠΈΠ²Π°ΡΡΡ ΠΎΡ Π΅ΡΡΠ΅ΡΡΠ²Π΅Π½Π½ΡΡ
ΡΡΠ°ΠΌΠΏΠ»ΠΈΠ½ΠΎΠ², ΡΡΡΠ΅ΠΊΡΠ½ΠΎ Π²Π·Π»Π΅ΡΠ°Π» Π½Π°Π΄
Π·Π΅ΠΌΠ»Π΅ΠΉ! Π Π΄Π΅Π±ΡΡΠ½ΠΎΠΌ 2003 Π³ΠΎΠ΄Ρ Π·Π° ΡΠΊΠΎΡΠΎΡΡΠ½ΡΠΌ Π±ΠΎΠ»ΡΡΠ΅Π³ΡΡΠ·ΠΎΠΌ ΠΎΡΡΠ°Π»ΠΈΡΡ ΠΏΠΎΠ±Π΅Π΄Ρ Π½Π° ΠΡΠ±ΠΊΠ΅ ΠΈ Π§Π΅ΠΌΠΏΠΈΠΎΠ½Π°ΡΠ΅ Π ΠΎΡΡΠΈΠΈ,
ΡΠ°Π»Π»ΠΈ Β«ΠΠ΅Π·Π΅ΡΡ Π§Π΅Π»Π»Π΅Π½Π΄ΠΆΒ», Β«Π₯Π°Π·Π°ΡΡΠΊΠΈΠ΅ ΡΡΠ΅ΠΏΠΈΒ», Β«ΠΠ°ΠΏΠΏΠ°Π΄ΠΎΠΊΠΈΡΒ», Π° Π³Π»Π°Π²Π½ΠΎΠ΅ β Π·ΠΎΠ»ΠΎΡΠΎΠΉ ΠΈ Π±ΡΠΎΠ½Π·ΠΎΠ²ΡΠΉ Π±Π΅ΡΠ±Π΅ΡΡ
Β«ΠΠ°ΠΊΠ°ΡΠ°Β». ΠΠΎΠΆΠ½ΠΎ Π»ΠΈ ΠΏΡΠΈΠ΄ΡΠΌΠ°ΡΡ ΠΌΠ°ΡΠΈΠ½Ρ Π»ΡΡΡΠ΅? Β«ΠΠΎΠΆΠ½ΠΎ!Β» β ΠΎΡΠ²Π΅ΡΠΈΠ»ΠΈ ΠΊΠ°ΠΌΠ°Π·ΠΎΠ²ΡΡ.
Π 2007 Π³ΠΎΠ΄Ρ ΡΠΎΠ΄ΠΈΠ»Π°ΡΡ Π½ΡΠ½Π΅ΡΠ½ΡΡ Π³Π΅Π½Π΅ΡΠ°ΡΠΈΡ ΡΠΏΠΎΡΡΠΈΠ²Π½ΡΡ
Π³ΡΡΠ·ΠΎΠ²ΠΈΠΊΠΎΠ² β Β«ΠΠ°ΠΌΠΠ-4326-9Β». ΠΠ° ΡΡΠΎΠΌ ΡΠΏΠΎΡΡΠΈΠ²Π½ΠΎΠΌ
Π³ΡΡΠ·ΠΎΠ²ΠΈΠΊΠ΅ ΡΡΡΠ°Π½ΠΎΠ²Π»Π΅Π½ ΡΠΎΡΡΠΈΠΉΡΠΊΠΈΠΉ Π΄Π²ΠΈΠ³Π°ΡΠ΅Π»Ρ Π―ΠΠ-7Π846 ΠΎΡΠ΅ΠΌΠΎΠΌ 18,47 Π». ΠΠ° ΡΡΠ΅Π½Π΄Π΅ 8-ΡΠΈΠ»ΠΈΠ½Π΄ΡΠΎΠ²ΡΠΉ V-ΠΎΠ±ΡΠ°Π·Π½ΡΠΉ
ΡΡΡΠ±ΠΎΠ΄ΠΈΠ·Π΅Π»Ρ ΡΠ°Π·Π²ΠΈΠ²Π°Π΅Ρ Π²Π½ΡΡΠΈΡΠ΅Π»ΡΠ½ΡΠ΅ 830 Π».Ρ. ΠΌΠΎΡΠ½ΠΎΡΡΠΈ ΠΈ 3500 ΠΒ·ΠΌ ΠΊΡΡΡΡΡΠ΅Π³ΠΎ ΠΌΠΎΠΌΠ΅Π½ΡΠ°. ΠΠΏΡΠΎΡΠ΅ΠΌ,
ΡΡΠΎΡΠ»Π°Π²ΡΠΊΠΈΠΉ ΡΡΡΠ±ΠΎΠΌΠΎΠ½ΡΡΡ Π½Π΅ΠΈΠ΄Π΅Π°Π»Π΅Π½: Π²ΠΎ-ΠΏΠ΅ΡΠ²ΡΡ
, ΠΏΡΠΎΠΆΠΎΡΠ»ΠΈΠ² (Π² Π³ΠΎΠ½ΠΊΠ΅ ΠΌΠΎΡΠΎΡ ΠΏΠΎΡΡΠ΅Π±Π»ΡΠ΅Ρ Π±ΠΎΠ»ΡΡΠ΅ 100 Π»ΠΈΡΡΠΎΠ²
ΡΠΎΠ»ΡΡΠΊΠΈ Π½Π° ΠΊΠ°ΠΆΠ΄ΡΠ΅ 100 ΠΊΠΈΠ»ΠΎΠΌΠ΅ΡΡΠΎΠ² ΠΏΡΠΎΠ±Π΅Π³Π°), Π²ΠΎ-Π²ΡΠΎΡΡΡ
, ΠΌΠ°ΡΡΠΈΠ²Π΅Π½ (1400 ΠΊΠ³), Π²-ΡΡΠ΅ΡΡΠΈΡ
, ΠΎΡΠ»ΠΈΡΠ°Π΅ΡΡΡ
ΡΠΊΡΠΎΠΌΠ½ΡΠΌ ΡΠ΅ΡΡΡΡΠΎΠΌ β Π΄ΠΎ ΡΠΏΠΈΡΠ°Π½ΠΈΡ Π΄Π²ΠΈΠ³Π°ΡΠ΅Π»Ρ ΠΏΡΠΎΡ
ΠΎΠ΄ΠΈΡ ΠΏΡΠΈΠΌΠ΅ΡΠ½ΠΎ 30 ΡΡΡΡΡ Π³ΠΎΠ½ΠΎΡΠ½ΡΡ
ΠΊΠΈΠ»ΠΎΠΌΠ΅ΡΡΠΎΠ².
ΠΡΡΠ°Π»ΡΠ½Π°Ρ ΠΌΠ΅Ρ
Π°Π½ΠΈΡΠ΅ΡΠΊΠ°Ρ Π½Π°ΡΠΈΠ½ΠΊΠ° Π³ΡΡΠ·ΠΎΠ²ΠΈΠΊΠΎΠ² ΠΊΠΎΠΌΠ°Π½Π΄Ρ Β«ΠΠ°ΠΌΠ°Π·-ΠΠ°ΡΡΠ΅ΡΒ» β ΡΠ±ΠΎΡΠ½Π°Ρ ΡΠΎΠ»ΡΠ½ΠΊΠ° ΠΈΠ· ΠΎΡΠ΅ΡΠ΅ΡΡΠ²Π΅Π½Π½ΡΡ
ΠΈ
ΠΈΠΌΠΏΠΎΡΡΠ½ΡΡ
Π°Π³ΡΠ΅Π³Π°ΡΠΎΠ²: ΡΡΠ΅ΠΏΠ»Π΅Π½ΠΈΠ΅ β Π°Π½Π³Π»ΠΈΠΉΡΠΊΠΎΠ΅ SACHS, ΠΊΠΎΡΠΎΠ±ΠΊΠ° ΠΏΠ΅ΡΠ΅Π΄Π°Ρ β Π½Π΅ΠΌΠ΅ΡΠΊΠ°Ρ 16-ΡΡΡΠΏΠ΅Π½ΡΠ°ΡΠ°Ρ ZF,
ΡΠ°Π·Π΄Π°ΡΠΎΡΠ½Π°Ρ ΠΊΠΎΡΠΎΠ±ΠΊΠ° β Π°Π²ΡΡΡΠΈΠΉΡΠΊΠ°Ρ Steyr, ΠΊΠ°ΡΠ΄Π°Π½Π½Π°Ρ ΠΏΠ΅ΡΠ΅Π΄Π°ΡΠ° β ΡΡΡΠ΅ΡΠΊΠ°Ρ Tirsan Kardan. ΠΡΠ»ΠΈ ΡΠ°Π½ΡΡΠ΅
ΡΡΡΠ°Π½Π°Π²Π»ΠΈΠ²Π°Π»ΠΈΡΡ ΡΡΠΆΠ΅Π»ΡΠ΅ ΠΊΠ°ΠΌΠ°Π·ΠΎΠ²ΡΠΊΠΈΠ΅ ΠΌΠΎΡΡΡ, ΡΠΎ ΡΠ΅ΠΏΠ΅ΡΡ Π³ΠΎΠ½ΠΎΡΠ½ΡΠ΅ Π³ΡΡΠ·ΠΎΠ²ΠΈΠΊΠΈ ΠΏΠΎΠ»ΡΡΠΈΠ»ΠΈ ΡΠΈΠ½ΡΠΊΠΈΠ΅ ΠΌΠΎΡΡΡ Sisu,
ΠΏΡΠ°Π²Π΄Π°, Π²ΠΌΠ΅ΡΡΠΎ ΡΡΠ°ΡΠ½ΡΡ
Π΄ΠΈΡΠΊΠΎΠ²ΡΡ
ΡΠΎΡΠΌΠΎΠ·ΠΎΠ² ΡΠΌΠΎΠ½ΡΠΈΡΠΎΠ²Π°Π½Ρ ΠΎΡΠ΅ΡΠ΅ΡΡΠ²Π΅Π½Π½ΡΠ΅ Π±Π°ΡΠ°Π±Π°Π½Π½ΡΠ΅ (ΠΏΡΠΈΠ²ΠΎΠ΄ ΡΠΎΡΠΌΠΎΠ·Π½ΡΡ
ΠΌΠ΅Ρ
Π°Π½ΠΈΠ·ΠΌΠΎΠ² β ΠΎΡ Π±Π΅Π»ΡΠ³ΠΈΠΉΡΠΊΠΎΠΉ ΠΊΠΎΠΌΠΏΠ°Π½ΠΈΠΈ Wabco). Π¨ΠΈΠ½Ρ β ΠΏΡΠΎΠ²Π΅ΡΠ΅Π½Π½ΡΠ΅ Π³ΠΎΠ½ΠΊΠ°ΠΌΠΈ Michelin 14.00 R20XZL.
ΠΡΡΠ°ΡΠΈ, ΠΌΠ°ΡΠΈΠ½Π° ΡΠ΅ΠΌΠΈΠΊΡΠ°ΡΠ½ΠΎΠ³ΠΎ ΠΏΠΎΠ±Π΅Π΄ΠΈΡΠ΅Π»Ρ Β«ΠΠ°ΠΊΠ°ΡΠ°Β» ΠΠ»Π°Π΄ΠΈΠΌΠΈΡΠ° Π§Π°Π³ΠΈΠ½Π° ΠΎΡΠ»ΠΈΡΠ°Π΅ΡΡΡ ΠΎΡ ΠΎΡΡΠ°Π»ΡΠ½ΡΡ Π³ΡΡΠ·ΠΎΠ²ΠΈΠΊΠΎΠ²
Β«ΡΠΈΠ½Π΅ΠΉ Π°ΡΠΌΠ°Π΄ΡΒ»: Π΅ΡΠ»ΠΈ Β«ΠΎΠ±ΡΡΠ½ΡΠΉΒ» Π³ΠΎΠ½ΠΎΡΠ½ΡΠΉ Β«ΠΠ°ΠΌΠΠΒ» ΡΡΠΎΠΈΡ ΠΎΠΊΠΎΠ»ΠΎ 200 ΡΡΡΡΡ Π΅Π²ΡΠΎ, ΡΠΎ ΡΡΠΎΠΈΠΌΠΎΡΡΡ 900-ΡΠΈΠ»ΡΠ½ΠΎΠ³ΠΎ
ΡΠ°Π³ΠΈΠ½ΡΠΊΠΎΠ³ΠΎ Π°Π²ΡΠΎΠΌΠΎΠ±ΠΈΠ»Ρ β 680 ΡΡΡΡΡ Π΅Π²ΡΠΎ! ΠΡΠΊΡΠ΄Π° Π½Π°Π±Π΅ΠΆΠ°Π»Π° ΡΠ°ΠΊΠ°Ρ ΡΠ°Π·Π½ΠΈΡΠ°? ΠΠ· Π²ΡΠ΅Ρ ΡΠΎΠ·Π΄Π°Π½Π½ΡΡ ΠΊΠΎΠΌΠ°Π½Π΄ΠΎΠΉ
Β«ΠΠ°ΠΌΠ°Π·-ΠΠ°ΡΡΠ΅ΡΒ» Π³ΡΡΠ·ΠΎΠ²ΠΈΠΊΠΎΠ² ΡΡΠΎΡ β ΡΠ°ΠΌΡΠΉ Π»Π΅Π³ΠΊΠΈΠΉ ΠΈ ΡΠ°ΠΌΡΠΉ Π±ΡΡΡΡΡΠΉ: ΠΌΠ°ΠΊΡΠΈΠΌΠ°Π»ΡΠ½Π°Ρ ΡΠΊΠΎΡΠΎΡΡΡ ΡΠΎΡΡΠ°Π²Π»ΡΠ΅Ρ 180
ΠΊΠΌ/Ρ, Π° ΡΠ°Π·Π³ΠΎΠ½ Π΄ΠΎ 100 ΠΊΠΌ/Ρ Π·Π°Π½ΠΈΠΌΠ°Π΅Ρ ΠΌΠ΅Π½ΡΡΠ΅ 10 ΡΠ΅ΠΊΡΠ½Π΄. Π Π²ΠΎΡ Π²ΠΈΠ·ΡΠ°Π»ΡΠ½ΠΎ ΠΌΠ°ΡΠΈΠ½Π° Π§Π°Π³ΠΈΠ½Π° ΠΎΡΠ»ΠΈΡΠ°Π΅ΡΡΡ ΡΠΎΠ»ΡΠΊΠΎ
ΠΌΠ°Π»Π΅Π½ΡΠΊΠΈΠΌΠΈ ΠΊΡΠ΅Π½ΠΎΠ½ΠΎΠ²ΡΠΌΠΈ ΡΠ°ΡΠ°ΠΌΠΈ, Π° ΡΠ°ΠΊΠΆΠ΅ ΠΊΠ°Π±ΠΈΠ½ΠΎΠΉ, ΠΌΠ°ΠΊΡΠΈΠΌΠ°Π»ΡΠ½ΠΎ ΡΠ΄Π²ΠΈΠ½ΡΡΠΎΠΉ Π²ΠΏΠ΅ΡΠ΅Π΄.
Π§ΡΠΎ Π±ΡΠ΄Π΅Ρ Π΄Π°Π»ΡΡΠ΅? Π‘ΠΎΠ²ΡΠ΅ΠΌ Π½Π΅Π΄Π°Π²Π½ΠΎ ΠΊΠ°ΠΌΠ°Π·ΠΎΠ²ΡΡ ΡΠ΅ΡΡΠΈΡΠΎΠ²Π°Π»ΠΈ Π°ΠΌΠ΅ΡΠΈΠΊΠ°Π½ΡΠΊΠΈΠ΅ ΠΌΠΎΡΠΎΡΡ Cummins, Π½ΠΎ ΠΏΠΎΠΊΠ°
Π°Π»ΡΡΠ΅ΡΠ½Π°ΡΠΈΠ²Ρ ΡΡΠΎΡΠ»Π°Π²ΡΠΊΠΎΠΌΡ Π΄Π²ΠΈΠ³Π°ΡΠ΅Π»Ρ Π½Π΅Ρ. ΠΡΠ΅ ΠΈΠ½ΠΆΠ΅Π½Π΅ΡΡ ΠΊΠΎΠΌΠ°Π½Π΄Ρ Π·Π°Π½ΠΈΠΌΠ°ΡΡΡΡ ΡΠ½ΠΈΠΆΠ΅Π½ΠΈΠ΅ΠΌ ΠΌΠ°ΡΡΡ Π³ΡΡΠ·ΠΎΠ²ΠΈΠΊΠΎΠ²
(ΡΠ΅ΠΉΡΠ°Ρ ΠΌΠ°ΡΠΈΠ½Ρ Π²Π΅ΡΡΡ ΠΏΠΎΡΡΠΈ 9200 ΠΊΠ³, Ρ
ΠΎΡΡ ΠΏΠΎ ΡΠ΅Π³Π»Π°ΠΌΠ΅Π½ΡΡ Β«ΠΠ°ΠΊΠ°ΡΠ°Β» ΠΌΠ°ΡΡΠ° ΠΌΠΎΠΆΠ΅Ρ ΡΠΎΡΡΠ°Π²Π»ΡΡΡ 8500 ΠΊΠ³) ΠΈ
ΡΠ»ΡΡΡΠ΅Π½ΠΈΠ΅ΠΌ ΡΠ°Π·Π²Π΅ΡΠΎΠ²ΠΊΠΈ (Π½Π° ΠΏΡΠΎΡΠΎΡΠΈΠΏΠ΅ Π§Π°Π³ΠΈΠ½Π° ΡΠ΄Π°Π»ΠΎΡΡ Π΄ΠΎΠ±ΠΈΡΡΡΡ ΠΏΡΠΎΠΏΠΎΡΡΠΈΠΈ Β«ΠΏΡΡΡΠ΄Π΅ΡΡΡ Π½Π° ΠΏΡΡΡΠ΄Π΅ΡΡΡΒ»).
ΠΠΏΡΠΎΡΠ΅ΠΌ, Π΄ΠΎΡΠ°Π±ΠΎΡΠΊΠ° Π½ΡΠ½Π΅ΡΠ½ΠΈΡ
Π°Π²ΡΠΎΠΌΠΎΠ±ΠΈΠ»Π΅ΠΉ β ΡΡΠΎ ΠΏΠΎΠΏΡΡΠΊΠ° ΡΠ΄Π΅Π»Π°ΡΡ ΠΈΠ· Π»ΡΡΡΠ΅Π³ΠΎ ΠΈΠ΄Π΅Π°Π»ΡΠ½ΠΎΠ΅: ΡΠΏΠΎΡΡΠΈΠ²Π½ΡΠΉ Β«ΠΠ°ΠΌΠΠΒ»
ΠΎΡΡΠ°Π΅ΡΡΡ Π±Π΅ΡΠΊΠΎΠΌΠΏΡΠΎΠΌΠΈΡΡΠ½ΠΎΠΉ ΠΌΠ°ΡΠΈΠ½ΠΎΠΉ, ΠΊΠΎΡΠΎΡΠ°Ρ ΠΏΠΎΠ·Π²ΠΎΠ»ΡΠ΅Ρ ΡΡΠ°ΠΌΠΏΠΎΠ²Π°ΡΡ ΠΏΠΎΠ±Π΅Π΄Ρ ΠΎΠ΄Π½Ρ Π·Π° Π΄ΡΡΠ³ΠΎΠΉ.
Π‘ΠΏΡΠ°Π²ΠΊΠ°:
ΠΠ°Π±ΠΈΠ½Π° β ΠΠ°ΠΌΠΠ, Π ΠΎΡΡΠΈΡ
ΠΠ²ΠΈΠ³Π°ΡΠ΅Π»Ρ β Π―ΠΠ (18,47 Π», 830 Π».Ρ., 3500 ΠΒ·ΠΌ), Π ΠΎΡΡΠΈΡ
Π‘ΡΠ΅ΠΏΠ»Π΅Π½ΠΈΠ΅ β SACHS, ΠΠ΅ΡΠΌΠ°Π½ΠΈΡ
ΠΠΎΡΠΎΠ±ΠΊΠ° ΠΏΠ΅ΡΠ΅Π΄Π°Ρ β ZF (16 ΡΡΡΠΏΠ΅Π½Π΅ΠΉ), ΠΠ΅ΡΠΌΠ°Π½ΠΈΡ
Π Π°Π·Π΄Π°ΡΠΎΡΠ½Π°Ρ ΠΊΠΎΡΠΎΠ±ΠΊΠ° β Steyr, ΠΠ²ΡΡΡΠΈΡ
ΠΠ°ΡΠ΄Π°Π½Π½Π°Ρ ΠΏΠ΅ΡΠ΅Π΄Π°ΡΠ° β Tirsan Kardan, Π’ΡΡΡΠΈΡ
ΠΠΎΡΡΡ β Sisu, Π€ΠΈΠ½Π»ΡΠ½Π΄ΠΈΡ
Π’ΠΎΡΠΌΠΎΠ·Π½Π°Ρ ΡΠΈΡΡΠ΅ΠΌΠ° β Wabco, ΠΠ΅Π»ΡΠ³ΠΈΡ
ΠΠΌΠΎΡΡΠΈΠ·Π°ΡΠΎΡΡ β Reiger, ΠΠΎΠ»Π»Π°Π½Π΄ΠΈΡ
Π¨ΠΈΠ½Ρ β Michelin (14.00 R20XZL), Π€ΡΠ°Π½ΡΠΈΡ
via auto.km
fishki.net
Π£ΡΡΡΠΎΠΉΡΡΠ²ΠΎ ΠΏΠΎΠ΄Π²Π΅ΡΠΊΠΈ Π°Π²ΡΠΎΠΌΠΎΠ±ΠΈΠ»Π΅ΠΉ ΠΠ°ΠΌΠΠ-5320, ΠΠ°ΠΌΠΠ-4310 ΠΈ Π£ΡΠ°Π»-4320
Π‘ΡΡΠΎΠΈΡΠ΅Π»ΡΠ½ΡΠ΅ ΠΌΠ°ΡΠΈΠ½Ρ ΠΈ ΠΎΠ±ΠΎΡΡΠ΄ΠΎΠ²Π°Π½ΠΈΠ΅, ΡΠΏΡΠ°Π²ΠΎΡΠ½ΠΈΠΊ
ΠΠ°ΡΠ΅Π³ΠΎΡΠΈΡ:
ΠΠ²ΡΠΎΠΌΠΎΠ±ΠΈΠ»ΠΈ ΠΠ°ΠΌΠ°Π· Π£ΡΠ°Π»
ΠΡΠ±Π»ΠΈΠΊΠ°ΡΠΈΡ:
Π£ΡΡΡΠΎΠΉΡΡΠ²ΠΎ ΠΏΠΎΠ΄Π²Π΅ΡΠΊΠΈ Π°Π²ΡΠΎΠΌΠΎΠ±ΠΈΠ»Π΅ΠΉ ΠΠ°ΠΌΠΠ-5320, ΠΠ°ΠΌΠΠ-4310 ΠΈ Π£ΡΠ°Π»-4320
Π§ΠΈΡΠ°ΡΡ Π΄Π°Π»Π΅Π΅:
Π£ΡΡΡΠΎΠΉΡΡΠ²ΠΎ ΠΏΠΎΠ΄Π²Π΅ΡΠΊΠΈ Π°Π²ΡΠΎΠΌΠΎΠ±ΠΈΠ»Π΅ΠΉ ΠΠ°ΠΌΠΠ-5320, ΠΠ°ΠΌΠΠ-4310 ΠΈ Π£ΡΠ°Π»-4320
ΠΠΎΠ΄Π²Π΅ΡΠΊΠ° Π°Π²ΡΠΎΠΌΠΎΠ±ΠΈΠ»Π΅ΠΉ ΡΠ΅ΡΡΠΎΡΠ½Π°Ρ, Π·Π°Π²ΠΈΡΠΈΠΌΠ°Ρ, Π²ΡΠΏΠΎΠ»Π½Π΅Π½Π° Π½Π° ΡΠ΅ΡΡΡΠ΅Ρ Π»ΠΈΡΡΠΎΠ²ΡΡ ΡΠ΅ΡΡΠΎΡΠ°Ρ . ΠΠ΅ΡΠ΅Π΄Π½ΠΈΠ΅ ΡΠ΅ΡΡΠΎΡΡ ΡΠ°Π±ΠΎΡΠ°ΡΡ ΡΠΎΠ²ΠΌΠ΅ΡΡΠ½ΠΎ Ρ ΡΠ΅Π»Π΅ΡΠΊΠΎΠΏΠΈΡΠ΅ΡΠΊΠΈΠΌΠΈ Π°ΠΌΠΎΡΡΠΈΠ·Π°ΡΠΎΡΠ°ΠΌΠΈ.
ΠΠΈΡΡΠΎΠ²ΡΠ΅ ΡΠ΅ΡΡΠΎΡΡ ΠΏΡΠ΅Π΄ΡΡΠ°Π²Π»ΡΡΡ ΡΠΎΠ±ΠΎΠΉ ΡΠΏΡΡΠ³ΠΈΠ΅ Π±Π°Π»ΠΊΠΈ, ΡΠΎΠ±ΡΠ°Π½Π½ΡΠ΅ ΠΈΠ· ΠΎΡΠ΄Π΅Π»ΡΠ½ΡΡ ΡΡΠ°Π»ΡΠ½ΡΡ Π»ΠΈΡΡΠΎΠ² ΡΠ°Π·Π»ΠΈΡΠ½ΠΎΠΉ Π΄Π»ΠΈΠ½Ρ, ΡΡΡΠ½ΡΡΡΡ ΡΠ΅Π½ΡΡΠΎΠ²ΡΠΌ Π±ΠΎΠ»ΡΠΎΠΌ. ΠΠΈΡΡ, ΠΈΠΌΠ΅ΡΡΠΈΠΉ Π½Π°ΠΈΠ±ΠΎΠ»ΡΡΡΡ Π΄Π»ΠΈΠ½Ρ, Π½Π°Π·ΡΠ²Π°Π΅ΡΡΡ ΠΊΠΎΡΠ΅Π½Π½ΡΠΌ. ΠΡ Π±ΠΎΠΊΠΎΠ²ΡΡ ΡΠ΄Π²ΠΈΠ³ΠΎΠ² Π»ΠΈΡΡΡ ΠΏΡΠ΅Π΄ΠΎΡ ΡΠ°Π½ΡΡΡΡΡ ΡΡΡΠΆΠ½ΡΠΌΠΈ Ρ ΠΎΠΌΡΡΠ°ΠΌΠΈ, ΠΊΠΎΡΠΎΡΡΠ΅ ΡΠ°ΠΊΠΆΠ΅ ΠΏΠ΅ΡΠ΅Π΄Π°ΡΡ Π½Π°Π³ΡΡΠ·ΠΊΡ ΠΎΡ Π²Π΅ΡΡ Π½Π΅Π³ΠΎ ΠΊΠΎΡΠ΅Π½Π½ΠΎΠ³ΠΎ Π»ΠΈΡΡΠ° Π½Π° Π½ΠΈΠΆΠ½ΠΈΠ΅ ΠΏΡΠΈ ΠΎΠ±ΡΠ°ΡΠ½ΠΎΠΌ ΠΏΡΠΎΠ³ΠΈΠ±Π΅ ΡΠ΅ΡΡΠΎΡΡ.
Π ΠΈΡ. 5.4. Π Π΅ΡΡΠΎΡΠ° ΠΏΠ΅ΡΠ΅Π΄Π½Π΅ΠΉ ΠΏΠΎΠ΄Π²Π΅ΡΠΊΠΈ Π°Π²ΡΠΎΠΌΠΎΠ±ΠΈΠ»Π΅ΠΉ ΠΠ°ΠΌΠΠ:
1 β ΠΎΡΡΠ΅ΠΌΠ½ΠΎΠ΅ ΡΡΠΊΠΎ; 2β Π±ΠΎΠ»Ρ; 3 β Π²ΡΡΠ»ΠΊΠ°; 4 β ΠΏΡΠ΅ΡΡ-ΠΌΠ°ΡΠ»Π΅Π½ΠΊΠ°; 5 β ΠΏΠ΅ΡΠ΅Π΄Π½ΠΈΠΉ ΠΊΡΠΎΠ½ΡΡΠ΅ΠΉΠ½; 6βΠ±ΠΎΠ»Ρ; 7 β Π½Π°ΠΊΠ»Π°Π΄ΠΊΠ° ΠΏΠ΅ΡΠ΅Π΄Π½Π΅ΠΉ ΡΠ΅ΡΡΠΎΡΡ; 8βΡΠ°ΡΠΊΠ° ΠΎΡΠ½ΠΎΠ²Π½ΠΎΠ³ΠΎ Π±ΡΡΠ΅ΡΠ°; 9 β ΡΡΡΠ΅ΠΌΡΠ½ΠΊΠ°; 10β Π½Π°ΠΊΠ»Π°Π΄ΠΊΠ° Π»ΠΈΡΡΠ°; 11 β Π·Π°Π΄Π½ΠΈΠΉ ΠΊΡΠΎΠ½ΡΡΠ΅ΠΉΠ½; 12 β ΡΡΡ
Π°ΡΡ; 13 β Π²ΠΊΠ»Π°Π΄ΡΡ Π·Π°Π΄Π½Π΅Π³ΠΎ ΠΊΡΠΎΠ½ΡΡΠ΅ΠΉΠ½Π°; 14 β ΠΏΠ°Π»Π΅Ρ ΡΡΡ
Π°ΡΡ; 15 β Π±ΠΎΠ»Ρ; 16β Π²ΡΡΠ»ΠΊΠ° Π±ΠΎΠ»ΡΠ°; 17 β ΠΊΡΠΎΠ½ΡΡΠ΅ΠΉΠ½ Π°ΠΌΠΎΡΡΠΈΠ·Π°ΡΠΎΡΠ°; 18 β ΠΏΠ°Π»Π΅Ρ; 19 β Π±ΠΎΠ»Ρ; 20βΠ½Π°ΠΊΠ»Π°Π΄ΠΊΠ° ΡΡΠΊΠ°
ΠΠ΅ΡΠ΅Π΄Π½ΡΡ ΠΏΠΎΠ΄Π²Π΅ΡΠΊΠ° Π°Π²ΡΠΎΠΌΠΎΠ±ΠΈΠ»Π΅ΠΉ ΡΠΎΡΡΠΎΠΈΡ ΠΈΠ· Π΄Π²ΡΡ Π»ΠΈΡΡΠΎΠ²ΡΡ ΡΠ΅ΡΡΠΎΡ ΠΈ Π΄Π²ΡΡ ΡΠ΅Π»Π΅ΡΠΊΠΎΠΏΠΈΡΠ΅ΡΠΊΠΈΡ Π°ΠΌΠΎΡΡΠΈΠ·Π°ΡΠΎΡΠΎΠ².
Π Π΅ΡΡΠΎΡΠ° ΠΏΠ΅ΡΠ΅Π΄Π½Π΅ΠΉ ΠΏΠΎΠ΄Π²Π΅ΡΠΊΠΈ Π°Π²ΡΠΎΠΌΠΎΠ±ΠΈΠ»Π΅ΠΉ ΠΠ°ΠΌΠΠ-5320 ΠΈ ΠΠ°ΠΌΠΠ-4310 Π½Π°Π±ΡΠ°Π½Π° ΠΈΠ· 15 Π»ΠΈΡΡΠΎΠ². ΠΠΎΡΠ΅Π½Π½ΠΎΠΉ Π»ΠΈΡΡ ΡΠ΅ΡΡΠΎΡΡ ΠΏΡΡΠΌΠΎΡΠ³ΠΎΠ»ΡΠ½ΠΎΠ³ΠΎ ΡΠ΅ΡΠ΅Π½ΠΈΡ, Π° ΠΎΡΡΠ°Π»ΡΠ½ΡΠ΅ Π’-ΠΎΠ±ΡΠ°Π·Π½ΠΎΠ³ΠΎ. ΠΡΠΎ ΠΏΠΎΠ·Π²ΠΎΠ»ΡΠ΅Ρ ΡΠΌΠ΅Π½ΡΡΠΈΡΡ ΠΌΠ°ΡΡΡ ΡΠ΅ΡΡΠΎΡΡ Π½Π° 7β¦ 10% ΠΏΡΠΈ ΡΠΎΡ ΡΠ°Π½Π΅Π½ΠΈΠΈ Π΅Π΅ Ρ Π°ΡΠ°ΠΊΡΠ΅ΡΠΈΡΡΠΈΠΊ. ΠΠ΅ΡΠ΅Π΄Π½ΠΈΠΉ ΠΊΠΎΠ½Π΅Ρ ΡΠ΅ΡΡΠΎΡΡ Ρ ΠΏΠΎΠΌΠΎΡΡΡ ΡΡΠΊΠ° ΠΈ ΠΏΠ°Π»ΡΡΠ° ΡΠΎΠ΅Π΄ΠΈΠ½Π΅Π½ Ρ ΠΊΡΠΎΠ½ΡΡΠ΅ΠΉΠ½ΠΎΠΌ ΡΠ°ΠΌΡ. ΠΡΡΠ΅ΠΌΠ½ΠΎΠ΅ ΡΡΠΊΠΎ ΠΏΡΠΈΠΊΡΠ΅ΠΏΠ»Π΅Π½ΠΎ ΠΊ ΠΊΠΎΡΠ΅Π½Π½ΠΎΠΌΡ Π»ΠΈΡΡΡ ΡΠ΅ΡΡΠΎΡΡ Π±ΠΎΠ»ΡΠΎΠΌ ΠΈ Π½Π°ΠΊΠ»Π°Π΄ΠΊΠΎΠΉ, ΠΊΠΎΡΠΎΡΠ°Ρ Π·Π°ΠΊΡΠ΅ΠΏΠ»Π΅Π½Π° Π½Π° ΡΡΠΊΠ΅ Π΄Π²ΡΠΌΡ Π±ΠΎΠ»ΡΠ°ΠΌΠΈ. Π ΡΡΠΊΠΎ Π·Π°ΠΏΡΠ΅ΡΡΠΎΠ²Π°Π½Π° Π²ΡΡΠ»ΠΊΠ°. ΠΠ°Π»Π΅Ρ, ΡΠΎΠ΅Π΄ΠΈΠ½ΡΡΡΠΈΠΉ ΡΡΠΊΠΎ Ρ ΠΊΡΠΎΠ½ΡΡΠ΅ΠΉΠ½ΠΎΠΌ, Π·Π°ΡΠΈΠΊΡΠΈΡΠΎΠ²Π°Π½ Π΄Π²ΡΠΌΡ Π±ΠΎΠ»ΡΠ°ΠΌΠΈ. Π‘ΠΌΠ°Π·ΠΊΠ° ΠΏΠ°Π»ΡΡΠ° ΠΏΡΠΎΠΈΠ·Π²ΠΎΠ΄ΠΈΡΡΡ ΡΠ΅ΡΠ΅Π· ΠΏΡΠ΅ΡΡ-ΠΌΠ°ΡΠ»Π΅Π½ΠΊΡ.ΠΠ°Π΄Π½ΠΈΠΉ ΠΊΠΎΠ½Π΅Ρ ΡΠ΅ΡΡΠΎΡΡ ΡΠΊΠΎΠ»ΡΠ·ΡΡΠΈΠΉ ΠΈ ΡΠ΅ΡΠ΅Π· Π½Π°ΠΊΠ»Π΅ΠΏΠ°Π½Π½ΡΡ Π½Π° ΠΊΠΎΡΠ΅Π½Π½ΠΎΠΉ Π»ΠΈΡΡ Π½Π°ΠΊΠ»Π°Π΄ΠΊΡ ΠΎΠΏΠΈΡΠ°Π΅ΡΡΡ Π½Π° ΡΠΌΠ΅Π½Π½ΡΠΉ ΡΡΡ Π°ΡΡ, Π½Π°ΠΏΡΠ΅ΡΡΠΎΠ²Π°Π½Π½ΡΠΉ Π½Π° ΠΊΡΠΎΠ½ΡΡΠ΅ΠΉΠ½. ΠΠ»Ρ ΠΏΡΠ΅Π΄ΠΎΡ ΡΠ°Π½Π΅Π½ΠΈΡ ΠΎΡ ΠΈΠ·Π½ΠΎΡΠ° ΡΡΠ΅Π½ΠΎΠΊ ΠΊΡΠΎΠ½ΡΡΠ΅ΠΉΠ½Π° Π½Π° ΠΏΠ°Π»ΡΡΠ°Ρ ΡΡΡ Π°ΡΠ΅ΠΉ ΡΡΡΠ°Π½ΠΎΠ²Π»Π΅Π½Ρ Π²ΠΊΠ»Π°Π΄ΡΡΠΈ, ΡΡΡΠ½ΡΡΡΠ΅ Π±ΠΎΠ»ΡΠΎΠΌ ΡΠ΅ΡΠ΅Π· ΡΠ°ΡΠΏΠΎΡΠ½ΡΡ Π²ΡΡΠ»ΠΊΡ.
Π ΡΡΠ΅Π΄Π½Π΅ΠΉ ΡΠ°ΡΡΠΈ ΡΠ΅ΡΡΠΎΡΡ ΡΡΡΠ°Π½ΠΎΠ²Π»Π΅Π½Π° Π½Π°ΠΊΠ»Π°Π΄ΠΊΠ°, ΡΠ΅ΡΠ΅Π· ΠΊΠΎΡΠΎΡΡΡ ΡΠ΅ΡΡΠΎΡΠ° Π΄Π²ΡΠΌΡ ΡΡΡΠ΅ΠΌΡΠ½ΠΊΠ°ΠΌΠΈ ΠΊΡΠ΅ΠΏΠΈΡΡΡ ΠΊ ΠΏΠ΅ΡΠ΅Π΄Π½Π΅ΠΌΡ ΠΌΠΎΡΡΡ. ΠΠ°ΠΊΠ»Π°Π΄ΠΊΠ° ΠΈΠΌΠ΅Π΅Ρ Π²ΡΡΡΠ°ΠΌΠΏΠΎΠ²ΠΊΡ, ΠΊΠΎΡΠΎΡΠ°Ρ Π²Ρ ΠΎΠ΄ΠΈΡ Π² ΡΠ³Π»ΡΠ±Π»Π΅Π½ΠΈΠ΅ ΠΏΠ΅ΡΠ²ΠΎΠ³ΠΎ Π»ΠΈΡΡΠ°. ΠΠ°ΠΆΠ΄ΡΠΉ Π»ΠΈΡΡ ΡΠ΅ΡΡΠΎΡΡ ΡΠ²ΠΎΠ΅ΠΉ Π²ΡΠ΄Π°Π²ΠΊΠΎΠΉ Π²Ρ ΠΎΠ΄ΠΈΡ Π² ΡΠ³Π»ΡΠ±Π»Π΅Π½ΠΈΠ΅ Π½ΠΈΠΆΠ΅Π»Π΅ΠΆΠ°ΡΠ΅Π³ΠΎ Π»ΠΈΡΡΠ°, ΠΏΡΠΈΡΠ΅ΠΌ Π²ΡΠ΄Π°Π²ΠΊΠ° ΠΏΠΎΡΠ»Π΅Π΄Π½Π΅Π³ΠΎ Π»ΠΈΡΡΠ° Π²Ρ ΠΎΠ΄ΠΈΡ Π² ΡΠΎΠΎΡΠ²Π΅ΡΡΡΠ²ΡΡΡΠ΅Π΅ ΡΠ³Π»ΡΠ±Π»Π΅Π½ΠΈΠ΅ ΠΊΡΠΎΠ½ΡΡΠ΅ΠΉΠ½Π° Π°ΠΌΠΎΡΡΠΈΠ·Π°ΡΠΎΡΠ°, Π·Π°ΡΠΈΠΊΡΠΈΡΠΎΠ²Π°Π½Π½ΠΎΠ³ΠΎ, Π² ΡΠ²ΠΎΡ ΠΎΡΠ΅ΡΠ΅Π΄Ρ, Π½Π° Π±Π°Π»ΠΊΠ΅ ΠΏΠ΅ΡΠ΅Π΄Π½Π΅Π³ΠΎ ΠΌΠΎΡΡΠ°. ΠΡ Π±ΠΎΠΊΠΎΠ²ΠΎΠ³ΠΎ ΡΠΌΠ΅ΡΠ΅Π½ΠΈΡ Π»ΠΈΡΡΡ ΡΠ΅ΡΡΠΎΡΡ Π΄ΠΎΠΏΠΎΠ»Π½ΠΈΡΠ΅Π»ΡΠ½ΠΎ ΡΠΊΡΠ΅ΠΏΠ»Π΅Π½Ρ Ρ ΠΎΠΌΡΡΠ°ΠΌΠΈ.
Π ΠΈΡ. 5.5. Π Π΅ΡΡΠΎΡΠ° ΠΏΠ΅ΡΠ΅Π΄Π½Π΅ΠΉ ΠΏΠΎΠ΄Π²Π΅ΡΠΊΠΈ Π°Π²ΡΠΎΠΌΠΎΠ±ΠΈΠ»Ρ Π£ΡΠ°Π»-4Ρ:
1 β- ΡΡΠΊΠΎ ΡΠ΅ΡΡΠΎΡΡ; 2 β ΠΊΠ»ΠΈΠ½; 3 β Π³Π°ΠΉΠΊΠ°; 4 β ΠΏΠ΅ΡΠ΅Π΄Π½ΠΈΠΉ ΠΊΡΠΎΠ½ΡΡΠ΅ΠΉΠ½; 5 β Π±ΡΡΠ΅Ρ ΡΠ΅ΡΡΠΎΡΡ; 6 β Π·Π°Π΄Π½ΠΈΠΉ ΠΊΡΠΎΠ½ΡΡΠ΅ΠΉΠ½; 7 β Π²ΠΊΠ»Π°Π΄ΡΡ; 8 β Π±ΠΎΠ»Ρ; 9 β ΡΠ°ΡΠΏΠΎΡΠ½Π°Ρ Π²ΡΡΠ»ΠΊΠ°; 10 β Π΄ΠΎΠΏΠΎΠ»Π½ΠΈΡΠ΅Π»Ρ ΡΠΉ Π±ΡΡΠ΅Ρ; 11 β ΡΡΡΠΆΠΊΠ°; 12 β Π½Π°ΠΊΠ»Π°Π΄ΠΊΠ°; 13 β ΠΏΠ°Π»Π΅Ρ ΡΡΠΊΠΉ ΡΠ΅ΡΡΠΎΡΡ; 14 β ΡΡΡΠ΅ΠΌΡΠ½ΠΊΠ° ΡΡΠΊΠ° ΡΠ΅ΡΡ< ΡΡ
ΠΠ»Ρ ΠΈΡΠΊΠ»ΡΡΠ΅Π½ΠΈΡ ΠΆΠ΅ΡΡΠΊΠΈΡ ΡΠ΄Π°ΡΠΎΠ² ΠΏΠ΅ΡΠ΅Π΄Π½Π΅Π³ΠΎ ΠΌΠΎΡΡΠ° ΠΎ ΡΠ°ΠΌΡ ΠΊ Π½ΠΈΠΆΠ½ΠΈΠΌ ΠΏΠΎΠ»ΠΊΠ°ΠΌ Π»ΠΎΠ½ΠΆΠ΅ΡΠΎΠ½ΠΎΠ² ΠΏΡΠΈΠ²Π΅ΡΠ½ΡΡΡ ΡΠ΅Π·ΠΈΠ½ΠΎΠ²ΡΠ΅ Π±ΡΡΠ΅ΡΠ° 8. ΠΠ° Π°Π²ΡΠΎΠΌΠΎΠ±ΠΈΠ»Π΅ ΠΠ°ΠΌΠΠ-4310 ΡΡΡΠ°Π½Π°Π²Π»ΠΈΠ²Π°ΡΡΡΡ Π΄Π²Π° Π±ΡΡΠ΅ΡΠ°.
Π Π΅ΡΡΠΎΡΠ° ΠΏΠ΅ΡΠ΅Π΄Π½Π΅ΠΉ ΠΏΠΎΠ΄Π²Π΅ΡΠΊΠΈ Π°Π²ΡΠΎΠΌΠΎΠ±ΠΈΠ»Ρ Π£ΡΠ°Π»-4320 (ΡΠΈΡ. 5.5) Π½Π°Π±ΡΠ°Π½Π° ΠΈΠ· 10 Π»ΠΈΡΡΠΎΠ². ΠΠΎΡΠ΅Π½Π½ΠΎΠΉ ΠΈ ΠΏΠΎΠ΄ΠΊΠΎΡΠ΅Π½Π½ΠΎΠΉ Π»ΠΈΡΡΡ ΡΠ΅ΡΡΠΎΡΡ ΠΏΡΡΠΌΠΎΡΠ³ΠΎΠ»ΡΠ½ΠΎΠ³ΠΎ ΡΠ΅ΡΠ΅Π½ΠΈΡ, Π° ΠΎΡΡΠ°Π»ΡΠ½ΡΠ΅ Π’-ΠΎΠ±ΡΠ°Π·Π½ΠΎΠ³ΠΎ.
Π₯ΠΎΠ΄ ΠΌΠΎΡΡΠ° Π²Π²Π΅ΡΡ ΠΎΠ³ΡΠ°Π½ΠΈΡΠΈΠ²Π°Π΅ΡΡΡ ΡΠ΅Π·ΠΈΠ½ΠΎΠ²ΡΠΌ Π±ΡΡΠ΅ΡΠΎΠΌ Π½Π° Π»ΠΎΠ½ΠΆΠ΅ΡΠΎΠ½Π΅ ΡΠ°ΠΌΡ. ΠΡΠΎΡ Π΄ΠΎΠΏΠΎΠ»Π½ΠΈΡΠ΅Π»ΡΠ½ΡΠΉ Π±ΡΡΠ΅Ρ ΡΠΌΠ΅Π½ΡΡΠ°Π΅Ρ ΡΠ°ΠΊΠΆΠ΅ Π½Π°ΠΏΡΡΠΆΠ΅Π½ΠΈΠ΅ Π² ΡΠ΅ΡΡΠΎΡΠ΅ ΠΏΡΠΈ ΡΠ΅Π·ΠΊΠΎΠΌ ΡΠΎΡΠΌΠΎΠΆΠ΅Π½ΠΈΠΈ Π°Π²ΡΠΎΠΌΠΎΠ±ΠΈΠ»Ρ, ΠΎΠ³ΡΠ°Π½ΠΈΡΠΈΠ²Π°Ρ Π΅Π΅ Π·Π°ΠΊΡΡΡΠΊΡ. ΠΠ°Π΄Π½ΠΈΠ΅ ΠΏΠΎΠ΄Π²Π΅ΡΠΊΠΈ Π°Π²ΡΠΎΠΌΠΎΠ±ΠΈΠ»Π΅ΠΉ ΠΠ°ΠΌΠΠ (ΡΠΈΡ. 5.6) ΠΈ Π£ΡΠ°Π» ΠΏΠΎ ΠΊΠΎΠ½ΡΡΡΡΠΊΡΠΈΠΈ Π°Π½Π°Π»ΠΎΠ³ΠΈΡΠ½Ρ.
ΠΠ°ΠΆΠ΄Π°Ρ ΡΠ΅ΡΡΠΎΡΠ° ΡΡΠ΅Π΄Π½Π΅ΠΉ ΡΠ°ΡΡΡΡ ΠΏΡΠΈΠΊΡΠ΅ΠΏΠ»Π΅Π½Π° ΡΡΡΠ΅ΠΌΡΠ½ΠΊΠ°ΠΌΠΈ ΠΊ ΠΊΠ°ΡΠ°ΡΡΠ΅ΠΉΡΡ ΠΎΠΏΠΎΡΠ΅ Π±Π°Π»Π°Π½ΡΠΈΡΠ½ΠΎΠ³ΠΎ ΡΡΡΡΠΎΠΉΡΡΠ²Π°. ΠΠΎΠ½ΡΡ ΡΠ΅ΡΡΠΎΡ ΠΎΠΏΠΈΡΠ°ΡΡΡΡ Π½Π° ΠΎΠΏΠΎΡΡ. ΠΡΠΈ ΠΏΡΠΎΠ³ΠΈΠ±Π΅ ΡΠ΅ΡΡΠΎΡ ΠΊΠΎΠ½ΡΡ ΠΈΡ ΡΠΊΠΎΠ»ΡΠ·ΡΡ Π² ΠΎΠΏΠΎΡΠ°Ρ . ΠΠΎΡΠΊΠΎΠ»ΡΠΊΡ ΠΏΡΠΎΠ΄ΠΎΠ»ΡΠ½ΠΎΠ΅ ΠΏΠ΅ΡΠ΅ΠΌΠ΅ΡΠ΅Π½ΠΈΠ΅ ΠΊΠΎΠ½ΡΠΎΠ² ΡΠ΅ΡΡΠΎΡΡ Π² ΠΊΡΠΎΠ½ΡΡΠ΅ΠΉΠ½Π°Ρ Π½Π΅ ΠΎΠ³ΡΠ°Π½ΠΈΡΠ΅Π½ΠΎ, ΠΎΠ½Π° ΡΠ°Π·Π³ΡΡΠΆΠ΅Π½Π° ΠΎΡ ΠΏΠ΅ΡΠ΅Π΄Π°ΡΠΈ ΠΏΡΠΎΠ΄ΠΎΠ»ΡΠ½ΡΡ ΡΡΠΈΠ»ΠΈΠΉ ΠΈ ΠΌΠΎΠΌΠ΅Π½ΡΠΎΠ², Π΄Π΅ΠΉΡΡΠ²ΡΡΡΠΈΡ Π² ΠΏΡΠΎΠ΄ΠΎΠ»ΡΠ½ΠΎΠΉ ΠΏΠ»ΠΎΡΠΊΠΎΡΡΠΈ, Π½ΠΎ Π²ΠΎΡΠΏΡΠΈΠ½ΠΈΠΌΠ°Π΅Ρ Π±ΠΎΠΊΠΎΠ²ΡΠ΅ ΡΡΠΈΠ»ΠΈΡ.
ΠΠ»Ρ ΠΎΠ³ΡΠ°Π½ΠΈΡΠ΅Π½ΠΈΡ Ρ ΠΎΠ΄Π° ΠΌΠΎΡΡΠΎΠ² Π²Π²Π΅ΡΡ ΠΈ ΡΠΌΡΠ³ΡΠ΅Π½ΠΈΡ ΠΈΡ ΡΠ΄Π°ΡΠΎΠ² ΠΎ ΡΠ°ΠΌΡ Π½Π° Π»ΠΎΠ½ΠΆΠ΅ΡΠΎΠ½Π΅ ΡΡΡΠ°Π½ΠΎΠ²Π»Π΅Π½Ρ Π±ΡΡΠ΅ΡΠ°. Π’ΠΎΠ»ΠΊΠ°ΡΡΠΈΠ΅ ΡΡΠΈΠ»ΠΈΡ ΠΈ ΡΠ΅Π°ΠΊΡΠΈΠ²Π½ΡΠ΅ ΠΌΠΎΠΌΠ΅Π½ΡΡ ΠΏΠ΅ΡΠ΅Π΄Π°ΡΡΡΡ Π½Π° ΡΠ°ΠΌΡ ΡΠ΅ΡΡΡΡ ΡΠ΅Π°ΠΊΡΠΈΠ²Π½ΡΠΌΠΈ ΡΡΠ°Π½Π³Π°ΠΌΠΈ (ΡΠ΅ΡΡΡΠ΅ ΡΡΠ°Π½Π³ΠΈ Π½ΠΈΠΆΠ½ΠΈΠ΅ ΠΈ Π΄Π²Π΅ Π²Π΅ΡΡ Π½ΠΈΠ΅).
Π ΠΈΡ. 5.6. ΠΠ°Π΄Π½ΡΡ ΠΏΠΎΠ΄Π²Π΅ΡΠΊΠ° Π°Π²ΡΠΎΠΌΠΎΠ±ΠΈΠ»Ρ ΠΠ°ΠΌΠΠ-5320:
1 β ΡΡΠ΅Π΄Π½ΠΈΠΉ ΠΌΠΎΡΡ; 2 β ΠΊΡΠΎΠ½ΡΡΠ΅ΠΉΠ½ Π²Π΅ΡΡ
Π½Π΅ΠΉ ΡΠ΅Π°ΠΊΡΠΈΠ²Π½ΠΎΠΉ ΡΡΠ°Π½Π³ΠΈ; 3 β ΠΊΡΠΎΠ½ΡΡΠ΅ΠΉΠ½ Π½ΠΈΠΆΠ½Π΅ΠΉ ΡΠ΅Π°ΠΊΡΠΈΠ²Π½ΠΎΠΉ ΡΡΠ°Π½Π³ΠΈ; 4, 8 β ΠΊΡΠΎΠ½ΡΡΠ΅ΠΉΠ½Ρ ΡΡΡΠ°Π½ΠΎΠ²ΠΊΠΈ Dec ΡΠΎΡΡ; 5βΡΠ΅ΡΡΠΎΡΠ°; 6 β ΠΊΡΠΎΠ½ΡΡΠ΅ΠΉΠ½ ΠΏΠΎΠ΄Π²Π΅ΡΠΊΠΈ; 7 β ΡΡΡΠ΅ΠΌΡΠ½ΠΊΠ° ΡΠ΅ΡΡΠΎΡΡ; 9 β Π·Π°Π΄Π½ΠΈΠΉ ΠΌΠΎΡΡ; 10 β Π²Π΅ΡΡ
Π½ΡΡ ΡΠ΅Π°ΠΊΡΠΈΠ²Π½Π°Ρ ΡΡΠ°Π½Π³Π°; 11 14 β Π½ΠΈΠΆΠ½ΠΈΠ΅ DeaK ΡΠΈΠ²Π½ΡΠ΅ ΡΡΠ°Π½Π³ΠΈ; 12 β ΠΊΠ°ΡΠ°ΡΡΠ°ΡΡΡ ΠΎΠΏΠΎΡΠ°; 13 β ΠΎΡΡ ΠΎΠΏΠΎΡΡ
Π ΠΈΡ. 5.7. ΠΠΌΠΎΡΡΠΈΠ·Π°ΡΠΎΡ:
Π° β ΡΠ°Π±ΠΎΡΠ΅Π΅ ΠΏΠΎΠ»ΠΎΠΆΠ΅Π½ΠΈΠ΅ ΠΏΡΠΈ Ρ
ΠΎΠ΄Π΅ ΡΠΆΠ°ΡΠΈΡ; Π± β ΡΠ°Π±ΠΎΡΠ΅Π΅ ΠΏΠΎΠ»ΠΎΠΆΠ΅Π½ΠΈΠ΅ ΠΏΡΠΈ Ρ
ΠΎΠ΄Π΅ ΠΎΡΠ΄Π°ΡΠΈ; 1 β ΠΏΡΠΎΡΡΠΈΠ½Π°; 2 β ΠΊΠΎΡΠΏΡΡ ΠΊΠ»Π°ΠΏΠ°Π½ΠΎΠ²; 3 β ΠΊΠ»Π°ΠΏΠ°Π½ ΡΠΆΠ°ΡΠΈΡ; 4 β ΠΏΠ΅ΡΠ΅ΠΏΡΡΠΊΠ½ΠΎΠΉ ΠΊΠ»Π°ΠΏΠ°Π½ ΠΎΡΠ΄Π°ΡΠΈ; 5 β ΠΊΠΎΡΠΏΡΡ ΡΠ΅Π·Π΅ΡΠ²ΡΠ°ΡΠ°; 6 β ΡΠ°Π±ΠΎΡΠΈΠΉ ΡΠΈΠ»ΠΈΠ½Π΄Ρ; 7 β ΠΊΠ»Π°ΠΏΠ°Π½ ΠΎΡΠ΄Π°ΡΠΈ; 8 β ΠΏΠΎΡΡΠ΅Π½Ρ; 9 β ΠΏΠ΅ΡΠ΅ΠΏΡΡΠΊΠ½ΠΎΠΉ ΠΊΠ»Π°ΠΏΠ°Π½ ΡΠΆΠ°ΡΠΈΡ; 10 β ΡΡΠΎΠΊ
Π¨Π°ΡΠ½ΠΈΡΡ ΡΠ΅Π°ΠΊΡΠΈΠ²Π½ΡΡ ΡΡΠ°Π½Π³ ΡΠ°ΠΌΠΎΠΏΠΎΠ΄ΠΆΠΈΠΌΠ½ΡΠ΅, ΡΠΎΡΡΠΎΡΡΠΈΠ΅ ΠΈΠ· ΡΠ°ΡΠΎΠ²ΡΡ ΠΏΠ°Π»ΡΡΠ΅Π², Π²Π½ΡΡΡΠ΅Π½Π½ΠΈΡ ΠΈ Π½Π°ΡΡΠΆΠ½ΡΡ Π²ΠΊΠ»Π°Π΄ΡΡΠ΅ΠΉ ΠΈ ΠΏΠΎΠ΄Π½ΠΈΠΌΠ°ΡΡΠΈΡ ΠΈΡ ΠΏΡΡΠΆΠΈΠ½. ΠΡΡΡΠΊΠΈ ΠΊΡΠ΅ΠΏΡΡΡΡ Π±ΠΎΠ»ΡΠ°ΠΌΠΈ, ΡΡΠΎ ΠΏΠΎΠ·Π²ΠΎΠ»ΡΠ΅Ρ Π»Π΅Π³ΠΊΠΎ ΡΠ°Π·Π±ΠΈΡΠ°ΡΡ ΠΈ ΡΠΎΠ±ΠΈΡΠ°ΡΡ ΡΠ°ΡΠ½ΠΈΡΡ. ΠΠ»Ρ Π·Π°ΡΠΈΡΡ ΡΠ°ΡΠ½ΠΈΡΠΎΠ² ΠΎΡ Π²ΠΎΠ΄Ρ ΠΈ Π³ΡΡΠ·ΠΈ ΡΡΡΠ°Π½ΠΎΠ²Π»Π΅Π½Ρ ΡΠ΅Π·ΠΈΠ½ΠΎΠ²ΡΠ΅ ΡΠ°Π»ΡΠ½ΠΈΠΊΠΈ. ΠΠ»Ρ ΡΠΌΠ°Π·ΠΊΠΈ ΠΈΠΌΠ΅ΡΡΡΡ ΠΌΠ°ΡΠ»Π΅Π½ΠΊΠΈ, ΡΠ°Π·ΠΌΠ΅ΡΠ΅Π½Π½ΡΠ΅ Π² ΠΊΡΡΡΠΊΠ΅ ΡΠ΅Π°ΠΊΡΠΈΠ²Π½ΡΡ ΡΡΠ°Π½Π³.
ΠΠ°Π»Π°Π½ΡΠΈΡΠ½ΠΎΠ΅ ΡΡΡΡΠΎΠΉΡΡΠ²ΠΎ ΡΠΎΡΡΠΎΠΈΡ ΠΈΠ· Π΄Π²ΡΡ ΠΎΡΠ΅ΠΉ, Π·Π°ΠΏΡΠ΅ΡΡΠΎΠ²Π°Π½Π½ΡΡ Π² ΠΊΡΠΎΠ½ΡΡΠ΅ΠΉΠ½Ρ ΠΊΠ°ΡΠ°ΡΡΠΈΡ ΡΡ ΠΎΠΏΠΎΡ, Π±Π°ΡΠΌΠ°ΠΊΠΎΠ² Ρ Π²ΡΡΠ»ΠΊΠ°ΠΌΠΈ ΠΈΠ· Π°Π½ΡΠΈΡΡΠΈΠΊΡΠΈΠΎΠ½Π½ΠΎΠ³ΠΎ ΠΌΠ°ΡΠ΅ΡΠΈΠ°Π»Π°. ΠΡΠΎΠ½ΡΡΠ΅ΠΉΠ½Ρ 6 Π±Π°Π»Π°Π½ΡΠΈΡΠ½ΠΎΠ³ΠΎ ΡΡΡΡΠΎΠΉΡΡΠ²Π° ΡΠΎΠ΅Π΄ΠΈΠ½Π΅Π½Ρ Π½Π° Π°Π²ΡΠΎΠΌΠΎΠ±ΠΈΠ»ΡΡ ΠΠ°ΠΌΠΠ ΡΡΡΠΆΠΊΠΎΠΉ ΠΈ Π·Π°ΠΊΡΠ΅ΠΏΠ»Π΅Π½Ρ ΡΠΏΠΈΠ»ΡΠΊΠ°ΠΌΠΈ Π½Π° ΠΊΡΠΎΠ½ΡΡΠ΅ΠΉΠ½Π°Ρ Π·Π°Π΄Π½Π΅ΠΉ ΠΏΠΎΠ΄Π²Π΅ΡΠΊΠΈ, ΠΊΠΎΡΠΎΡΡΠ΅ ΠΊΡΠ΅ΠΏΡΡΡΡ Π±ΠΎΠ»ΡΠ°ΠΌΠΈ ΠΊ Π»ΠΎΠ½ΠΆΠ΅ΡΠΎΠ½Π°ΠΌ ΡΠ°ΠΌΡ. ΠΠ°Π΄Π½ΡΡ ΠΏΠΎΠ΄Π²Π΅ΡΠΊΠ° Π°Π²ΡΠΎΠΌΠΎΠ±ΠΈΠ»Ρ Π£ΡΠ°Π»-4320, Π² ΠΎΡΠ»ΠΈΡΠΈΠ΅ ΠΎΡ ΡΠ°ΡΡΠΌΠΎΡΡΠ΅Π½Π½ΠΎΠΉ, ΠΈΠΌΠ΅Π΅Ρ Π±Π°Π»Π°Π½ΡΠΈΡΠ½ΠΎΠ΅ ΡΡΡΡΠΎΠΉΡΡΠ²ΠΎ Ρ ΠΎΠ΄Π½ΠΎΠΉ ΠΎΡΡΡ, Π·Π°ΠΏΡΠ΅ΡΡΠΎΠ²Π°Π½Π½ΠΎΠΉ Π² ΠΊΡΠΎΠ½ΡΡΠ΅ΠΉΠ½ Π±Π°Π»Π°Π½ΡΠΈΡΠ° ΠΈ Π²ΡΠΏΠΎΠ»Π½ΡΡΡΠ΅ΠΉ ΡΠΎΠ»Ρ ΡΡΡΠΆΠΊΠΈ.
ΠΠ°ΡΠΌΠ°ΠΊΠΈ Π·Π°ΠΊΡΠ΅ΠΏΠ»Π΅Π½Ρ Π½Π° ΠΎΡΡΡ ΡΠ°Π·ΡΠ΅Π·Π½ΡΠΌΠΈ Π³Π°ΠΉΠΊΠ°ΠΌΠΈ, ΡΡΡΠ½ΡΡΡΠΌΠΈ Π±ΠΎΠ»ΡΠ°ΠΌΠΈ. ΠΠ°ΠΉΠΊΠΈ ΡΡΡΠΆΠ½ΡΡ Π±ΠΎΠ»ΡΠΎΠ² ΡΠ°ΠΌΠΎΠΊΠΎΠ½ΡΡΡΡΠΈΠ΅ΡΡ; Π² ΠΊΡΡΡΠΊΠ΅ Π±Π°ΡΠΌΠ°ΠΊΠ° ΡΠ΄Π΅Π»Π°Π½ΠΎ ΠΎΡΠ²Π΅ΡΡΡΠΈΠ΅ Ρ ΠΏΡΠΎΠ±ΠΊΠΎΠΉ Π΄Π»Ρ Π·Π°Π»ΠΈΠ²Π° ΠΌΠ°ΡΠ»Π°.
ΠΠΌΠΎΡΡΠΈΠ·Π°ΡΠΎΡΡ Π°Π²ΡΠΎΠΌΠΎΠ±ΠΈΠ»Π΅ΠΉ ΡΠ΅Π»Π΅ΡΠΊΠΎΠΏΠΈΡΠ΅ΡΠΊΠΎΠ³ΠΎ ΡΠΈΠΏΠ°. Π‘ΠΈΠ»Π° ΡΠΎΠΏΡΠΎΡΠΈΠ²Π»Π΅Π½ΠΈΡ Π°ΠΌΠΎΡΡΠΈΠ·Π°ΡΠΎΡΠ° ΠΏΡΠΈ Ρ ΠΎΠ΄Π΅ ΡΠΆΠ°ΡΠΈΡ Π·Π½Π°ΡΠΈΡΠ΅Π»ΡΠ½ΠΎ ΠΌΠ΅Π½ΡΡΠ΅, ΡΠ΅ΠΌ ΠΏΡΠΈ Ρ ΠΎΠ΄Π΅ ΠΎΡΠ΄Π°ΡΠΈ, ΡΡΠΎ ΠΎΠ±Π΅ΡΠΏΠ΅ΡΠΈΠ²Π°Π΅ΡΡΡ ΠΏΡΠΎΡ ΠΎΠ΄Π½ΡΠΌΠΈ ΡΠ΅ΡΠ΅Π½ΠΈΡΠΌΠΈ ΠΊΠ»Π°ΠΏΠ°Π½ΠΎΠ².
ΠΡΠΈ ΠΏΠ»Π°Π²Π½ΠΎΠΌ ΡΠΆΠ°ΡΠΈΠΈ (ΡΠΈΡ. 5.7,Π°) ΡΡΠΎΠΊΠΏΠ΅ΡΠ΅ΠΌΠ΅ΡΠ°Π΅Ρ ΠΏΠΎΡΡΠ΅Π½Ρ Π²Π½ΠΈΠ·. ΠΠ΅ΡΠ΅ΠΏΡΡΠΊΠ½ΠΎΠΉ ΠΊΠ»Π°ΠΏΠ°Π½ ΠΎΡΠΊΡΡΠ²Π°Π΅ΡΡΡ, ΠΈ ΠΆΠΈΠ΄ΠΊΠΎΡΡΡ ΠΏΠ΅ΡΠ΅ΡΠ΅ΠΊΠ°Π΅Ρ Π² Π²Π΅ΡΡ Π½ΡΡ ΠΏΠΎΠ»ΠΎΡΡΡ, Π²ΡΡΡΠ΅ΡΠ°Ρ Π½Π΅Π·Π½Π°ΡΠΈΡΠ΅Π»ΡΠ½ΠΎΠ΅ ΡΠΎΠΏΡΠΎΡΠΈΠ²Π»Π΅Π½ΠΈΠ΅. ΠΠ΄Π½Π°ΠΊΠΎ Π²ΡΡ ΠΆΠΈΠ΄ΠΊΠΎΡΡΡ ΠΏΠΎΡΡΡΠΏΠΈΡΡ Π² Π²Π΅ΡΡ Π½ΡΡ ΠΏΠΎΠ»ΠΎΡΡΡ Π½Π΅ ΠΌΠΎΠΆΠ΅Ρ, ΡΠ°ΠΊ ΠΊΠ°ΠΊ Π² ΡΠ°Π±ΠΎΡΠΈΠΉ ΡΠΈΠ»ΠΈΠ½Π΄Ρ Π²Π²ΠΎΠ΄ΠΈΡΡΡ ΡΡΠΎΠΊ. ΠΠΎΡΡΠΎΠΌΡ ΡΠ°ΡΡΡ ΠΆΠΈΠ΄ΠΊΠΎΡΡΠΈ, ΡΠ°Π²Π½Π°Ρ ΠΏΠΎ ΠΎΠ±ΡΠ΅ΠΌΡ Π²Π΄Π²ΠΈΠ³Π°ΡΡΠ΅ΠΉΡΡ Π² ΡΠΈΠ»ΠΈΠ½Π΄Ρ ΡΠ°ΡΡΠΈ ΡΡΠΎΠΊΠ°, ΠΏΠ΅ΡΠ΅ΡΠ΅ΠΊΠ°Π΅Ρ ΡΠ΅ΡΠ΅Π· ΠΊΠ°Π»ΠΈΠ±ΡΠΎΠ²Π°Π½Π½ΡΠ΅ ΠΎΡΠ²Π΅ΡΡΡΠΈΡ Π² ΡΠΎΡΡΠ΅ ΠΊΠ»Π°ΠΏΠ°Π½Π° ΡΠΆΠ°ΡΠΈΡ 3 ΠΈ ΠΊΠ°Π½Π°Π»Ρ ΠΊΠΎΡΠΏΡΡΠ° 2 ΠΊΠ»Π°ΠΏΠ°Π½ΠΎΠ² Π² ΠΊΠΎΠΌΠΏΠ΅Π½ΡΠ°ΡΠΈΠΎΠ½Π½ΡΡ ΠΊΠ°ΠΌΠ΅ΡΡ, Π½Π΅ΡΠΊΠΎΠ»ΡΠΊΠΎ ΡΠ²Π΅Π»ΠΈΡΠΈΠ²Π°Ρ Π΄Π°Π²Π»Π΅Π½ΠΈΠ΅ Π½Π°Ρ ΠΎΠ΄ΡΡΠ΅Π³ΠΎΡΡ Π² Π½Π΅ΠΉ Π²ΠΎΠ·Π΄ΡΡ Π°.
ΠΠ°Π»ΠΈΠ±ΡΠΎΠ²Π°Π½Π½ΡΠ΅ ΠΎΡΠ²Π΅ΡΡΡΠΈΡ ΡΠΎΠ·Π΄Π°ΡΡ Π΄Π»Ρ ΠΆΠΈΠ΄ΠΊΠΎΡΡΠΈ ΡΠΎΠΏΡΠΎΡΠΈΠ²Π»Π΅Π½ΠΈΠ΅, ΠΏΡΠΎΠΏΠΎΡΡΠΈΠΎΠ½Π°Π»ΡΠ½ΠΎΠ΅ ΠΊΠ²Π°Π΄ΡΠ°ΡΡ ΡΠΊΠΎΡΠΎΡΡΠΈ Π΅Π΅ ΠΈΡΡΠ΅ΡΠ΅Π½ΠΈΡ. ΠΡΠΈ ΡΠ΅Π·ΠΊΠΎΠΌ ΡΠΆΠ°ΡΠΈΠΈ ΠΆΠΈΠ΄ΠΊΠΎΡΡΡ Π½Π΅ ΡΡΠΏΠ΅Π²Π°Π΅Ρ ΠΏΠ΅ΡΠ΅ΡΠ΅ΠΊΠ°ΡΡ ΡΠ΅ΡΠ΅Π· ΠΊΠ°Π»ΠΈΠ±ΡΠΎΠ²Π°Π½Π½ΡΠ΅ ΠΎΡΠ²Π΅ΡΡΡΠΈΡ, Π΄Π°Π²Π»Π΅Π½ΠΈΠ΅ Π² ΡΠ°Π±ΠΎΡΠ΅ΠΌ ΡΠΈΠ»ΠΈΠ½Π΄ΡΠ΅ Π²ΠΎΠ·ΡΠ°ΡΡΠ°Π΅Ρ ΠΈ ΠΎΡΠΊΡΡΠ²Π°Π΅ΡΡΡ ΠΊΠ»Π°ΠΏΠ°Π½ ΡΠΆΠ°ΡΠΈΡ. Π ΡΠ΅Π·ΡΠ»ΡΡΠ°ΡΠ΅ ΡΠΈΠ»Π° ΡΠΎΠΏΡΠΎΡΠΈΠ²Π»Π΅Π½ΠΈΡ Π°ΠΌΠΎΡΡΠΈΠ·Π°ΡΠΎΡΠ° ΡΠ²Π΅Π»ΠΈΡΠΈΠ²Π°Π΅ΡΡΡ ΠΌΠ΅Π½Π΅Π΅ ΠΈΠ½ΡΠ΅Π½ΡΠΈΠ²Π½ΠΎ.
Π ΠΈΡ. 5.8. Π£ΠΏΡΠ°Π²Π»ΡΠ΅ΠΌΡΠΉ ΠΌΠΎΡΡ Π°Π²ΡΠΎΠΌΠΎΠ±ΠΈΠ»Ρ ΠΠ°ΠΌΠΠ-5320:
1 β Π±Π°Π»ΠΊΠ° ΠΌΠΎΡΡΠ°; 2 β ΠΏΠΎΠΏΠ΅ΡΠ΅ΡΠ½Π°Ρ ΡΡΠ»Π΅Π²Π°Ρ ΡΡΠ³Π°; 3 β ΡΠΊΠ²ΠΎΡΠ΅Π½Ρ; 4 β ΠΏΠΎΠ΄ΡΠΈΠΏΠ½ΠΈΠΊ ΡΠΊΠΎΠ»ΡΠΆΠ΅Π½ΠΈΡ; 5 βΠΏΠΎΠ²ΠΎΡΠΎΡΠ½ΡΠΉ ΠΊΡΠ»Π°ΠΊ; 6 β ΡΠΏΠΎΡ ΠΏΠΎΠ²ΠΎΡΠΎΡΠ½ΠΎΠ³ΠΎ ΠΊΡΠ»Π°ΠΊΠ°; 7 β ΡΡΡΠ°Π³ ΠΏΠΎΠ²ΠΎΡΠΎΡΠ½ΠΎΠ³ΠΎ ΠΊΡΠ»Π°ΠΊΠ° ΠΊ ΡΡΠ³Π΅ ΡΠΎΡΠΊΠΈ ΡΡΠ»Π΅Π²ΠΎΠ³ΠΎ ΠΌΠ΅Ρ
Π°Π½ΠΈΠ·ΠΌΠ°; 8βΡΠ΅Π³ΡΠ»ΠΈΡΠΎΠ²ΠΎΡΠ½ΡΠ΅ ΡΠ°ΠΉΠ±Ρ; 9 β ΡΡΡΠ°Π³ ΠΏΠΎΠ²ΠΎΡΠΎΡΠ½ΠΎΠ³ΠΎ ΠΊΡΠ»Π°ΠΊΠ° ΠΊ ΡΡΠ³Π΅ ΡΡΠ»Π΅Π²ΠΎΠΉ ΡΡΠ°ΠΏΠ΅ΡΠΈΠΈ
ΠΡΠΈ ΠΏΠ»Π°Π²Π½ΠΎΠΉ ΠΎΡΠ΄Π°ΡΠ΅ ΡΡΠΎΠΊ Ρ ΠΏΠΎΡΡΠ½Π΅ΠΌ ΠΏΠ΅ΡΠ΅ΠΌΠ΅ΡΠ°Π΅ΡΡΡ Π²Π²Π΅ΡΡ . ΠΠΈΠ΄ΠΊΠΎΡΡΡ ΠΏΠ΅ΡΠ΅ΡΠ΅ΠΊΠ°Π΅Ρ Π² ΠΏΡΠΎΡΡΡΠ°Π½ΡΡΠ²ΠΎ ΠΏΠΎΠ΄ ΠΏΠΎΡΡΠ½Π΅ΠΌ ΡΠ΅ΡΠ΅Π· ΠΎΡΠ²Π΅ΡΡΡΠΈΡ Π² ΠΏΠΎΡΡΠ½Π΅ ΠΈ ΠΊΠ°Π»ΠΈΠ±ΡΠΎΠ²Π°Π½Π½ΡΠ΅ ΠΎΡΠ²Π΅ΡΡΡΠΈΡ Π² ΠΊΠ»Π°ΠΏΠ°Π½Π΅. ΠΡΠΎΠΌΠ΅ ΡΠΎΠ³ΠΎ, ΡΠ°ΡΡΡ ΠΆΠΈΠ΄ΠΊΠΎΡΡΠΈ Π²ΠΎΠ·Π²ΡΠ°ΡΠ°Π΅ΡΡΡ ΠΈΠ· ΠΊΠΎΠΌΠΏΠ΅Π½ΡΠ°ΡΠΈΠΎΠ½Π½ΠΎΠΉ ΠΏΠΎΠ»ΠΎΡΡΠΈ ΡΠ΅ΡΠ΅Π· ΠΊΠ»Π°ΠΏΠ°Π½ ΠΎΡΠ΄Π°ΡΠΈ. ΠΡΠΈ ΡΠ΅Π·ΠΊΠΎΠΉ ΠΎΡΠ΄Π°ΡΠ΅ ΠΏΠ΅ΡΠ΅ΡΠ΅ΠΊΠ°Π½ΠΈΠ΅ ΠΆΠΈΠ΄ΠΊΠΎΡΡΠΈ ΠΎΠ±Π΅ΡΠΏΠ΅ΡΠΈΠ²Π°Π΅ΡΡΡ ΠΎΡΠΊΡΡΡΠΈΠ΅ΠΌ ΠΊΠ»Π°ΠΏΠ°Π½Π° ΠΎΡΠ΄Π°ΡΠΈ. Π‘ΡΠ΅ΠΏΠ΅Π½Ρ ΠΎΡΠΊΡΡΡΠΈΡ ΠΊΠ»Π°ΠΏΠ°Π½Π° ΠΎΡΠ΄Π°ΡΠΈ Π·Π°Π²ΠΈΡΠΈΡ ΠΎΡ ΡΠ΅Π·ΠΊΠΎΡΡΠΈ Ρ ΠΎΠ΄Π° ΠΎΡΠ΄Π°ΡΠΈ: ΡΠ΅ΠΌ ΡΠ΅Π·ΡΠ΅ ΠΎΡΠ΄Π°ΡΠ°, ΡΠ΅ΠΌ Π±ΠΎΠ»ΡΡΠ΅ ΠΎΡΡ ΠΎΠ΄ΠΈΡ ΠΊΠ»Π°ΠΏΠ°Π½ ΠΎΡ ΡΠ²ΠΎΠ΅Π³ΠΎ ΡΠ΅Π΄Π»Π°.
Π Π΅ΠΊΠ»Π°ΠΌΠ°:
Π§ΠΈΡΠ°ΡΡ Π΄Π°Π»Π΅Π΅: Π£ΡΡΡΠΎΠΉΡΡΠ²ΠΎ ΠΌΠΎΡΡΠΎΠ² Π°Π²ΡΠΎΠΌΠΎΠ±ΠΈΠ»Π΅ΠΉ
ΠΠ°ΡΠ΅Π³ΠΎΡΠΈΡ: β ΠΠ²ΡΠΎΠΌΠΎΠ±ΠΈΠ»ΠΈ ΠΠ°ΠΌΠ°Π· Π£ΡΠ°Π»
ΠΠ»Π°Π²Π½Π°Ρ β Π‘ΠΏΡΠ°Π²ΠΎΡΠ½ΠΈΠΊ β Π‘ΡΠ°ΡΡΠΈ β Π€ΠΎΡΡΠΌ
stroy-technics.ru
ΠΠΠΠΠ Π΄Π²ΠΈΠ³Π°ΡΠ΅Π»Ρ. ΠΡΠ½ΠΎΠ²Π½ΡΠ΅ Ρ Π°ΡΠ°ΠΊΡΠ΅ΡΠΈΡΡΠΈΠΊΠΈ ΡΠΈΠ»ΠΎΠ²ΡΡ ΡΡΡΠ°Π½ΠΎΠ²ΠΎΠΊ
ΠΡΠ΅Π΄ΠΏΡΠΈΡΡΠΈΠ΅, ΠΏΠΎ Π²ΡΠΏΡΡΠΊΡ Π°Π²ΡΠΎΠΌΠΎΠ±ΠΈΠ»Π΅ΠΉ ΠΠΠΠΠ (ΠΠ°ΠΌΡΠΊΠΈΠΉ Π°Π²ΡΠΎΠΌΠΎΠ±ΠΈΠ»ΡΠ½ΡΠΉ Π·Π°Π²ΠΎΠ΄), Π±ΡΠ»ΠΎ ΠΎΡΠ½ΠΎΠ²Π°Π½ΠΎ Π² 1976 Π³ΠΎΠ΄Ρ. ΠΡΠΎ Π ΠΎΡΡΠΈΠΉΡΠΊΠ°Ρ ΠΊΠΎΠΌΠΏΠ°Π½ΠΈΡ, ΠΎΡΠ½ΠΎΠ²Π½ΡΠΌ Π·Π°Π½ΡΡΠΈΠ΅ΠΌ ΠΊΠΎΡΠΎΡΠΎΠΉ ΡΠ²Π»ΡΠ΅ΡΡΡ ΠΏΡΠΎΠΈΠ·Π²ΠΎΠ΄ΡΡΠ²ΠΎ Π³ΡΡΠ·ΠΎΠ²ΡΡ Π°Π²ΡΠΎΠΌΠΎΠ±ΠΈΠ»Π΅ΠΉ, ΡΠ°Π±ΠΎΡΠ°ΡΡΠΈΡ Π½Π° Π΄ΠΈΠ·Π΅Π»ΡΠ½ΠΎΠΌ ΡΠΎΠΏΠ»ΠΈΠ²Π΅. ΠΡΠΎΠΌΠ΅ ΡΠΎΠ³ΠΎ, Π²ΡΠΏΡΡΠΊΠ°ΡΡ Π°Π²ΡΠΎΠ±ΡΡΡ, ΡΡΠ°ΠΊΡΠΎΡΠ°, ΠΊΠΎΠΌΠ±Π°ΠΉΠ½Ρ, ΡΠ»Π΅ΠΊΡΡΠΎΡΡΠ°Π½ΡΠΈΠΈ ΠΈ Π΄ΡΡΠ³ΠΈΠ΅ ΠΊΠΎΠΌΠΏΠ»Π΅ΠΊΡΡΡΡΠΈΠ΅. Π‘ΠΈΠ»ΠΎΠ²ΡΠ΅ ΡΡΡΠ°Π½ΠΎΠ²ΠΊΠΈ, ΠΏΡΠΈΠΌΠ΅Π½ΡΠ΅ΠΌΡΠ΅ Π½Π° ΡΠ΅Ρ Π½ΠΈΠΊΠ΅, ΡΠ°Π·ΡΠ°Π±Π°ΡΡΠ²Π°Π»ΠΈΡΡ ΠΊΠΎΠ½ΡΡΡΡΠΊΡΠΎΡΠ°ΠΌΠΈ Π·Π°Π²ΠΎΠ΄Π°, ΠΈΠ·Π½Π°ΡΠ°Π»ΡΠ½ΠΎ Π·Π° ΠΎΡΠ½ΠΎΠ²Ρ Π±ΡΠ°Π»ΠΈΡΡ Π»ΡΡΡΠΈΠ΅ Π·Π°ΡΡΠ±Π΅ΠΆΠ½ΡΠ΅ Π°Π½Π°Π»ΠΎΠ³ΠΈ.
ΠΠ²ΠΈΠ³Π°ΡΠ΅Π»ΠΈ ΠΠΠΠΠ Π·Π° ΡΠ²ΠΎΠΉ Π½Π΅ΠΏΡΠΈΡ ΠΎΡΠ»ΠΈΠ²ΡΠΉ Π½ΡΠ°Π²: Π½Π°Π΄ΡΠΆΠ½ΠΎΡΡΡ, Π΄ΠΎΠ»Π³ΠΎΠ²Π΅ΡΠ½ΠΎΡΡΡ, ΠΏΡΠΎΡΡΠΎΡΡ ΠΊΠΎΠ½ΡΡΡΡΠΊΡΠΈΠΈ ΠΈ Π΄ΠΎΡΡΠΎΠΉΠ½ΡΠ΅ Ρ Π°ΡΠ°ΠΊΡΠ΅ΡΠΈΡΡΠΈΠΊΠΈ ΠΏΠΎΠ»ΡΡΠΈΠ»ΠΈ Π²ΡΡΠΎΠΊΡΡ ΠΎΡΠ΅Π½ΠΊΡ Ρ ΠΏΠΎΡΡΠ΅Π±ΠΈΡΠ΅Π»Π΅ΠΉ. ΠΠ° ΡΠ΅Π³ΠΎΠ΄Π½ΡΡΠ½ΠΈΠΉ Π΄Π΅Π½Ρ, ΡΡΠΎ ΠΎΠ΄Π½Π° ΠΈΠ· ΡΠ°ΠΌΡΡ ΠΏΠΎΠΏΡΠ»ΡΡΠ½ΡΡ ΠΌΠ°ΡΠΎΠΊ Π³ΡΡΠ·ΠΎΠ²ΡΡ Π°Π²ΡΠΎΠΌΠΎΠ±ΠΈΠ»Π΅ΠΉ, ΡΠΊΡΠΏΠ»ΡΠ°ΡΠΈΡΡΠ΅ΠΌΡΡ ΠΊΠ°ΠΊ Π² Π½Π°ΡΠ΅ΠΌ ΡΠ΅Π³ΠΈΠΎΠ½Π΅, ΡΠ°ΠΊ ΠΈ Π·Π° ΡΡΠ±Π΅ΠΆΠΎΠΌ.
Π’ΠΎΠ»ΡΠΎΠΊ Π² ΡΠ°Π·Π²ΠΈΡΠΈΠΈ ΠΏΡΠ΅Π΄ΠΏΡΠΈΡΡΠΈΡ Π±ΡΠ» Π΄Π°Π½ Π΄ΡΡΠ³ΠΈΠΌ Π·Π°Π²ΠΎΠ΄ΠΎΠΌ, ΠΠΠ (Π·Π°Π²ΠΎΠ΄ ΠΈΠΌΠ΅Π½ΠΈ ΠΠΈΡ Π°ΡΡΠ²Π°), Π΄ΠΎ 1956 Π³ΠΎΠ΄Π° ΠΈΠΌΠ΅Π½ΠΎΠ²Π°Π»ΡΡ ΠΠΠ‘ (Π·Π°Π²ΠΎΠ΄ ΠΈΠΌΠ΅Π½ΠΈ Π‘ΡΠ°Π»ΠΈΠ½Π°). Π 1976 Π³ΠΎΠ΄Ρ ΠΏΠΎ ΠΏΡΠΈΠΊΠ°Π·Ρ ΡΡΠΊΠΎΠ²ΠΎΠ΄ΡΡΠ²Π° Π²ΡΡ ΡΠ΅Ρ Π½ΠΈΡΠ΅ΡΠΊΠ°Ρ Π΄ΠΎΠΊΡΠΌΠ΅Π½ΡΠ°ΡΠΈΡ ΠΏΠΎ ΡΠ°Π·ΡΠ°Π±ΠΎΡΠΊΠ΅ Π°Π²ΡΠΎΠΌΠΎΠ±ΠΈΠ»Ρ ΠΠΠ-170, ΠΊΠΎΡΠΎΡΡΡ Π²ΡΠ» Π·Π°Π²ΠΎΠ΄, Π±ΡΠ»Π° ΠΏΠ΅ΡΠ΅Π΄Π°Π½Π° Π½Π° ΠΠΠΠΠ. Π’Π°ΠΊ, Π½Π°ΡΠ°Π»ΡΡ Π²ΡΠΏΡΡΠΊ Π°Π²ΡΠΎΠΌΠΎΠ±ΠΈΠ»Ρ ΠΠΠΠΠ-5320. ΠΠΎ 1980 Π³ΠΎΠ΄Π° ΠΠΠ ΡΠ°Π·ΡΠ°Π±ΠΎΡΠ°Π» 9 ΠΌΠΎΠ΄Π΅Π»Π΅ΠΉ ΠΠΠΠΠ, ΠΎΠ±ΡΡΠ°Π» ΠΊΠΎΠ»Π»Π΅ΠΊΡΠΈΠ² Π·Π°Π²ΠΎΠ΄Π° ΠΈ ΡΡΡΡΠ°Π½ΡΠ» Π½Π΅Π΄ΠΎΡΠ°Π±ΠΎΡΠΊΠΈ ΠΊΠΎΠ½ΡΡΡΡΠΊΡΠΈΠΈ.
ΠΠ° Π²ΡΡ ΡΠ²ΠΎΡ ΠΈΡΡΠΎΡΠΈΡ Π±ΡΠ»ΠΎ Π²ΡΠΏΡΡΠ΅Π½ΠΎ ΠΎΠ³ΡΠΎΠΌΠ½ΠΎΠ΅ ΠΊΠΎΠ»ΠΈΡΠ΅ΡΡΠ²ΠΎ ΡΠΈΠ»ΠΎΠ²ΡΡ Π°Π³ΡΠ΅Π³Π°ΡΠΎΠ². Π‘Π°ΠΌΡΡ Π±ΠΎΠ»ΡΡΡΡ ΠΏΠΎΠΏΡΠ»ΡΡΠ½ΠΎΡΡΡ ΠΏΠΎΠ»ΡΡΠΈΠ»Π° ΡΠ΅ΡΠΈΡ ΠΠΠΠΠ 740. ΠΠ°ΡΠΈΠ°Π½ΡΠΎΠ² ΡΠΈΠ»ΠΎΠ²ΡΡ ΡΡΡΠ°Π½ΠΎΠ²ΠΎΠΊ 740-ΠΉ ΡΠ΅ΡΠΈΠΈ Π½Π΅ΡΠΊΠΎΠ»ΡΠΊΠΎ, ΠΎΡΠ½ΠΎΠ²Π½ΡΠΌΠΈ ΠΎΡΠ»ΠΈΡΠΈΡΠΌΠΈ ΠΈΡ Π΄ΡΡΠ³ ΠΎΡ Π΄ΡΡΠ³Π° Π±ΡΠ»ΠΎ ΡΠΎΠΎΡΠ²Π΅ΡΡΡΠ²ΠΈΠ΅ ΡΠΎΠΌΡ ΠΈΠ»ΠΈ ΠΈΠ½ΠΎΠΌΡ ΡΡΠ°Π½Π΄Π°ΡΡΡ ΠΠ²ΡΠΎ.
ΠΠΎΡΠΎΡΡ ΠΏΠΎΠ»ΡΡΠΈΠ»ΠΈΡΡ ΡΠ΄Π°ΡΠ½ΡΠΌΠΈ, Π΄Π»ΠΈΡΠ΅Π»ΡΠ½ΠΎΠ΅ Π²ΡΠ΅ΠΌΡ Π΄ΡΡΠ³ΠΈΠ΅ ΠΏΡΠΎΠΈΠ·Π²ΠΎΠ΄ΠΈΡΠ΅Π»ΠΈ Π·Π°ΠΊΡΠΏΠ°Π»ΠΈ ΠΈΡ Π΄Π»Ρ ΡΡΡΠ°Π½ΠΎΠ²ΠΊΠΈ Π½Π° ΡΠ²ΠΎΠΈ Π°Π²ΡΠΎΠΌΠΎΠ±ΠΈΠ»ΠΈ. Π’Π°ΠΊ, Ρ 1979 ΠΏΠΎ 1992 Π³ΠΎΠ΄Ρ Π²ΡΠΏΡΡΠΊΠ°Π»ΠΈ Π°Π²ΡΠΎΠΌΠΎΠ±ΠΈΠ»Ρ ΠΠΠ Ρ Π΄Π²ΠΈΠ³Π°ΡΠ΅Π»Π΅ΠΌ ΠΠΠΠΠ. ΠΡΠΎ Π±ΡΠ»ΠΈ ΡΠ°ΠΊΠΈΠ΅ ΠΌΠΎΠ΄ΠΈΡΠΈΠΊΠ°ΡΠΈΠΈ: ΠΠΠ-133Π2 ΠΈ ΠΠΠ-133ΠΠ― (ΡΡΠ³Π°Ρ, ΡΠ°ΠΌΠΎΡΠ²Π°Π» ΠΈ ΠΊΡΠ°Π½) Ρ ΡΠΈΠ»ΠΎΠ²ΡΠΌΠΈ ΡΡΡΠ°Π½ΠΎΠ²ΠΊΠ°ΠΌΠΈ ΠΠΠΠΠ-740; ΠΠΠ-Π133ΠΠ―Π’ (ΡΡΠ³Π°Ρ) Ρ Π°Π³ΡΠ΅Π³Π°ΡΠΎΠΌ ΠΠΠΠΠ-7403.
ΠΡΠ½ΠΎΠ²Π½ΡΠ΅ Ρ Π°ΡΠ°ΠΊΡΠ΅ΡΠΈΡΡΠΈΠΊΠΈ ΡΠΈΠ»ΠΎΠ²ΡΡ ΡΡΡΠ°Π½ΠΎΠ²ΠΎΠΊ ΡΠ΅ΡΠΈΠΈ 740
Π ΠΎΠ΄ΠΎΠ½Π°ΡΠ°Π»ΡΠ½ΠΈΠΊΠΎΠΌ ΡΠ΅ΡΠΈΠΈ Π΄Π²ΠΈΠ³Π°ΡΠ΅Π»Π΅ΠΉ Π±ΡΠ»Π° ΠΌΠΎΠ΄Π΅Π»Ρ ΠΠΠΠΠ 740 V8, ΠΏΠ΅ΡΠ²ΡΠ΅ ΠΌΠΎΠ΄Π΅Π»ΠΈ ΡΡΠΎΠ³ΠΎ ΠΌΠΎΡΠΎΡΠ° ΠΈΠΌΠ΅Π»ΠΈ ΠΎΠ±ΡΡΠΌ 10852 ΡΠΌ3, ΠΏΡΠΈ ΡΡΠΎΠΌ ΠΌΠΎΡΠ½ΠΎΡΡΡ ΡΠ°Π·Π²ΠΈΠ²Π°Π»ΠΈ Π΄ΠΎ 210 Π»ΠΎΡΠ°Π΄ΠΈΠ½ΡΡ ΡΠΈΠ». ΠΠΎΠ»Π΅Π΅ ΠΏΠΎΠ·Π΄Π½ΠΈΠ΅ ΠΌΠΎΠ΄Π΅Π»ΠΈ Π²ΡΡ ΠΎΠ΄ΠΈΠ»ΠΈ Ρ ΠΌΠΎΡΠ½ΠΎΡΡΡΡ Π² Π΄ΠΈΠ°ΠΏΠ°Π·ΠΎΠ½Π΅ ΠΎΡ 180-360 Π»Ρ. ΠΡΠ΅ ΡΠΈΠ»ΠΎΠ²ΡΠ΅ ΡΡΡΠ°Π½ΠΎΠ²ΠΊΠΈ ΠΠΠΠΠΠ° ΡΠ°Π±ΠΎΡΠ°ΡΡ Π½Π° Π΄ΠΈΠ·Π΅Π»ΡΠ½ΠΎΠΌ ΡΠΎΠΏΠ»ΠΈΠ²Π΅, Π²ΡΠ±ΠΎΡ Π² Π΅Π³ΠΎ ΠΏΠΎΠ»ΡΠ·Ρ Π½Π΅ ΡΠ»ΡΡΠ°Π΅Π½: Π²ΠΎ-ΠΏΠ΅ΡΠ²ΡΡ , ΡΠ°ΡΡ ΠΎΠ΄ΡΠ΅ΡΡΡ ΠΌΠ΅Π½ΡΡΠ΅ Π³ΠΎΡΡΡΠ΅Π³ΠΎ, Π²ΠΎ-Π²ΡΠΎΡΡΡ , ΠΏΡΠΎΠΈΡΡ ΠΎΠ΄ΠΈΡ Π»ΡΡΡΠ΅ ΡΠΌΠ°Π·ΠΊΠ° Π΄Π²ΠΈΠ³Π°ΡΠ΅Π»Ρ ΠΈ Π΅Π³ΠΎ Π΄Π΅ΡΠ°Π»Π΅ΠΉ, Π²-ΡΡΠ΅ΡΡΠΈΡ , ΡΠΈΠ»ΠΎΠ²Π°Ρ ΡΡΡΠ°Π½ΠΎΠ²ΠΊΠ° ΠΎΠ±Π»Π°Π΄Π°Π΅Ρ Π±ΠΎΠ»ΡΡΠ΅ΠΉ ΠΌΠΎΡΠ½ΠΎΡΡΡΡ.
ΠΡΠΎΠ±Π΅Π½Π½ΠΎΡΡΡΡ ΡΠ°Π±ΠΎΡΡ Π΄Π²ΠΈΠ³Π°ΡΠ΅Π»Π΅ΠΉ ΠΠΠΠΠ ΠΌΠΎΠΆΠ½ΠΎ ΡΡΠΈΡΠ°ΡΡ ΠΈ ΡΠ°ΠΊΠΎΠΉ ΠΏΠΎΠΊΠ°Π·Π°ΡΠ΅Π»Ρ, ΠΊΠ°ΠΊ ΡΠ²Π΅Π»ΠΈΡΠ΅Π½Π½Π°Ρ ΡΡΠ΅ΠΏΠ΅Π½Ρ ΡΠΆΠ°ΡΠΈΡ, ΠΏΠΎ ΡΡΠ°Π²Π½Π΅Π½ΠΈΡ Ρ Π±Π΅Π½Π·ΠΈΠ½ΠΎΠ²ΡΠΌΠΈ Π΄Π²ΠΈΠ³Π°ΡΠ΅Π»ΡΠΌΠΈ Π²Π½ΡΡΡΠ΅Π½Π½Π΅Π³ΠΎ ΡΠ³ΠΎΡΠ°Π½ΠΈΡ. Π’Π°ΠΊ, Π±Π΅Π½Π·ΠΈΠ½ΠΎΠ²ΡΠ΅ ΡΠΈΠ»ΠΎΠ²ΡΠ΅ ΡΡΡΠ°Π½ΠΎΠ²ΠΊΠΈ ΠΈΠΌΠ΅ΡΡ ΡΡΠ΅ΠΏΠ΅Π½Ρ 8-10 Π΅Π΄ΠΈΠ½ΠΈΡ, ΡΠΎΠ³Π΄Π° ΠΊΠ°ΠΊ ΠΠΠΠΠ Π΄Π²ΠΈΠ³Π°ΡΠ΅Π»Ρ 17 Π΅Π΄ΠΈΠ½ΠΈΡ. ΠΡΠΎΠΌΠ΅ ΡΠΎΠ³ΠΎ, Π² ΠΌΠΎΡΠΎΡΠ°Ρ ΠΎΡΡΡΡΡΡΠ²ΡΡΡ ΡΠ²Π΅ΡΠΈ Π·Π°ΠΆΠΈΠ³Π°Π½ΠΈΡ, ΡΡΠΎ ΠΎΠ±ΡΡΠ»ΠΎΠ²Π»Π΅Π½ΠΎ ΡΠΏΠ΅ΡΠΈΡΠΈΠΊΠΎΠΉ ΡΠ°Π±ΠΎΡΡ Π΄ΠΈΠ·Π΅Π»Ρ. ΠΠΎΡΠΏΠ»Π°ΠΌΠ΅Π½Π΅Π½ΠΈΠ΅ ΠΈ ΡΠ³ΠΎΡΠ°Π½ΠΈΠ΅ Π² ΡΠ°ΠΊΠΈΡ ΡΠΈΠ»ΠΎΠ²ΡΡ ΡΡΡΠ°Π½ΠΎΠ²ΠΊΠ°Ρ ΠΏΡΠΎΠΈΡΡ ΠΎΠ΄ΠΈΡ Π·Π° ΡΡΡΡ Π²ΡΡΠΎΠΊΠΎΠ³ΠΎ Π΄Π°Π²Π»Π΅Π½ΠΈΡ.
ΠΡΠ»Π΅Π΄ΡΡΠ²ΠΈΠ΅ Π΄Π²ΠΈΠΆΠ΅Π½ΠΈΡ ΠΏΠΎΡΡΠ½Ρ Π² ΠΏΠΎΠ»ΠΎΠΆΠ΅Π½ΠΈΠ΅ Π²Π΅ΡΡ Π½Π΅ΠΉ ΠΌΡΡΡΠ²ΠΎΠΉ ΡΠΎΡΠΊΠΈ, Π²Π½ΡΡΡΠ΅Π½Π½ΠΈΠΉ ΠΎΠ±ΡΡΠΌ ΡΠ΅Π·ΠΊΠΎ ΡΠΌΠ΅Π½ΡΡΠ°Π΅ΡΡΡ, ΠΏΡΠΎΠΈΡΡ ΠΎΠ΄ΠΈΡ ΡΠΊΠ°ΡΠΎΠΊ ΡΠ²Π΅Π»ΠΈΡΠ΅Π½ΠΈΡ Π΄Π°Π²Π»Π΅Π½ΠΈΡ ΠΈ ΡΠ΅ΠΌΠΏΠ΅ΡΠ°ΡΡΡΡ. ΠΠΌΠ΅Π½Π½ΠΎ ΠΏΠΎ ΡΡΠΎΠΌΡ ΠΏΡΠΈΠ½ΡΠΈΠΏΡ ΡΠ°Π±ΠΎΡΠ°Π΅Ρ Π΄ΠΈΠ·Π΅Π»ΡΠ½ΡΠΉ ΠΌΠΎΡΠΎΡ.
Π ΠΌΠ°ΡΠΊΠΈΡΠΎΠ²ΠΊΠ΅ ΡΠ²ΠΎΠ΅ΠΉ ΠΏΡΠΎΠ΄ΡΠΊΡΠΈΠΈ ΠΏΡΠΎΠΈΠ·Π²ΠΎΠ΄ΠΈΡΠ΅Π»Ρ ΠΈΡΠΏΠΎΠ»ΡΠ·ΡΠ΅Ρ ΡΠ°Π·Π»ΠΈΡΠ½ΡΠ΅ ΠΎΠ±ΠΎΠ·Π½Π°ΡΠ΅Π½ΠΈΡ, ΠΊΠΎΡΠΎΡΡΠ΅ ΠΎΡΠ²Π΅ΡΠ°ΡΡ Π·Π° ΡΠΈΠΏ ΡΠΈΠ»ΠΎΠ²ΠΎΠΉ ΡΡΡΠ°Π½ΠΎΠ²ΠΊΠΈ:
- VβΡΠΈΠ»ΠΈΠ½Π΄ΡΡ ΠΌΠΎΡΠΎΡΠ° ΡΠ°ΡΠΏΠΎΠ»ΠΎΠΆΠ΅Π½Ρ Π² Π΄Π²Π° ΡΡΠ΄Π°, ΡΠ³ΠΎΠ» ΠΌΠ΅ΠΆΠ΄Ρ ΠΊΠΎΡΠΎΡΡΠΌΠΈ ΠΌΠ΅Π½Π΅Π΅ 90Β°;
- LβΡΠΈΠ»ΠΈΠ½Π΄ΡΡ ΡΠ°ΡΠΏΠΎΠ»ΠΎΠΆΠ΅Π½Ρ Π² Π΄Π²Π° ΡΡΠ΄Π°, ΡΠ³ΠΎΠ» ΠΌΠ΅ΠΆΠ΄Ρ ΠΊΠΎΡΠΎΡΡΠΌΠΈ ΠΏΡΠΈΠ±Π»ΠΈΠΆΠ°Π΅ΡΡΡ ΠΊ 90Β°;
- RβΡΠ°ΡΠΏΠΎΠ»ΠΎΠΆΠ΅Π½ΠΈΠ΅ ΡΠΈΠ»ΠΈΠ½Π΄ΡΠΎΠ² ΡΡΠ΄Π½ΠΎΠ΅.
Π‘ΠΈΠ»ΠΎΠ²Π°Ρ ΡΡΡΠ°Π½ΠΎΠ²ΠΊΠ° ΠΠΠΠΠ 740
ΠΠ°ΠΌΠ°Π·ΠΎΠ²ΡΠΊΠΈΠΉ Π΄Π²ΠΈΠ³Π°ΡΠ΅Π»Ρ 740-ΠΉ ΠΌΠΎΠ΄ΠΈΡΠΈΠΊΠ°ΡΠΈΠΈ ΠΈΠΌΠ΅Π΅Ρ ΡΡΠ΄ ΠΏΡΠ΅ΠΈΠΌΡΡΠ΅ΡΡΠ² ΠΈ ΠΎΡΠΎΠ±Π΅Π½Π½ΠΎΡΡΠ΅ΠΉ ΠΏΠ΅ΡΠ΅Π΄ ΡΠ²ΠΎΠΈΠΌΠΈ ΠΊΠΎΠ½ΠΊΡΡΠ΅Π½ΡΠ°ΠΌΠΈ:
- Π‘ΡΡΠΎΠ΅Π½ΠΈΠ΅ ΠΌΠΎΡΠΎΡΠ° ΡΠ°ΠΊΠΎΠ²ΠΎ, ΡΡΠΎ ΠΏΡΠΈ ΡΠ΅Ρ ΠΆΠ΅ Ρ Π°ΡΠ°ΠΊΡΠ΅ΡΠΈΡΡΠΈΠΊΠ°Ρ , ΠΊΠ°ΠΊ Ρ Π°Π½Π°Π»ΠΎΠ³ΠΈΡΠ½ΡΡ ΠΏΡΠΎΠΈΠ·Π²ΠΎΠ΄ΠΈΡΠ΅Π»Π΅ΠΉ, ΠΎΠ½ Π·Π½Π°ΡΠΈΡΠ΅Π»ΡΠ½ΠΎ ΠΌΠ΅Π½ΡΡΠΈΡ ΡΠ°Π·ΠΌΠ΅ΡΠΎΠ². ΠΠΎΡΠΎΡ ΡΠ²Π»ΡΠ΅ΡΡΡ ΡΠ²ΠΎΠ΅ΠΎΠ±ΡΠ°Π·Π½ΡΠΌ ΠΊΠΎΠΌΠΏΡΠΎΠΌΠΈΡΡΠΎΠΌ ΠΌΠ΅ΠΆΠ΄Ρ Π±ΠΎΠ»ΡΡΠΈΠΌΠΈ, Π½ΠΎ ΠΌΠ°Π»ΠΎΠΌΠΎΡΠ½ΡΠΌΠΈ ΡΡΡΠ°Π½ΠΎΠ²ΠΊΠ°ΠΌΠΈ, ΠΏΠΎΡΡΠ΅Π±Π»ΡΡΡΠΈΠΌΠΈ Π΄ΠΎΡΡΠ°ΡΠΎΡΠ½ΠΎ Π±ΠΎΠ»ΡΡΠΎΠ΅ ΠΊΠΎΠ»ΠΈΡΠ΅ΡΡΠ²ΠΎ ΡΠΎΠΏΠ»ΠΈΠ²Π°, ΠΈ Π΄ΠΎΠ²ΠΎΠ»ΡΠ½ΠΎ Π½Π°Π΄ΡΠΆΠ½ΡΠΌΠΈ, ΠΈ ΠΌΠΎΡΠ½ΡΠΌΠΈ, ΡΠΊΠΎΠ½ΠΎΠΌΠΈΡΠ½ΡΠΌΠΈ, Π½ΠΎ ΠΌΠ΅Π½Π΅Π΅ Π½Π°Π΄ΡΠΆΠ½ΡΠΌΠΈ ΠΈ Π²ΡΠ½ΠΎΡΠ»ΠΈΠ²ΡΠΌΠΈ.
- ΠΠ²ΡΠΎΠΌΠΎΠ±ΠΈΠ»Ρ ΠΏΡΠΈΠΎΠ±ΡΡΠ» ΡΠΈΡΠΎΠΊΡΡ ΡΠ°ΡΠΏΡΠΎΡΡΡΠ°Π½ΡΠ½Π½ΠΎΡΡΡ, Π±Π»Π°Π³ΠΎΠ΄Π°ΡΡ Π²ΠΎΠ·ΠΌΠΎΠΆΠ½ΠΎΡΡΠΈ ΡΠ°Π±ΠΎΡΠ°ΡΡ Π² ΡΡΠ»ΠΎΠ²ΠΈΡΡ Π½ΠΈΠ·ΠΊΠΈΡ ΡΠ΅ΠΌΠΏΠ΅ΡΠ°ΡΡΡ. Π ΡΠ°ΡΡΠ½ΠΎΡΡΠΈ, Ρ ΠΠΠΠΠΠ° Π½Π΅ Π²ΠΎΠ·Π½ΠΈΠΊΠ°Π΅Ρ ΠΏΡΠΎΠ±Π»Π΅ΠΌ Ρ Π·Π°ΠΏΡΡΠΊΠΎΠΌ Π² Ρ ΠΎΠ»ΠΎΠ΄Π½ΠΎΠ΅ Π²ΡΠ΅ΠΌΡ Π³ΠΎΠ΄Π°. ΠΠΎΡΠΎΡ ΠΈΠΌΠ΅Π΅Ρ ΠΌΠΎΡΠ½ΡΠΉ Π°ΠΊΠΊΡΠΌΡΠ»ΡΡΠΎΡ ΠΈ ΡΡΠ°ΡΡΠ΅Ρ, Π° ΡΠ°ΠΊ ΠΆΠ΅ ΡΠΈΡΡΠ΅ΠΌΡ Π½Π°Π³ΡΠ΅Π²Π° Π΄Π²ΠΈΠ³Π°ΡΠ΅Π»Ρ.
- ΠΡΠΈΠ²ΠΎΠ΄ ΡΠΈΡΡΠ΅ΠΌΡ Π³Π°Π·ΠΎΡΠ°ΡΠΏΡΠ΅Π΄Π΅Π»Π΅Π½ΠΈΡ, ΠΊΠΎΠΌΠΏΡΠ΅ΡΡΠΎΡΡ, Π³ΠΈΠ΄ΡΠ°Π²Π»ΠΈΡΠ΅ΡΠΊΠΈΠΉ ΡΡΠΈΠ»ΠΈΡΠ΅Π»Ρ, Π½Π°ΡΠΎΡ: ΡΠ°Π±ΠΎΡΠ°ΡΡ Π·Π° ΡΡΡΡ ΠΏΠ΅ΡΠ΅Π΄Π°ΡΠΈ ΠΊΡΡΡΡΡΠ΅Π³ΠΎ ΠΌΠΎΠΌΠ΅Π½ΡΠ° ΠΎΡ ΠΌΠΎΡΠΎΡΠ° ΠΏΠΎΡΡΠ΅Π΄ΡΡΠ²ΠΎΠΌ ΡΠ΅ΡΡΠ΅ΡΡΠ½ΡΠ°ΡΡΡ ΠΏΠ΅ΡΠ΅Π΄Π°Ρ Ρ ΠΏΡΡΠΌΡΠΌΠΈ Π·ΡΠ±ΡΡΠΌΠΈ .
Π‘ΠΈΠ»ΠΎΠ²ΡΠ΅ ΡΡΡΠ°Π½ΠΎΠ²ΠΊΠΈ ΠΠ²ΡΠΎ ΠΊΠ»Π°ΡΡΠ°
ΠΡΠ½ΠΎΠ²Π°ΡΠ΅Π»Π΅ΠΌ Π΄Π²ΠΈΠ³Π°ΡΠ΅Π»Π΅ΠΉ ΠΠΠΠΠ 740-ΠΉ ΡΠ΅ΡΠΈΠΈ ΠΌΠΎΠΆΠ½ΠΎ ΡΡΠΈΡΠ°ΡΡ ΠΌΠΎΠ΄Π΅Π»Ρ ΠΠ²ΡΠΎ 0. ΠΡΠΎ ΠΎΡΠ΅Π½Ρ Π½Π°Π΄ΡΠΆΠ½ΡΠΉ Π°Π³ΡΠ΅Π³Π°Ρ, ΠΈΠΌΠ΅ΡΡΠΈΠΉ Ρ ΠΎΡΠΎΡΠΈΠ΅ ΡΠ΅Ρ Π½ΠΈΡΠ΅ΡΠΊΠΈΠ΅ Ρ Π°ΡΠ°ΠΊΡΠ΅ΡΠΈΡΡΠΈΠΊΠΈ, Π²ΡΡΠΎΠΊΡΡ Π½Π°Π΄ΡΠΆΠ½ΠΎΡΡΡ ΠΈ ΡΠ΅ΡΡΡΡ. ΠΠ΄Π½Π°ΠΊΠΎ, ΠΌΠΎΡΠΎΡ ΠΠΠΠΠ Π½Π΅ ΡΠΎΠΎΡΠ²Π΅ΡΡΡΠ²ΠΎΠ²Π°Π» ΠΊΠ»Π°ΡΡΠ°ΠΌ ΡΠΊΠΎΠ»ΠΎΠ³ΠΈΡΠ΅ΡΠΊΠΎΠΉ Π±Π΅Π·ΠΎΠΏΠ°ΡΠ½ΠΎΡΡΠΈ ΠΈ ΡΡΠΎ Π±ΡΠ» ΠΎΡΠ½ΠΎΠ²Π½ΠΎΠΉ Π΅Π³ΠΎ ΠΌΠΈΠ½ΡΡ.
Π‘ΠΈΠ»ΠΎΠ²Π°Ρ ΡΡΡΠ°Π½ΠΎΠ²ΠΊΠ° ΠΠΠΠΠ (ΠΠ²ΡΠΎ 0)
ΠΠΎΠ΄Π΅Π»Ρ ΡΠΈΠ»ΠΎΠ²ΠΎΠΉ ΡΡΡΠ°Π½ΠΎΠ²ΠΊΠΈ | 740-210 | 740-260 |
ΠΠΎΡΠ½ΠΎΡΡΡ, Π»Ρ | 210 | 260 |
ΠΠΎΠ»Π΅Π½ΡΠ°ΡΡΠΉ Π²Π°Π», ΡΠ°ΡΡΠΎΡΠ° Π²ΡΠ°ΡΠ΅Π½ΠΈΡ | 2600 | |
ΠΡΡΡΡΡΠΈΠΉ ΠΌΠΎΠΌΠ΅Π½Ρ, ΠΠΌ | 667 | 765 |
Π¦ΠΈΠ»ΠΈΠ½Π΄ΡΡ, ΡΡΡΠΊ, ΡΠ°ΡΠΏΠΎΠ»ΠΎΠΆΠ΅Π½ΠΈΠ΅ | 8, V | |
Π¦ΠΈΠ»ΠΈΠ½Π΄Ρ, Γ/ΠΠΎΡΡΠ΅Π½Ρ, Ρ ΠΎΠ΄, ΠΌΠΌ | 120/120 | |
ΠΠ²ΠΈΠ³Π°ΡΠ΅Π»Ρ, ΠΎΠ±ΡΡΠΌ, Π». | 10,85 | |
Π’ΠΎΠΏΠ»ΠΈΠ²Π½Π°Ρ ΡΠΌΠ΅ΡΡ, ΡΡΠ΅ΠΏΠ΅Π½Ρ ΡΠΆΠ°ΡΠΈΡ | 17 | 16,5 |
Π¦ΠΈΠ»ΠΈΠ½Π΄ΡΡ, ΡΠ°Π±ΠΎΡΠ° | 1,5,4,2,6,3,7,8 | |
ΠΠΎΠ»Π΅Π½ΡΠ°ΡΡΠΉ Π²Π°Π», Π½Π°ΠΏΡΠ°Π²Π»Π΅Π½ΠΈΠ΅ Π²ΡΠ°ΡΠ΅Π½ΠΈΡ | ΠΏΡΠ°Π²ΠΎΠ΅ | |
ΠΠ²ΠΈΠ³Π°ΡΠ΅Π»Ρ, Π²Π΅Ρ, Π±ΡΡΡΡΠΎ, ΠΊΠ³. | 750 | 780 |
Π‘ΠΈΡΡΠ΅ΠΌΠ° ΡΠΌΠ°Π·ΠΊΠΈ, Π». | 26 | 28 |
Π‘ΠΈΡΡΠ΅ΠΌΠ° ΠΎΡ Π»Π°ΠΆΠ΄Π΅Π½ΠΈΡ, Π». | 18 |
Π‘ΠΈΠ»ΠΎΠ²ΡΠ΅ ΡΡΡΠ°Π½ΠΎΠ²ΠΊΠΈ ΠΠΠΠΠ ΠΠ²ΡΠΎ 2 Π±ΡΠ»ΠΈ Π±ΠΎΠ»Π΅Π΅ ΡΠΎΠ²ΡΠ΅ΠΌΠ΅Π½Π½Ρ ΠΈ Π΄ΠΎΡΠ°Π±ΠΎΡΠ°Π½Ρ, ΠΏΠΎ ΡΡΠ°Π²Π½Π΅Π½ΠΈΡ Ρ ΠΏΡΠ΅Π΄ΡΠ΅ΡΡΠ²ΡΡΡΠΈΠΌ ΠΊΠ»Π°ΡΡΠΎΠΌ. ΠΠ° ΡΠΎ Π²ΡΠ΅ΠΌΡ ΠΎΠ½ΠΈ ΡΠΎΠΎΡΠ²Π΅ΡΡΡΠ²ΠΎΠ²Π°Π»ΠΈ Π²ΡΠ΅ΠΌ ΡΡΠ΅Π±ΠΎΠ²Π°Π½ΠΈΡΠΌ, ΠΏΡΠ΅Π΄ΡΡΠ²Π»ΡΠ΅ΠΌΡΠΌ Π°Π³ΡΠ΅Π³Π°ΡΠ°ΠΌ Π² ΠΏΠ»Π°Π½Π΅ ΡΠΊΠΎΠ»ΠΎΠ³ΠΈΡΠ΅ΡΠΊΠΎΠΉ Π±Π΅Π·ΠΎΠΏΠ°ΡΠ½ΠΎΡΡΠΈ. ΠΠΎΠ΄ΠΈΡΠΈΠΊΠ°ΡΠΈΠΉ ΠΌΠΎΡΠΎΡΠΎΠ² Π±ΡΠ»ΠΎ 4, ΠΈΡ Ρ Π°ΡΠ°ΠΊΡΠ΅ΡΠΈΡΡΠΈΠΊΠΈ ΡΠ»Π΅Π΄ΡΡΡΠΈΠ΅:
Π‘ΠΈΠ»ΠΎΠ²Π°Ρ ΡΡΡΠ°Π½ΠΎΠ²ΠΊΠ° ΠΠΠΠΠ (ΠΠ²ΡΠΎ 2)
ΠΠΎΠ΄Π΅Π»Ρ ΡΠΈΠ»ΠΎΠ²ΠΎΠΉ ΡΡΡΠ°Π½ΠΎΠ²ΠΊΠΈ | 740.31-240 | 740.30-260 | 740.51-320 | 740.50-360 |
ΠΠΎΡΠ½ΠΎΡΡΡ, Π»Ρ | 240 | 260 | 320 | 360 |
ΠΠΎΠ»Π΅Π½ΡΠ°ΡΡΠΉ Π²Π°Π», ΡΠ°ΡΡΠΎΡΠ° Π²ΡΠ°ΡΠ΅Π½ΠΈΡ | 2200 | |||
ΠΡΡΡΡΡΠΈΠΉ ΠΌΠΎΠΌΠ΅Π½Ρ, ΠΠΌ | 980 | 1078 | 1020 | 1147 |
Π¦ΠΈΠ»ΠΈΠ½Π΄ΡΡ, ΡΡΡΠΊ, ΡΠ°ΡΠΏΠΎΠ»ΠΎΠΆΠ΅Π½ΠΈΠ΅ | 8, V | |||
Π¦ΠΈΠ»ΠΈΠ½Π΄Ρ, Γ/ΠΠΎΡΡΠ΅Π½Ρ, Ρ ΠΎΠ΄, ΠΌΠΌ | 120/120 | 120/130 | ||
ΠΠ²ΠΈΠ³Π°ΡΠ΅Π»Ρ, ΠΎΠ±ΡΡΠΌ, Π». | 10,85 | 10,85 | 11,76 | 11,76 |
Π’ΠΎΠΏΠ»ΠΈΠ²Π½Π°Ρ ΡΠΌΠ΅ΡΡ, ΡΡΠ΅ΠΏΠ΅Π½Ρ ΡΠΆΠ°ΡΠΈΡ | 16 | 16,5 | 16,5 | 16,5 |
Π¦ΠΈΠ»ΠΈΠ½Π΄ΡΡ, ΡΠ°Π±ΠΎΡΠ° | 1,5,4,2,6,3,7,8 | |||
ΠΠΎΠ»Π΅Π½ΡΠ°ΡΡΠΉ Π²Π°Π», Π²ΡΠ°ΡΠ΅Π½ΠΈΠ΅ | ΠΏΡΠ°Π²ΠΎΠ΅ | |||
ΠΠ²ΠΈΠ³Π°ΡΠ΅Π»Ρ, Π²Π΅Ρ, Π±ΡΡΡΡΠΎ, ΠΊΠ³. | 760 | 885 | 885 | 885 |
Π‘ΠΈΡΡΠ΅ΠΌΠ° ΡΠΌΠ°Π·ΠΊΠΈ, Π». | 26 | 28 | 28 | 28 |
Π‘ΠΈΡΡΠ΅ΠΌΠ° ΠΎΡ Π»Π°ΠΆΠ΄Π΅Π½ΠΈΡ, Π». | 18 |
Π‘ΠΈΠ»ΠΎΠ²ΡΠ΅ ΡΡΡΠ°Π½ΠΎΠ²ΠΊΠΈ ΠΠΠΠΠ ΠΠ²ΡΠΎ 3 Π±ΡΠ»ΠΈ ΠΏΠ΅ΡΠ΅Ρ ΠΎΠ΄Π½ΡΠΌ Π·Π²Π΅Π½ΠΎΠΌ ΠΌΠ΅ΠΆΠ΄Ρ ΠΠ²ΡΠΎ 2 ΠΈ ΠΠ²ΡΠΎ 4. ΠΠΎΠ»Π΅Π΅ ΡΠΎΠ²ΡΠ΅ΠΌΠ΅Π½Π½ΡΠΌΠΈ ΠΈ Π²ΠΎΡΡΡΠ΅Π±ΠΎΠ²Π°Π½Π½ΡΠΌΠΈ ΠΌΠΎΡΠΎΡΠ°ΠΌΠΈ ΡΠ²Π»ΡΡΡΡΡ Π°Π³ΡΠ΅Π³Π°ΡΡ ΠΌΠΎΠ΄ΠΈΡΠΈΠΊΠ°ΡΠΈΠΈ ΠΠ²ΡΠΎ 4. ΠΠ²ΠΈΠ³Π°ΡΠ΅Π»ΠΈ ΠΠΠΠΠ ΡΠ΅Ρ Π½ΠΈΡΠ΅ΡΠΊΠΈΠ΅ Ρ Π°ΡΠ°ΠΊΡΠ΅ΡΠΈΡΡΠΈΠΊΠΈ:
Π‘ΠΈΠ»ΠΎΠ²ΡΠ΅ ΡΡΡΠ°Π½ΠΎΠ²ΠΊΠΈ ΠΠΠΠΠ (ΠΠ²ΡΠΎ 4)
ΠΠΎΠ΄Π΅Π»Ρ ΡΡΡΠ°Π½ΠΎΠ²ΠΊΠΈ | 740.70-280 | 740.71.320 | 740.72-360 | 740.73-400 | 740.74-420 | 740.75-440 |
Π¦ΠΈΠ»ΠΈΠ½Π΄ΡΡ, ΡΡΡΠΊ, ΡΠ°ΡΠΏΠΎΠ»ΠΎΠΆΠ΅Π½ΠΈΠ΅ | 8, V | |||||
Π¦ΠΈΠ»ΠΈΠ½Π΄Ρ, Γ /ΠΠΎΡΡΠ΅Π½Ρ, Ρ ΠΎΠ΄, ΠΌΠΌ | 120/130 | |||||
ΠΠ²Ρ, ΠΎΠ±ΡΡΠΌ, Π». | 11.76 | |||||
Π‘ΡΠ΅ΠΏΠ΅Π½Ρ ΡΠΆΠ°ΡΠΈΡ | 16.8 | |||||
ΠΠΎΡΠ½ΠΎΡΡΡ, Π»Ρ | 280 | 280 | 320 | 360 | 400 | 420/440 |
ΠΠΎΠ»Π΅Π½ΡΠ°ΡΡΠΉ Π²Π°Π», ΡΠ°ΡΡΠΎΡΠ° Π²ΡΠ°ΡΠ΅Π½ΠΈΡ | 1900 | |||||
ΠΠΎΠΌΠ΅Π½Ρ, ΠΠΌ | 1177 | 1177 | 1373 | 1570 | 1766 | 1864/2060 |
ΠΠΠ‘, Π²Π΅Ρ, Π½Π΅ΡΡΠΎ, ΠΊΠ³. | 870 | |||||
Π Π°Π·ΠΌΠ΅Ρ: Π΄xΡxΠ², ΠΌΠΌ. | 1260Γ930Γ1045 |
ΠΡΠΎΠΌΠ΅ ΡΠΎΠ³ΠΎ, Π½Π° Π°Π²ΡΠΎΠΌΠΎΠ±ΠΈΠ»ΠΈ ΠΌΠ°ΡΠΊΠΈ ΠΠΠΠΠ ΡΡΡΠ°Π½Π°Π²Π»ΠΈΠ²Π°Π»ΠΈΡΡ ΡΠΈΠ»ΠΎΠ²ΡΠ΅ ΡΡΡΠ°Π½ΠΎΠ²ΠΊΠΈ Π·Π°ΡΡΠ±Π΅ΠΆΠ½ΠΎΠ³ΠΎ ΠΏΡΠΎΠΈΠ·Π²ΠΎΠ΄ΡΡΠ²Π°. ΠΠ½ΠΈ Π½ΠΈ ΡΠ΅ΠΌ Π½Π΅ ΡΡΡΡΠΏΠ°Π»ΠΈ ΠΏΠΎ Ρ Π°ΡΠ°ΠΊΡΠ΅ΡΠΈΡΡΠΈΠΊΠ°ΠΌ Π½Π°ΡΠΈΠΌ Π΄Π²ΠΈΠ³Π°ΡΠ΅Π»ΡΠΌ, Π½ΠΎ ΠΈΠΌΠ΅Π»ΠΈ ΡΡΡΠ΅ΡΡΠ²Π΅Π½Π½ΡΠΉ Π½Π΅Π΄ΠΎΡΡΠ°ΡΠΎΠΊ Π² ΡΠ΅Π½Π΅ β Π±ΡΠ»ΠΈ Π΄ΠΎΡΠΎΠΆΠ΅. ΠΠ³ΡΠ΅Π³Π°ΡΡ Π·Π°ΡΠ΅ΠΊΠΎΠΌΠ΅Π½Π΄ΠΎΠ²Π°Π»ΠΈ ΡΠ΅Π±Ρ ΠΊΠ°ΠΊ Π½Π°Π΄ΡΠΆΠ½Π°Ρ, Π΄ΠΎΠ»Π³ΠΎΠ²Π΅ΡΠ½Π°Ρ, ΠΌΠΎΡΠ½Π°Ρ ΡΠ΅Ρ Π½ΠΈΠΊΠ°, Π΄ΠΎΡΡΠΎΠΉΠ½Π°Ρ Π²Π½ΠΈΠΌΠ°Π½ΠΈΡ ΠΏΠΎΠ»ΡΠ·ΠΎΠ²Π°ΡΠ΅Π»Ρ.
Π£ Π²ΡΠ΅Ρ ΠΌΠΎΡΠΎΡΠΎΠ² ΡΠ΅ΡΠΈΠΈ 740 ΠΏΡΠΈΠ½ΡΠΈΠΏ ΡΠ°Π±ΠΎΡΡ ΠΏΠΎΡ ΠΎΠΆ. Π ΠΎΡΠΎΠ±Π΅Π½Π½ΠΎΡΡΡΠΌ ΠΌΠΎΠΆΠ½ΠΎ ΠΎΡΠ½Π΅ΡΡΠΈ:
- ΠΠ»ΠΎΠΊ ΡΠΈΠ»ΠΈΠ½Π΄ΡΠΎΠ² ΡΠ²Π»ΡΠ΅ΡΡΡ ΠΎΡΠ½ΠΎΠ²Π½ΠΎΠΉ Π΄Π΅ΡΠ°Π»ΡΡ Π΄Π²ΠΈΠ³Π°ΡΠ΅Π»Ρ, Π²ΡΠΏΠΎΠ»Π½Π΅Π½ ΠΏΠΎ ΠΏΡΠΈΠ½ΡΠΈΠΏΡ Π΅Π΄ΠΈΠ½ΠΎΠ³ΠΎ Π±Π»ΠΎΠΊΠ°, Π²ΡΠ΅ Π½Π°Π²Π΅ΡΠ½ΠΎΠ΅ ΠΎΠ±ΠΎΡΡΠ΄ΠΎΠ²Π°Π½ΠΈΠ΅ ΠΊΡΠ΅ΠΏΠΈΡΡΡ ΠΊ Π½Π΅ΠΌΡ;
- ΠΠΎ ΡΠ΅Π½ΡΡΡ ΡΡΡΠ°Π½ΠΎΠ²ΠΊΠΈ ΡΠ°ΡΠΏΠΎΠ»ΠΎΠΆΠ΅Π½ ΠΊΠΎΠ»Π΅Π½ΡΠ°ΡΡΠΉ Π²Π°Π», ΠΈΠΌΠ΅Π΅Ρ Π·Π½Π°ΡΠΈΡΠ΅Π»ΡΠ½ΡΠΉ ΡΠ΄Π²ΠΈΠ³ Π² Π½ΠΈΠΆΠ½ΡΡ ΡΠ°ΡΡΡ ΠΌΠΎΡΠΎΡΠ°. ΠΠΎΠ΄ ΠΊΠΎΠ»Π΅Π½ΡΠ°ΡΡΠΌ Π²Π°Π»ΠΎΠΌ ΡΠ°ΡΠΏΠΎΠ»ΠΎΠΆΠ΅Π½ ΠΊΠ°ΡΡΠ΅Ρ, ΡΠΎΠ΄Π΅ΡΠΆΠ°ΡΠΈΠΉ ΠΌΠ°ΡΠ»ΠΎ. ΠΠ±ΡΠ΅ΠΌ ΠΌΠ°ΡΠ»Π° Π² Π΄Π²ΠΈΠ³Π°ΡΠ΅Π»Π΅ ΠΏΠΎΡΡΠ΄ΠΊΠ° 26 ΠΈΠ»ΠΈ 28 Π»ΠΈΡΡΠΎΠ².
- Π§ΡΠΎ ΠΊΠ°ΡΠ°Π΅ΡΡΡ ΠΊΠ»Π°ΠΏΠ°Π½ΠΎΠ² β ΠΈΡ ΠΊΠΎΠ»ΠΈΡΠ΅ΡΡΠ²ΠΎ 16, ΠΏΠΎ Π΄Π²Π° ΠΊΠ»Π°ΠΏΠ°Π½Π° Π½Π° ΡΠΈΠ»ΠΈΠ½Π΄Ρ.
Π Π΅ΠΌΠΎΠ½Ρ Π΄Π²ΠΈΠ³Π°ΡΠ΅Π»Ρ ΠΠΠΠΠ 740 Π½Π΅ΠΎΠ±Ρ ΠΎΠ΄ΠΈΠΌΠΎ ΠΏΡΠΎΠΈΠ·Π²ΠΎΠ΄ΠΈΡΡ Π² ΡΠΏΠ΅ΡΠΈΠ°Π»ΠΈΠ·ΠΈΡΠΎΠ²Π°Π½Π½ΡΡ ΠΌΠ°ΡΡΠ΅ΡΡΠΊΠΈΡ . ΠΠ΅Π»ΠΎ Π² ΡΠΎΠΌ, ΡΡΠΎ ΠΎΠ±ΡΠ»ΡΠΆΠΈΠ²Π°Π½ΠΈΠ΅ Π΄ΠΈΠ·Π΅Π»ΡΠ½ΡΡ ΡΠΈΠ»ΠΎΠ²ΡΡ ΡΡΡΠ°Π½ΠΎΠ²ΠΎΠΊ ΡΡΠ»ΠΎΠΆΠ½Π΅Π½ΠΎ ΠΎΡΠΎΠ±Π΅Π½Π½ΠΎΡΡΡΠΌΠΈ ΡΠ°ΠΌΠΈΡ ΠΌΠΎΡΠΎΡΠΎΠ² ΠΈ ΡΠ²Π»ΡΠ΅ΡΡΡ Π½Π΅ ΠΏΡΠΎΡΡΠΎΠΉ Π·Π°Π΄Π°ΡΠ΅ΠΉ.
ΠΠ΄ΠΈΠ½ΡΡΠ²Π΅Π½Π½ΠΎΠ΅, ΡΡΠΎ ΠΌΠΎΠΆΠ½ΠΎ ΡΠ΄Π΅Π»Π°ΡΡ ΡΠ²ΠΎΠΈΠΌΠΈ ΡΡΠΊΠ°ΠΌΠΈ Π½Π΅ ΠΏΡΠΈΡΠΈΠ½ΡΡ Π·Π½Π°ΡΠΈΡΠ΅Π»ΡΠ½ΠΎΠ³ΠΎ Π²ΡΠ΅Π΄Π° ΠΎΡΡΡΡΡΡΠ²ΠΈΠ΅ΠΌ ΡΠΏΠ΅ΡΠΈΠ°Π»ΡΠ½ΡΡ Π²ΠΈΠ΄ΠΎΠ² ΠΈΠ½ΡΡΡΡΠΌΠ΅Π½ΡΠΎΠ² β ΡΡΠΎ ΠΏΠΎΠΌΠ΅Π½ΡΡΡ ΠΌΠ°ΡΠ»ΠΎ ΠΈ ΠΎΡ Π»Π°ΠΆΠ΄Π°ΡΡΡΡ ΠΆΠΈΠ΄ΠΊΠΎΡΡΡ.
ΠΡ Π»Π°ΠΆΠ΄Π°ΡΡΠ°Ρ ΠΆΠΈΠ΄ΠΊΠΎΡΡΡ, Π·Π°ΠΌΠ΅Π½Π°
Π‘ΠΈΡΡΠ΅ΠΌΠ° ΠΎΡ Π»Π°ΠΆΠ΄Π΅Π½ΠΈΡ ΠΏΡΠ΅Π΄ΡΡΠ°Π²Π»ΡΠ΅Ρ ΡΠΎΠ±ΠΎΠΉ Π·Π°ΠΌΠΊΠ½ΡΡΡΡ ΡΠΈΡΡΠ΅ΠΌΡ ΠΆΠΈΠ΄ΠΊΠΎΡΡΠ½ΠΎΠ³ΠΎ ΡΠΈΠΏΠ° Ρ ΠΏΡΠΈΠ½ΡΠ΄ΠΈΡΠ΅Π»ΡΠ½ΠΎΠΉ ΡΠΈΡΠΊΡΠ»ΡΡΠΈΠ΅ΠΉ. Π’Π΅ΠΏΠ»ΠΎΠ²ΠΎΠΉ ΡΠ΅ΠΆΠΈΠΌ ΠΊΠΎΠ½ΡΡΠΎΠ»ΠΈΡΡΡΡ ΡΠ΅ΡΠΌΠΎΡΡΠ°Ρ ΠΈ Π³ΠΈΠ΄ΡΠΎΠΌΡΡΡΡ. Π‘Π°ΠΌΠ° ΡΠΈΡΠΊΡΠ»ΡΡΠΈΡ ΠΏΡΠΎΠΈΡΡ ΠΎΠ΄ΠΈΡ Π·Π° ΡΡΡΡ ΡΠ΅Π½ΡΡΠΎΠ±Π΅ΠΆΠ½ΠΎΠ³ΠΎ Π½Π°ΡΠΎΡΠ°, ΠΏΡΠΎΡΠ΅ΡΡ Π²ΡΠ³Π»ΡΠ΄ΠΈΡ ΡΠ»Π΅Π΄ΡΡΡΠΈΠΌ ΠΎΠ±ΡΠ°Π·ΠΎΠΌ: ΡΠ½Π°ΡΠ°Π»Π° ΠΎΠΌΡΠ²Π°Π΅ΡΡΡ Π»Π΅Π²ΡΠΉ ΡΡΠ΄ ΡΠΈΠ»ΠΈΠ½Π΄ΡΠΎΠ², ΠΏΠΎΡΠΎΠΌ ΠΏΡΠ°Π²ΡΠΉ.
ΠΡ Π»Π°ΠΆΠ΄Π°ΡΡΠ°Ρ ΠΆΠΈΠ΄ΠΊΠΎΡΡΡ ΠΏΡΠΎΡ ΠΎΠ΄ΠΈΡ ΡΠ΅ΡΠ΅Π· Π³ΠΈΠ»ΡΠ·Ρ ΡΠΈΠ»ΠΈΠ½Π΄ΡΠΎΠ² ΠΈ ΡΠ΅ΡΠ΅Π· ΠΎΡΠ²Π΅ΡΡΡΠΈΠ΅ Π² Π³ΠΎΠ»ΠΎΠ²ΠΊΡ Π±Π»ΠΎΠΊΠ° ΡΠΈΠ»ΠΈΠ½Π΄ΡΠΎΠ². ΠΠ°Π³ΡΠ΅ΡΡΠΉ Π°Π½ΡΠΈΡΡΠΈΠ· ΠΏΠΎΡΡΡΠΏΠ°Π΅Ρ Π² ΡΠ΅ΡΠΌΠΎΡΡΠ°Ρ ΠΈ Π² Π·Π°Π²ΠΈΡΠΈΠΌΠΎΡΡΠΈ ΠΎΡ ΡΠΎΠ³ΠΎ, ΠΊΡΠ΄Π° ΡΠΎΡ Π΅Π³ΠΎ ΠΎΠΏΡΠ΅Π΄Π΅Π»ΠΈΡ, Π² Π²ΠΎΠ΄ΡΠ½ΠΎΠΉ Π½Π°ΡΠΎΡ, ΠΈΠ»ΠΈ Π² ΡΠ°Π΄ΠΈΠ°ΡΠΎΡ.
Π‘ΠΎΠ³Π»Π°ΡΠ½ΠΎ ΠΏΡΠ΅Π΄ΠΏΠΈΡΠ°Π½ΠΈΡΠΌ ΡΠ΅Ρ Π½ΠΈΡΠ΅ΡΠΊΠΎΠ³ΠΎ ΡΠ΅Π³Π»Π°ΠΌΠ΅Π½ΡΠ°, ΠΎΡ Π»Π°ΠΆΠ΄Π°ΡΡΡΡ ΠΆΠΈΠ΄ΠΊΠΎΡΡΡ Π² ΡΠΈΠ»ΠΎΠ²ΠΎΠΉ ΡΡΡΠ°Π½ΠΎΠ²ΠΊΠ΅ Π½Π΅ΠΎΠ±Ρ ΠΎΠ΄ΠΈΠΌΠΎ ΠΌΠ΅Π½ΡΡΡ, Π² Π·Π°Π²ΠΈΡΠΈΠΌΠΎΡΡΠΈ ΠΎΡ ΡΠΊΡΠΏΠ»ΡΠ°ΡΠ°ΡΠΈΠΈ, ΠΊΠ°ΠΆΠ΄ΡΠ΅ ΡΡΠΈ ΠΈΠ»ΠΈ ΠΏΡΡΡ Π»Π΅Ρ. ΠΡΠ½ΠΎΠ²Π½ΡΠΌ ΠΏΠΎΠΊΠ°Π·Π°ΡΠ΅Π»Π΅ΠΌ Π½Π΅ΠΏΡΠΈΠ³ΠΎΠ΄Π½ΠΎΡΡΠΈ ΠΆΠΈΠ΄ΠΊΠΎΡΡΠΈ ΠΊ Π΄Π°Π»ΡΠ½Π΅ΠΉΡΠ΅ΠΌΡ ΠΈΡΠΏΠΎΠ»ΡΠ·ΠΎΠ²Π°Π½ΠΈΡ ΡΠ²Π»ΡΠ΅ΡΡΡ Π΅Ρ ΡΠ²Π΅Ρ. ΠΡΠ»ΠΈ ΠΎΠ½ ΠΈΠΌΠ΅Π΅Ρ Π³ΡΡΠ·Π½ΡΠΉ ΠΎΡΡΠ΅Π½ΠΎΠΊ ΠΈ ΠΎΡΠ»ΠΈΡΠ°Π΅ΡΡΡ ΠΎΡ ΠΏΠ΅ΡΠ²ΠΎΠ½Π°ΡΠ°Π»ΡΠ½ΠΎΠ³ΠΎ ΡΠ²Π΅ΡΠ°, Π΄Π°Π»ΡΠ½Π΅ΠΉΡΠ΅Π΅ ΠΈΡΠΏΠΎΠ»ΡΠ·ΠΎΠ²Π°Π½ΠΈΠ΅ Π½Π΅Π΄ΠΎΠΏΡΡΡΠΈΠΌΠΎ.
Π‘Π»Π΅Π΄ΠΈΡΡ Π·Π° ΡΠ΅ΠΌ, ΠΊΠ°ΠΊΠΎΠΉ ΡΡΠΎΠ²Π΅Π½Ρ ΠΎΡ Π»Π°ΠΆΠ΄Π°ΡΡΠ΅ΠΉ ΠΆΠΈΠ΄ΠΊΠΎΡΡΠΈ Π² Π΄Π°Π½Π½ΡΠΉ ΠΌΠΎΠΌΠ΅Π½Ρ ΠΈΠΌΠ΅Π΅Ρ ΡΠΈΠ»ΠΎΠ²Π°Ρ ΡΡΡΠ°Π½ΠΎΠ²ΠΊΠ° Π½Π°Π΄ΠΎ ΠΏΠΎΡΡΠΎΡΠ½Π½ΠΎ, Π²ΠΎ ΠΈΠ·Π±Π΅ΠΆΠ°Π½ΠΈΠ΅ ΠΏΠ΅ΡΠ΅Π³ΡΠ΅Π²Π° ΠΌΠΎΡΠΎΡΠ°. Π ΡΠ»ΡΡΠ°Π΅ Π½Π΅ΠΎΠ±Ρ ΠΎΠ΄ΠΈΠΌΠΎΡΡΠΈ ΡΠ»Π΅Π΄ΡΠ΅Ρ Π΄ΠΎΠ»ΠΈΡΡ Π½ΡΠΆΠ½ΠΎΠ΅ ΠΊΠΎΠ»ΠΈΡΠ΅ΡΡΠ²ΠΎ ΠΆΠΈΠ΄ΠΊΠΎΡΡΠΈ, ΡΠΈΠΏΠ° Π’ΠΎΡΠΎΠ»-Π40. ΠΡΠΈ ΠΊΠ°ΠΆΠ΄ΠΎΠΌ ΡΡΠ°ΡΡΠ΅ ΠΌΠΎΡΠΎΡΠ° ΠΆΠ΅Π»Π°ΡΠ΅Π»ΡΠ½ΠΎ ΠΏΡΠΎΠ²ΠΎΠ΄ΠΈΡΡ ΡΠ»Π΅Π΄ΡΡΡΠΈΠ΅ Π΄Π΅ΠΉΡΡΠ²ΠΈΡ:
- ΠΠ° ΡΠΏΠ΅ΡΠΈΠ°Π»ΡΠ½ΠΎΠΌ ΡΠ°ΡΡΠΈΡΠΈΡΠ΅Π»ΡΠ½ΠΎΠΌ Π±Π°ΡΠΊΠ΅ ΠΎΡΠΊΡΡΡΡ ΠΊΡΠ°Π½ ΠΈ ΠΏΠΎΡΠΌΠΎΡΡΠ΅ΡΡ, ΠΏΠΎΡΠ΅ΠΊΠ»Π° Π»ΠΈ ΠΆΠΈΠ΄ΠΊΠΎΡΡΡ. ΠΡΠ»ΠΈ Π΄Π°, ΡΡΠΎΠ²Π΅Π½Ρ Π² Π½ΠΎΡΠΌΠ΅. ΠΡΠΈΠ²Π΅ΡΡΠΈ ΠΊΡΠ°Π½ Π² ΠΏΠ΅ΡΠ²ΠΎΠ½Π°ΡΠ°Π»ΡΠ½ΠΎΠ΅ ΡΠΎΡΡΠΎΡΠ½ΠΈΠ΅ ΠΈ Π·Π°Π²Π΅ΡΡΠΈ ΠΌΠΎΡΠΎΡ. ΠΡΠ»ΠΈ Π½Π΅Ρ, Π΄ΠΎΠ»ΠΈΡΡ ΠΎΡ Π»Π°ΠΆΠ΄Π°ΡΡΡΡ ΠΆΠΈΠ΄ΠΊΠΎΡΡΡ Π΄ΠΎ ΠΌΠΎΠΌΠ΅Π½ΡΠ°, ΠΏΠΎΠΊΠ° ΠΎΠ½Π° Π½Π΅ ΠΏΠΎΡΠ΅ΡΡΡ ΠΈΠ· ΠΊΡΠ°Π½Π°. ΠΡΠ»ΠΈ ΠΆΠΈΠ΄ΠΊΠΎΡΡΡ Π½Π΅ ΡΠ΅ΡΡΡ, ΠΏΡΠΎΠ²Π΅ΡΠΈΡΡ ΠΊΡΠ°Π½ ΠΈ ΡΠΈΡΡΠ΅ΠΌΡ ΠΎΡ Π»Π°ΠΆΠ΄Π΅Π½ΠΈΡ Π² ΡΠ΅Π»ΠΎΠΌ Π½Π° Π½Π°Π»ΠΈΡΠΈΠ΅ ΠΏΠΎΠ²ΡΠ΅ΠΆΠ΄Π΅Π½ΠΈΠΉ.
- ΠΡΠΈ Π½Π΅Ρ Π²Π°ΡΠΊΠ΅ ΠΎΡ Π»Π°ΠΆΠ΄Π°ΡΡΠ΅ΠΉ ΠΆΠΈΠ΄ΠΊΠΎΡΡΠΈ, ΠΈΠ»ΠΈ Π΅Ρ ΠΎΡΡΡΡΡΡΠ²ΠΈΠΈ Π²ΠΎΠΎΠ±ΡΠ΅, ΠΊΠ°ΡΠ΅Π³ΠΎΡΠΈΡΠ΅ΡΠΊΠΈ Π·Π°ΠΏΡΠ΅ΡΠ°Π΅ΡΡΡ Π·Π°Π²ΠΎΠ΄ΠΈΡΡ ΡΠΈΠ»ΠΎΠ²ΡΡ ΡΡΡΠ°Π½ΠΎΠ²ΠΊΡ. ΠΡΠΏΠΎΠ»Π½ΠΈΠ² ΡΡΠΎ Π΄Π΅ΠΉΡΡΠ²ΠΈΠ΅, ΠΌΠΎΠΆΠ½ΠΎ ΠΏΡΠΈΠ²Π΅ΡΡΠΈ Π² Π½Π΅Π³ΠΎΠ΄Π½ΠΎΡΡΡ ΠΊΡΡΠ»ΡΡΠ°ΡΠΊΡ, ΡΡΠΎ ΠΏΠΎΠ²Π»Π΅ΡΡΡ Π·Π° ΡΠΎΠ±ΠΎΠΉ Π΄ΠΎΡΠΎΠ³ΠΎΡΡΠΎΡΡΠΈΠΉ ΡΠ΅ΠΌΠΎΠ½Ρ.
- Π ΡΠ»ΡΡΠ°Π΅ Π½Π΅ΠΎΠ±Ρ ΠΎΠ΄ΠΈΠΌΠΎΡΡΠΈ Π·Π°ΠΌΠ΅Π½ΠΈΡΡ ΠΆΠΈΠ΄ΠΊΠΎΡΡΡ Π² ΡΠ²ΡΠ·ΠΈ Ρ Π΅Ρ Π½Π΅ΡΠ΄ΠΎΠ²Π»Π΅ΡΠ²ΠΎΡΠΈΡΠ΅Π»ΡΠ½ΡΠΌ ΡΠΎΡΡΠΎΡΠ½ΠΈΠ΅ΠΌ: Π½Π°Π΄ΠΎ ΡΠ»ΠΈΡΡ ΠΆΠΈΠ΄ΠΊΠΎΡΡΡ Ρ Π½ΠΈΠΆΠ½Π΅Π³ΠΎ ΠΊΡΠ°Π½Π° ΡΠ°Π΄ΠΈΠ°ΡΠΎΡΠ°, ΠΊΠΎΡΠ»Π°, ΠΏΠΎΠ΄ΠΎΠ³ΡΠ΅Π²Π°ΡΠ΅Π»Ρ, ΠΈΠ· ΡΡΡΠ±Ρ ΠΏΠ΅ΡΠΊΠΈ ΠΊΠ°Π±ΠΈΠ½Ρ. ΠΠΎΡΠ»Π΅ ΡΠ΅Π³ΠΎ Π½Π΅ΠΎΠ±Ρ ΠΎΠ΄ΠΈΠΌΠΎ Π·Π°ΠΊΡΡΡΡ Π²ΡΠ΅ ΠΊΡΠ°Π½Ρ ΠΈ ΡΠ½ΠΎΠ²Π° Π½Π°ΠΏΠΎΠ»Π½ΠΈΡΡ ΡΠΈΡΡΠ΅ΠΌΡ Π΄ΠΎ Π½ΡΠΆΠ½ΠΎΠ³ΠΎ ΡΡΠΎΠ²Π½Ρ.
ΠΠ°ΡΠ»ΠΎ, Π·Π°ΠΌΠ΅Π½Π°
Π‘ΠΈΠ»ΠΎΠ²Π°Ρ ΡΡΡΠ°Π½ΠΎΠ²ΠΊΠ° ΠΎΡΠ½Π°ΡΠ΅Π½Π° ΡΠΈΡΡΠ΅ΠΌΠΎΠΉ ΡΠΌΠ°Π·ΠΊΠΈ ΠΊΠΎΠΌΠ±ΠΈΠ½ΠΈΡΠΎΠ²Π°Π½Π½ΠΎΠ³ΠΎ ΡΠΈΠΏΠ°, ΠΌΠ°ΡΠ»ΠΎ ΠΊ ΡΡΡΡΠΈΠΌΡΡ Π΄Π΅ΡΠ°Π»ΡΠΌ ΠΏΠΎΠ΄Π°ΡΡΡΡ ΡΠ°Π·Π»ΠΈΡΠ½ΡΠΌΠΈ ΡΠΏΠΎΡΠΎΠ±Π°ΠΌΠΈ, ΡΠ°ΠΊΠΈΠΌΠΈ, ΠΊΠ°ΠΊ: ΡΠ°Π·Π±ΡΡΠ·Π³ΠΈΠ²Π°Π½ΠΈΠ΅, ΡΠ°ΠΌΠΎΡΡΠΊ, ΠΏΠΎΠ΄ Π΄Π°Π²Π»Π΅Π½ΠΈΠ΅ΠΌ. Π£Π·Π΅Π» ΡΠΎΡΡΠΎΠΈΡ ΠΈΠ· ΡΡΡΡΠΎΠΉΡΡΠ²: Ρ ΡΠ°Π½Π΅Π½ΠΈΡ, ΠΏΠΎΠ΄Π²ΠΎΠ΄Π°, ΡΠΈΠ»ΡΡΡΠ°ΡΠΈΠΈ, ΠΎΡ Π»Π°ΠΆΠ΄Π΅Π½ΠΈΡ ΠΌΠ°ΡΠ»Π°.
ΠΠ²ΠΈΠΆΠ΅Π½ΠΈΠ΅ ΠΌΠ°ΡΠ»Π° Π½Π°ΡΠΈΠ½Π°Π΅ΡΡΡ ΠΈΠ· ΠΏΠΎΠ΄Π΄ΠΎΠ½Π° ΠΏΡΠΈ ΠΏΠΎΠΌΠΎΡΠΈ Π½Π°ΡΠΎΡΠ°. ΠΠ½ΠΎ ΠΏΡΠΈΡ ΠΎΠ΄ΠΈΡ ΡΠ΅ΡΠ΅Π· ΡΠΈΠ»ΡΡΡ Π² ΠΌΠ°ΡΠ»ΠΎΠΏΡΠΈΡΠΌΠ½ΠΈΠΊ, Π·Π°ΡΠ΅ΠΌ ΠΊ Π½Π°ΡΠΎΡΡ ΠΈ Π² ΡΠ΅ΠΊΡΠΈΡ Π½Π°Π³Π½Π΅ΡΠ°Π½ΠΈΡ. ΠΠ· ΡΠ΅ΠΊΡΠΈΠΈ, ΡΠ΅ΡΠ΅Π· ΠΊΠ°Π½Π°Π» ΠΏΠΎΠΏΠ°Π΄Π°Π΅Ρ Π² ΡΠΏΠ΅ΡΠΈΠ°Π»ΡΠ½ΡΠΉ ΠΌΠ°ΡΠ»ΡΠ½ΡΠΉ ΡΠΈΠ»ΡΡΡ, Π° ΠΏΠΎΡΠ»Π΅ Π² ΠΌΠ°Π³ΠΈΡΡΡΠ°Π»Ρ. ΠΠ΅ΡΠ²ΡΠΌ ΡΠΌΠ°Π·ΡΠ²Π°Π΅ΡΡΡ Π³ΠΎΠ»ΠΎΠ²ΠΊΠ° Π±Π»ΠΎΠΊΠ° ΡΠΈΠ»ΠΈΠ½Π΄ΡΠΎΠ² ΠΈ ΡΠ°ΠΌΠΈ ΡΠΈΠ»ΠΈΠ½Π΄ΡΡ, Π·Π°ΡΠ΅ΠΌ ΠΊΠΎΠ»Π΅Π½ΡΠ°ΡΡΠΉ Π²Π°Π», Π³Π°Π·ΠΎΡΠ°ΡΠΏΡΠ΅Π΄Π΅Π»ΠΈΡΠ΅Π»ΡΠ½ΡΠΉ ΠΌΠ΅Ρ Π°Π½ΠΈΠ·ΠΌ, ΠΊΠΎΠΌΠΏΡΠ΅ΡΡΠΎΡ, ΡΠΎΠΏΠ»ΠΈΠ²Π½ΡΠΉ Π½Π°ΡΠΎΡ.
ΠΠΈΡΠ½ΡΡ ΡΠΌΠ°Π·ΠΊΠ° ΡΠ½ΠΈΠΌΠ°Π΅ΡΡΡ Ρ ΠΏΠΎΠΌΠΎΡΡΡ ΠΌΠ°ΡΠ»ΠΎΡΡΡΠΌΠ½ΡΡ ΠΊΠΎΠ»Π΅Ρ Π² ΡΠΈΠ»ΠΈΠ½Π΄ΡΠ°Ρ , Π·Π°ΡΠ΅ΠΌ Π²ΡΠ²ΠΎΠ΄ΠΈΡΡΡ ΡΠ΅ΡΠ΅Π· ΠΏΠΎΡΡΠ½Π΅Π²ΡΠ΅ ΠΊΠ°Π½Π°Π»Ρ, ΡΠΌΠ°Π·ΡΠ²Π°Ρ ΠΎΠΏΠΎΡΡ ΠΏΠΎΡΡΠ½Π΅Π²ΠΎΠ³ΠΎ ΠΏΠ°Π»ΡΡΠ°. ΠΠΎΠΏΠ°Π΄Π°Ρ ΠΊ ΡΠΈΠ»ΠΎΠ²ΠΎΠΌΡ ΡΠ΅ΡΠΌΠΈΡΠ΅ΡΠΊΠΎΠΌΡ Π΄Π°ΡΡΠΈΠΊΡ ΠΈΠ· ΠΎΡΠ½ΠΎΠ²Π½ΠΎΠΉ ΠΌΠ°Π³ΠΈΡΡΡΠ°Π»ΠΈ, ΠΏΡΠΈ ΠΎΡΠΊΡΡΡΠΎΠΌ ΠΊΡΠ°Π½Π΅, Π²ΠΊΠ»ΡΡΠ°ΡΡΠ΅ΠΌ Π³ΠΈΠ΄ΡΠ°Π²Π»ΠΈΡΠ΅ΡΠΊΡΡ ΠΌΡΡΡΡ, ΠΌΠ°ΡΠ»ΠΎ ΡΠΌΠ°Π·ΡΠ²Π°Π΅Ρ ΠΈ Π΅. ΠΡΠ»ΠΈ ΠΊΡΠ°Π½ Π·Π°ΠΊΡΡΡ, ΠΌΠ°ΡΠ»ΠΎ ΠΏΠΎΡΡΡΠΏΠ°Π΅Ρ Π² ΡΠΈΠ»ΡΡΡ ΡΠ΅Π½ΡΡΠΎΠ±Π΅ΠΆΠ½ΠΎΠΉ ΠΎΡΠΈΡΡΠΊΠΈ ΠΈ Π΄Π°Π»Π΅Π΅ Π² ΠΏΠΎΠ΄Π΄ΠΎΠ½.
Π‘ΠΊΠΎΠ»ΡΠΊΠΎ ΠΌΠ°ΡΠ»Π° Π² Π΄Π²ΠΈΠ³Π°ΡΠ΅Π»Π΅ ΠΠΠΠΠ, ΠΊΠ°ΠΊΠΎΠ²Π° ΠΏΠ΅ΡΠΈΠΎΠ΄ΠΈΡΠ½ΠΎΡΡΡ Π·Π°ΠΌΠ΅Π½Ρ ΠΈ ΠΊΠ°ΠΊ ΠΏΡΠ°Π²ΠΈΠ»ΡΠ½ΠΎ ΠΏΡΠΎΠ²Π΅ΡΡΠΈ Π²Π΅ΡΡ ΠΏΡΠΎΡΠ΅ΡΡ, ΠΎΡΠ²Π΅ΡΡ Π½Π° Π²ΡΠ΅ ΡΡΠΈ Π²ΠΎΠΏΡΠΎΡΡ Π΄ΠΎΠ»ΠΆΠ΅Π½ Π·Π½Π°ΡΡ ΠΊΠ°ΠΆΠ΄ΡΠΉ, ΠΊΡΠΎ ΡΠ°Π±ΠΎΡΠ°Π΅Ρ Ρ Π°Π²ΡΠΎΠΌΠΎΠ±ΠΈΠ»ΡΠΌΠΈ ΠΌΠ°ΡΠΊΠΈ.
ΠΠ°ΡΠ»ΠΎ, ΠΊΠ°ΠΊ ΠΈ Π²ΡΠ΅ ΡΠ°Π±ΠΎΡΠΈΠ΅ ΠΆΠΈΠ΄ΠΊΠΎΡΡΠΈ, ΠΈΠΌΠ΅ΡΡ ΡΠ²ΠΎΡ ΠΏΠ΅ΡΠΈΠΎΠ΄ΠΈΡΠ½ΠΎΡΡΡ Π·Π°ΠΌΠ΅Π½Ρ. Π Π΄ΠΎΠΊΡΠΌΠ΅Π½ΡΠ°ΡΠΈΠΈ ΠΊ ΠΊΠ°ΠΆΠ΄ΠΎΠΉ ΡΠΈΠ»ΠΎΠ²ΠΎΠΉ ΡΡΡΠ°Π½ΠΎΠ²ΠΊΠ΅ ΡΠΊΠ°Π·Π°Π½ΠΎ, ΠΏΡΠΈ ΠΊΠ°ΠΊΠΎΠΌ ΠΏΡΠΎΠ±Π΅Π³Π΅ Π½Π΅ΠΎΠ±Ρ ΠΎΠ΄ΠΈΠΌΠΎ ΠΏΡΠΎΠ²Π΅ΡΡΠΈ Π·Π°ΠΌΠ΅Π½Ρ.
ΠΠ»Ρ ΠΏΡΠΎΠ²Π΅ΡΠΊΠΈ ΡΡΠΎΠ²Π½Ρ ΠΌΠ°ΡΠ»Π° Π² ΠΌΠΎΡΠΎΡΠ΅ ΠΈΡΠΏΠΎΠ»ΡΠ·ΡΠ΅ΡΡΡ ΡΠΏΠ΅ΡΠΈΠ°Π»ΡΠ½ΡΠΉ ΡΡΠΏ Ρ ΠΎΡΠΌΠ΅ΡΠΊΠΎΠΉ. ΠΡΠΈ Π½ΠΎΡΠΌΠ°Π»ΡΠ½ΠΎΠΌ ΡΡΠΎΠ²Π½Π΅, ΠΌΠ°ΡΠ»ΠΎ Π±ΡΠ΄Π΅Ρ Π½Π°Ρ ΠΎΠ΄ΠΈΡΡΡΡ Π½Π° Π·Π½Π°ΡΠ΅Π½ΠΈΠΈ Β«ΠΒ». ΠΡΠΈ Π½Π΅Π΄ΠΎΡΡΠ°ΡΠΎΡΠ½ΠΎΠΌ ΠΊΠΎΠ»ΠΈΡΠ΅ΡΡΠ²Π΅, ΡΡΠ΅Π±ΡΠ΅ΡΡΡ Π΄ΠΎΠ»ΠΈΡΡ ΡΠΌΠ°Π·ΡΠ²Π°ΡΡΡΡ ΠΆΠΈΠ΄ΠΊΠΎΡΡΡ Π΄ΠΎ Π½Π΅ΠΎΠ±Ρ ΠΎΠ΄ΠΈΠΌΠΎΠ³ΠΎ Π·Π½Π°ΡΠ΅Π½ΠΈΡ, ΠΈΠ½Π°ΡΠ΅, ΡΠ°Π±ΠΎΡΠ°Ρ, Π΄Π²ΠΈΠ³Π°ΡΠ΅Π»Ρ ΠΈ Π΅Π³ΠΎ Π΄Π΅ΡΠ°Π»ΠΈ Π±ΡΠ΄ΡΡ ΠΏΡΠ΅ΡΠ΅ΡΠΏΠ΅Π²Π°ΡΡ Π·Π½Π°ΡΠΈΡΠ΅Π»ΡΠ½ΡΠΉ ΠΈΠ·Π½ΠΎΡ ΠΈ ΡΠ°Π½Π½Π΅Π³ΠΎ Π²ΡΡ ΠΎΠ΄Π° ΠΈΠ· ΡΡΡΠΎΡ Π½Π΅ ΠΈΠ·Π±Π΅ΠΆΠ°ΡΡ. ΠΠ΅ΡΠ΅ΠΈΠ·Π±ΡΡΠΊΠ° ΠΌΠ°ΡΠ»Π° Π»ΡΡΡΠ΅ Π½Π΅ Π΄ΠΎΠΏΡΡΠΊΠ°ΡΡ, ΡΠ°ΠΊ ΠΊΠ°ΠΊ ΠΎΠ½ ΠΌΠΎΠΆΠ΅Ρ ΠΏΡΠΈΠ²Π΅ΡΡΠΈ ΠΊ ΠΏΠΎΡΡΠ΅ ΠΌΠ΅Ρ Π°Π½ΠΈΠ·ΠΌΠΎΠ² Ρ ΡΠ΅Π·ΠΈΠ½ΠΎΠ²ΡΠΌΠΈ ΡΠΏΠ»ΠΎΡΠ½Π΅Π½ΠΈΡΠΌΠΈ.
ΠΡΠΈ Π½Π΅ΠΎΠ±Ρ ΠΎΠ΄ΠΈΠΌΠΎΡΡΠΈ Π·Π°ΠΌΠ΅Π½ΠΈΡΡ ΠΌΠ°ΡΠ»ΠΎ:
- ΠΠ°Π²Π΅Π΄ΠΈΡΠ΅ Π΄Π²ΠΈΠ³Π°ΡΠ΅Π»Ρ ΠΈ ΠΏΡΠΎΠ³ΡΠ΅ΠΉΡΠ΅ Π΄ΠΎ 80Β°Π‘;
- ΠΡΠΊΠ»ΡΡΠΈΡΠ΅ ΠΌΠΎΡΠΎΡ ΠΈ Π²ΡΠΊΡΡΡΠΈΡΠ΅ ΡΠ»ΠΈΠ²Π½ΡΡ ΠΏΡΠΎΠ±ΠΊΡ ΠΊΠ°ΡΡΠ΅ΡΠ°;
- ΠΠΎΠ»Π½ΠΎΡΡΡΡ ΡΠ»Π΅ΠΉΡΠ΅ ΠΌΠ°ΡΠ»ΠΎ;
- ΠΠ±ΡΠ·Π°ΡΠ΅Π»ΡΠ½ΠΎ ΠΏΠΎΠΌΠ΅Π½ΡΠΉΡΠ΅ ΡΠΈΠ»ΡΡΡΡ;
- Π¦Π΅Π½ΡΡΠΎΠ±Π΅ΠΆΠ½ΡΠΉ ΡΠΈΠ»ΡΡΡ ΠΎΡΠΈΡΡΠΊΠΈ ΠΌΠ°ΡΠ»Π° Π½Π΅ΠΎΠ±Ρ ΠΎΠ΄ΠΈΠΌΠΎ ΡΠ°Π·ΠΎΠ±ΡΠ°ΡΡ ΠΈ ΠΏΡΠΎΠΌΡΡΡ ΡΠΎΡΠΎΡ;
- ΠΠ°Π»Π΅ΠΉΡΠ΅ ΠΌΠ°ΡΠ»ΠΎ Π΄ΠΎ ΠΎΡΠΌΠ΅ΡΠΊΠΈ Β«ΠΒ» Π½Π° ΡΡΠΏΠ΅;
- ΠΠ°Π²Π΅Π΄ΠΈΡΠ΅ ΡΠΈΠ»ΠΎΠ²ΡΡ ΡΡΡΠ°Π½ΠΎΠ²ΠΊΡ ΠΈ Π΄Π°ΠΉΡΠ΅ ΠΏΡΠΎΡΠ°Π±ΠΎΡΠ°ΡΡ 10 ΠΌΠΈΠ½ΡΡ Π½Π° Ρ ΠΎΠ»ΠΎΡΡΠΎΠΌ Ρ ΠΎΠ΄Ρ;
- ΠΠ°Π³Π»ΡΡΠΈΡΠ΅ Π΄Π²ΠΈΠ³Π°ΡΠ΅Π»Ρ, Π΄Π°ΠΉΡΠ΅ ΠΎΡΠ΅ΡΡΡ ΠΌΠ°ΡΠ»Ρ (ΠΌΠΈΠ½ΡΡ 10) ΠΈ Π΄ΠΎΠ»Π΅ΠΉΡΠ΅ Π½Π΅ΠΎΠ±Ρ ΠΎΠ΄ΠΈΠΌΠΎΠ΅ ΠΊΠΎΠ»ΠΈΡΠ΅ΡΡΠ²ΠΎ Π΄ΠΎ ΠΎΡΠΌΠ΅ΡΠΊΠΈ Β«ΠΒ».
ΠΠ΅Π΄ΠΎΡΡΠ°ΡΠΊΠΈ ΠΈ Ρ Π°ΡΠ°ΠΊΡΠ΅ΡΠ½ΡΠ΅ ΠΏΠΎΠ»ΠΎΠΌΠΊΠΈ ΡΠΈΠ»ΠΎΠ²ΡΡ ΡΡΡΠ°Π½ΠΎΠ²ΠΎΠΊ
Π Π΅ΠΌΠΎΠ½Ρ Π΄Π²ΠΈΠ³Π°ΡΠ΅Π»Π΅ΠΉ ΠΠΠΠΠ, Π½Π΅ ΠΏΡΠΈΠ½ΠΎΡΠΈΡ Π²Π»Π°Π΄Π΅Π»ΡΡΡ ΠΎΡΠΎΠ±Π΅Π½Π½ΡΡ Ρ Π»ΠΎΠΏΠΎΡ, Π΅ΡΠ»ΠΈ ΡΡΡΠΎΠ³ΠΎ ΡΠΎΠ±Π»ΡΠ΄Π°ΡΡ, ΡΠ΅Π³Π»Π°ΠΌΠ΅Π½Ρ ΡΠ΅Ρ Π½ΠΈΡΠ΅ΡΠΊΠΎΠ³ΠΎ ΠΎΠ±ΡΠ»ΡΠΆΠΈΠ²Π°Π½ΠΈΡ ΠΈ Π²ΡΠΏΠΎΠ»Π½ΡΡΡ Π΅Π³ΠΎ Π² ΡΠΎΠΎΡΠ²Π΅ΡΡΡΠ²ΠΈΠΈ Ρ ΠΏΠ°ΡΠΏΠΎΡΡΠ½ΡΠΌΠΈ ΡΠ΅ΠΊΠΎΠΌΠ΅Π½Π΄Π°ΡΠΈΡΠΌΠΈ. Π’Π°ΠΊ, Π½Π΅ΠΎΠ±Ρ ΠΎΠ΄ΠΈΠΌΠΎ ΡΠ΅Π³ΡΠ»ΡΡΠ½ΠΎ, Ρ ΡΡΡΠ°Π½ΠΎΠ²Π»Π΅Π½Π½ΠΎΠΉ ΠΏΠ΅ΡΠΈΠΎΠ΄ΠΈΡΠ½ΠΎΡΡΡΡ ΠΏΡΠΎΠ²ΠΎΠ΄ΠΈΡΡ ΡΠ΅ΡΠ²ΠΈΡΠ½ΠΎΠ΅ ΠΎΠ±ΡΠ»ΡΠΆΠΈΠ²Π°Π½ΠΈΠ΅ ΠΎΡΠ½ΠΎΠ²Π½ΡΡ ΠΊΠΎΠΌΠΏΠΎΠ½Π΅Π½ΡΠΎΠ², ΠΌΠ΅Π½ΡΡΡ ΡΠ°Π±ΠΎΡΠΈΠ΅ ΠΆΠΈΠ΄ΠΊΠΎΡΡΠΈ, ΡΠ΅Π³ΡΠ»ΠΈΡΠΎΠ²Π°ΡΡ ΡΠ΅ΠΏΠ»ΠΎΠ²ΡΠ΅ Π·Π°Π·ΠΎΡΡ, ΠΌΠ΅Π½ΡΡΡ ΡΠΈΠ»ΡΡΡΡ.
ΠΡΠ»ΠΈ ΠΆΠ΅ ΡΠ΅ΡΡΡΠ·Π½ΡΡ ΠΏΠΎΠ»ΠΎΠΌΠΎΠΊ ΠΈΠ·Π±Π΅ΠΆΠ°ΡΡ Π½Π΅ ΡΠ΄Π°Π»ΠΎΡΡ, ΠΊΠ°ΠΊ ΡΠ΅ΠΊΠΎΠΌΠ΅Π½Π΄Π°ΡΠΈΡ Π΄Π²ΠΈΠ³Π°ΡΠ΅Π»Ρ ΠΠΠΠΠ ΡΠ΅ΠΌΠΎΠ½Ρ Π»ΡΡΡΠ΅ ΠΏΡΠΎΠΈΠ·Π²ΠΎΠ΄ΠΈΡΡ ΡΠΈΠ»Π°ΠΌΠΈ ΠΊΠ²Π°Π»ΠΈΡΠΈΡΠΈΡΠΎΠ²Π°Π½Π½ΡΡ ΡΠΏΠ΅ΡΠΈΠ°Π»ΠΈΡΡΠΎΠ², ΠΏΠΎΡΠΊΠΎΠ»ΡΠΊΡ Π΄Π»Ρ Π²ΡΠΏΠΎΠ»Π½Π΅Π½ΠΈΡ Π²ΡΠ΅Ρ Π½Π΅ΠΎΠ±Ρ ΠΎΠ΄ΠΈΠΌΡΡ ΡΠ°Π±ΠΎΡ ΡΡΠ΅Π±ΡΠ΅ΡΡΡ Π½Π°Π»ΠΈΡΠΈΠ΅ ΡΠΏΠ΅ΡΠΈΠ°Π»ΡΠ½ΠΎΠ³ΠΎ ΠΎΠ±ΠΎΡΡΠ΄ΠΎΠ²Π°Π½ΠΈΡ ΠΈ ΡΡΠ΅Π½Π΄ΠΎΠ².
Π ΠΎΡΠ½ΠΎΠ²Π½ΡΠΌ Π½Π΅ΠΈΡΠΏΡΠ°Π²Π½ΠΎΡΡΡΠΌ ΡΠΈΠ»ΠΎΠ²ΡΡ ΡΡΡΠ°Π½ΠΎΠ²ΠΎΠΊ ΠΎΡΠ½ΠΎΡΡΡ:
- Π‘ΠΈΠ»ΠΎΠ²Π°Ρ ΡΡΡΠ°Π½ΠΎΠ²ΠΊΠ° Π½Π΅ Π·Π°ΠΏΡΡΠΊΠ°Π΅ΡΡΡ. ΠΠΎΠ·ΠΌΠΎΠΆΠ½ΠΎ, Π² ΡΠΈΡΡΠ΅ΠΌΠ΅ ΠΏΠΈΡΠ°Π½ΠΈΡ ΡΠΎΠΏΠ»ΠΈΠ²ΠΎΠΌ ΠΏΡΠΈΡΡΡΡΡΠ²ΡΠ΅Ρ Π²ΠΎΠ·Π΄ΡΡ . ΠΠ΅ΠΎΠ±Ρ ΠΎΠ΄ΠΈΠΌΠΎ Π²ΡΡΠ²ΠΈΡΡ ΠΏΡΠΈΡΠΈΠ½Ρ ΠΏΠΎΡΠ²Π»Π΅Π½ΠΈΡ Π²ΠΎΠ·Π΄ΡΡ Π°, ΠΏΡΠΈΠ²Π΅ΡΡΠΈ ΡΠΈΡΡΠ΅ΠΌΡ Π² Π³Π΅ΡΠΌΠ΅ΡΠΈΡΠ½ΠΎΠ΅ ΡΠΎΡΡΠΎΡΠ½ΠΈΠ΅ ΠΈ ΠΏΡΠΎΠΊΠ°ΡΠ°ΡΡ ΡΠΎΠΏΠ»ΠΈΠ²ΠΎ.
- ΠΠΎΡΠΎΡ Π½Π΅ Π·Π°Π²ΠΎΠ΄ΠΈΡΡΡ. ΠΠΎΠ·ΠΌΠΎΠΆΠ½ΠΎ, Π½Π°ΡΡΡΠ΅Π½ ΡΠ³ΠΎΠ» ΠΎΠΏΠ΅ΡΠ΅ΠΆΠ΅Π½ΠΈΡ Π²ΠΏΡΡΡΠΊΠ° ΡΠΎΠΏΠ»ΠΈΠ²Π°. ΠΠ΅ΠΎΠ±Ρ ΠΎΠ΄ΠΈΠΌΠΎ ΠΎΡΡΠ΅Π³ΡΠ»ΠΈΡΠΎΠ²Π°ΡΡ ΡΠ³ΠΎΠ» ΠΎΠΏΠ΅ΡΠ΅ΠΆΠ΅Π½ΠΈΡ.
- ΠΠ²ΠΈΠ³Π°ΡΠ΅Π»Ρ Π½Π΅ Π·Π°Π²ΠΎΠ΄ΠΈΡΡΡ ΠΏΡΠΈ ΠΌΠΈΠ½ΡΡΠΎΠ²ΠΎΠΉ ΡΠ΅ΠΌΠΏΠ΅ΡΠ°ΡΡΡΠ΅. ΠΠΎΠΏΠ°Π΄Π°Π½ΠΈΠ΅ Π²ΠΎΠ΄Ρ Π² ΡΠΎΠΏΠ»ΠΈΠ²Π½ΡΠ΅ ΡΡΡΠ±ΠΊΠΈ ΠΈΠ»ΠΈ Π½Π° ΡΠ΅ΡΠΊΡ Π·Π°Π±ΠΎΡΠ° ΡΠΎΠΏΠ»ΠΈΠ²Π° ΠΈ ΠΏΠΎΡΠ»Π΅Π΄ΡΡΡΠ΅Π΅ Π΅Ρ Π·Π°ΠΌΠ΅ΡΠ·Π°Π½ΠΈΠ΅. ΠΠ°Π΄ΠΎ ΠΏΡΠΎΠ³ΡΠ΅ΡΡ ΡΠΎΠΏΠ»ΠΈΠ²Π½ΡΠ΅ ΡΠΈΠ»ΡΡΡΡ, Π±Π°ΠΊΠΈ ΠΈ ΡΡΡΠ±ΠΊΠΈ Π³ΠΎΡΡΡΠ΅ΠΉ Π²ΠΎΠ΄ΠΎΠΉ Ρ ΡΠ΅Π»ΡΡ ΡΠ°ΡΡΠΎΠΏΠΈΡΡ Π·Π°ΠΌΠ΅ΡΠ·ΡΡΡ ΠΆΠΈΠ΄ΠΊΠΎΡΡΡ.
- ΠΠ΅ΡΠΎΠ²Π½Π°Ρ ΡΠ°Π±ΠΎΡΠ° ΡΠΈΠ»ΠΎΠ²ΠΎΠ³ΠΎ Π°Π³ΡΠ΅Π³Π°ΡΠ°, ΠΌΠΎΡΠΎΡ ΡΠΈΠ»ΡΠ½ΠΎ Π²ΠΈΠ±ΡΠΈΡΡΠ΅Ρ, Π½Π΅ Π΄Π΅ΡΠΆΠΈΡ Ρ ΠΎΠ»ΠΎΡΡΡΠ΅ ΠΎΠ±ΠΎΡΠΎΡΡ, ΠΏΡΠΎΠ²Π°Π»Ρ ΠΌΠΎΡΠ½ΠΎΡΡΠΈ ΠΏΡΠΈ ΡΠ²Π΅Π»ΠΈΡΠ΅Π½ΠΈΠΈ ΠΎΠ±ΠΎΡΠΎΡΠΎΠ². ΠΠΎΠ·ΠΌΠΎΠΆΠ½ΠΎΠΉ ΠΏΡΠΈΡΠΈΠ½ΠΎΠΉ ΡΠ²Π»ΡΠ΅ΡΡΡ Π·Π°ΡΠΎΡΠ΅Π½ΠΈΠ΅ ΡΠΎΡΡΡΠ½ΠΎΠΊ. ΠΠ»Ρ ΡΡΡΡΠ°Π½Π΅Π½ΠΈΡ Π½Π΅ΠΈΡΠΏΡΠ°Π²Π½ΠΎΡΡΠΈ Π½Π΅ΠΎΠ±Ρ ΠΎΠ΄ΠΈΠΌΠΎ ΠΏΡΠΎΠΌΡΡΡ ΡΠΎΡΡΡΠ½ΠΊΠΈ Π½Π° ΡΠΏΠ΅ΡΠΈΠ°Π»ΡΠ½ΠΎΠΌ ΡΡΠ΅Π½Π΄Π΅.
avtodvigateli.com
Π£ΡΡΡΠΎΠΉΡΡΠ²ΠΎ ΠΊΡΠΈΠ²ΠΎΡΠΈΠΏΠ½ΠΎ-ΡΠ°ΡΡΠ½Π½ΠΎΠ³ΠΎ ΠΌΠ΅Ρ Π°Π½ΠΈΠ·ΠΌΠ° ΠΠ°ΠΌΠΠ-5320, ΠΠ°ΠΌΠΠ-4310 ΠΈ Π£ΡΠ°Π»-4320
Π‘ΡΡΠΎΠΈΡΠ΅Π»ΡΠ½ΡΠ΅ ΠΌΠ°ΡΠΈΠ½Ρ ΠΈ ΠΎΠ±ΠΎΡΡΠ΄ΠΎΠ²Π°Π½ΠΈΠ΅, ΡΠΏΡΠ°Π²ΠΎΡΠ½ΠΈΠΊ
ΠΠ°ΡΠ΅Π³ΠΎΡΠΈΡ:
ΠΠ²ΡΠΎΠΌΠΎΠ±ΠΈΠ»ΠΈ ΠΠ°ΠΌΠ°Π· Π£ΡΠ°Π»
ΠΡΠ±Π»ΠΈΠΊΠ°ΡΠΈΡ:
Π£ΡΡΡΠΎΠΉΡΡΠ²ΠΎ ΠΊΡΠΈΠ²ΠΎΡΠΈΠΏΠ½ΠΎ-ΡΠ°ΡΡΠ½Π½ΠΎΠ³ΠΎ ΠΌΠ΅Ρ Π°Π½ΠΈΠ·ΠΌΠ° ΠΠ°ΠΌΠΠ-5320, ΠΠ°ΠΌΠΠ-4310 ΠΈ Π£ΡΠ°Π»-4320
Π§ΠΈΡΠ°ΡΡ Π΄Π°Π»Π΅Π΅:
Π£ΡΡΡΠΎΠΉΡΡΠ²ΠΎ ΠΊΡΠΈΠ²ΠΎΡΠΈΠΏΠ½ΠΎ-ΡΠ°ΡΡΠ½Π½ΠΎΠ³ΠΎ ΠΌΠ΅Ρ Π°Π½ΠΈΠ·ΠΌΠ° ΠΠ°ΠΌΠΠ-5320, ΠΠ°ΠΌΠΠ-4310 ΠΈ Π£ΡΠ°Π»-4320
ΠΡΠΈΠ²ΠΎΡΠΈΠΏΠ½ΠΎ-ΡΠ°ΡΡΠ½Π½ΡΠΉ ΠΌΠ΅Ρ Π°Π½ΠΈΠ·ΠΌ ΡΠ»ΡΠΆΠΈΡ Π΄Π»Ρ Π²ΠΎΡΠΏΡΠΈΡΡΠΈΡ Π΄Π°Π²Π»Π΅Π½ΠΈΡ Π³Π°Π·ΠΎΠ² Π² ΡΠ°ΠΊΡΠ΅ ΡΠ°Π±ΠΎΡΠ΅Π³ΠΎ Ρ ΠΎΠ΄Π° ΠΈ ΠΏΡΠ΅ΠΎΠ±ΡΠ°Π·ΠΎΠ²Π°Π½ΠΈΡ Π²ΠΎΠ·Π²ΡΠ°ΡΠ½ΠΎ-ΠΏΠΎΡΡΡΠΏΠ°ΡΠ΅Π»ΡΠ½ΠΎΠ³ΠΎ Π΄Π²ΠΈΠΆΠ΅Π½ΠΈΡ ΠΏΠΎΡΡΠ½Π΅ΠΉ Π²ΠΎ Π²ΡΠ°ΡΠ°ΡΠ΅Π»ΡΠ½ΠΎΠ΅ Π΄Π²ΠΈΠΆΠ΅Π½ΠΈΠ΅ ΠΊΠΎΠ»Π΅Π½ΡΠ°ΡΠΎΠ³ΠΎ Π²Π°Π»Π°. ΠΠ½ ΡΠΎΡΡΠΎΠΈΡ ΠΈΠ· Π±Π»ΠΎΠΊΠ° ΡΠΈΠ»ΠΈΠ½Π΄ΡΠΎΠ², Π³ΠΈΠ»ΡΠ· ΠΈ Π³ΠΎΠ»ΠΎΠ²ΠΎΠΊ ΡΠΈΠ»ΠΈΠ½Π΄ΡΠΎΠ², ΠΏΠΎΡΡΠ½Π΅ΠΉ Ρ ΠΊΠΎΠ»ΡΡΠ°ΠΌΠΈ ΠΈ ΠΏΠΎΡΡΠ½Π΅Π²ΡΠΌΠΈ ΠΏΠ°Π»ΡΡΠ°ΠΌΠΈ, ΡΠ°ΡΡΠ½ΠΎΠ², ΠΊΠΎΠ»Π΅Π½ΡΠ°ΡΠΎΠ³ΠΎ Π²Π°Π»Π°, ΠΊΠΎΡΠ΅Π½Π½ΡΡ ΠΈ ΡΠ°ΡΡΠ½Π½ΡΡ ΠΏΠΎΠ΄ΡΠΈΠΏΠ½ΠΈΠΊΠΎΠ² ΠΈ ΠΌΠ°Ρ ΠΎΠ²ΠΈΠΊΠ°.
ΠΠ»ΠΎΠΊ ΡΠΈΠ»ΠΈΠ½Π΄ΡΠΎΠ² ΠΏΡΠ΅Π΄ΡΡΠ°Π²Π»ΡΠ΅Ρ ΡΠΎΠ±ΠΎΠΉ ΠΆΠ΅ΡΡΠΊΡΡ ΠΌΠΎΠ½ΠΎΠ±Π»ΠΎΡΠ½ΡΡ V-ΠΎΠ±ΡΠ°Π·Π½ΡΡ ΠΊΠΎΠ½ΡΡΡΡΠΊΡΠΈΡ, ΠΎΡΠ»ΠΈΡΡΡ ΠΈΠ· Π»Π΅Π³ΠΈΡΠΎΠ²Π°Π½Π½ΠΎΠ³ΠΎ ΡΠ΅ΡΠΎΠ³ΠΎ ΡΡΠ³ΡΠ½Π° ΠΊΠ°ΠΊ ΠΎΠ΄Π½ΠΎ ΡΠ΅Π»ΠΎΠ΅ Ρ Π²Π΅ΡΡ Π½Π΅ΠΉ ΡΠ°ΡΡΡΡ ΠΊΠ°ΡΡΠ΅ΡΠ°. ΠΡΡΠΎΠΊΠ°Ρ ΠΆΠ΅ΡΡΠΊΠΎΡΡΡ Π±Π»ΠΎΠΊΠ° ΠΎΠ±Π΅ΡΠΏΠ΅ΡΠΈΠ²Π°Π΅ΡΡΡ ΡΠ°Π·Π΄Π΅Π»Π΅Π½ΠΈΠ΅ΠΌ ΠΊΠ°ΡΡΠ΅ΡΠ½ΠΎΠ³ΠΎ ΠΏΡΠΎΡΡΡΠ°Π½ΡΡΠ²Π° Π½Π° ΠΎΡΠ΄Π΅Π»ΡΠ½ΡΠ΅ ΠΎΡΡΠ΅ΠΊΠΈ ΠΏΠΎΠΏΠ΅ΡΠ΅ΡΠ½ΡΠΌΠΈ ΠΏΠ΅ΡΠ΅Π³ΠΎΡΠΎΠ΄ΠΊΠ°ΠΌΠΈ Ρ ΡΠΈΠ»ΠΎΠ²ΡΠΌ ΠΎΡΠ΅Π±ΡΠ΅Π½ΠΈΠ΅ΠΌ ΠΈ Π½ΠΈΠ·ΠΊΠΈΠΌ ΡΠ°ΡΠΏΠΎΠ»ΠΎΠΆΠ΅Π½ΠΈΠ΅ΠΌ ΠΏΠ»ΠΎΡΠΊΠΎΡΡΠΈ ΡΠ°Π·ΡΠ΅ΠΌΠ° Π²Π΅ΡΡ Π½Π΅ΠΉ ΠΏΠΎΠ»ΠΎΠ²ΠΈΠ½Ρ ΠΊΠ°ΡΡΠ΅ΡΠ° Ρ ΠΌΠ°ΡΠ»ΡΠ½ΡΠΌ ΠΏΠΎΠ΄Π΄ΠΎΠ½ΠΎΠΌ (Π·Π½Π°ΡΠΈΡΠ΅Π»ΡΠ½ΠΎ Π½ΠΈΠΆΠ΅ ΠΎΡΠΈ ΠΊΠΎΠ»Π΅Π½ΡΠ°ΡΠΎΠ³ΠΎ Π²Π°Π»Π°).
Π Π²Π΅ΡΡ Π½Π΅ΠΉ ΡΠ°ΡΡΠΈ Π±Π»ΠΎΠΊΠ° ΠΏΠΎΠ΄ ΡΠ³Π»ΠΎΠΌ 90Β° ΡΠ°ΡΠΏΠΎΠ»ΠΎΠΆΠ΅Π½Ρ Π΄Π²Π° ΡΡΠ΄Π° ΡΠΈΠ»ΠΈΠ½Π΄ΡΠΎΠ²ΡΡ Π³Π½Π΅Π·Π΄ ΠΏΠΎΠ΄ Π²ΡΡΠ°Π²Π½ΡΠ΅ Β«ΠΌΠΎΠΊΡΡΠ΅Β» Π³ΠΈΠ»ΡΠ·Ρ Ρ ΠΏΡΠΈΠ²Π°Π»ΠΎΡ-Π½ΡΠΌΠΈ ΠΏΠΎΠ²Π΅ΡΡ Π½ΠΎΡΡΡΠΌΠΈ ΠΏΠΎΠ΄ Π³ΠΎΠ»ΠΎΠ²ΠΊΠΈ ΡΠΈΠ»ΠΈΠ½Π΄ΡΠΎΠ². ΠΠ΅Π²ΡΠΉ ΡΡΠ΄ ΡΠΈΠ»ΠΈΠ½Π΄ΡΠΎΠ² ΡΠΌΠ΅ΡΠ΅Π½ ΠΎΡΠ½ΠΎΡΠΈΡΠ΅Π»ΡΠ½ΠΎ ΠΏΡΠ°Π²ΠΎΠ³ΠΎ Π²ΠΏΠ΅ΡΠ΅Π΄ Π½Π° 29,5 ΠΌΠΌ, ΡΡΠΎ Π²ΡΠ·Π²Π°Π½ΠΎ ΡΡΡΠ°Π½ΠΎΠ²ΠΊΠΎΠΉ Π΄Π²ΡΡ Π½ΠΈΠΆΠ½ΠΈΡ Π³ΠΎΠ»ΠΎΠ²ΠΎΠΊ ΡΠ°ΡΡΠ½ΠΎΠ² Π½Π° ΠΎΠ±ΡΡΡ ΡΠ°ΡΡΠ½Π½ΡΡ ΡΠ΅ΠΉΠΊΡ ΠΊΠΎΠ»Π΅Π½ΡΠ°ΡΠΎΠ³ΠΎ Π²Π°Π»Π°.
ΠΠΎ Π²ΡΠ΅ΠΉ Π²ΡΡΠ΄ΡΠ΅ ΡΠΈΠ»ΠΈΠ½Π΄ΡΠΎΠ² ΡΠ΄Π΅Π»Π°Π½Ρ ΠΏΡΠΎΡΠΎΠΊΠΈ Π΄Π»Ρ ΠΎΡ Π»Π°ΠΆΠ΄Π°ΡΡΠ΅ΠΉ ΠΆΠΈΠ΄ΠΊΠΎΡΡΠΈ, Π±Π»Π°Π³ΠΎΠ΄Π°ΡΡ ΡΠ΅ΠΌΡ ΠΎΠ±Π΅ΡΠΏΠ΅ΡΠΈΠ²Π°Π΅ΡΡΡ ΠΈΠ½ΡΠ΅Π½ΡΠΈΠ²Π½ΡΠΉ ΠΎΡΠ²ΠΎΠ΄ ΡΠ΅ΠΏΠ»Π° ΠΎΡ Π³ΠΈΠ»ΡΠ· ΡΠΈΠ»ΠΈΠ½Π΄ΡΠΎΠ², ΡΠ»ΡΡΡΠ°Ρ ΠΎΡ Π»Π°ΠΆΠ΄Π΅Π½ΠΈΠ΅ ΠΏΠΎΡΡΠ½Π΅ΠΉ ΠΈ ΠΏΠΎΡΡΠ½Π΅Π²ΡΡ ΠΊΠΎΠ»Π΅Ρ. ΠΠΎΠ΄ΡΠ½ΡΠ΅ ΡΡΠ±Π°ΡΠΊΠΈ Π±Π»ΠΎΠΊΠ° ΡΠΈΠ»ΠΈΠ½Π΄ΡΠΎΠ² ΠΈ Π³ΠΎΠ»ΠΎΠ²ΠΎΠΊ Π±Π»ΠΎΠΊΠ° ΡΠΎΠΎΠ±ΡΠ°ΡΡΡΡ ΡΠ΅ΡΠ΅Π· ΡΠΏΠ΅ΡΠΈΠ°Π»ΡΠ½ΡΠ΅ ΠΎΡΠ²Π΅ΡΡΡΠΈΡ Π² ΠΏΡΠΈΠ»Π΅Π³Π°ΡΡΠΈΡ ΠΏΠ»ΠΎΡΠΊΠΎΡΡΡΡ , ΡΠΏΠ»ΠΎΡΠ½ΡΠ΅ΠΌΡΡ ΡΠ΅Π·ΠΈΠ½ΠΎΠ²ΡΠΌΠΈ ΠΊΠΎΠ»ΡΡΠ°ΠΌΠΈ.
Π ΠΊΠ°ΡΡΠ΅ΡΠ½ΠΎΠΉ ΡΠ°ΡΡΠΈ Π±Π»ΠΎΠΊΠ° ΠΈΠΌΠ΅Π΅ΡΡΡ ΡΠΈΡΡΠ΅ΠΌΠ° ΠΊΠ°Π½Π°Π»ΠΎΠ² Π΄Π»Ρ ΠΏΠΎΠ΄Π²ΠΎΠ΄Π° ΠΌΠ°ΡΠ»Π° ΠΈΠ· ΡΠ΅Π½ΡΡΠ°Π»ΡΠ½ΠΎΠΉ ΠΌΠ°Π³ΠΈΡΡΡΠ°Π»ΠΈ ΠΊ ΠΏΠΎΠ΄ΡΠΈΠΏΠ½ΠΈΠΊΠ°ΠΌ ΠΊΠΎΠ»Π΅Π½ΡΠ°ΡΠΎΠ³ΠΎ ΠΈ ΡΠ°ΡΠΏΡΠ΅Π΄Π΅Π»ΠΈΡΠ΅Π»ΡΠ½ΠΎΠ³ΠΎ Π²Π°Π»ΠΎΠ², Π΄Π΅ΡΠ°Π»ΡΠΌ ΠΏΡΠΈΠ²ΠΎΠ΄Π° ΠΌΠ΅Ρ Π°Π½ΠΈΠ·ΠΌΠ° Π³Π°Π·ΠΎΡΠ°ΡΠΏΡΠ΅Π΄Π΅Π»Π΅Π½ΠΈΡ, ΡΠΈΠ»ΡΡΡΡ ΠΎΡΠΈΡΡΠΊΠΈ ΠΌΠ°ΡΠ»Π°, ΡΠ΅Π½ΡΡΠΎΠ±Π΅ΠΆΠ½ΠΎΠΌΡ ΡΠΈΠ»ΡΡΡΡ ΠΈ ΠΊΠΎΠΌΠΏΡΠ΅ΡΡΠΎΡΡ.
ΠΠ½Π΅Π·Π΄Π° Π² Π±Π»ΠΎΠΊΠ΅ ΠΏΠΎΠ΄ ΠΊΠΎΡΠ΅Π½Π½ΡΠ΅ Π²ΠΊΠ»Π°Π΄ΡΡΠΈ ΡΠ°ΡΡΠ°ΡΠΈΠ²Π°ΡΡΡΡ Π²ΠΌΠ΅ΡΡΠ΅ Ρ ΠΊΡΡΡΠΊΠ°ΠΌΠΈ ΠΊΠΎΡΠ΅Π½Π½ΡΡ ΠΎΠΏΠΎΡ, ΠΏΠΎΡΡΠΎΠΌΡ ΠΎΠ½ΠΈ Π½Π΅Π²Π·Π°ΠΈΠΌΠΎΠ·Π°ΠΌΠ΅Π½ΡΠ΅ΠΌΡ ΠΈ ΡΡΡΠ°Π½Π°Π²Π»ΠΈΠ²Π°ΡΡΡΡ Π² ΡΡΡΠΎΠ³ΠΎ ΡΠΈΠΊΡΠΈΡΠΎΠ²Π°Π½Π½ΠΎΠΌ ΠΏΠΎΠ»ΠΎΠΆΠ΅Π½ΠΈΠΈ. ΠΠ°ΡΡΠ΅ΡΠ½Π°Ρ ΡΠ°ΡΡΡ Π±Π»ΠΎΠΊΠ° ΡΠΎΠ΅Π΄ΠΈΠ½Π΅Π½Π° Ρ ΠΊΡΡΡΠΊΠ°ΠΌΠΈ ΠΊΠΎΡΠ΅Π½Π½ΡΡ ΠΎΠΏΠΎΡ ΠΏΠΎΠΏΠ΅ΡΠ΅ΡΠ½ΡΠΌΠΈ Π±ΠΎΠ»ΡΠ°ΠΌΠΈ-ΡΡΡΠΆΠΊΠ°ΠΌΠΈ.
Π ΠΏΠ΅ΡΠ΅Π΄Π½Π΅ΠΌΡ ΡΠΎΡΡΡ Π±Π»ΠΎΠΊΠ° ΡΠΈΠ»ΠΈΠ½Π΄ΡΠΎΠ² ΠΏΡΠΈΠΊΡΠ΅ΠΏΠ»Π΅Π½Π° ΠΊΡΡΡΠΊΠ°, ΠΊ Π·Π°Π΄Π½Π΅ΠΌΡ β ΠΊΠ°ΡΡΠ΅Ρ ΠΌΠ°Ρ ΠΎΠ²ΠΈΠΊΠ°, ΡΠ½ΠΈΠ·Ρ Π±Π»ΠΎΠΊ Π·Π°ΠΊΡΡΡ ΠΏΠΎΠ΄Π΄ΠΎΠ½ΠΎΠΌ, ΠΊΠΎΡΠΎΡΡΠΉ ΠΎΠ΄Π½ΠΎΠ²ΡΠ΅ΠΌΠ΅Π½Π½ΠΎ ΡΠ»ΡΠΆΠΈΡ Π΅ΠΌΠΊΠΎΡΡΡΡ Π΄Π»Ρ ΡΠΈΡΡΠ΅ΠΌΡ ΡΠΌΠ°Π·ΠΊΠΈ Π΄Π²ΠΈΠ³Π°ΡΠ΅Π»Ρ.
ΠΠΈΠ»ΡΠ·Ρ ΡΠΈΠ»ΠΈΠ½Π΄ΡΠΎΠ² Β«ΠΌΠΎΠΊΡΠΎΠ³ΠΎΒ» ΡΠΈΠΏΠ° Π»Π΅Π³ΠΊΠΎΡΡΠ΅ΠΌΠ½ΡΠ΅, ΠΈΠ·Π³ΠΎΡΠΎΠ²Π»Π΅Π½Ρ ΠΈΠ· ΡΠΏΠ΅ΡΠΈΠ°Π»ΡΠ½ΠΎΠ³ΠΎ ΡΡΠ³ΡΠ½Π° Ρ ΠΏΠ΅ΡΠ»ΠΈΡΠ½ΠΎΠΉ ΡΡΡΡΠΊΡΡΡΠΎΠΉ ΡΠ΅Π½ΡΡΠΎΠ±Π΅ΠΆΠ½ΡΠΌ Π»ΠΈΡΡΠ΅ΠΌ ΠΈ ΠΎΠ±ΡΠ΅ΠΌΠ½ΠΎ Π·Π°ΠΊΠ°Π»Π΅Π½Ρ ΡΠΎΠΊΠ°ΠΌΠΈ Π²ΡΡΠΎΠΊΠΎΠΉ ΡΠ°ΡΡΠΎΡΡ Π΄Π»Ρ ΠΏΠΎΠ²ΡΡΠ΅Π½ΠΈΡ ΠΈΠ·Π½ΠΎΡΠΎΡΡΠΎΠΉΠΊΠΎΡΡΠΈ. ΠΠ½ΡΡΡΠ΅Π½Π½ΡΡ ΠΏΠΎΠ²Π΅ΡΡ Π½ΠΎΡΡΡ Π³ΠΈΠ»ΡΠ·Ρ ΠΎΠ±ΡΠ°Π±ΠΎΡΠ°Π½Π° ΠΏΠ»ΠΎΡΠΊΠΎΠ²Π΅ΡΡΠΈΠ½Π½ΡΠΌ Ρ ΠΎΠ½ΠΈΠ½Π³ΠΎΠ²Π°Π½ΠΈΠ΅ΠΌ Π΄Π»Ρ ΠΏΠΎΠ»ΡΡΠ΅Π½ΠΈΡ ΡΠ΅Π΄ΠΊΠΎΠΉ ΡΠ΅ΡΠΊΠΈ Π²ΠΏΠ°Π΄ΠΈΠ½ ΠΈ ΠΏΠ»ΠΎΡΠ°Π΄ΠΎΠΊ ΠΏΠΎΠ΄ ΡΠ³Π»ΠΎΠΌ ΠΊ ΠΎΡΠΈ Π³ΠΈΠ»ΡΠ·Ρ. Π’Π°ΠΊΠ°Ρ ΠΎΠ±ΡΠ°Π±ΠΎΡΠΊΠ° ΡΠΏΠΎΡΠΎΠ±ΡΡΠ²ΡΠ΅Ρ ΡΠ΄Π΅ΡΠΆΠ°Π½ΠΈΡ ΠΌΠ°ΡΠ»Π° Π²ΠΎ Π²ΠΏΠ°Π΄ΠΈΠ½Π°Ρ ΠΈ Π»ΡΡΡΠ΅ΠΉ ΠΏΡΠΈΡΠ°Π±Π°ΡΡΠ²Π°Π΅ΠΌΠΎΡΡΠΈ Π³ΠΈΠ»ΡΠ·Ρ.
Π¦Π΅Π½ΡΡΠΈΡΠΎΠ²Π°Π½ΠΈΠ΅ Π³ΠΈΠ»ΡΠ·Ρ Π² Π³Π½Π΅Π·Π΄Π°Ρ Π±Π»ΠΎΠΊΠ° ΠΎΡΡΡΠ΅ΡΡΠ²Π»ΡΠ΅ΡΡΡ ΠΏΡΠΈ ΠΏΠΎΠΌΠΎΡΠΈ Π²Π΅ΡΡ Π½Π΅Π³ΠΎ ΠΈ Π½ΠΈΠΆΠ½Π΅Π³ΠΎ Π½Π°ΡΡΠΆΠ½ΡΡ ΠΎΠ±ΡΠ°Π±ΠΎΡΠ°Π½Π½ΡΡ ΠΏΠΎΡΡΠΎΠ². Π Π²Π΅ΡΡ Π½Π΅ΠΉ ΡΠ°ΡΡΠΈ Π³ΠΈΠ»ΡΠ·Π° ΠΈΠΌΠ΅Π΅Ρ ΡΠΏΠΎΡΠ½ΡΠΉ Π±ΡΡΡ Ρ Π²ΡΡΡΡΠΏΠ°ΠΌΠΈ Π΄Π»Ρ ΡΡΡΠ°Π½ΠΎΠ²ΠΊΠΈ Π½Π° ΡΠΏΠΎΡΠ½ΡΠΉ ΡΠΎΡΠ΅Ρ Π±Π»ΠΎΠΊΠ° ΡΠΈΠ»ΠΈΠ½Π΄ΡΠΎΠ² ΠΈ Π½Π°Π΄Π΅ΠΆΠ½ΠΎΠ³ΠΎ ΡΠΏΠ»ΠΎΡΠ½Π΅Π½ΠΈΡ Π³Π°Π·ΠΎΠ²ΠΎΠ³ΠΎ ΡΡΡΠΊΠ° Ρ Π³ΠΎΠ»ΠΎΠ²ΠΊΠΎΠΉ ΡΠΈΠ»ΠΈΠ½Π΄ΡΠ°.
ΠΠΎΠ΄ΡΠ½Π°Ρ ΠΏΠΎΠ»ΠΎΡΡΡ ΠΌΠ΅ΠΆΠ΄Ρ Π±Π»ΠΎΠΊΠΎΠΌ ΠΈ Π³ΠΈΠ»ΡΠ·ΠΎΠΉ ΡΠΏΠ»ΠΎΡΠ½Π΅Π½Π° ΡΠ΅Π·ΠΈΠ½ΠΎΠ²ΡΠΌΠΈ ΠΊΠΎΠ»ΡΡΠ°ΠΌΠΈ ΠΊΡΡΠ³Π»ΠΎΠ³ΠΎ ΡΠ΅ΡΠ΅Π½ΠΈΡ: Π² Π²Π΅ΡΡ Π½Π΅ΠΉ ΡΠ°ΡΡΠΈ ΠΎΠ΄Π½ΠΎ ΠΊΠΎΠ»ΡΡΠΎ ΡΡΡΠ°Π½ΠΎΠ²Π»Π΅Π½ΠΎ ΠΏΠΎΠ΄ Π±ΡΡΡΠΎΠΌ Π² ΠΏΡΠΎΡΠΎΡΠΊΠ΅ Π³ΠΈΠ»ΡΠ·Ρ, Π² Π½ΠΈΠΆΠ½Π΅ΠΉ ΡΠ°ΡΡΠΈ Π΄Π²Π° ΠΊΠΎΠ»ΡΡΠ° β Π² ΠΏΡΠΎΡΠΎΡΠΊΠ°Ρ Π±Π»ΠΎΠΊΠ°.
ΠΠΎΠ»ΠΎΠ²ΠΊΠΈ ΡΠΈΠ»ΠΈΠ½Π΄ΡΠΎΠ² (ΡΠΈΡ. 2.6), ΠΎΡΠ΄Π΅Π»ΡΠ½ΡΠ΅ Π½Π° ΠΊΠ°ΠΆΠ΄ΡΠΉ ΡΠΈΠ»ΠΈΠ½Π΄Ρ, ΠΈΠ·Π³ΠΎΡΠΎΠ²Π»Π΅Π½Ρ ΠΈΠ· Π°Π»ΡΠΌΠΈΠ½ΠΈΠ΅Π²ΠΎΠ³ΠΎ ΡΠΏΠ»Π°Π²Π°. ΠΠ½ΠΈ ΠΈΠΌΠ΅ΡΡ Π²ΠΎΠ΄ΡΠ½ΡΠ΅ ΠΏΠΎΠ»ΠΎΡΡΠΈ, ΡΠΎΠΎΠ±ΡΠ°ΡΡΠΈΠ΅ΡΡ Ρ ΠΏΠΎΠ»ΠΎΡΡΡΠΌΠΈ Π±Π»ΠΎΠΊΠ°, Π²ΠΏΡΡΠΊΠ½ΡΠ΅ ΠΈ Π²ΡΠΏΡΡΠΊΠ½ΡΠ΅ ΠΊΠ°Π½Π°Π»Ρ, Π²ΡΡΠ°Π²Π½ΡΠ΅ ΡΠ΅Π΄Π»Π° ΠΈ Π½Π°ΠΏΡΠ°Π²Π»ΡΡΡΠΈΠ΅ Π²ΡΡΠ»ΠΊΠΈ ΠΊΠ»Π°ΠΏΠ°Π½ΠΎΠ².
Π‘ΡΡΠΊ Π³ΠΎΠ»ΠΎΠ²ΠΊΠΈ ΡΠΈΠ»ΠΈΠ½Π΄ΡΠ° Ρ Π±Π»ΠΎΠΊΠΎΠΌ ΡΠΏΠ»ΠΎΡΠ½ΡΠ΅ΡΡΡ Π΄Π²ΡΠΌΡ ΡΠΈΠΏΠ°ΠΌΠΈ ΠΏΡΠΎΠΊΠ»Π°Π΄ΠΎΠΊ. Π€ΠΎΡΠΌΠΎΠ²Π°Π½Π½ΡΠ΅ ΡΠ΅Π·ΠΈΠ½ΠΎΠ²ΡΠ΅ ΠΏΡΠΎΠΊΠ»Π°Π΄ΠΊΠΈ ΡΠΏΠ»ΠΎΡΠ½ΡΡΡ ΠΏΠ΅ΡΠ΅ΠΏΡΡΠΊΠ½ΡΠ΅ ΠΎΡΠ²Π΅ΡΡΡΠΈΡ Π΄Π»Ρ Π²ΠΎΠ΄Ρ ΠΈ ΠΌΠ°ΡΠ»Π°, Π° ΡΠ°ΠΊΠΆΠ΅ ΡΡΡΠΊ Π³ΠΎΠ»ΠΎΠ²ΠΊΠΈ Ρ Π±Π»ΠΎΠΊΠΎΠΌ ΠΏΠΎ ΠΊΠΎΠ½ΡΡΡΡ. Π‘ΡΠ°Π»ΡΠ½Π°Ρ ΠΏΡΠΎΠΊΠ»Π°Π΄ΠΊΠ°, Π΄Π΅ΡΠΎΡΠΌΠΈΡΡΠ΅ΠΌΠ°Ρ ΡΡΠ°Π»ΡΠ½ΡΠΌ ΡΠΏΠΎΡΠ½ΡΠΌ ΠΊΠΎΠ»ΡΡΠΎΠΌ, Π·Π°ΠΏΡΠ΅ΡΡΠΎΠ²Π°Π½Π½ΡΠΌ Π² Π³ΠΎΠ»ΠΎΠ²ΠΊΡ Π½Π° Π½ΠΈΠΆΠ½Π΅ΠΉ ΠΏΠ»ΠΎΡΠΊΠΎΡΡΠΈ, β Π³Π°Π·ΠΎΠ²ΡΠΉ ΡΡΡΠΊ.
Π ΠΈΡ. 2.6. ΠΠΎΠ»ΠΎΠ²ΠΊΠ° ΡΠΈΠ»ΠΈΠ½Π΄ΡΠ° Ρ ΠΊΠ»Π°ΠΏΠ°Π½Π°ΠΌΠΈ Π² ΡΠ±ΠΎΡΠ΅:
1 βΠ³ΠΎΠ»ΠΎΠ²ΠΊΠ° ΡΠΈΠ»Π½Π½Π΄ΡΠ°; 2 β ΠΏΡΠΎΠΊΠ»Π°Π΄ΠΊΠ° ΠΊΡΡΡΠΊΠΈ Π³ΠΎΠ»ΠΎΠ²ΠΊΠΈ; 3 β Π±ΠΎΠ»Ρ ΠΊΡΠ΅ΠΏΠ»Π΅Π½ΠΈΡ ΠΊΡΡΡΠΊΠΈ; 4 β ΠΊΡΡΡΠΊΠ° Π³ΠΎΠ»ΠΎΠ²ΠΊΠΈ ΡΠΈΠ»ΠΈΠ½Π΄ΡΠ°; Π±β Π±ΠΎΠ»Ρ ΠΊΡΠΎΠΏΠ»Π΅Π½ΠΈΡ Π³ΠΎΠ»ΠΎΠ²ΠΊΠΈ; 6 β Π²ΡΡΠ»ΠΊΠ° ΠΏΡΠΎΠΊΠ»Π°Π΄ΠΊΠΈ ΠΏΠ°ΡΡΡΠ±ΠΊΠ°; 7βΡΠΏΠ»ΠΎΡΠ½ΠΈΡΠ΅Π»ΡΠ½ΠΎΠ΅ ΠΊΠΎΠ»ΡΡΠΎ Π³Π°Π·ΠΎΡΠΎΠ³ΠΎ ΡΡΡΠΊΠ°; 8 β Π²ΡΠΏΡΡΠΊΠ½ΠΎΠΉ ΠΊΠ»Π°ΠΏΠ°Π½; 9 β ΡΠ΅Π΄Π»ΠΎ ΠΊΠ»Π°ΠΏΠ°Π½Π°; J8β Π½Π°ΠΏΡΠ°Π²Π»ΡΡΡΠ°Ρ Π²ΡΡΠ»ΠΊΠ° ΠΊΠ»Π°ΠΏΠ°Π½Π°; 11 β ΡΠ°ΠΉΠ±Π° ΠΏΡΡΠΆΠΈΠ½ ΠΊΠ»Π°ΠΏΠ°Π½Π°; 12 β Π½Π°ΡΡΠΆΠ½Π°Ρ ΠΈ Π²Π½ΡΡΡΠ΅Π½Π½ΡΡ ΠΏΡΡΠΆΠΈΠ½Ρ ΠΊΠ»Π°ΠΏΠ°Π½Π°; 13 β ΡΠ°ΡΠ΅Π»ΠΊΠ° ΠΏΡΡΠΆΠΈΠ½ ΠΊΠ»Π°ΠΏΠ°Π½Π°; 14 β Π²ΡΡΠ»ΠΊΠ° ΡΠ°ΡΠ΅Π»ΠΊΠΈ; 15 β ΡΡΡ
Π°ΡΡ ΠΊΠ»Π°ΠΏΠ°Π½Π°; 16 β ΡΠΏΠ»ΠΎΡΠ½ΠΈΡΠ΅Π»ΡΠ½Π°Ρ ΠΌΠ°Π½ΠΆΠ΅ΡΠ°; 17 β Π²ΠΏΡΡΠΊΠ½ΠΎΠΉ ΠΊΠ»Π°ΠΏΠ°Π½
Π Π³ΠΎΠ»ΠΎΠ²ΠΊΠ°Ρ ΡΠΈΠ»ΠΈΠ½Π΄ΡΠΎΠ² ΡΠ°Π·ΠΌΠ΅ΡΠ΅Π½Ρ ΠΊΠ»Π°ΠΏΠ°Π½Π½ΡΠΉ ΠΌΠ΅Ρ Π°Π½ΠΈΠ·ΠΌ ΠΈ ΡΠΎΡΡΡΠ½ΠΊΠ°. ΠΠ»Π°ΠΏΠ°Π½Π½ΡΠΉ ΠΌΠ΅Ρ Π°Π½ΠΈΠ·ΠΌ Π³ΠΎΠ»ΠΎΠ²ΠΊΠΈ Π·Π°ΠΊΡΡΡ Π°Π»ΡΠΌΠΈΠ½ΠΈΠ΅Π²ΠΎΠΉ ΠΊΡΡΡΠΊΠΎΠΉ, ΡΠΏΠ»ΠΎΡΠ½Π΅Π½Π½ΠΎΠΉ ΠΏΡΠΎΠΊΠ»Π°Π΄ΠΊΠΎΠΉ. Π§ΡΠ³ΡΠ½Π½ΡΠ΅ ΡΠ΅Π΄Π»Π° ΠΈ ΠΌΠ΅ΡΠ°Π»Π»ΠΎΠΊΠ΅ΡΠ°-ΠΌΠΈΡΠ΅ΡΠΊΠΈΠ΅ Π½Π°ΠΏΡΠ°Π²Π»ΡΡΡΠΈΠ΅ Π²ΡΡΠ»ΠΊΠΈ ΠΊΠ»Π°ΠΏΠ°Π½ΠΎΠ² ΡΠ°ΡΡΠ°ΡΠΈΠ²Π°ΡΡΡΡ ΠΏΠΎΡΠ»Π΅ ΠΈΡ Π·Π°ΠΏΡΠ΅ΡΡΠΎΠ²ΠΊΠΈ Π² Π³ΠΎΠ»ΠΎΠ²ΠΊΡ. Π‘ΠΎ Π‘ΡΠΎΡΠΎΠ½Ρ ΠΏΡΠΈΠ²Π°Π»ΠΎΡΠ½ΠΎΠΉ ΠΏΠ»ΠΎΡΠΊΠΎΡΡΠΈ ΠΊΠ°ΠΆΠ΄ΠΎΠΉ Π³ΠΎΠ»ΠΎΠ²ΠΊΠΈ Π²ΡΠΏΠΎΠ»Π½Π΅Π½Ρ Π΄Π²Π° ΠΎΡΠ²Π΅ΡΡΡΠΈΡ, Π² ΠΊΠΎΡΠΎΡΡΠ΅ ΠΏΡΠΈ ΡΠ±ΠΎΡΠΊΠ΅ Π΄Π²ΠΈΠ³Π°ΡΠ΅Π»Ρ Π²Ρ ΠΎΠ΄ΡΡ Π·Π°ΠΏΡΠ΅ΡΡΠΎΠ²Π°Π½Π½ΡΠ΅ Π² Π±Π»ΠΎΠΊ ΡΠΈΠΊΡΠΈΡΡΡΡΠΈΠ΅ ΡΡΠΈΡΡΡ. ΠΠ°ΠΆΠ΄Π°Ρ Π³ΠΎΠ»ΠΎΠ²ΠΊΠ° ΠΊΡΠ΅ΠΏΠΈΡΡΡ ΠΊ Π±Π»ΠΎΠΊΡ ΡΠΈΠ»ΠΈΠ½Π΄ΡΠΎΠ² ΡΠ΅ΡΡΡΡΠΌΡ Π±ΠΎΠ»ΡΠ°ΠΌΠΈ. ΠΡΠ²Π΅ΡΡΡΠΈΡ ΠΏΠΎΠ΄ Π±ΠΎΠ»ΡΡ Π²ΡΠΏΠΎΠ»Π½Π΅Π½Ρ Π² ΡΠΏΠ΅ΡΠΈΠ°Π»ΡΠ½ΡΡ Π±ΠΎΠ±ΡΡΠΊΠ°Ρ , ΡΠ΄Π΅Π»Π°Π½Π½ΡΡ Π² Π±ΠΎΠΊΠΎΠ²ΡΡ ΡΡΠ΅Π½ΠΊΠ°Ρ Π²ΠΎΠ΄ΡΠ½ΠΎΠΉ ΡΡΠ±Π°ΡΠΊΠΈ.
ΠΠΏΡΡΠΊΠ½ΠΎΠΉ ΠΈ Π²ΡΠΏΡΡΠΊΠ½ΠΎΠΉ ΠΊΠ°Π½Π°Π»Ρ ΡΠ°ΡΠΏΠΎΠ»ΠΎΠΆΠ΅Π½Ρ Π² ΠΏΡΠΎΡΠΈΠ²ΠΎΠΏΠΎΠ»ΠΎΠΆΠ½ΡΡ Π±ΠΎΠΊΠΎΠ²ΡΡ ΡΡΠ΅Π½ΠΊΠ°Ρ Π³ΠΎΠ»ΠΎΠ²ΠΊΠΈ. ΠΠΏΡΡΠΊΠ½ΠΎΠΉ ΠΊΠ°Π½Π°Π» ΠΈΠΌΠ΅Π΅Ρ ΡΠ°Π½Π³Π΅Π½ΡΠΈΠ°Π»ΡΠ½ΡΠΉ ΠΏΡΠΎΡΠΈΠ»Ρ, ΠΎΠ±Π΅ΡΠΏΠ΅ΡΠΈΠ²Π°ΡΡΠΈΠΉ Π²ΠΈΡ ΡΠ΅Π²ΠΎΠ΅ Π΄Π²ΠΈΠΆΠ΅Π½ΠΈΠ΅ Π²ΠΎΠ·Π΄ΡΡ Π° Π² ΡΠΈΠ»ΠΈΠ½Π΄ΡΠ΅, ΡΠ»ΡΡΡΠ΅Π½ΠΈΠ΅ ΡΠΌΠ΅ΡΠ΅ΠΎΠ±ΡΠ°Π·ΠΎΠ²Π°Π½ΠΈΡ ΠΈ ΡΡΠΊΠΎΡΠ΅Π½ΠΈΠ΅ ΠΏΡΠΎΡΠ΅ΡΡΠ° ΡΠ³ΠΎΡΠ°Π½ΠΈΡ Π²ΠΏΡΡΡΠΊΠΈΠ²Π°Π΅ΠΌΠΎΠ³ΠΎ ΡΠΎΠΏΠ»ΠΈΠ²Π°. ΠΠ½Π΅Π·Π΄ΠΎ ΠΏΠΎΠ΄ ΡΠΎΡΡΡΠ½ΠΊΡ ΡΠ°ΡΠΏΠΎΠ»ΠΎΠΆΠ΅Π½ΠΎ ΡΠΎ ΡΡΠΎΡΠΎΠ½Ρ ΠΈΡΠΏΡΡΠΊΠ° ΠΏΠΎΠ΄ ΡΠ³Π»ΠΎΠΌ ΠΊ ΠΎΡΠΈ ΡΠΈΠ»ΠΈΠ½Π΄ΡΠ°.
ΠΠΎΡΡΠ½ΠΈ (ΡΠΈΡ. 2.7) ΠΈΠ·Π³ΠΎΡΠΎΠ²Π»Π΅Π½Ρ ΠΈΠ· Π²ΡΡΠΎΠΊΠΎΠΊΡΠ΅ΠΌΠ½ΠΈΡΡΠΎΠ³ΠΎ Π°Π»ΡΠΌΠΈΠ½ΠΈΠ΅Π²ΠΎΠ³ΠΎ ΡΠΏΠ»Π°Π²Π°. ΠΡΠΈΠΌΠ΅Π½Π΅Π½ΠΈΠ΅ Π°Π»ΡΠΌΠΈΠ½ΠΈΠ΅Π²ΠΎΠ³ΠΎ ΡΠΏΠ»Π°Π²Π° ΡΠ»ΡΡΡΠ°Π΅Ρ ΡΠ΅ΠΏΠ»ΠΎΠΎΡΠ΄Π°ΡΡ ΠΈ ΡΠΌΠ΅Π½ΡΡΠ°Π΅Ρ ΠΌΠ°ΡΡΡ ΠΏΠΎΡΡΠ½Π΅ΠΉ, Π° ΡΠ»Π΅Π΄ΠΎΠ²Π°ΡΠ΅Π»ΡΠ½ΠΎ, ΠΈ ΠΈΠ½Π΅ΡΡΠΈΠΎΠ½Π½ΡΠ΅ ΡΠΈΠ»Ρ, Π΄Π΅ΠΉΡΡΠ²ΡΡΡΠΈΠ΅ Π² ΠΊΡΠΈΠ²ΠΎΡΠΈΠΏΠ½ΠΎ-ΡΠ°ΡΡΠ½Π½ΠΎΠΌ ΠΌΠ΅Ρ Π°Π½ΠΈΠ·ΠΌΠ΅ ΠΈΠ·-Π·Π° Π½Π΅ΡΠ°Π²Π½ΠΎΠΌΠ΅ΡΠ½ΠΎΠ³ΠΎ Π΄Π²ΠΈΠΆΠ΅Π½ΠΈΡ ΠΏΠΎΡΡΠ½Π΅ΠΉ.
Π ΠΈΡ. 2.7. ΠΠΎΡΡΠ΅Π½Ρ Ρ ΡΠ°ΡΡΠ½ΠΎΠΌ:
1 β ΠΌΠ°ΡΠ΄ΠΎ.ΡΡΠ΅ΠΌΠ½ΠΎΠ΅ ΠΊΠΎΠ»ΡΡΠΎ Π² ΠΎΠ±ΠΎΡΠ΅;, 2, β Π²ΠΈΡΠΎΠΉ ΠΏΡΡΠΆΠΈΠ½Π½ΡΠΉ, ΡΠ°ΡΡΠΈΡΠΈΡΠ΅Π»Ρ; 3 β ΡΡΠ³ΡΠ½Π½ΠΎΠ΅ ΠΊΠΎΠ»ΡΡΠΎ; 4 β ΠΊΠΎΠΌΠΏΡΠ΅ΡΡΠΈΠΎΠ½Π½ΠΎΠ΅ ΠΊΠΎΠ»ΡΡΠΎ; 5 β ΡΡΠΎΠΏΠΎΡΠ½ΠΎΠ΅ ΠΊΠΎΠ»ΡΡΠΎ ΠΏΠΎΡΡΠ½Π΅Π²ΠΎΠ³ΠΎ ΠΏΠ°Π»ΡΡΠ°; 6 β ΠΏΠΎΡΡΠ΅Π½Ρ; 7 β Π²ΡΡΠ»ΠΊΠ° ΡΠ°ΡΡΠ½Π°; 8 β ΡΠ°ΡΡΠ½; 9Π±ΠΎΠ»Ρ ΠΊΡΠ΅ΠΏΠ»Π΅Π½ΠΈΡ ΠΊΡΡΡΠΊΠΈ ΡΠ°ΡΡΠ½Π°; 10 β ΠΊΡΡΡΠΊΠ°, ΡΠ°ΡΡΠ½Π½ΠΎΠ³ΠΎ ΠΏΠΎΠ΄ΡΠΈΠΏΠ½ΠΈΠΊΠ°; 11 β Π²ΠΊΠ»Π°Π΄ΡΡ Π½ΠΈΠΆΠ½Π΅ΠΉ Π³ΠΎΠ»ΠΎΠ²ΠΊΠΈ ΡΠ°ΡΡΠ½Π°
Π ΡΠΎΠ»ΡΡΠΎΡΡΠ΅Π½Π½ΠΎΠΌ Π΄Π½ΠΈΡΠ΅ ΠΏΠΎΡΡΠ½Ρ Π²ΡΠΏΠΎΠ»Π½Π΅Π½Π° ΠΎΡΠΊΡΡΡΠ°Ρ ΡΠΎΡΠΎΠΈΠ΄Π°Π»ΡΠ½Π°Ρ ΠΊΠ°ΠΌΠ΅ΡΠ° ΡΠ³ΠΎΡΠ°Π½ΠΈΡ, Π° Π² Π³ΠΎΠ»ΠΎΠ²ΠΊΠ΅ ΠΏΠΎΡΡΠ½Ρ β ΡΡΠΈ ΠΊΠ°Π½Π°Π²ΠΊΠΈ ΠΏΠΎΠ΄ ΠΏΠΎΡΡΠ½Π΅Π²ΡΠ΅ ΠΊΠΎΠ»ΡΡΠ°. ΠΠ΅ΡΡ Π½ΡΡ ΠΊΠ°Π½Π°Π²ΠΊΠ°, Π½Π°ΠΈΠ±ΠΎΠ»Π΅Π΅ Π½Π°Π³ΡΡΠΆΠ΅Π½Π½Π°Ρ, ΠΈΠΌΠ΅Π΅Ρ Π²ΡΡΠ°Π²ΠΊΡ ΠΈΠ· ΠΆΠ°ΡΠΎΠΏΡΠΎΡΠ½ΠΎΠ³ΠΎ ΡΡΠ³ΡΠ½Π°.
ΠΠΎΠΊΠΎΠ²Π°Ρ ΠΏΠΎΠ²Π΅ΡΡ Π½ΠΎΡΡΡ ΠΏΠΎΡΡΠ½Ρ ΠΏΠΎ Π²ΡΡΠΎΡΠ΅ Π±ΠΎΡΠΊΠΎΠΎΠ±ΡΠ°Π·Π½Π°Ρ (Π΄ΠΈΠ°ΠΌΠ΅ΡΡ Π³ΠΎΠ»ΠΎΠ²ΠΊΠΈ ΠΏΠΎΡΡΠ½Ρ ΠΌΠ΅Π½ΡΡΠ΅ Π΄ΠΈΠ°ΠΌΠ΅ΡΡΠ° ΡΠ±ΠΊΠΈ). Π ΠΏΠΎΠΏΠ΅ΡΠ΅ΡΠ½ΠΎΠΌ ΡΠ΅ΡΠ΅Π½ΠΈΠΈ ΡΠ±ΠΊΠ° ΠΈΠΌΠ΅Π΅Ρ ΡΠΎΡΠΌΡ ΡΠ»Π»ΠΈΠΏΡΠ°, ΠΏΡΠΈΡΠ΅ΠΌ Π±ΠΎΠ»ΡΡΠ°Ρ ΠΎΡΡ ΡΠ»Π»ΠΈΠΏΡΠ° ΡΠ°ΡΠΏΠΎΠ»ΠΎΠΆΠ΅Π½Π° Π² ΠΏΠ»ΠΎΡΠΊΠΎΡΡΠΈ, ΠΏΠ΅ΡΠΏΠ΅Π½Π΄ΠΈΠΊΡΠ»ΡΡΠ½ΠΎΠΉ ΠΊ ΠΎΡΠΈ ΠΏΠ°Π»ΡΡΠ°. Π’Π°ΠΊΠ°Ρ ΠΊΠΎΠ½ΡΡΡΡΠΊΡΠΈΡ ΠΏΠΎΡΡΠ½Ρ ΠΎΠ±Π΅ΡΠΏΠ΅ΡΠΈΠ²Π°Π΅Ρ ΠΏΡΠ°ΠΊΡΠΈΡΠ΅ΡΠΊΡΡ Π½Π΅Π·Π°Π²ΠΈΡΠΈΠΌΠΎΡΡΡ Π·Π°Π·ΠΎΡΠ° ΠΌΠ΅ΠΆΠ΄Ρ ΠΏΠΎΡΡΠ½Π΅ΠΌ ΠΈ Π³ΠΈΠ»ΡΠ·ΠΎΠΉ, Π² ΠΏΠ»ΠΎΡΠΊΠΎΡΡΠΈ Π΄Π²ΠΈΠΆΠ΅Π½ΠΈΡ ΡΠ°ΡΡΠ½Π° ΠΎΡ ΡΠ΅ΠΏΠ»ΠΎΠ²ΠΎΠ³ΠΎ ΡΠΎΡΡΠΎΡΠ½ΠΈΡ Π΄Π²ΠΈΠ³Π°ΡΠ΅Π»Ρ ΠΈ ΡΠ΅ΠΌ ΡΠ°ΠΌΡΠΌ ΠΏΡΠ΅Π΄ΠΎΡΠ²ΡΠ°ΡΠ°Π΅Ρ Π·Π°ΠΊΠ»ΠΈΠ½ΠΈΠ²Π°Π½ΠΈΠ΅ ΠΏΠΎΡΡΠ½Ρ ΠΏΡΠΈ ΡΠ°Π±ΠΎΡΠ΅ ΠΏΡΠΎΠ³ΡΠ΅ΡΠΎΠ³ΠΎ Π΄Π²ΠΈΠ³Π°ΡΠ΅Π»Ρ.Π ΡΠΎ ΠΆΠ΅ Π²ΡΠ΅ΠΌΡ Π²ΡΠ»Π΅Π΄ΡΡΠ²ΠΈΠ΅ ΡΠ»Π»ΠΈΠΏΡΠΈΡΠ½ΠΎΡΡΠΈ ΠΏΠΎΡΡΠ½Ρ ΠΏΡΠΈ ΡΠ°Π±ΠΎΡΠ΅ Π½Π΅ΠΏΡΠΎΠ³ΡΠ΅ΡΠΎΠ³ΠΎ Π΄Π²ΠΈΠ³Π°ΡΠ΅Π»Ρ ΡΠ½ΠΈΠΆΠ°Π΅ΡΡΡ ΡΡΠΌ Π±Π»Π°Π³ΠΎΠ΄Π°ΡΡ ΡΠΌΠ΅Π½ΡΡΠ΅Π½Π½ΠΎΠΌΡ Π·Π°Π·ΠΎΡΡ ΠΌΠ΅ΠΆΠ΄Ρ ΠΏΠΎΡΡΠ½Π΅ΠΌ ΠΈ ΡΡΠ΅Π½ΠΊΠΎΠΉ Π¦ΠΈΠ»ΠΈΠ½Π΄ΡΠ° Π² Π½Π°ΠΏΡΠ°Π²Π»Π΅Π½ΠΈΠΈ Π΄Π΅ΠΉΡΡΠ²ΡΡΡΠ΅ΠΉ Π½Π° ΠΏΠΎΡΡΠ΅Π½Ρ Π±ΠΎΠΊΠΎΠ²ΠΎΠΉ ΡΠΈΠ»Ρ ΠΎΡ ΡΠ°ΡΡΠ½Π°..
ΠΠ° ΠΏΠΎΠ²Π΅ΡΡ Π½ΠΎΡΡΡ ΡΠ±ΠΊΠΈ ΠΏΠΎΡΡΠ½Ρ Π½Π°Π½Π΅ΡΠ΅Π½ΠΎ ΠΊΠΎΠ»Π»ΠΎΠΈΠ΄Π½ΠΎ-Π³ΡΠ°ΡΠΈΡΠΎΠ²ΠΎΠ΅ ΠΏΠΎΠΊΡΡΡΠΈΠ΅ Π΄Π»Ρ ΡΠ»ΡΡΡΠ΅Π½ΠΈΡ ΠΏΡΠΈΡΠ°Π±ΠΎΡΠΊΠΈ ΠΏΠΎΡΡΠ½Ρ ΠΊ Π³ΠΈΠ»ΡΠ·Π΅.
ΠΠ½ΡΡΡΠ΅Π½Π½ΡΡ ΡΠΎΡΠΌΠ° ΠΏΠΎΡΡΠ½Ρ ΠΎΠ±Π΅ΡΠΏΠ΅ΡΠΈΠ²Π°Π΅Ρ ΡΠ°Π²Π½ΠΎΠΌΠ΅ΡΠ½ΠΎΠ΅ ΡΠ°ΡΠΏΡΠ΅Π΄Π΅Π»Π΅Π½ΠΈΠ΅ ΡΠ΅ΠΏΠ»Π° ΠΎΡ Π΄Π½ΠΈΡΠ° ΠΊ ΡΠ±ΠΊΠ΅. ΠΠΎΠ»ΡΡΠ΅Π²ΠΎΠ΅ ΡΡΠΎΠ»ΡΠ΅Π½ΠΈΠ΅ Π½Π° Π½ΠΈΠΆΠ½Π΅ΠΉ Π²Π½ΡΡΡΠ΅Π½Π½Π΅ΠΉ ΡΡΠΎΡΠΎΠ½Π΅ ΡΠ±ΠΊΠΈ ΡΠ²Π΅Π»ΠΈΡΠΈΠ²Π°Π΅Ρ ΠΆΠ΅ΡΡΠΊΠΎΡΡΡ ΠΏΠΎΡΡΠ½Ρ ΠΈ ΠΎΠ±Π΅ΡΠΏΠ΅ΡΠΈΠ²Π°Π΅Ρ Π²ΠΎΠ·ΠΌΠΎΠΆΠ½ΠΎΡΡΡ ΡΠ»ΡΡΠΈΡΠ½ΠΎΠ³ΠΎ ΡΡΠ΅Π·Π°Π½ΠΈΡ ΡΡΠΎΠ³ΠΎ ΡΡΠΎΠ»ΡΠ΅Π½ΠΈΡ Π΄Π»Ρ ΠΏΠΎΠ΄Π³ΠΎΠ½ΠΊΠΈ ΠΏΠΎΡΡΠ½Π΅ΠΉ ΠΏΠΎ ΠΌΠ°ΡΡΠ΅.
ΠΠΈΠΆΠ½ΡΡ ΠΊΠ°Π½Π°Π²ΠΊΠ° ΠΏΠΎΠ΄ ΠΌΠ°ΡΠ»ΠΎΡΡΠ΅ΠΌΠ½ΠΎΠ΅ ΠΊΠΎΠ»ΡΡΠΎ ΠΈΠΌΠ΅Π΅Ρ ΠΎΡΠ²Π΅ΡΡΡΠΈΡ ΠΏΠΎ Π²ΡΠ΅ΠΉ ΠΎΠΊΡΡΠΆΠ½ΠΎΡΡΠΈ Π΄Π»Ρ ΠΎΡΠ²ΠΎΠ΄Π° ΠΌΠ°ΡΠ»Π°, ΡΠ½ΠΈΠΌΠ°Π΅ΠΌΠΎΠ³ΠΎ ΠΊΠΎΠ»ΡΡΠΎΠΌ Ρ ΠΏΠΎΠ²Π΅ΡΡ Π½ΠΎΡΡΠΈ ΡΠΈΠ»ΠΈΠ½Π΄ΡΠ°.
ΠΠ° ΠΊΠ°ΠΆΠ΄ΠΎΠΌ ΠΏΠΎΡΡΠ½Π΅ ΡΡΡΠ°Π½Π°Π²Π»ΠΈΠ²Π°ΡΡΡΡ Π΄Π²Π° ΠΊΠΎΠΌΠΏΡΠ΅ΡΡΠΈΠΎΠ½Π½ΡΡ ΠΈ ΠΎΠ΄Π½ΠΎ ΠΌΠ°ΡΠ»ΠΎΡΡΠ΅ΠΌΠ½ΠΎΠ΅ ΠΊΠΎΠ»ΡΡΠ°. ΠΠΎΠΌΠΏΡΠ΅ΡΡΠΈΠΎΠ½Π½ΡΠ΅ ΠΊΠΎΠ»ΡΡΠ° ΠΈΠ·Π³ΠΎΡΠΎΠ²Π»Π΅Π½Ρ ΠΈΠ· ΡΡΠ³ΡΠ½Π° Ρ ΡΠ°ΡΠΎΠ²ΠΈΠ΄Π½ΡΠΌ Π³ΡΠ°ΡΠΈΡΠΎΠΌ. Π Π°Π±ΠΎΡΠ°Ρ ΠΏΠΎΠ²Π΅ΡΡ Π½ΠΎΡΡΡ Π½Π°ΠΈΠ±ΠΎΠ»Π΅Π΅ Π½Π°Π³ΡΡΠΆΠ΅Π½Π½ΠΎΠ³ΠΎ Π²Π΅ΡΡ Π½Π΅Π³ΠΎ ΠΊΠΎΠΌΠΏΡΠ΅ΡΡΠΈΠΎΠ½Π½ΠΎΠ³ΠΎ ΠΊΠΎΠ»ΡΡΠ° ΠΏΠΎΠΊΡΡΡΠ° ΡΠ»ΠΎΠ΅ΠΌ Ρ ΡΠΎΠΌΠ°, Π½ΠΈΠΆΠ½Π΅Π³ΠΎ β ΡΠ»ΠΎΠ΅ΠΌ ΠΌΠΎΠ»ΠΈΠ±Π΄Π΅Π½Π°. ΠΠ°ΡΠ»ΠΎΡΡΠ΅ΠΌΠ½ΠΎΠ΅ ΠΊΠΎΠ»ΡΡΠΎΠΌ ΡΠ±ΠΎΡΠ½ΠΎΠΉ ΠΊΠΎΠ½ΡΡΡΡΠΊΡΠΈΠΈ. ΠΠ½ΠΎ ΡΠΎΡΡΠΎΠΈΡ ΠΈΠ· ΡΡΠ³ΡΠ½Π½ΠΎΠ³ΠΎ ΠΊΠΎΠ»ΡΡΠ° ΠΊΠΎΡΠΎΠ±ΡΠ°ΡΠΎΠ³ΠΎ ΡΠ΅ΡΠ΅Π½ΠΈΡ Ρ Ρ ΡΠΎΠΌΠΈΡΠΎΠ²Π°Π½Π½ΠΎΠΉ ΡΠ°Π±ΠΎΡΠ΅ΠΉ ΠΏΠΎΠ²Π΅ΡΡ Π½ΠΎΡΡΡΡ ΠΈ Π²ΠΈΡΠΎΠ³ΠΎ ΠΏΡΡΠΆΠΈΠ½Π½ΠΎΠ³ΠΎ ΡΠ°ΡΡΠΈΡΠΈΡΠ΅Π»Ρ. Π₯ΡΠΎΠΌΠΈΡΠΎΠ²Π°Π½ΠΈΠ΅ ΠΊΠΎΠ»Π΅Ρ ΠΏΠΎΠ²ΡΡΠ°Π΅Ρ ΠΈΡ ΠΈΠ·Π½ΠΎΡΠΎΡΡΠΎΠΉΠΊΠΎΡΡΡ.
ΠΠΎΡΡΠ΅Π½Ρ Ρ ΡΠ°ΡΡΠ½ΠΎΠΌ ΡΠΎΠ΅Π΄ΠΈΠ½Π΅Π½ ΠΏΡΡΡΠΎΡΠ΅Π»ΡΠΌ ΠΏΠ°Π»ΡΡΠ΅ΠΌ ΠΏΠ»Π°Π²Π°ΡΡΠ΅Π³ΠΎ ΡΠΈΠΏΠ°, ΠΎΡΠ΅Π²ΠΎΠ΅ ΠΏΠ΅ΡΠ΅ΠΌΠ΅ΡΠ΅Π½ΠΈΠ΅ ΠΊΠΎΡΠΎΡΠΎΠ³ΠΎ Π² ΠΏΠΎΡΡΠ½Π΅ ΠΎΠ³ΡΠ°Π½ΠΈΡΠΈΠ²Π°Π΅ΡΡΡ Π΄Π²ΡΠΌΡ ΠΏΡΡΠΆΠΈΠ½Π½ΡΠΌΠΈ ΡΡΠΎΠΏΠΎΡΠ½ΡΠΌΠΈ ΠΊΠΎΠ»ΡΡΠ°ΠΌΠΈ.
Π¨Π°ΡΡΠ½Ρ ΡΡΠ°Π»ΡΠ½ΡΠ΅, Π΄Π²ΡΡΠ°Π²ΡΠΎΠ²ΠΎΠ³ΠΎ ΡΠ΅ΡΠ΅Π½ΠΈΡ. ΠΠΈΠΆΠ½ΡΡ Π³ΠΎΠ»ΠΎΠ²ΠΊΠ° ΡΠ°ΡΡΠ½Π° ΡΠ°Π·ΡΠ΅ΠΌΠ½Π°Ρ. ΠΠ»Ρ ΡΠΎΡΠ½ΠΎΠΉ ΠΏΠΎΡΠ°Π΄ΠΊΠΈ Π²ΠΊΠ»Π°Π΄ΡΡΠ΅ΠΉ ΠΏΠΎΠ΄ΡΠΈΠΏΠ½ΠΈΠΊΠ° Π½ΠΈΠΆΠ½ΡΡ Π³ΠΎΠ»ΠΎΠ²ΠΊΡ ΡΠ°ΡΡΠ½Π° ΠΎΠΊΠΎΠ½ΡΠ°ΡΠ΅Π»ΡΠ½ΠΎ ΠΎΠ±ΡΠ°Π±Π°ΡΡΠ²Π°ΡΡ Π² ΡΠ±ΠΎΡΠ΅ Ρ ΠΊΡΡΡΠΊΠΎΠΉ, Π²ΡΠ»Π΅Π΄ΡΡΠ²ΠΈΠ΅ ΡΠ΅Π³ΠΎ ΠΊΡΡΡΠΊΠΈ ΡΠ°ΡΡΠ½ΠΎΠ² Π½Π΅Π²Π·Π°ΠΈΠΌΠΎΠ·Π°ΠΌΠ΅Π½ΡΠ΅ΠΌΡΠ΅. ΠΠ° ΠΊΡΡΡΠΊΠ΅ ΠΈ ΡΠ°ΡΡΠ½Π΅ Π½Π°Π½Π΅ΡΠ΅Π½Ρ ΠΌΠ΅ΡΠΊΠΈ ΡΠΏΠ°ΡΠ΅Π½Π½ΠΎΡΡΠΈ Π² Π²ΠΈΠ΄Π΅ ΡΡΠ΅Ρ Π·Π½Π°ΡΠ½ΡΡ ΠΏΠΎΡΡΠ΄ΠΊΠΎΠ²ΡΡ Π½ΠΎΠΌΠ΅ΡΠΎΠ². ΠΡΠΎΠΌΠ΅ ΡΠΎΠ³ΠΎ, Π½Π° ΠΊΡΡΡΠΊΠ΅ ΡΠ°ΡΡΠ½Π° Π²ΡΠ±ΠΈΡ ΠΏΠΎΡΡΠ΄ΠΊΠΎΠ²ΡΠΉ Π½ΠΎΠΌΠ΅Ρ ΡΠΈΠ»ΠΈΠ½Π΄ΡΠ°.
ΠΠΎΠ΄ΡΠΈΠΏΠ½ΠΈΠΊΠ°ΠΌΠΈ ΡΠΊΠΎΠ»ΡΠΆΠ΅Π½ΠΈΡ Π² Π²Π΅ΡΡ Π½Π΅ΠΉ Π³ΠΎΠ»ΠΎΠ²ΠΊΠ΅ ΡΠ°ΡΡΠ½Π° ΡΠ»ΡΠΆΠ°Ρ Π±ΠΈΠΌΠ΅ΡΠ°Π»Π»ΠΈΡΠ΅ΡΠΊΠΈΠ΅ Π½Π΅ΡΠ°Π·ΡΠ΅ΠΌΠ½ΡΠ΅ Π²ΡΡΠ»ΠΊΠΈ Ρ ΡΠ°Π±ΠΎΡΠΈΠΌ Π±ΡΠΎΠ½Π·ΠΎΠ²ΡΠΌ ΡΠ»ΠΎΠ΅ΠΌ; Π² Π½ΠΈΠΆΠ½Π΅ΠΉ Π³ΠΎΠ»ΠΎΠ²ΠΊΠ΅ ΡΠ°ΡΡΠ½Π° β ΡΡΠ΅ΠΌΠ½ΡΠ΅ Π²Π·Π°ΠΈΠΌΠΎΠ·Π°ΠΌΠ΅Π½ΡΠ΅ΠΌΡΠ΅ Π²ΠΊΠ»Π°Π΄ΡΡΠΈ. ΠΡΡΡΠΊΠ° Π½ΠΈΠΆΠ½Π΅ΠΉ Π³ΠΎΠ»ΠΎΠ²ΠΊΠΈ ΡΠ°ΡΡΠ½Π° ΠΊΡΠ΅ΠΏΠΈΡΡΡ Π³Π°ΠΉΠΊΠ°ΠΌΠΈ Π½Π° Π΄Π²ΡΡ Π±ΠΎΠ»ΡΠ°Ρ , Π·Π°ΠΏΡΠ΅ΡΡΠΎΠ²Π°Π½Π½ΡΡ Π² Π±ΠΎΠΊΠΎΠ²ΡΠ΅ Π²ΡΡΡΡΠΏΡ Π²Π΅ΡΡ Π½Π΅ΠΉ Π³ΠΎΠ»ΠΎΠ²ΠΊΠΈ ΡΠ°ΡΡΠ½Π°. ΠΠ° ΠΊΠ°ΠΆΠ΄ΠΎΠΉ ΡΠ°ΡΡΠ½Π½ΠΎΠΉ ΡΠ΅ΠΉΠΊΠ΅ ΠΊΠΎΠ»Π΅Π½ΡΠ°ΡΠΎΠ³ΠΎ Π²Π°Π»Π° ΡΡΡΠ°Π½Π°Π²Π»ΠΈΠ²Π°Π΅ΡΡΡ ΠΏΠΎ Π΄Π²Π° ΡΠ°ΡΡΠ½Π°.
ΠΠΎΠ»Π΅Π½ΡΠ°ΡΡΠΉ Π²Π°Π» (ΡΠΈΡ. 2.8) ΠΈΠ·Π³ΠΎΡΠΎΠ²Π»Π΅Π½ ΠΈΠ· Π²ΡΡΠΎΠΊΠΎΡΠ³Π»Π΅ΡΠΎΠ΄ΠΈΡΡΠΎΠΉ ΡΡΠ°Π»ΠΈ ΠΌΠ΅ΡΠΎΠ΄ΠΎΠΌ Π³ΠΎΡΡΡΠ΅ΠΉ ΡΡΠ°ΠΌΠΏΠΎΠ²ΠΊΠΈ ΠΈ ΡΠΏΡΠΎΡΠ½Π΅Π½ Π°Π·ΠΎΡΠΈΡΠΎΠ²Π°Π½ΠΈΠ΅ΠΌ ΠΈ Π·Π°ΠΊΠ°Π»ΠΊΠΎΠΉ ΡΠΎΠΊΠ°ΠΌΠΈ Π²ΡΡΠΎΠΊΠΎΠΉ ΡΠ°ΡΡΠΎΡΡ ΡΠ°ΡΡΠ½Π½ΡΡ ΠΈ ΠΊΠΎΡΠ΅Π½Π½ΡΡ ΡΠ΅Π΅ΠΊ. ΠΠ½ ΠΈΠΌΠ΅Π΅Ρ ΠΏΡΡΡ ΠΊΠΎΡΠ΅Π½Π½ΡΡ ΠΎΠΏΠΎΡ ΠΈ ΡΠ΅ΡΡΡΠ΅ ΡΠ°ΡΡΠ½Π½ΡΠ΅ ΡΠ΅ΠΉΠΊΠΈ, ΠΊΠΎΡΠΎΡΡΠ΅ ΡΠ²ΡΠ·Π°Π½Ρ ΠΌΠ΅ΠΆΠ΄Ρ ΡΠΎΠ±ΠΎΠΉ ΡΠ΅ΠΊΠ°ΠΌΠΈ. Π ΡΠ°ΡΡΠ½Π½ΡΡ ΡΠ΅ΠΉΠΊΠ°Ρ Π²Π°Π»Π° Π²ΡΠΏΠΎΠ»Π½Π΅Π½Ρ ΠΏΠΎΠ»ΠΎΡΡΠΈ, Π·Π°ΠΊΡΡΡΡΠ΅ Π·Π°Π³Π»ΡΡΠΊΠ°ΠΌΠΈ. Π ΠΏΠΎΠ»ΠΎΡΡΡΡ ΠΌΠ°ΡΠ»ΠΎ ΠΏΠΎΠ΄Π²Π΅ΡΠ³Π°Π΅ΡΡΡ Π΄ΠΎΠΏΠΎΠ»Π½ΠΈΡΠ΅Π»ΡΠ½ΠΎΠΉ ΡΠ΅Π½ΡΡΠΎΠ±Π΅ΠΆΠ½ΠΎΠΉ ΠΎΡΠΈΡΡΠΊΠ΅. ΠΠΎΠ»ΠΎΡΡΠΈ ΡΠ°ΡΡΠ½Π½ΡΡ ΡΠ΅Π΅ΠΊ ΡΠΎΠΎΠ±ΡΠ°ΡΡΡΡ Π½Π°ΠΊΠ»ΠΎΠ½Π½ΡΠΌΠΈ ΠΎΡΠ²Π΅ΡΡΡΠΈΡΠΌΠΈ, ΠΏΡΠΎΡΠ²Π΅ΡΠ»Π΅Π½Π½ΡΠΌΠΈ Π² ΡΠ΅ΠΊΠ°Ρ Π²Π°Π»Π°, Ρ ΠΏΠΎΠΏΠ΅ΡΠ΅ΡΠ½ΡΠΌΠΈ ΠΊΠ°Π½Π°Π»Π°ΠΌΠΈ Π² ΠΊΠΎΡΠ΅Π½Π½ΡΡ ΡΠ΅ΠΉΠΊΠ°Ρ .
ΠΠ° ΡΠ΅ΠΊΠ°Ρ , Π½ΠΎΡΠΊΠ΅ ΠΈ Ρ Π²ΠΎΡΡΠΎΠ²ΠΈΠΊΠ΅ ΠΊΠΎΠ»Π΅Π½ΡΠ°ΡΠΎΠ³ΠΎ Π²Π°Π»Π° ΠΈΠΌΠ΅ΡΡΡΡ ΠΏΡΠΎΡΠΈΠ²ΠΎΠ²Π΅ΡΡ ΡΠΈΡΡΠ΅ΠΌΡ ΡΡΠ°Π²Π½ΠΎΠ²Π΅ΡΠΈΠ²Π°Π½ΠΈΡ: Π½Π° ΡΠ΅ΠΊΠ°Ρ ΠΎΠ½ΠΈ Π²ΡΠΏΠΎΠ»Π½Π΅Π½Ρ ΠΊΠ°ΠΊ ΠΎΠ΄Π½ΠΎ ΡΠ΅Π»ΠΎΠ΅ Ρ ΠΊΠΎΠ»Π΅Π½ΡΠ°ΡΡΠΌ Π²Π°Π»ΠΎΠΌ, Π½Π° Π½ΠΎΡΠΊΠ΅ ΠΈ Ρ Π²ΠΎΡΡΠΎΠ²ΠΈΠΊΠ΅ Π½Π°ΠΏΡΠ΅ΡΡΠΎΠ²Π°Π½Ρ ΠΏΡΠΈ ΡΠ±ΠΎΡΠΊΠ΅ ΠΈ ΡΠΈΠΊΡΠΈΡΡΡΡΡΡ ΡΠ΅Π³ΠΌΠ΅Π½ΡΠ½ΠΎΠΉ ΡΠΏΠΎΠ½ΠΊΠΎΠΉ.
ΠΠ° Π½ΠΎΡΠΊΠ΅ ΠΊΠΎΠ»Π΅Π½ΡΠ°ΡΠΎΠ³ΠΎ Π²Π°Π»Π° ΡΡΡΠ°Π½ΠΎΠ²Π»Π΅Π½Π° Π²Π΅Π΄ΡΡΠ°Ρ ΡΠ΅ΡΡΠ΅ΡΠ½Ρ ΠΏΡΠΈΠ²ΠΎΠ΄Π° ΠΌΠ°ΡΠ»ΡΠ½ΠΎΠ³ΠΎ Π½Π°ΡΠΎΡΠ°, Π½Π° Ρ Π²ΠΎΡΡΠΎΠ²ΠΈΠΊΠ΅ β ΡΠ°ΡΠΏΡΠ΅Π΄Π΅Π»ΠΈΡΠ΅Π»ΡΠ½Π°Ρ ΡΠ΅ΡΡΠ΅ΡΠ½Ρ Π² ΡΠ±ΠΎΡΠ΅ Ρ ΠΌΠ°ΡΠ»ΠΎΠΎΡΡΠ°ΠΆΠ°ΡΠ΅Π»Π΅ΠΌ. Π ΡΠΎΡΡΠ΅Π²ΠΎΠΉ ΡΠ°ΡΡΠΈ Π½ΠΎΡΠΊΠ° ΠΊΠΎΠ»Π΅Π½ΡΠ°ΡΠΎΠ³ΠΎ Π²Π°Π»Π° ΠΈΠΌΠ΅Π΅ΡΡΡ ΠΎΡΠ²Π΅ΡΡΡΠΈΠ΅ Π΄Π»Ρ ΡΡΡΠ°Π½ΠΎΠ²ΠΊΠΈ ΠΏΠΎΠ»ΡΠΌΡΡΡΡ ΠΎΡΠ±ΠΎΡΠ° ΠΌΠΎΡΠ½ΠΎΡΡΠΈ, Π² ΡΠΎΡΡΠ΅Π²ΠΎΠΉ ΡΠ°ΡΡΠΈ Ρ Π²ΠΎΡΡΠΎΠ²ΠΈΠΊΠ° β Π΄Π²Π° ΠΎΡΠ²Π΅ΡΡΡΠΈΡ Π΄Π»Ρ Π·Π°ΠΏΡΠ΅ΡΡΠΎΠ²ΠΊΠΈ ΡΡΠΈΡΡΠΎΠ² ΡΠΈΠΊΡΠ°ΡΠΈΠΈ ΠΌΠ°Ρ ΠΎΠ²ΠΈΠΊΠ°, ΠΎΡΠ΅Π²ΠΎΠ΅ ΠΎΡΠ²Π΅ΡΡΡΠΈΠ΅ Π΄Π»Ρ ΠΎΠΏΠΎΡΠ½ΠΎΠ³ΠΎ ΠΏΠΎΠ΄ΡΠΈΠΏΠ½ΠΈΠΊΠ° ΠΏΠ΅ΡΠ²ΠΈΡΠ½ΠΎΠ³ΠΎ Π²Π°Π»Π° ΠΊΠΎΡΠΎΠ±ΠΊΠΈ ΠΏΠ΅ΡΠ΅Π΄Π°Ρ ΠΈ ΡΠ΅Π·ΡΠ±ΠΎΠ²ΡΠ΅ ΠΎΡΠ²Π΅ΡΡΡΠΈΡ Π΄Π»Ρ Π±ΠΎΠ»ΡΠΎΠ² ΠΊΡΠ΅ΠΏΠ»Π΅Π½ΠΈΡ ΠΌΠ°Ρ ΠΎΠ²ΠΈΠΊΠ°.
Π ΠΈΡ. 2.8. ΠΠΎΠ»Π΅Π½ΡΠ°ΡΡΠΉ Π²Π°Π»:
1 β ΠΏΠΎΠ»ΡΠΌΡΡΡΠ° ΠΎΡΠ±ΠΎΡΠ° ΠΌΠΎΡΠ½ΠΎΡΡΠΈ; 2β ΡΡΠΎΠΏΠΎΡΠ½Π°Ρ ΡΠ°ΠΉΠ±Π° Π½ΠΎΡΠΊΠ° ΠΊΠΎΠ»Π΅Π½ΡΠ°ΡΠΎΠ³ΠΎ Π²Π°Π»Π°: 3 β ΠΏΠ΅ΡΠ΅Π΄Π½ΠΈΠΉ ΠΏΡΠΎΡΠΈΠ²ΠΎΠ²Π΅Ρ; 4 β Π²Π΅Π΄ΡΡΡΡ ΡΠ΅ΡΡΠ΅ΡΠ½Ρ ΠΏΡΠΈΠ²ΠΎΠ΄Π° ΠΌΠ°ΡΠ»ΡΠ½ΠΎΠ³ΠΎ Π½Π°ΡΠΎΡΠ°; 5 β Π·Π°Π³Π»ΡΡΠΊΠ° ΠΏΠΎΠ»ΠΎΡΡΠΈ ΡΠ°ΡΡΠ½Π½ΠΎΠΉ ΡΠ΅ΠΉΠΊΠΈ; Π± β Π·Π°Π΄Π½ΠΈΠΉ ΠΌΠ°ΡΠ»ΠΎΠΎΡΡΠ°ΠΆΠ°ΡΠ΅Π»Ρ; 7 β ΡΠ°ΡΠΏΡΠ΅Π΄Π΅Π»ΠΈΡΠ΅Π»ΡΠ½Π°Ρ ΡΠ΅ΡΡΠ΅ΡΠ½Ρ: 8 β Π·Π°Π΄Π½ΠΈΠΉ ΠΏΡΠΎΡΠΈΠ²ΠΎΠ²Π΅Ρ; 9 β ΠΏΠΎΠ»ΡΠΊΠΎΠ»ΡΡΠ° ΡΠΏΠΎΡΠ½ΠΎΠ³ΠΎ ΠΏΠΎΠ΄ΡΠΈΠΏΠ½ΠΈΠΊΠ° ΠΊΠΎΠ»Π΅Π½ΡΠ°ΡΠΎΠ³ΠΎ Π²Π°Π»Π°β, 10 β ΠΊΡΡΡΠΊΠ° ΠΊΠΎΡΠ΅Π½Π½ΠΎΠ³ΠΎ ΠΏΠΎΠ΄ΡΠΈΠΏΠ½ΠΈΠΊΠ° ΠΊΠΎΠ»Π΅Π½ΡΠ°ΡΠΎΠ³ΠΎ Π²Π°Π»Π°; 11 β Π²ΠΊΠ»Π°Π΄ΡΡ ΠΊΠΎΡΠ΅Π½Π½ΠΎΠ³ΠΎ ΠΏΠΎΠ΄ΡΠΈΠΏΠ½ΠΈΠΊΠ° ΠΊΠΎΠ»Π΅Π½ΡΠ°ΡΠΎΠ³ΠΎ Π²Π°Π»Π°
ΠΡ ΠΎΡΠ΅Π²ΡΡ ΡΠΌΠ΅ΡΠ΅Π½ΠΈΠΉ Π²Π°Π» ΡΠΈΠΊΡΠΈΡΡΠ΅ΡΡΡ ΡΠ΅ΡΡΡΡΠΌΡ ΡΠΏΠΎΡΠ½ΡΠΌΠΈ ΡΡΠ°-Π»Π΅Π°Π»ΡΠΌΠΈΠ½ΠΈΠ΅Π²ΡΠΌΠΈ ΠΏΠΎΠ»ΡΠΊΠΎΠ»ΡΡΠ°ΠΌΠΈ, ΡΡΡΠ°Π½ΠΎΠ²Π»Π΅Π½Π½ΡΠΌΠΈ Π² Π²ΡΡΠΎΡΠΊΠ°Ρ Π±Π»ΠΎΠΊΠ° ΠΈ ΠΊΡΡΡΠΊΠΈ Π·Π°Π΄Π½Π΅ΠΉ ΠΊΠΎΡΠ΅Π½Π½ΠΎΠΉ ΠΎΠΏΠΎΡΡ.
Π£ΠΏΠ»ΠΎΡΠ½Π΅Π½ΠΈΠ΅ ΠΊΠΎΠ»Π΅Π½ΡΠ°ΡΠΎΠ³ΠΎ Π²Π°Π»Π° ΠΎΡΡΡΠ΅ΡΡΠ²Π»ΡΠ΅ΡΡΡ ΡΠ°ΠΌΠΎΠΏΠΎΠ΄ΠΆΠΈΠΌΠ½ΡΠΌ ΡΠ°Π»ΡΠ½ΠΈΠΊΠΎΠΌ, Π·Π°ΠΏΡΠ΅ΡΡΠΎΠ²Π°Π½Π½ΡΠΌ Π² ΠΊΠ°ΡΡΠ΅Ρ ΠΌΠ°Ρ ΠΎΠ²ΠΈΠΊΠ°, ΠΈ ΠΌΠ°ΡΠ»ΠΎΠΎΡΡΠ°ΠΆΠ°ΡΠ΅Π»Π΅ΠΌ.
ΠΠΊΠ»Π°Π΄ΡΡΠΈ ΠΊΠΎΡΠ΅Π½Π½ΡΡ ΠΈ ΡΠ°ΡΡΠ½Π½ΡΡ ΠΏΠΎΠ΄ΡΠΈΠΏΠ½ΠΈΠΊΠΎΠ² ΠΊΠΎΠ»Π΅Π½ΡΠ°ΡΠΎΠ³ΠΎ Π²Π°Π»Π° ΠΈΠ·Π³ΠΎΡΠΎΠ²Π»Π΅Π½Ρ ΠΈΠ· ΡΡΠ°Π»ΡΠ½ΠΎΠΉ Π»Π΅Π½ΡΡ, ΠΏΠΎΠΊΡΡΡΠΎΠΉ ΡΠ»ΠΎΠ΅ΠΌ ΡΠ²ΠΈΠ½ΡΠΎΠ²ΠΈΡΡΠΎΠΉ Π±ΡΠΎΠ½Π·Ρ ΠΈ ΡΠΎΠ½ΠΊΠΈΠΌ ΡΠ»ΠΎΠ΅ΠΌ ΡΠ²ΠΈΠ½ΡΠΎΠ²ΠΈΡΡΠΎΠ³ΠΎ ΡΠΏΠ»Π°Π²Π°. ΠΠ΅ΡΡ Π½ΠΈΠ΅ ΠΈ Π½ΠΈΠΆΠ½ΠΈΠ΅ Π²ΠΊΠ»Π°Π΄ΡΡΠΈ ΠΊΠΎΡΠ΅Π½Π½ΡΡ ΠΏΠΎΠ΄ΡΠΈΠΏΠ½ΠΈΠΊΠΎΠ² ΠΊΠΎΠ»Π΅Π½ΡΠ°ΡΠΎΠ³ΠΎ Π²Π°Π»Π° Π½Π΅Π²Π·Π°ΠΈΠΌΠΎΠ·Π°ΠΌΠ΅Π½ΡΠ΅ΠΌΡ. ΠΠ΅ΡΡ Π½ΠΈΠ΅ Π²ΠΊΠ»Π°Π΄ΡΡΠΈ ΠΊΠΎΡΠ΅Π½Π½ΡΡ ΠΏΠΎΠ΄ΡΠΈΠΏΠ½ΠΈΠΊΠΎΠ² ΠΎΡΠ»ΠΈΡΠ°ΡΡΡΡ ΠΎΡ Π½ΠΈΠΆΠ½ΠΈΡ Π½Π°Π»ΠΈΡΠΈΠ΅ΠΌ ΠΎΡΠ²Π΅ΡΡΡΠΈΠΉ Π΄Π»Ρ ΠΏΠΎΠ΄Π²ΠΎΠ΄Π° ΠΌΠ°ΡΠ»Π° ΠΈ ΠΊΠΎΠ»ΡΡΠ΅Π²ΠΎΠΉ ΠΊΠ°Π½Π°Π²ΠΊΠΈ Π΄Π»Ρ Π΅Π³ΠΎ ΡΠ°ΡΠΏΡΠ΅Π΄Π΅Π»Π΅Π½ΠΈΡ. ΠΠ΅ΡΡ Π½ΠΈΠ΅ ΠΈ Π½ΠΈΠΆΠ½ΠΈΠ΅ Π²ΠΊΠ»Π°Π΄ΡΡΠΈ ΡΠ°ΡΡΠ½Π½ΡΡ ΠΏΠΎΠ΄ΡΠΈΠΏΠ½ΠΈΠΊΠΎΠ² ΠΊΠΎΠ»Π΅Π½ΡΠ°ΡΠΎΠ³ΠΎ Π²Π°Π»Π° ΠΈ Π½ΠΈΠΆΠ½Π΅ΠΉ Π³ΠΎΠ»ΠΎΠ²ΠΊΠΈ ΡΠ°ΡΡΠ½Π° Π²Π·Π°ΠΈΠΌΠΎΠ·Π°ΠΌΠ΅Π½ΡΠ΅ΠΌΡ.
ΠΠ»Ρ ΠΏΡΠ΅Π΄ΠΎΡΠ²ΡΠ°ΡΠ΅Π½ΠΈΡ ΠΎΡ ΠΏΡΠΎΠ²ΠΎΡΠ°ΡΠΈΠ²Π°Π½ΠΈΡ ΠΈ ΠΎΡΠ΅Π²ΡΡ ΠΏΠ΅ΡΠ΅ΠΌΠ΅ΡΠ΅Π½ΠΈΠΉ Π²ΠΊΠ»Π°Π΄ΡΡΠ΅ΠΉ Π² Π³Π½Π΅Π·Π΄Π°Ρ Π½Π° ΠΊΡΠ°ΡΡ ΠΏΠΎΡΡΠ΅Π»Π΅ΠΉ Π²ΠΊΠ»Π°Π΄ΡΡΠ΅ΠΉ Π²ΡΠ΄Π°Π²Π»Π΅Π½Ρ ΠΊΡΠΎΠΌΠΊΠΈ, ΠΊΠΎΡΠΎΡΡΠ΅ Π²Ρ ΠΎΠ΄ΡΡ Π² ΡΠΎΠΎΡΠ²Π΅ΡΡΡΠ²ΡΡΡΠΈΠ΅ ΠΏΠ°Π·Ρ, Π²ΡΠΏΠΎΠ»Π½Π΅Π½Π½ΡΠ΅ Π² ΠΏΠΎΡΡΠ΅Π»ΡΡ Π±Π»ΠΎΠΊΠ° ΠΈ ΠΊΡΡΡΠΊΠ°Ρ ΠΊΠΎΡΠ΅Π½Π½ΡΡ ΠΈ ΡΠ°ΡΡΠ½Π½ΡΡ ΠΏΠΎΠ΄ΡΠΈΠΏΠ½ΠΈΠΊΠΎΠ².
Π ΠΈΡ. 2.9. ΠΠ°Ρ
ΠΎΠ²ΠΈΠΈ:
1 β Π°ΡΠ±ΡΠ°ΡΡΠΉ Π²Π΅Π½Π΅Ρ ΠΌΠ°Ρ
ΠΎΠ²ΠΈΠΊΠ°; 2 β ΡΠΈΠΊΡΠ°ΡΠΎΡ ΠΌΠ°Ρ
ΠΎΠ²ΠΈΠΊΠ° Π² ΡΠ±ΠΎΡΠ΅; 3β Π±ΠΎΠ»Ρ ΠΊΡΠ΅ΠΏΠ»Π΅Π½ΠΈΡ ΠΌΠ°Ρ
ΠΎΠ²ΠΈΠΊΠ°; 4 β ΡΠΏΠΎΡΠ½ΠΎΠ΅ ΠΏΡΡΠΆΠΈΠ½Π½ΠΎΠ΅ ΠΊΠΎΠ»ΡΡΠΎ; 5 β ΡΡΡΠ°Π½ΠΎΠ²ΠΎΡΠ½Π°Ρ Π²ΡΡΠ»ΠΊΠ° ΠΌΠ°Ρ
ΠΎΠ²ΠΈΠΊΠ°; 6β ΠΌΠ°Π½ΠΆΠ΅ΡΠ° ΠΏΠ΅ΡΠ²ΠΈΡΠ½ΠΎΠ³ΠΎ Π²Π°Π»Π°
ΠΠ°Ρ ΠΎΠ²ΠΈΠΊ (ΡΠΈΡ. 2.9) ΠΎΡΠ»ΠΈΡ ΠΈΠ· ΡΠΏΠ΅ΡΠΈΠ°Π»ΡΠ½ΠΎΠ³ΠΎ ΡΠ΅ΡΠΎΠ³ΠΎ ΡΡΠ³ΡΠ½Π°. ΠΠ½ ΠΊΡΠ΅ΠΏΠΈΡΡΡ ΠΊ Π·Π°Π΄Π½Π΅ΠΌΡ ΡΠΎΡΡΡ ΠΊΠΎΠ»Π΅Π½ΡΠ°ΡΠΎΠ³ΠΎ Π²Π°Π»Π° Π²ΠΎΡΠ΅ΠΌΡΡ Π±ΠΎΠ»ΡΠ°ΠΌΠΈ ΠΈΠ· Π»Π΅Π³ΠΈΡΠΎΠ²Π°Π½Π½ΠΎΠΉ ΡΡΠ°Π»ΠΈ. Π’ΠΎΡΠ½Π°Ρ ΡΠΈΠΊΡΠ°ΡΠΈΡ ΠΌΠ°Ρ ΠΎΠ²ΠΈΠΊΠ° Π½Π° ΠΊΠΎΠ»Π΅Π½ΡΠ°ΡΠΎΠΌ Π²Π°Π»Ρ Π΄ΠΎΡΡΠΈΠ³Π°Π΅ΡΡΡ ΠΏΡΠΈ ΠΏΠΎΠΌΠΎΡΠΈ Π΄Π²ΡΡ ΡΡΡΠ°Π½ΠΎΠ²ΠΎΡΠ½ΡΡ ΡΡΠΈΡΡΠΎΠ², Π·Π°ΠΏΡΠ΅ΡΡΠΎΠ²Π°Π½Π½ΡΡ Π² ΡΠΎΡΠ΅Ρ ΠΊΠΎΠ»Π΅Π½ΡΠ°ΡΠΎΠ³ΠΎ Π²Π°Π»Π°. ΠΠ° ΠΎΠ±ΡΠ°Π±ΠΎΡΠ°Π½Π½ΡΡ ΡΠΈΠ»ΠΈΠ½Π΄ΡΠΈΡΠ΅ΡΠΊΡΡ ΠΏΠΎΠ²Π΅ΡΡ Π½ΠΎΡΡΡ ΠΌΠ°Ρ ΠΎΠ²ΠΈΠΊΠ° Π½Π°ΠΏΡΠ΅ΡΡΠΎΠ²Π°Π½ Π·ΡΠ±ΡΠ°ΡΡΠΉ Π²Π΅Π½Π΅Ρ, ΠΏΡΠ΅Π΄Π½Π°Π·Π½Π°ΡΠ΅Π½Π½ΡΠΉ Π΄Π»Ρ ΡΠΎΠ΅Π΄ΠΈΠ½Π΅Π½ΠΈΡ Ρ ΡΠ΅ΡΡΠ΅ΡΠ½Π΅ΠΉ Π²Π°Π»Π° ΡΡΠ°ΡΡΠ΅ΡΠ° ΠΏΡΠΈ ΠΏΡΡΠΊΠ΅ Π΄Π²ΠΈΠ³Π°ΡΠ΅Π»Ρ. ΠΠ° Π·Π°Π΄Π½Π΅ΠΌ ΡΠΎΡΡΠ΅ ΠΌΠ°Ρ ΠΎΠ²ΠΈΠΊΠ° ΡΡΡΠ°Π½Π°Π²Π»ΠΈΠ²Π°Π΅ΡΡΡ ΡΡΠ΅ΠΏΠ»Π΅Π½ΠΈΠ΅. ΠΠ»Ρ ΠΏΡΠΎΠ²Π΅Π΄Π΅Π½ΠΈΡ ΡΠ΅Π³ΡΠ»ΠΈΡΠΎΠ²ΠΎΠΊ Π΄Π²ΠΈΠ³Π°ΡΠ΅Π»Ρ Π½Π° ΠΌΠ°Ρ ΠΎΠ²ΠΈΠΊΠ΅ ΠΈΠΌΠ΅ΡΡΡΡ ΠΏΠ°Π· ΠΏΠΎΠ΄ ΡΠΈΠΊΡΠ°ΡΠΎΡ ΠΌΠ°Ρ ΠΎΠ²ΠΈΠΊΠ° ΠΈ ΠΎΡΠ²Π΅ΡΡΡΠΈΡ Π΄Π»Ρ ΠΏΡΠΎΠ²ΠΎΡΠ°ΡΠΈΠ²Π°Π½ΠΈΡ ΠΊΠΎΠ»Π΅Π½ΡΠ°ΡΠΎΠ³ΠΎ Π²Π°Π»Π° Π»ΠΎΠΌΠΈΠΊΠΎΠΌ.
Π Π΅ΠΊΠ»Π°ΠΌΠ°:
Π§ΠΈΡΠ°ΡΡ Π΄Π°Π»Π΅Π΅: Π£ΡΡΡΠΎΠΉΡΡΠ²ΠΎ ΠΌΠ΅Ρ Π°Π½ΠΈΠ·ΠΌΠ° Π³Π°Π·ΠΎΡΠ°ΡΠΏΡΠ΅Π΄Π΅Π»Π΅Π½ΠΈΡ ΠΠ°ΠΌΠΠ-5320, ΠΠ°ΠΌΠΠ-4310 ΠΈ Π£ΡΠ°Π»-4320
ΠΠ°ΡΠ΅Π³ΠΎΡΠΈΡ: β ΠΠ²ΡΠΎΠΌΠΎΠ±ΠΈΠ»ΠΈ ΠΠ°ΠΌΠ°Π· Π£ΡΠ°Π»
ΠΠ»Π°Π²Π½Π°Ρ β Π‘ΠΏΡΠ°Π²ΠΎΡΠ½ΠΈΠΊ β Π‘ΡΠ°ΡΡΠΈ β Π€ΠΎΡΡΠΌ
stroy-technics.ru
ΡΠ΅Ρ Π½ΠΈΡΠ΅ΡΠΊΠΈΠ΅ Ρ Π°ΡΠ°ΠΊΡΠ΅ΡΠΈΡΡΠΈΠΊΠΈ, Π΄Π²ΠΈΠ³Π°ΡΠ΅Π»Ρ, ΡΡ Π΅ΠΌΠ° :: SYL.ru
ΠΡΠΎΡ Π³ΡΡΠ·ΠΎΠ²ΠΈΠΊ Π½Π°ΡΠ°Π»ΠΈ ΠΏΡΠΎΠΈΠ·Π²ΠΎΠ΄ΠΈΡΡ Π΅ΡΠ΅ Π² 80-Ρ Π³ΠΎΠ΄Π°Ρ ΠΏΡΠΎΡΠ»ΠΎΠ³ΠΎ Π²Π΅ΠΊΠ°. ΠΠ΄Π½Π°ΠΊΠΎ ΠΎΠ½ Π΄ΠΎ ΡΠΈΡ ΠΏΠΎΡ ΠΏΠΎΠ»ΡΠ·ΡΠ΅ΡΡΡ ΠΏΠΎΠΏΡΠ»ΡΡΠ½ΠΎΡΡΡΡ Ρ ΡΡΡΠΆΠ΅Π½ΠΈΠΊΠΎΠ² ΡΠ΅Π»ΡΡΠΊΠΎΠ³ΠΎ Ρ ΠΎΠ·ΡΠΉΡΡΠ²Π°. Π ΡΡΠ»ΠΎΠ²ΠΈΡΡ ΡΠ΅Π»ΡΡΠΊΠΎΡ ΠΎΠ·ΡΠΉΡΡΠ²Π΅Π½Π½ΠΎΠΉ ΠΏΡΠΎΠΌΡΡΠ»Π΅Π½Π½ΠΎΡΡΠΈ ΡΡΠ΅Π±ΠΎΠ²Π°Π»Π°ΡΡ Π±ΠΎΠ»ΡΡΠ°Ρ Π²ΠΌΠ΅ΡΡΠΈΠΌΠΎΡΡΡ ΠΈ Ρ ΠΎΡΠΎΡΠ°Ρ Π³ΡΡΠ·ΠΎΠΏΠΎΠ΄ΡΠ΅ΠΌΠ½ΠΎΡΡΡ, ΠΊ ΡΠΎΠΌΡ ΠΆΠ΅ Π΄Π»Ρ Π½ΡΠΆΠ΄ ΡΠ΅Π»Π° Π½Π΅ΠΎΠ±Ρ ΠΎΠ΄ΠΈΠΌ Π±ΡΠ» Π°Π²ΡΠΎΠΌΠΎΠ±ΠΈΠ»Ρ Ρ Π²ΠΎΠ·ΠΌΠΎΠΆΠ½ΠΎΡΡΡΡ ΡΠ°Π·Π³ΡΡΠ·ΠΊΠΈ ΡΡΠ°Π·Ρ Ρ ΡΡΠ΅Ρ ΡΡΠΎΡΠΎΠ½. Π’Π°ΠΊ ΠΈ ΠΏΠΎΡΠ²ΠΈΠ»ΡΡ Π°Π²ΡΠΎΠΌΠΎΠ±ΠΈΠ»Ρ ΠΠ°ΠΌΠΠ-55102.

ΠΠΎΠ΅-ΡΡΠΎ ΠΈΠ· ΠΈΡΡΠΎΡΠΈΠΈ
ΠΠ»Π°ΡΡΠΎΡΠΌΠ° Π³ΡΡΠ·ΠΎΠ²ΠΈΠΊΠ° Π²ΡΠΏΡΡΠΊΠ°Π»Π°ΡΡ Π² ΠΠ°Π±Π΅ΡΠ΅ΠΆΠ½ΡΡ Π§Π΅Π»Π½Π°Ρ . ΠΠ°Π±ΠΈΠ½Π° Π½Π° ΡΠ°ΡΡΠΈ ΡΡΡΠ°Π½Π°Π²Π»ΠΈΠ²Π°Π»Π°ΡΡ ΡΠΆΠ΅ Π² ΠΠ΅ΡΡΠ΅ΠΊΠ°ΠΌΡΠΊΠ΅. Π’Π°ΠΌ ΠΆΠ΅ ΠΌΠΎΠ½ΡΠΈΡΠΎΠ²Π°Π»ΠΈ ΠΈ ΠΊΡΠ·ΠΎΠ² Π΄Π»Ρ ΡΡΠ°Π½ΡΠΏΠΎΡΡΠΈΡΠΎΠ²ΠΊΠΈ Π³ΡΡΠ·ΠΎΠ². ΠΠΎΠ½ΡΡΡΡΠΊΡΠΈΡ ΡΠ°Π·ΡΠ°Π±Π°ΡΡΠ²Π°Π»Π°ΡΡ Π½Π° ΠΡΡΠΈΡΠΈΠ½ΡΠΊΠΎΠΌ ΠΌΠ°ΡΠΈΠ½ΠΎΡΡΡΠΎΠΈΡΠ΅Π»ΡΠ½ΠΎΠΌ Π·Π°Π²ΠΎΠ΄Π΅. ΠΠ΄Π½Π°ΠΊΠΎ ΠΌΠ°ΡΠΈΠ½Π° ΠΏΠΎΠ»ΡΡΠΈΠ»Π°ΡΡ ΠΏΠΎΡ ΠΎΠΆΠ΅ΠΉ Π½Π° Π΄Π΅ΡΡΡΠΈΡΠΎΠ½Π½ΡΡ ΠΌΠΎΠ΄Π΅Π»Ρ 5320. ΠΠ΅ ΠΈΠ·Π³ΠΎΡΠ°Π²Π»ΠΈΠ²Π°Π»ΠΈ Π² 70-Ρ . Π§Π΅ΠΌ ΠΎΡΠ»ΠΈΡΠ°Π΅ΡΡΡ ΠΠ°ΠΌΠΠ-55102? Π Π°Π·Π½ΠΈΡΠ° Π² ΠΊΠ°Π±ΠΈΠ½Π΅, Π³Π΄Π΅ Π½Π΅Ρ ΠΌΠ΅ΡΡΠ° Π΄Π»Ρ ΠΎΡΠ΄ΡΡ Π° Π²ΠΎΠ΄ΠΈΡΠ΅Π»Ρ, ΠΈ Π² ΠΊΡΠ·ΠΎΠ²Π΅ Ρ Π²ΠΎΠ·ΠΌΠΎΠΆΠ½ΠΎΡΡΡΠΌΠΈ ΡΠ°ΠΌΠΎΡΠ²Π°Π»Π°.
Π₯ΠΎΡΡ ΠΈ Π±ΡΠ» Π²ΡΠΏΠΎΠ»Π½Π΅Π½ Π² ΡΠΎΡΠΌΠ°ΡΠ΅ ΡΠ°ΠΌΠΎΡΠ²Π°Π»Π°, Π°Π²ΡΠΎΠΌΠΎΠ±ΠΈΠ»Ρ ΡΠ°ΠΊΠΆΠ΅ ΠΈΡΠΏΠΎΠ»ΡΠ·ΠΎΠ²Π°Π»ΡΡ Π² ΠΊΠ°ΡΠ΅ΡΡΠ²Π΅ ΡΡΠ³Π°ΡΠ° Π΄Π»Ρ Π°Π²ΡΠΎΠΏΠΎΠ΅Π·Π΄ΠΎΠ². ΠΠ°ΠΊ ΠΈ ΠΎΡΡΠ°Π»ΡΠ½ΡΠ΅ ΠΌΠΎΠ΄Π΅Π»ΠΈ ΡΡΠΎΠ³ΠΎ ΠΏΡΠΎΠΈΠ·Π²ΠΎΠ΄ΠΈΡΠ΅Π»Ρ, Π΄Π°Π½Π½ΡΠΉ Π³ΡΡΠ·ΠΎΠ²ΠΈΠΊ ΠΏΡΠ΅Π΄Π½Π°Π·Π½Π°ΡΠ°Π»ΡΡ Π΄Π»Ρ ΡΠ°Π±ΠΎΡΡ Π² ΡΠ°ΠΌΡΡ ΡΠ°Π·Π»ΠΈΡΠ½ΡΡ ΠΊΠ»ΠΈΠΌΠ°ΡΠΈΡΠ΅ΡΠΊΠΈΡ Π·ΠΎΠ½Π°Ρ . ΠΡΠΎ ΠΏΠΎΠ·Π²ΠΎΠ»ΠΈΠ»ΠΎ ΠΌΠ°ΡΠΈΠ½Π°ΠΌ Π²ΡΠΉΡΠΈ Π½Π° ΠΎΡΠΎΠ±ΡΠΉ ΡΡΠΎΠ²Π΅Π½Ρ, ΠΊΠΎΠ½ΠΊΡΡΠ΅Π½ΡΠΈΠΈ Ρ Π½ΠΈΡ ΠΏΡΠ°ΠΊΡΠΈΡΠ΅ΡΠΊΠΈ Π½Π΅ Π±ΡΠ»ΠΎ.
ΠΡΠ½ΠΎΠ²Π½ΠΎΠ΅ ΠΏΡΠ΅Π΄Π½Π°Π·Π½Π°ΡΠ΅Π½ΠΈΠ΅ ΠΌΠΎΠ΄Π΅Π»ΠΈ β ΠΏΠ΅ΡΠ΅Π²ΠΎΠ·ΠΊΠ° ΡΠ°Π·Π»ΠΈΡΠ½ΡΡ ΡΡΠΏΡΡΠΈΡ Π³ΡΡΠ·ΠΎΠ² ΡΡΡΠΎΠΈΡΠ΅Π»ΡΠ½ΠΎΠ³ΠΎ, Π° ΡΠ°ΠΊΠΆΠ΅ ΡΠ΅Π»ΡΡ ΠΎΠ·Π½Π°Π·Π½Π°ΡΠ΅Π½ΠΈΡ.

ΠΠ±ΡΠΈΠ΅ Ρ Π°ΡΠ°ΠΊΡΠ΅ΡΠΈΡΡΠΈΠΊΠΈ
ΠΠ»Π°ΡΡΠΎΡΠΌΠ° β ΡΡΠ΅Ρ ΠΎΡΠ½Π°Ρ ΠΊΠΎΠ½ΡΡΡΡΠΊΡΠΈΡ Ρ Π·Π°Π΄Π½ΠΈΠΌ ΠΏΡΠΈΠ²ΠΎΠ΄ΠΎΠΌ. Π’Π°ΠΊΡΡ Π²Π΅ΡΡΠΈΡ ΠΈΡΠΏΠΎΠ»Π½Π΅Π½ΠΈΡ ΠΈΠΌΠ΅Π»ΠΈ Π²ΡΠ΅ Π³ΡΡΠ·ΠΎΠ²ΠΈΠΊΠΈ ΠΠ°ΠΌΠΠ-55102. Π‘Ρ Π΅ΠΌΠ° (ΠΊΠΎΠ»Π΅ΡΠ½Π°Ρ ΡΠΎΡΠΌΡΠ»Π°) ΡΠ°ΡΡΠΈ β 6Γ4.
ΠΡΠ½ΠΎΠ²Π½Π°Ρ Π½Π΅ΡΡΡΠ°Ρ ΡΠ°ΡΡΡ ΠΌΠ°ΡΠΈΠ½Ρ β ΡΡΠΎ Π»Π΅ΡΡΠ½ΠΈΡΠ½Π°Ρ ΠΊΠ»Π΅ΠΏΠ°Π½Π°Ρ ΡΠ°ΠΌΠ°. ΠΠ½Π° ΠΈΠ·Π³ΠΎΡΠ°Π²Π»ΠΈΠ²Π°Π»Π°ΡΡ ΠΈΠ· ΡΠ²Π΅Π»Π»Π΅ΡΠΎΠ². ΠΡΠΎΡΠΈΠ»Ρ ΠΈΠΌΠ΅Π» ΡΠΎΠ»ΡΠΈΠ½Ρ 8 ΠΌΠΌ. ΠΠ½ Π±ΡΠ» ΠΏΡΠΎΠΈΠ·Π²Π΅Π΄Π΅Π½ ΠΈΠ· Π½ΠΈΠ·ΠΊΠΎΠ»Π΅Π³ΠΈΡΠΎΠ²Π°Π½Π½ΠΎΠΉ ΡΡΠ°Π»ΠΈ. ΠΠΎΠ½ΠΆΠ΅ΡΠΎΠ½Ρ ΡΡΡΠ°Π½ΠΎΠ²Π»Π΅Π½Ρ ΠΏΡΠΎΠ΄ΠΎΠ»ΡΠ½ΠΎ. ΠΡ ΡΠΎΠ΅Π΄ΠΈΠ½ΡΠ»ΠΈ ΡΠ΅ΠΌΡ ΡΠ°ΠΊ Π½Π°Π·ΡΠ²Π°Π΅ΠΌΡΡ ΠΏΠΎΠΏΠ΅ΡΠ΅ΡΠΈΠ½. Π‘ΠΏΠ΅ΡΠ΅Π΄ΠΈ ΡΠ°ΠΌΡ ΡΠ°ΡΠΏΠΎΠ»Π°Π³Π°Π»ΠΈΡΡ ΠΊΡΡΠΊΠΈ Π΄Π»Ρ Π±ΡΠΊΡΠΈΡΠΎΠ²ΠΊΠΈ. ΠΠ΄Π΅ΡΡ Π·Π°ΠΊΡΠ΅ΠΏΠ»ΡΠ»ΡΡ ΡΡΠ°Π»ΡΠ½ΠΎΠΉ Π±ΡΡΠ΅Ρ. ΠΠΎΠΏΠ΅ΡΠ΅ΡΠΈΠ½Π° Π² Π·Π°Π΄Π½Π΅ΠΉ ΡΠ°ΡΡΠΈ ΠΎΠ±ΠΎΡΡΠ΄ΠΎΠ²Π°Π½Π° ΡΠΏΠ΅ΡΠΈΠ°Π»ΡΠ½ΠΎΠΉ ΡΡΠ΅ΠΏΠ½ΠΎΠΉ ΡΡΠ³ΠΎΠ²ΠΎΠΉ ΡΠΈΡΡΠ΅ΠΌΠΎΠΉ. ΠΠ½Π° ΠΏΡΠ΅Π΄ΡΡΠ°Π²Π»Π΅Π½Π° Π² Π²ΠΈΠ΄Π΅ Β«ΠΊΡΡΠΊ-ΠΏΠ΅ΡΠ»ΡΒ».
ΠΠ΅ΡΠ΅Π΄Π½ΡΡ ΠΎΡΡ ΠΊΠΎΠ»Π΅Ρ ΠΈΠ·Π³ΠΎΡΠΎΠ²Π»Π΅Π½Π° Π² Π²ΠΈΠ΄Π΅ ΠΈΠ·ΠΎΠ³Π½ΡΡΠΎΠΉ Π±Π°Π»ΠΊΠΈ Π΄Π²ΡΡΠ°Π²ΡΠΎΠ²ΠΎΠ³ΠΎ ΡΠ΅ΡΠ΅Π½ΠΈΡ. ΠΠ½Π° ΠΎΡΠ½Π°ΡΠ°Π»Π°ΡΡ ΡΠΈΠ»ΠΈΠ½Π΄ΡΠΈΡΠ΅ΡΠΊΠΈΠΌΠΈ ΡΠΊΠ²ΠΎΡΠ½ΡΠΌΠΈ ΠΈ ΠΏΠΎΠ²ΠΎΡΠΎΡΠ½ΡΠΌΠΈ ΠΊΡΠ»Π°ΡΠΊΠ°ΠΌΠΈ. ΠΠΎΡΡΡ ΡΠ·Π°Π΄ΠΈ ΠΈΠ·Π³ΠΎΡΠ°Π²Π»ΠΈΠ²Π°Π»ΠΈΡΡ ΠΈΠ· ΡΠ΅Π»ΡΠ½ΡΡ Π±Π°Π»ΠΎΠΊ Ρ Π²Π°ΡΠ΅Π½ΡΠΌΠΈ ΠΊΠ°ΡΡΠ΅ΡΠ°ΠΌΠΈ. Π‘Π·Π°Π΄ΠΈ Π΄Π°Π½Π½ΡΠ΅ ΡΠ»Π΅ΠΌΠ΅Π½ΡΡ ΠΈΠΌΠ΅ΡΡ ΠΊΡΠ΅ΠΏΠ»Π΅Π½ΠΈΡ Π΄Π»Ρ ΡΠ°Π·Π»ΠΈΡΠ½ΠΎΠ³ΠΎ ΠΎΠ±ΠΎΡΡΠ΄ΠΎΠ²Π°Π½ΠΈΡ. Π’ΡΠ΄Π° ΠΊΡΠ΅ΠΏΡΡΡΡ ΡΠ΅Π΄ΡΠΊΡΠΎΡΡ, Π° ΡΠ°ΠΊΠΆΠ΅ ΡΠΎΡΠΌΠΎΠ·Π½ΡΠ΅ ΡΡΠΏΠΏΠΎΡΡΡ, ΡΠ°ΠΏΡΡ ΠΊΠΎΠ»Π΅ΡΠ½ΡΡ ΡΡΡΠΏΠΈΡ, ΠΊΡΠΎΠ½ΡΡΠ΅ΠΉΠ½Ρ Π΄Π»Ρ ΠΊΡΠ΅ΠΏΠ»Π΅Π½ΠΈΡ ΡΡΠ°Π½Π³. ΠΡΠΎΠΌΠ΅ ΡΡΠΎΠ³ΠΎ Π½Π° Π±Π°Π»ΠΊΠ°Ρ Π·Π°ΠΊΡΠ΅ΠΏΠ»ΡΠ»ΠΈΡΡ ΠΎΠΏΠΎΡΡ Π΄Π»Ρ ΡΠ΅ΡΡΠΎΡ. ΠΠΎΡ ΡΠ°ΠΊΠ°Ρ Ρ Π³ΡΡΠ·ΠΎΠ²ΠΈΠΊΠ° Ρ Π°ΡΠ°ΠΊΡΠ΅ΡΠΈΡΡΠΈΠΊΠ°.
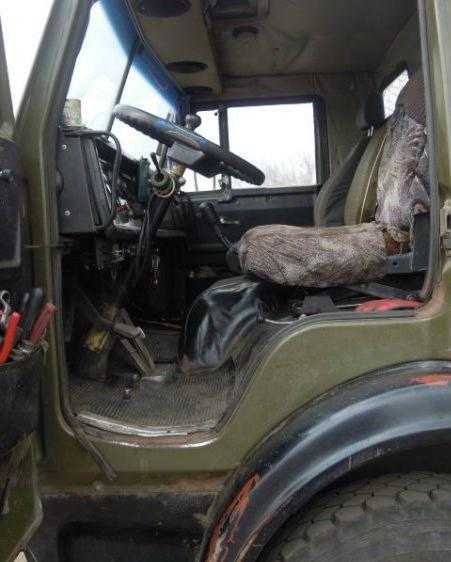
ΠΠ°ΠΌΠΠ-55102: ΠΊΠΎΠ½ΡΡΡΡΠΊΡΠΈΡ ΠΏΠΎΠ΄Π²Π΅ΡΠΊΠΈ
Π‘ΠΏΠ΅ΡΠ΅Π΄ΠΈ ΠΌΠΎΠ΄Π΅Π»Ρ ΠΎΡΠ½Π°ΡΠ°Π΅ΡΡΡ Π·Π°Π²ΠΈΡΠΈΠΌΠΎΠΉ ΠΏΠΎΠ΄Π²Π΅ΡΠΊΠΎΠΉ. ΠΠΎΠ½ΡΡΡΡΠΊΡΠΈΡ ΠΏΡΠ΅Π΄ΡΡΠ°Π²Π»ΡΠ΅Ρ ΡΠΎΠ±ΠΎΠΉ Π΄ΡΠ±Π»ΠΈΡΠΎΠ²Π°Π½Π½ΡΠ΅ Π»ΠΈΡΡΠΎΠ²ΡΠ΅ ΡΠ΅ΡΡΠΎΡΡ Ρ ΠΏΡΠΎΡΠΈΠ»Π΅ΠΌ ΠΏΠΎΠ»ΡΡΠ»Π»ΠΈΠΏΡΠ°. ΠΠ°ΡΠ΅ΠΌ ΡΠ΅ΡΡΠΎΡΡ ΡΠΎΠΏΡΡΠ³Π°ΡΡΡΡ Ρ ΡΠ΅Π»Π΅ΡΠΊΠΎΠΏΠΈΡΠ΅ΡΠΊΠΈΠΌΠΈ Π°ΠΌΠΎΡΡΠΈΠ·Π°ΡΠΎΡΠ°ΠΌΠΈ. ΠΠΎΠΏΠΎΠ»Π½ΠΈΡΠ΅Π»ΡΠ½ΠΎ ΠΏΡΠΈΠΌΠ΅Π½ΡΠ»ΠΈ ΡΠΏΠ΅ΡΠΈΠ°Π»ΡΠ½ΡΠ΅ Π±ΡΡΠ΅ΡΡ ΡΠΆΠ°ΡΠΈΡ Π² Π²ΠΈΠ΄Π΅ ΠΏΠΎΠ»ΡΡ ΡΠΈΠ»ΠΈΠ½Π΄ΡΠΎΠ² ΠΈΠ· ΡΠ΅Π·ΠΈΠ½Ρ.
ΠΠΎΠ»Π΅ΡΠ°
ΠΠ°ΠΌΠΠ-55102 ΠΎΡΠ½Π°ΡΠ΅Π½ ΠΊΠΎΠ»Π΅ΡΠ°ΠΌΠΈ Π±Π΅Π· Π΄ΠΈΡΠΊΠΎΠ². ΠΠ½ΠΈ ΠΏΡΠ΅Π΄ΡΡΠ°Π²Π»Π΅Π½Ρ Π² Π²ΠΈΠ΄Π΅ ΠΎΠ±ΠΎΠ΄Π°, Π·Π°ΠΌΠΎΡΠ½ΡΡ ΠΈ Π±ΠΎΡΡΠΎΠ²ΡΡ ΠΊΠΎΠ»Π΅Ρ. ΠΠΎΡΡΠΎΠ²ΠΎΠ΅ ΠΊΠΎΠ»ΡΡΠΎ ΡΠΈΠΊΡΠΈΡΡΠ΅ΡΡΡ Π½Π° ΠΎΠ±ΠΎΠ΄Π΅ ΠΊΠΎΠ»Π΅ΡΠ° ΠΏΡΠΈ ΠΏΠΎΠΌΠΎΡΠΈ Π·Π°ΠΌΠΎΡΠ½ΠΎΠ³ΠΎ ΠΊΠΎΠ»ΡΡΠ°. ΠΠ° ΡΡΡΠΏΠΈΡΠ°Ρ ΠΊΠΎΠ»Π΅ΡΠ° Π½Π°Π΄Π΅ΠΆΠ½ΠΎ Π·Π°ΡΠΈΠΊΡΠΈΡΠΎΠ²Π°Π½Ρ Π³Π°ΠΉΠΊΠ°ΠΌΠΈ ΠΈ ΡΠΏΠΈΠ»ΡΠΊΠ°ΠΌΠΈ.
ΠΠ»Ρ ΡΠΎΠ³ΠΎ ΡΡΠΎΠ±Ρ ΠΏΡΠΎΠ²Π΅ΡΡΠΈ ΠΌΠΎΠ½ΡΠ°ΠΆ ΠΊΠΎΠ»Π΅ΡΠ½ΠΎΠΉ ΠΏΠ°ΡΡ Π½Π° ΡΡΡΠΏΠΈΡΡ, ΠΈΡΠΏΠΎΠ»ΡΠ·ΠΎΠ²Π°Π»ΠΈ ΡΠΏΠ΅ΡΠΈΠ°Π»ΡΠ½ΠΎΠ΅ ΠΏΡΠΎΡΡΠ°Π²ΠΎΡΠ½ΠΎΠ΅ ΠΊΠΎΠ»ΡΡΠΎ. ΠΠ½ΠΎ ΠΎΠ±Π΅ΡΠΏΠ΅ΡΠΈΠ²Π°Π»ΠΎ Π½Π΅ΠΊΠΎΡΠΎΡΠΎΠ΅ ΡΠ°ΡΡΡΠΎΡΠ½ΠΈΠ΅ ΠΌΠ΅ΠΆΠ΄Ρ ΡΠ΅Π·ΠΈΠ½ΠΎΠΉ. ΠΠΎΠΊΡΡΡΠΊΠΈ ΡΠΎΡΡΠΎΡΠ»ΠΈ ΠΈΠ· 12 ΡΠ»ΠΎΠ΅Π². ΠΡΠΎ Π±ΡΠ»ΠΈ ΡΠ°Π΄ΠΈΠ°Π»ΡΠ½ΡΠ΅ ΠΊΠ°ΠΌΠ΅ΡΠ½ΡΠ΅ ΡΠΈΠ½Ρ. Π¨ΠΈΡΠΈΠ½Π° ΡΠΈΠ½Ρ β 260 ΠΌΠΌ.
ΠΠ°Π±ΠΈΠ½Π°

Π£ Π°Π²ΡΠΎΠΌΠΎΠ±ΠΈΠ»Ρ ΡΠ΅Π»ΡΠ½ΠΎΠΌΠ΅ΡΠ°Π»Π»ΠΈΡΠ΅ΡΠΊΠ°Ρ ΠΊΠ°Π±ΠΈΠ½Π°, ΠΏΠΎΡΡΡΠΎΠ΅Π½Π½Π°Ρ Π² Π±Π΅ΡΠΊΠ°ΠΏΠΎΡΠ½ΠΎΠΉ ΠΊΠΎΠΌΠΏΠΎΠ½ΠΎΠ²ΠΊΠ΅. ΠΠ½Π° ΡΠ°ΡΠΏΠΎΠ»Π°Π³Π°Π΅ΡΡΡ Π½Π°Π΄ ΠΌΠΎΡΠΎΡΠΎΠΌ, ΡΠ°ΡΡΡΠΈΡΠ°Π½Π° Π½Π° Π΄Π²ΡΡ ΠΏΠ°ΡΡΠ°ΠΆΠΈΡΠΎΠ². ΠΡΠ»ΠΈ ΡΡΡΠ΅ΡΡΠ²ΡΠ΅Ρ Π½Π΅ΠΎΠ±Ρ ΠΎΠ΄ΠΈΠΌΠΎΡΡΡ, ΠΌΠΎΠΆΠ½ΠΎ Π΄ΠΎΠΎΡΠ½Π°ΡΡΠΈΡΡ Π΄ΠΎΠΏΠΎΠ»Π½ΠΈΡΠ΅Π»ΡΠ½ΠΎΠ΅ ΠΊΡΠ΅ΡΠ»ΠΎ. ΠΡΠΈ Π½Π΅ΠΎΠ±Ρ ΠΎΠ΄ΠΈΠΌΠΎΡΡΠΈ ΠΎΠ±ΡΠ»ΡΠΆΠΈΠ²Π°Π½ΠΈΡ ΠΈΠ»ΠΈ ΡΠ΅ΠΌΠΎΠ½ΡΠ° ΠΊΠ°Π±ΠΈΠ½Π° Π»Π΅Π³ΠΊΠΎ ΠΈ Π½Π΅ΠΏΡΠΈΠ½ΡΠΆΠ΄Π΅Π½Π½ΠΎ ΠΎΡΠΊΠΈΠ΄ΡΠ²Π°Π΅ΡΡΡ Π²ΠΏΠ΅ΡΠ΅Π΄. ΠΠ½ΡΡΡΠΈ ΡΡΡΠ°Π½ΠΎΠ²Π»Π΅Π½Π° ΡΠΈΡΡΠ΅ΠΌΠ° ΠΎΡΠΎΠΏΠ»Π΅Π½ΠΈΡ. ΠΠ»Ρ ΠΊΠΎΠΌΡΠΎΡΡΠ° Π²ΠΎΠ΄ΠΈΡΠ΅Π»Ρ ΠΊΠ°Π±ΠΈΠ½Π° Π³ΡΡΠ·ΠΎΠ²ΠΈΠΊΠ° ΠΠ°ΠΌΠΠ-55102 ΠΎΡΠ½Π°ΡΠ΅Π½Π° ΠΏΠΎΠ΄ΡΠ΅ΡΡΠΎΡΠ΅Π½Π½ΠΎΠΉ ΠΏΠΎΠ΄Π²Π΅ΡΠΊΠΎΠΉ. ΠΠ²Π΅ΡΠΈ ΠΎΠ±ΠΎΡΡΠ΄ΡΡΡΡΡ ΠΎΠΏΡΡΠΊΠ°ΡΡΠΈΠΌΠΈΡΡ ΠΎΠΊΠ½Π°ΠΌΠΈ. ΠΠ±ΠΈΠ²ΠΊΠ° ΠΊΠ°Π±ΠΈΠ½Ρ ΠΎΠ±Π΅ΡΠΏΠ΅ΡΠΈΠ²Π°Π΅Ρ Π΄ΠΎΡΡΠ°ΡΠΎΡΠ½ΡΠΉ ΡΡΠΎΠ²Π΅Π½Ρ ΡΠ΅ΡΠΌΠΎ- ΠΈ ΡΡΠΌΠΎΠΈΠ·ΠΎΠ»ΡΡΠΈΠΈ.
ΠΠ΄Π΅ΡΡ Π½Π΅ Π±ΡΠ»ΠΎ ΡΠΈΡΡΠ΅ΠΌ ΠΏΡΠΈΠ½ΡΠ΄ΠΈΡΠ΅Π»ΡΠ½ΠΎΠΉ Π²Π΅Π½ΡΠΈΠ»ΡΡΠΈΠΈ. ΠΠ»Ρ ΡΠΎΠ³ΠΎ ΡΡΠΎΠ±Ρ ΠΏΡΠΎΠ²Π΅ΡΡΠΈΡΡ ΠΊΠ°Π±ΠΈΠ½Ρ, ΠΈΡΠΏΠΎΠ»ΡΠ·ΡΡΡ Π΅ΡΡΠ΅ΡΡΠ²Π΅Π½Π½ΡΡ Π²Π΅Π½ΡΠΈΠ»ΡΡΠΈΡ ΠΏΡΠΈ ΠΏΠΎΠΌΠΎΡΠΈ ΡΠΎΡΡΠΎΡΠ΅ΠΊ ΠΈ Π»ΡΠΊΠ°, ΡΠ°ΡΠΏΠΎΠ»ΠΎΠΆΠ΅Π½Π½ΠΎΠ³ΠΎ Π½Π° ΠΊΡΡΡΠ΅. Π‘ΠΈΠ΄Π΅Π½ΡΡ ΠΊΠΎΠΌΠΏΠ»Π΅ΠΊΡΡΡΡΡΡ ΡΠ΅ΠΌΠ½ΡΠΌΠΈ Π±Π΅Π·ΠΎΠΏΠ°ΡΠ½ΠΎΡΡΠΈ.
ΠΠ°ΠΌΠΠ-55102: ΡΠ΅Ρ Π½ΠΈΡΠ΅ΡΠΊΠΈΠ΅ Ρ Π°ΡΠ°ΠΊΡΠ΅ΡΠΈΡΡΠΈΠΊΠΈ Π³ΡΡΠ·ΠΎΠ²ΠΎΠ³ΠΎ ΠΎΡΡΠ΅ΠΊΠ°
ΠΠ»Π°ΡΡΠΎΡΠΌΠ° ΡΠ°ΠΌΠΎΡΠ²Π°Π»Π° Π²ΡΠΏΠΎΠ»Π½Π΅Π½Π° ΠΏΠΎΠ»Π½ΠΎΡΡΡΡ ΠΈΠ· ΠΌΠ΅ΡΠ°Π»Π»Π° Ρ ΠΏΠΎΠΌΠΎΡΡΡ ΡΠ²Π°ΡΠΊΠΈ. ΠΠ»Π°ΡΡΠΎΡΠΌΠ° ΡΠ°ΡΠΏΠΎΠ»Π°Π³Π°Π΅ΡΡΡ Π½Π° Π½Π°ΡΠ°ΠΌΠ½ΠΈΠΊΠ΅. Π’Π°ΠΊ ΠΊΠ°ΠΊ Π΄Π°Π½Π½ΡΠΉ Π°Π²ΡΠΎΠΌΠΎΠ±ΠΈΠ»Ρ ΠΈΠ·Π³ΠΎΡΠ°Π²Π»ΠΈΠ²Π°Π»ΡΡ Π΄Π»Ρ Π½ΡΠΆΠ΄ ΡΠ΅Π»ΡΡΠΊΠΎΡ ΠΎΠ·ΡΠΉΡΡΠ²Π΅Π½Π½ΠΎΠΉ ΠΎΡΡΠ°ΡΠ»ΠΈ, ΡΠΎ ΠΊΠΎΠ½ΡΡΡΡΠΊΡΠΈΡ ΠΊΡΠ·ΠΎΠ²Π° ΠΏΡΠ΅Π΄ΡΡΠΌΠ°ΡΡΠΈΠ²Π°Π΅Ρ 3 Π±ΠΎΡΡΠ°, ΠΊΠΎΡΠΎΡΡΠ΅ ΠΎΡΠΊΠΈΠ΄ΡΠ²Π°ΡΡΡΡ. ΠΠ΅ΡΠ΅Π΄Π½ΠΈΠΉ Π½Π°Π΄Π΅ΠΆΠ½ΠΎ ΠΏΡΠΈΠ²Π°ΡΠ΅Π½ ΠΊ ΠΎΡΠ½ΠΎΠ²Π°Π½ΠΈΡ ΠΊΡΠ·ΠΎΠ²Π°.
ΠΡΠ·ΠΎΠ² ΠΠ°ΠΌΠΠ-55102 ΠΈΠΌΠ΅Π΅Ρ ΡΠ°ΠΊΠΎΠΉ, ΠΊΠΎΡΠΎΡΡΠΉ ΠΌΠΎΠΆΠ½ΠΎ Π΄ΠΎΠΏΠΎΠ»Π½ΠΈΡΠ΅Π»ΡΠ½ΠΎ Π΄ΠΎΡΠΊΠΎΠΌΠΏΠ»Π΅ΠΊΡΠΎΠ²Π°ΡΡ Ρ ΠΏΠΎΠΌΠΎΡΡΡ Π½Π°Π΄ΡΡΠ°Π²Π½ΠΎΠ³ΠΎ Π±ΠΎΡΡΠ° ΠΈΠ· ΠΌΠ΅ΡΠ°Π»Π»Π° ΠΈΠ»ΠΈ ΠΆΠ΅ ΠΈΠ· Π΄Π΅ΡΠ΅Π²Π°. Π§ΡΠΎΠ±Ρ Π±ΠΎΡΡΠΎΠ²ΡΠ΅ ΡΡΠ΅Π½ΠΊΠΈ ΠΌΠΎΠ³Π»ΠΈ ΠΎΡΠΊΡΡΠ²Π°ΡΡΡΡ Π±ΡΡΡΡΠ΅Π΅, ΠΈΡΠΏΠΎΠ»ΡΠ·ΠΎΠ²Π°Π»ΠΈΡΡ ΡΠΏΠ΅ΡΠΈΠ°Π»ΡΠ½ΡΠ΅ ΡΡΡΡΠΎΠΉΡΡΠ²Π°, ΡΠ°ΠΊ Π½Π°Π·ΡΠ²Π°Π΅ΠΌΡΠ΅ ΠΏΠΎΠΌΠΎΡΠ½ΠΈΠΊΠΈ. ΠΠ»Ρ ΡΠΎΠ³ΠΎ ΡΡΠΎΠ±Ρ ΠΌΠΎΠΆΠ½ΠΎ Π±ΡΠ»ΠΎ Π΄Π΅ΡΠΆΠ°ΡΡ Π±ΠΎΡΡΠ° Π² ΠΎΡΠΊΡΡΡΠΎΠΌ Π²ΠΈΠ΄Π΅, ΠΏΡΠΈΠΌΠ΅Π½ΡΡΡΡΡ ΡΠ΅ΠΏΠΈ.

ΠΠΎΠ»Π΅Π·Π½ΡΠΉ ΠΎΠ±ΡΠ΅ΠΌ ΠΊΡΠ·ΠΎΠ²Π° ΡΠΎΡΡΠ°Π²Π»ΡΠ΅Ρ 7,9 ΠΊΡΠ±ΠΈΡΠ΅ΡΠΊΠΈΡ ΠΌΠ΅ΡΡΠΎΠ². ΠΡΠ»ΠΈ ΡΡΡΠ°Π½ΠΎΠ²ΠΈΡΡ Π½Π°Π΄ΡΡΠ°Π²Π½ΡΠ΅ Π±ΠΎΡΡΠ°, ΡΠΎΠ³Π΄Π° ΠΎΠ½ Π²ΡΡΠ°ΡΡΠ΅Ρ Π΄ΠΎ 15,8 ΠΊΡΠ±ΠΈΡΠ΅ΡΠΊΠΈΡ ΠΌΠ΅ΡΡΠΎΠ². Π’Π°ΠΊ, Π΄Π»Ρ ΡΠ΅Π»ΡΡΠΊΠΎΠ³ΠΎ Ρ ΠΎΠ·ΡΠΉΡΡΠ²Π° ΠΈ ΡΡΡΠΎΠΈΡΠ΅Π»ΡΡΡΠ²Π° ΡΡΠΎ Π±ΡΠ» ΡΠ°ΠΌΡΠΉ Π»ΡΡΡΠΈΠΉ Π°Π²ΡΠΎΠΌΠΎΠ±ΠΈΠ»Ρ. Π ΡΠΎΠΌΡ ΠΆΠ΅ ΠΎΠ½ ΠΈΡΠΏΠΎΠ»ΡΠ·ΠΎΠ²Π°Π»ΡΡ Π΅ΡΠ΅ ΠΈ Π² ΠΊΠ°ΡΠ΅ΡΡΠ²Π΅ ΡΡΠ³Π°ΡΠ°.
Π’Π°ΠΊ ΠΊΠ°ΠΊ ΠΌΠ°ΡΠΈΠ½Π° ΠΏΠΎΠ·ΠΈΡΠΈΠΎΠ½ΠΈΡΠΎΠ²Π°Π»Π°ΡΡ ΠΊΠ°ΠΊ ΡΠ°ΠΌΠΎΡΠ²Π°Π», Π΄Π»Ρ ΡΠΎΠ³ΠΎ ΡΡΠΎΠ±Ρ Ρ ΠΊΡΠ·ΠΎΠ²Π° Π±ΡΠ»Π° Π²ΠΎΠ·ΠΌΠΎΠΆΠ½ΠΎΡΡΡ ΠΎΠΏΡΠΎΠΊΠΈΠ΄ΡΠ²Π°ΡΡΡΡ, ΠΈΡΠΏΠΎΠ»ΡΠ·ΠΎΠ²Π°Π»ΡΡ ΡΠΏΠ΅ΡΠΈΠ°Π»ΡΠ½ΡΠΉ Π³ΠΈΠ΄ΡΠ°Π²Π»ΠΈΡΠ΅ΡΠΊΠΈΠΉ ΠΌΠ΅Ρ Π°Π½ΠΈΠ·ΠΌ. ΠΠ½ ΡΠΎΡΡΠΎΡΠ» ΠΈΠ· ΠΏΡΡΠΈΠ·Π²Π΅Π½Π½ΠΎΠ³ΠΎ Π³ΠΈΠ΄ΡΠ°Π²Π»ΠΈΡΠ΅ΡΠΊΠΎΠ³ΠΎ ΡΠΈΠ»ΠΈΠ½Π΄ΡΠ° Ρ ΠΎΠ΄Π½ΠΎΡΡΠΎΡΠΎΠ½Π½ΠΈΠΌ Π΄Π΅ΠΉΡΡΠ²ΠΈΠ΅ΠΌ. ΠΡΠΎ ΡΠ°ΠΊ Π½Π°Π·ΡΠ²Π°Π΅ΠΌΡΠΉ Π³ΠΈΠ΄ΡΠΎΡΠΈΠ»ΠΈΠ½Π΄Ρ. ΠΠ°ΠΌΠΠ-55102 Π±Π»Π°Π³ΠΎΠ΄Π°ΡΡ ΡΡΠΎΠΌΡ ΠΌΠΎΠ³ Π·Π° 19 ΡΠ΅ΠΊΡΠ½Π΄ Π²ΡΠΏΠΎΠ»Π½ΠΈΡΡ ΠΏΠΎΠ΄ΡΠ΅ΠΌ ΠΊΡΠ·ΠΎΠ²Π° Π½Π° 50 Π³ΡΠ°Π΄ΡΡΠΎΠ².
Π‘ΠΈΠ»ΠΎΠ²ΠΎΠΉ Π°Π³ΡΠ΅Π³Π°Ρ
Π Π°Π±ΠΎΡΠ΅Π΅ Π·Π²Π΅Π½ΠΎ ΠΌΠ°ΡΠΈΠ½Ρ β ΡΡΠΎ, ΠΊΠΎΠ½Π΅ΡΠ½ΠΎ ΠΆΠ΅, Π΄Π²ΠΈΠ³Π°ΡΠ΅Π»Ρ. ΠΠ°ΠΌΠΠ-55102 ΡΠΊΠΎΠΌΠΏΠ»Π΅ΠΊΡΠΎΠ²Π°Π½ ΡΠ΅ΡΡΡΠ΅Ρ ΡΠ°ΠΊΡΠ½ΡΠΌ Π²ΠΎΡΡΠΌΠΈΡΠΈΠ»ΠΈΠ½Π΄ΡΠΎΠ²ΡΠΌ Π΄ΠΈΠ·Π΅Π»ΡΠ½ΡΠΌ Π΄Π²ΠΈΠ³Π°ΡΠ΅Π»Π΅ΠΌ ΠΠ°ΠΌΠΠ 740,1. ΠΠ³ΡΠ΅Π³Π°Ρ ΠΈΠΌΠ΅Π΅Ρ ΡΡΠ°Π½Π΄Π°ΡΡΠ½ΡΡ ΠΊΠΎΠ½ΡΡΡΡΠΊΡΠΈΡ. ΠΠΎΡΠΎΡ ΠΎΡΠ½Π°ΡΠ°Π΅ΡΡΡ ΡΡΡΠ±ΠΎΠ½Π°Π΄Π΄ΡΠ²ΠΎΠΌ ΠΈ ΡΠΈΡΡΠ΅ΠΌΠΎΠΉ ΠΏΡΠ΅Π΄Π²Π°ΡΠΈΡΠ΅Π»ΡΠ½ΠΎΠ³ΠΎ ΠΎΡ Π»Π°ΠΆΠ΄Π΅Π½ΠΈΡ Π²ΠΎΠ·Π΄ΡΡ Π°.
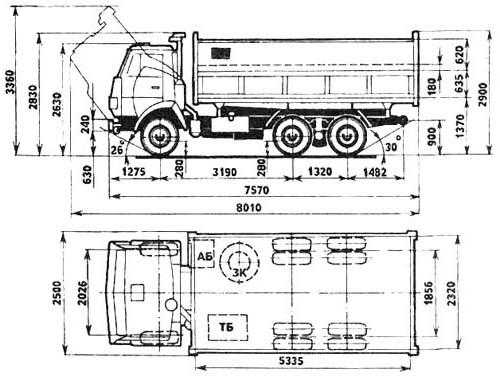
Π‘ΠΈΠ»ΠΎΠ²ΠΎΠΉ ΡΠ·Π΅Π» ΠΈΠΌΠ΅Π΅Ρ ΠΌΠΎΡΠ½ΠΎΡΡΡ Π² 240 Π».Ρ. ΠΠ±ΡΠ΅ΠΌ Π°Π³ΡΠ΅Π³Π°ΡΠ° ΡΠΎΡΡΠ°Π²Π»ΡΠ΅Ρ 10,5 Π». ΠΡΡΡΡΡΠΈΠΉ ΠΌΠΎΠΌΠ΅Π½Ρ ΡΠ°Π²Π΅Π½ 667 ΠΠΌ. Π‘ΡΠ΅ΠΏΠ΅Π½Ρ ΡΠΆΠ°ΡΠΈΡ ΡΠΎΡΡΠ°Π²Π»ΡΠ΅Ρ 17. ΠΡΠΎΡ ΠΌΠΎΡΠΎΡ ΠΌΠΎΠΆΠ½ΠΎ Π·Π°ΠΏΡΡΡΠΈΡΡ ΠΏΡΠΈ Π»ΡΠ±ΡΡ ΡΠ΅ΠΌΠΏΠ΅ΡΠ°ΡΡΡΠ°Ρ , ΡΠ°ΠΊ ΠΊΠ°ΠΊ ΠΈΠ½ΠΆΠ΅Π½Π΅ΡΡ ΠΏΡΠ΅Π΄ΡΡΠΌΠΎΡΡΠ΅Π»ΠΈ ΡΠ»Π΅ΠΊΡΠΎΡΠ°ΠΊΠ΅Π»ΡΠ½ΡΠΉ Π°ΠΏΠΏΠ°ΡΠ°Ρ ΠΏΠΎΠ΄ΠΎΠ³ΡΠ΅Π²Π°.
Π‘ΠΌΠ°Π·ΠΎΡΠ½Π°Ρ ΡΠΈΡΡΠ΅ΠΌΠ° ΠΈ ΡΠΈΡΡΠ΅ΠΌΠ° ΠΏΠΈΡΠ°Π½ΠΈΡ
Π‘Π°ΠΌΠΎΡΠ²Π°Π» ΠΎΡΠ½Π°ΡΠ΅Π½ ΡΠ°Π·Π΄Π΅Π»Π΅Π½Π½ΠΎΠΉ ΡΠΎΠΏΠ»ΠΈΠ²Π½ΠΎΠΉ ΡΠΈΡΡΠ΅ΠΌΠΎΠΉ. Π Π΅Π΅ ΡΠΎΡΡΠ°Π²Π΅ Π½Π°ΡΠΎΡ Π΄Π»Ρ Π²ΡΡΠΎΠΊΠΎΠ³ΠΎ Π΄Π°Π²Π»Π΅Π½ΠΈΡ, ΠΌΡΡΡΠ° ΠΎΠΏΠ΅ΡΠ΅ΠΆΠ΅Π½ΠΈΡ Π²ΠΏΡΡΡΠΊΠ°, ΡΠΎΡΡΡΠ½ΠΊΠΈ Ρ ΠΈΠ³Π»ΠΎΠΉ Π΄Π»Ρ ΡΠ΅Π³ΡΠ»ΠΈΡΠΎΠ²ΠΊΠΈ ΠΏΠΎΠ΄Π°ΡΠΈ ΡΠΎΠΏΠ»ΠΈΠ²Π°. Π’Π°ΠΊΠΆΠ΅ ΡΠΎΠΏΠ»ΠΈΠ²Π½Π°Ρ ΡΠΈΡΡΠ΅ΠΌΠ° ΠΎΡΠ½Π°ΡΠ°Π΅ΡΡΡ Π½Π°ΡΠΎΡΠΎΠΌ Π½ΠΈΠ·ΠΊΠΎΠ³ΠΎ Π΄Π°Π²Π»Π΅Π½ΠΈΡ.
Π‘ΠΈΡΡΠ΅ΠΌΠ° ΡΠΌΠ°Π·ΠΊΠΈ ΠΊΠΎΠΌΠ±ΠΈΠ½ΠΈΡΠΎΠ²Π°Π½Π½Π°Ρ. Π‘ΠΎΡΡΠΎΠΈΡ ΠΎΠ½Π° ΠΈΠ· ΠΌΠΎΠΊΡΠΎΠ³ΠΎ ΠΊΠ°ΡΡΠ΅ΡΠ° ΠΈ ΡΠΈΠ»ΡΡΡΠΎΠ² ΠΎΡΠΈΡΡΠΊΠΈ. ΠΠΎΠ·Π΄ΡΡΠ½ΡΠΉ ΡΠΈΠ»ΡΡΡ ΠΈΠΌΠ΅Π΅Ρ Π΄Π²ΡΡ ΡΡΡΠΏΠ΅Π½ΡΠ°ΡΡΡ ΠΊΠΎΠ½ΡΡΡΡΠΊΡΠΈΡ.
Π‘ΡΠ΅ΠΏΠ»Π΅Π½ΠΈΠ΅, ΠΠΠ
ΠΠ°ΠΌΠΠ-55102 ΠΎΡΠ½Π°ΡΠ°Π΅ΡΡΡ Π΄ΠΈΡΠΊΠΎΠ²ΡΠΌ ΡΡΠΈΠΊΡΠΈΠΎΠ½Π½ΡΠΌ ΡΡΡ ΠΈΠΌ ΡΡΠ΅ΠΏΠ»Π΅Π½ΠΈΠ΅ΠΌ. ΠΠΠ β ΠΌΠ΅Ρ Π°Π½ΠΈΡΠ΅ΡΠΊΠ°Ρ. 10 ΡΡΡΠΏΠ΅Π½Π΅ΠΉ ΠΊΠΎΡΠΎΠ±ΠΊΠΈ ΠΏΡΠ΅Π΄ΡΡΠΌΠ°ΡΡΠΈΠ²Π°ΡΡ 5 ΠΏΠ΅ΡΠ΅Π΄Π½ΠΈΡ ΠΏΠ΅ΡΠ΅Π΄Π°Ρ (ΠΏΠΎΠ»ΠΎΠ²ΠΈΠ½ΡΠ°ΡΡΠ΅) ΠΈ 1 Π·Π°Π΄Π½ΡΡ. ΠΠΠ ΡΠ°Π±ΠΎΡΠ°Π΅Ρ Π² ΠΏΠ°ΡΠ΅ Ρ ΡΠ΅Π΄ΡΠΊΡΠΎΡΠΎΠΌ, ΠΊΠΎΡΠΎΡΡΠΉ ΠΎΠ±Π΅ΡΠΏΠ΅ΡΠΈΠ²Π°Π΅Ρ Π°Π²ΡΠΎΠΌΠΎΠ±ΠΈΠ»Ρ ΠΏΡΡΠΌΡΠΌΠΈ ΠΈ ΠΏΠΎΠ½ΠΈΠΆΠ΅Π½Π½ΡΠΌΠΈ Π΄ΠΈΠ°ΠΏΠ°Π·ΠΎΠ½Π°ΠΌΠΈ ΡΠ°Π±ΠΎΡΡ. Π‘ΠΈΠ»ΠΎΠ²ΡΠ΅ ΡΠ·Π»Ρ Π°Π²ΡΠΎΠΌΠΎΠ±ΠΈΠ»Ρ Π·Π°ΠΊΡΠ΅ΠΏΠ»ΡΡΡΡΡ Π½Π° ΠΏΡΡΠΈ ΠΎΠΏΠΎΡΠ°Ρ Π½Π° ΡΠ°ΡΡΠΈ.

Π’ΡΠ°Π½ΡΠΌΠΈΡΡΠΈΡ ΡΠ°ΠΊΠΆΠ΅ ΠΈΠΌΠ΅Π΅Ρ Π±Π»ΠΎΠΊΠΈΡΡΠ΅ΠΌΡΠΉ ΠΌΠ΅ΠΆΠΎΡΠ΅Π²ΠΎΠΉ Π΄ΠΈΡΡΠ΅ΡΠ΅Π½ΡΠΈΠ°Π» ΠΈ ΡΡΠ΅Π΄Π½ΠΈΠΉ ΠΌΠΎΡΡ. ΠΠ°ΡΠ΄Π°Π½Π½ΡΠΉ Π²Π°Π» Π²ΡΠΏΠΎΠ»Π½Π΅Π½ Π² Π²ΠΈΠ΄Π΅ Π΄Π²ΡΡ Π²Π°Π»ΠΎΠ². ΠΠ½ΠΈ ΠΏΡΠΎΠ»ΠΎΠΆΠ΅Π½Ρ Π½Π΅ΠΏΠΎΡΡΠ΅Π΄ΡΡΠ²Π΅Π½Π½ΠΎ ΠΎΡ ΡΠ΅Π΄ΡΠΊΡΠΎΡΠ° ΡΡΠ΅Π΄Π½Π΅Π³ΠΎ ΠΌΠΎΡΡΠ° ΠΊ Π·Π°Π΄Π½Π΅ΠΌΡ ΠΌΠΎΡΡΡ.
Π’ΠΎΡΠΌΠΎΠ·Π½Π°Ρ ΡΠΈΡΡΠ΅ΠΌΠ°
ΠΠ½Π° ΡΠ΅Π°Π»ΠΈΠ·ΠΎΠ²Π°Π½Π° ΠΏΠΎΡΡΠ΅Π΄ΡΡΠ²ΠΎΠΌ Π±Π°ΡΠ°Π±Π°Π½Π½ΡΡ ΡΠΎΡΠΌΠΎΠ·ΠΎΠ² Π½Π° Π²ΡΠ΅ ΠΊΠΎΠ»Π΅ΡΠ°. Π Π΄Π΅ΠΉΡΡΠ²ΠΈΠ΅ ΠΎΠ½Π° ΠΏΡΠΈΠ²ΠΎΠ΄ΠΈΡΡΡ ΠΏΠΎΡΡΠ΅Π΄ΡΡΠ²ΠΎΠΌ ΠΏΠ½Π΅Π²ΠΌΠ°ΡΠΈΡΠ΅ΡΠΊΠΎΠ³ΠΎ ΠΏΡΠΈΠ²ΠΎΠ΄Π°. Π’Π°ΠΊΠΆΠ΅ ΡΠ°ΠΌΠΎΡΠ²Π°Π» ΠΎΡΠ½Π°ΡΠ΅Π½ ΡΡΠΎΡΠ½ΠΎΡΠ½ΡΠΌ ΡΠΎΡΠΌΠΎΠ·ΠΎΠΌ.
ΠΡΠΎΡΠΈΠ΅ ΡΠ΅Ρ Π½ΠΈΡΠ΅ΡΠΊΠΈΠ΅ Π΄Π°Π½Π½ΡΠ΅
Π‘Π°ΠΌΠΎΡΠ²Π°Π» Π² ΡΠ½Π°ΡΡΠΆΠ΅Π½Π½ΠΎΠΌ ΡΠΎΡΡΠΎΡΠ½ΠΈΠΈ Π²Π΅ΡΠΈΡ 8480 ΠΊΠ³. ΠΡΡΠ·ΠΎΠΏΠΎΠ΄ΡΠ΅ΠΌΠ½ΠΎΡΡΡ Π΅Π³ΠΎ ΡΠΎΡΡΠ°Π²Π»ΡΠ΅Ρ 7 Ρ. ΠΠΎΠ»Π½Π°Ρ ΠΌΠ°ΡΡΠ° ΠΌΠ°ΡΠΈΠ½Ρ 15 630 ΠΊΠ³. ΠΠΎΡΠΎΡ Π²ΠΎΡΡΠΌΠΈΡΠΈΠ»ΠΈΠ½Π΄ΡΠΎΠ²ΡΠΉ V-ΠΎΠ±ΡΠ°Π·Π½ΡΠΉ Π΄ΠΈΠ·Π΅Π»ΡΠ½ΡΠΉ Ρ ΡΡΡΠ±ΠΎΠ½Π°Π΄Π΄ΡΠ²ΠΎΠΌ. ΠΠΎΠΌΠΈΠ½Π°Π»ΡΠ½Π°Ρ ΠΌΠΎΡΠ½ΠΎΡΡΡ Π°Π³ΡΠ΅Π³Π°ΡΠ° ΡΠΎΡΡΠ°Π²Π»ΡΠ΅Ρ 240 Π».Ρ. Π Π°Π±ΠΎΡΠΈΠΉ ΠΎΠ±ΡΠ΅ΠΌ ΡΠΈΠ»ΠΎΠ²ΠΎΠ³ΠΎ ΡΠ·Π»Π° β 10,5 Π». ΠΠ°ΠΊΡΠΈΠΌΠ°Π»ΡΠ½Π°Ρ ΡΠΊΠΎΡΠΎΡΡΡ, Ρ ΠΊΠΎΡΠΎΡΠΎΠΉ ΠΌΠΎΠΆΠ΅Ρ Π΄Π²ΠΈΠ³Π°ΡΡΡΡ ΡΡΠΎΡ Π°Π²ΡΠΎΠΌΠΎΠ±ΠΈΠ»Ρ β 80 ΠΊΠΌ/Ρ. ΠΠ°ΠΊ Π΄Π»Ρ ΡΠΎΠΏΠ»ΠΈΠ²Π° ΠΈΠΌΠ΅Π΅Ρ ΠΎΠ±ΡΠ΅ΠΌ Π² 210 Π».

ΠΠ° Π³ΡΡΠ·ΠΎΠ²ΠΈΠΊΠ΅ ΠΠ°ΠΌΠΠ-55102 ΡΠ»Π΅ΠΊΡΡΠΎΡΡ Π΅ΠΌΠ° ΡΠΎΡΡΠΎΠΈΡ ΠΈΠ· ΠΌΠ½ΠΎΠΆΠ΅ΡΡΠ²Π° ΡΠ°Π·Π»ΠΈΡΠ½ΡΡ ΡΠ»Π΅ΠΌΠ΅Π½ΡΠΎΠ². ΠΠΈΡΠ°Π΅ΡΡΡ ΠΎΠ½ ΠΎΡ 2 Π°ΠΊΠΊΡΠΌΡΠ»ΡΡΠΎΡΠΎΠ², Π° ΡΠ°ΠΊΠΆΠ΅ ΡΡ Π΅ΠΌΠ° ΡΠΎΠ΄Π΅ΡΠΆΠΈΡ Π³Π΅Π½Π΅ΡΠ°ΡΠΎΡ.
Π ΠΊΠ°ΡΠ΅ΡΡΠ²Π΅ Π·Π°ΠΊΠ»ΡΡΠ΅Π½ΠΈΡ
ΠΡΠΈ ΠΌΠ°ΡΠΈΠ½Ρ ΡΠΆΠ΅ ΡΠ½ΡΡΡ Ρ ΠΏΡΠΎΠΈΠ·Π²ΠΎΠ΄ΡΡΠ²Π°. ΠΠ΄Π½Π°ΠΊΠΎ ΡΠ°ΠΌΠΎΡΠ²Π°Π» ΠΈΠΌΠ΅Π΅Ρ ΠΌΠ½ΠΎΠΆΠ΅ΡΡΠ²ΠΎ ΠΏΡΠ΅ΠΈΠΌΡΡΠ΅ΡΡΠ². ΠΠ½ΠΎΠ³ΠΈΠ΅ Π΄ΠΎ ΡΠΈΡ ΠΏΠΎΡ ΠΈΡΠΏΠΎΠ»ΡΠ·ΡΡΡ Π³ΡΡΠ·ΠΎΠ²ΠΈΠΊΠΈ. ΠΠ½ΠΈ ΠΎΡΠ»ΠΈΡΠ°ΡΡΡΡ Π²ΡΡΠΎΠΊΠΎΠΉ Π½Π°Π΄Π΅ΠΆΠ½ΠΎΡΡΡΡ ΠΈ ΠΏΡΠΎΠΈΠ·Π²ΠΎΠ΄ΠΈΡΠ΅Π»ΡΠ½ΠΎΡΡΡΡ. ΠΠ½ΠΈ ΡΠ°Π±ΠΎΡΠ°ΡΡ Π² ΡΠ΅Ρ ΡΡΠ»ΠΎΠ²ΠΈΡΡ , Π³Π΄Π΅ ΠΈΠ½ΠΎΠΌΠ°ΡΠΊΠΈ Β«ΠΏΠΎΠ³ΠΈΠ±Π°ΡΡΒ». ΠΠ°ΠΆΠ΅ ΡΠ΅Π³ΠΎΠ΄Π½Ρ, ΠΊΠΎΠ³Π΄Π° Π½Π° Π°Π²ΡΠΎΠΌΠΎΠ±ΠΈΠ»ΡΠ½ΠΎΠΌ ΡΡΠ½ΠΊΠ΅ ΠΏΡΠ΅Π΄ΡΡΠ°Π²Π»Π΅Π½ΠΎ ΠΌΠ½ΠΎΠ³ΠΎ ΠΈΠΌΠΏΠΎΡΡΠ½ΠΎΠΉ ΡΠ΅Ρ Π½ΠΈΠΊΠΈ, ΡΡΠΎΡ Π³ΡΡΠ·ΠΎΠ²ΠΈΠΊ Π²ΡΠ΅-ΡΠ°ΠΊΠΈ Π·Π°Π½ΠΈΠΌΠ°Π΅Ρ ΡΠ²ΠΎΡ ΠΊΠΎΠ½ΠΊΡΠ΅ΡΠ½ΡΡ Π½ΠΈΡΡ. ΠΠΎ ΡΠΈΡ ΠΏΠΎΡ ΠΈΡΠΏΠΎΠ»ΡΠ·ΡΠ΅ΡΡΡ ΠΈ Π² ΡΡΡΠΎΠΈΡΠ΅Π»ΡΡΡΠ²Π΅ Π΄Π»Ρ ΠΏΠ΅ΡΠ΅Π²ΠΎΠ·ΠΊΠΈ Π³ΡΡΠ·ΠΎΠ², ΠΈ Π² ΡΠ΅Π»ΡΡΠΊΠΎΠΌ Ρ ΠΎΠ·ΡΠΉΡΡΠ²Π΅ Π±Π»Π°Π³ΠΎΠ΄Π°ΡΡ ΡΠΎΠΌΡ, ΡΡΠΎ ΠΈΠΌΠ΅Π΅Ρ ΠΎΠ±ΡΠ΅ΠΌΠ½ΡΠΉ ΠΊΡΠ·ΠΎΠ², ΠΠ°ΠΌΠΠ-55102.

Π’Π°ΠΊΠΆΠ΅ ΠΏΡΠΎΠΈΠ·Π²ΠΎΠ΄ΠΈΠ»ΠΈΡΡ ΡΠ°Π·Π»ΠΈΡΠ½ΡΠ΅ ΠΌΠΎΠ΄ΠΈΡΠΈΠΊΠ°ΡΠΈΠΈ Π½Π° Π±Π°Π·Π΅ ΡΡΠΎΠΉ ΠΌΠΎΠ΄Π΅Π»ΠΈ. ΠΠ° Π·Π°Π²ΠΎΠ΄Π°Ρ ΠΏΠΎΠ΄ Π·Π°ΠΌΠ΅Π½Ρ ΠΏΡΡΠΊΠ°Π»ΠΈΡΡ ΠΌΠ½ΠΎΠ³ΠΈΠ΅ ΡΠ·Π»Ρ Π°Π²ΡΠΎΠΌΠΎΠ±ΠΈΠ»Ρ, ΠΊΠΎΡΠΎΡΡΠ΅ ΡΠΆΠ΅ ΠΌΠΎΡΠ°Π»ΡΠ½ΠΎ ΡΡΡΠ°ΡΠ΅Π»ΠΈ. Π§ΡΠΎ ΠΊΠ°ΡΠ°Π΅ΡΡΡ ΠΌΠΎΠ΄ΠΈΡΠΈΡΠΈΡΠΎΠ²Π°Π½Π½ΡΡ ΡΠ°ΠΌΠΎΡΠ²Π°Π»ΠΎΠ², ΡΠΎ Π·Π΄Π΅ΡΡ ΠΎΡΠ»ΠΈΡΠΈΠ΅ Π² Π³ΡΡΠ·ΠΎΠΏΠΎΠ΄ΡΠ΅ΠΌΠ½ΠΎΡΡΠΈ ΠΏΡΠΈ ΠΎΡΡΠ°Π»ΡΠ½ΡΡ ΠΏΡΠ°ΠΊΡΠΈΡΠ΅ΡΠΊΠΈ ΠΎΠ΄ΠΈΠ½Π°ΠΊΠΎΠ²ΡΡ Ρ Π°ΡΠ°ΠΊΡΠ΅ΡΠΈΡΡΠΈΠΊΠ°Ρ .
ΠΡΠ°ΠΊ, ΠΌΡ Π²ΡΡΡΠ½ΠΈΠ»ΠΈ, ΠΊΠ°ΠΊΠΈΠ΅ ΠΈΠΌΠ΅Π΅Ρ ΠΠ°ΠΌΠΠ-55102 ΡΠ΅Ρ Π½ΠΈΡΠ΅ΡΠΊΠΈΠ΅ Ρ Π°ΡΠ°ΠΊΡΠ΅ΡΠΈΡΡΠΈΠΊΠΈ. ΠΠ°ΠΊ Π²ΠΈΠ΄ΠΈΠΌ, ΡΡΠΎ Ρ ΠΎΡΠΎΡΠΈΠΉ ΠΈ ΠΏΠΎΠ»Π΅Π·Π½ΡΠΉ Π°Π²ΡΠΎΠΌΠΎΠ±ΠΈΠ»Ρ.
www.syl.ru